What is FR4?
FR4 is a glass-reinforced epoxy laminate material. It consists of multiple layers of woven fiberglass cloth impregnated with epoxy resin, which is then cured under heat and pressure to form a rigid, stable, and durable material. The number “4” in FR4 refers to the woven glass reinforