Introduction to Rigid-Flex PCB
Rigid-flex PCBs are a hybrid of rigid and flexible printed Circuit boards, combining the best features of both technologies. They consist of multiple layers of flexible PCB substrates, such as polyimide, which are laminated together with rigid PCB Layers, usually made from FR-4 material. This unique construction allows for the creation of three-dimensional electronic assemblies that can be folded, bent, or twisted to fit into compact spaces or conform to irregular shapes.
Advantages of Rigid-Flex PCB
- Space savings: Rigid-flex PCBs enable the design of more compact and lightweight electronic devices by eliminating the need for bulky connectors and cables.
- Improved reliability: The integrated nature of rigid-flex PCBs reduces the number of interconnects, which are common points of failure in electronic assemblies.
- Enhanced signal integrity: Rigid-flex PCBs minimize signal loss and interference by reducing the length of traces and eliminating the need for connectors.
- Increased design flexibility: The ability to fold and bend rigid-flex PCBs allows for more creative and efficient packaging solutions.
- Cost-effectiveness: Although the initial cost of rigid-flex PCBs may be higher, they often result in overall cost savings by reducing assembly time, minimizing the number of components, and improving reliability.
Comparison of Rigid-Flex PCB and Flexible PCB
While both rigid-flex and flexible PCBs offer the ability to bend and fold, there are several key differences between the two technologies that make rigid-flex PCBs a better choice for many electronic projects.
Feature | Rigid-Flex PCB | Flexible PCB |
---|---|---|
Rigidity | Combines rigid and flexible layers | Entirely flexible |
Durability | More durable due to rigid layers | Less durable, prone to tearing |
Component mounting | Supports surface mount and through-hole components | Limited component mounting options |
Dimensional stability | Stable in rigid areas, flexible in designated regions | Can be prone to dimensional changes |
Shielding | Can incorporate shielding layers | Difficult to shield effectively |
Cost | Higher initial cost, but often results in overall cost savings | Lower initial cost, but may require additional components and assembly steps |
Durability and Reliability
One of the main advantages of rigid-flex PCBs over purely flexible PCBs is their increased durability and reliability. The rigid layers in a rigid-flex PCB provide structural support and protection for the flexible layers, reducing the risk of damage from repeated bending or exposure to environmental stresses. This makes rigid-flex PCBs a better choice for applications that require a high level of reliability, such as aerospace, military, and medical devices.
Component Mounting and Signal Integrity
Rigid-flex PCBs also offer superior component mounting options compared to flexible PCBs. The rigid layers in a rigid-flex PCB provide a stable surface for mounting surface mount and through-hole components, ensuring a robust and reliable connection. In contrast, flexible PCBs have limited component mounting options and may require additional support structures or adhesives to secure components in place.
Furthermore, rigid-flex PCBs can provide better signal integrity than flexible PCBs due to their ability to incorporate shielding layers and minimize the length of traces. The rigid layers in a rigid-flex PCB can be used to create controlled impedance structures, such as striplines or microstrips, which help to maintain signal integrity and reduce electromagnetic interference (EMI).
Applications of Rigid-Flex PCB
Rigid-flex PCBs are used in a wide range of electronic applications where space savings, reliability, and design flexibility are critical factors. Some common applications include:
-
Aerospace and defense: Rigid-flex PCBs are used in avionics, satellite systems, and military equipment due to their ability to withstand harsh environmental conditions and provide reliable performance in compact spaces.
-
Medical devices: Rigid-flex PCBs are used in implantable devices, diagnostic equipment, and wearable medical technology, where size, reliability, and biocompatibility are essential.
-
Consumer electronics: Rigid-flex PCBs are increasingly used in smartphones, tablets, and wearable devices to enable sleek, compact designs with enhanced functionality.
-
Automotive electronics: Rigid-flex PCBs are used in advanced driver assistance systems (ADAS), infotainment systems, and electronic control units (ECUs) to provide reliable performance in the harsh automotive environment.
-
Industrial automation: Rigid-flex PCBs are used in robotics, machine vision systems, and process control equipment, where they enable the integration of sensors, actuators, and control electronics in compact, reliable packages.
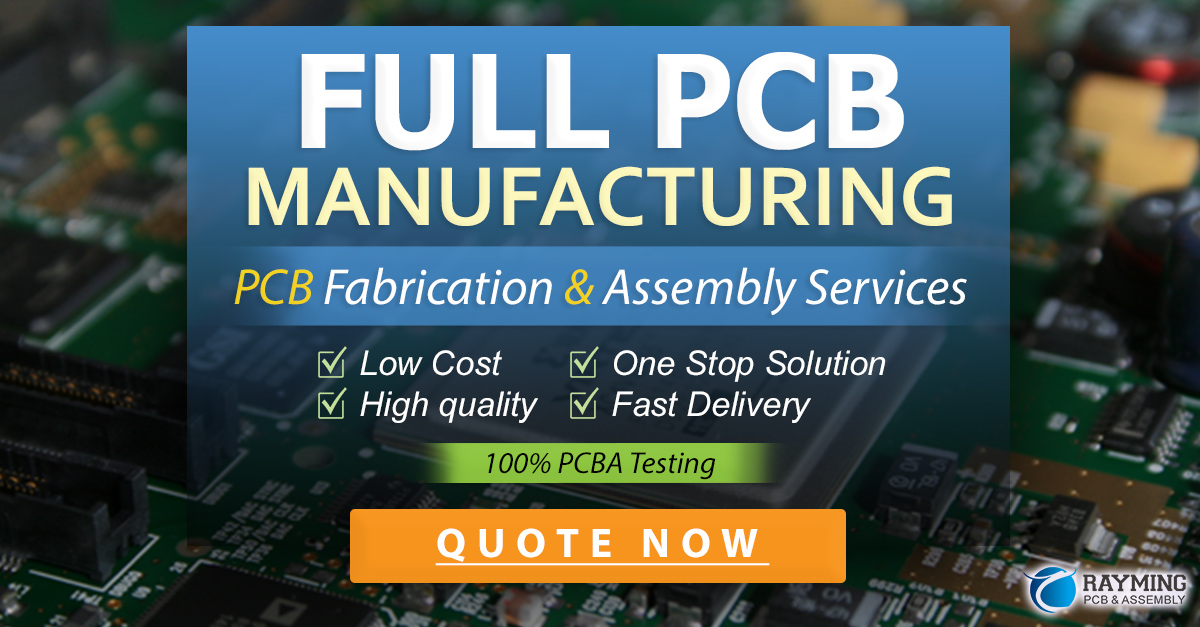
Design Considerations for Rigid-Flex PCB
Designing a rigid-flex PCB requires careful consideration of several factors to ensure optimal performance, reliability, and manufacturability. Some key design considerations include:
-
Material selection: Choosing the appropriate flexible and rigid substrate materials based on the application requirements, such as temperature range, chemical resistance, and dielectric properties.
-
Bend radius: Determining the minimum bend radius for the flexible layers to avoid excessive stress and potential failure.
-
Layer stack-up: Defining the number and arrangement of rigid and flexible layers to achieve the desired electrical and mechanical properties.
-
Coverlay and stiffener placement: Incorporating coverlay and stiffener materials to protect the flexible layers and provide additional support in critical areas.
-
Trace routing: Routing traces to minimize stress in the flexible regions and ensure reliable interconnections between the rigid and flexible layers.
-
Manufacturing constraints: Considering the limitations and capabilities of the PCB fabrication process, such as minimum feature sizes, tolerances, and assembly requirements.
FAQ
-
What is the difference between rigid-flex PCB and flexible PCB?
Rigid-flex PCB combines rigid and flexible layers into a single, integrated structure, while flexible PCB is entirely flexible. Rigid-flex PCBs offer increased durability, better component mounting options, and improved signal integrity compared to flexible PCBs. -
What are the advantages of using rigid-flex PCB in electronic projects?
The main advantages of using rigid-flex PCB include space savings, improved reliability, enhanced signal integrity, increased design flexibility, and potential cost-effectiveness. -
In what industries are rigid-flex PCBs commonly used?
Rigid-flex PCBs are commonly used in aerospace, defense, medical devices, consumer electronics, automotive electronics, and industrial automation. -
How does the cost of rigid-flex PCB compare to flexible PCB?
Rigid-flex PCBs generally have a higher initial cost compared to flexible PCBs due to their more complex manufacturing process. However, rigid-flex PCBs often result in overall cost savings by reducing assembly time, minimizing the number of components, and improving reliability. -
What are some key design considerations for rigid-flex PCB?
Key design considerations for rigid-flex PCB include material selection, bend radius, layer stack-up, coverlay and stiffener placement, trace routing, and manufacturing constraints.
Conclusion
Rigid-flex PCBs offer numerous advantages over traditional flexible PCBs, making them an attractive choice for a wide range of electronic projects. By combining the best features of rigid and flexible PCB technologies, rigid-flex PCBs enable the creation of compact, reliable, and high-performance electronic assemblies that can withstand harsh environments and demanding applications.
When designing a rigid-flex PCB, it is essential to carefully consider factors such as material selection, bend radius, layer stack-up, and manufacturing constraints to ensure optimal performance and reliability. By leveraging the benefits of rigid-flex PCB technology and following best design practices, electronic engineers and product designers can create innovative, efficient, and cost-effective solutions for a variety of industries and applications.
No responses yet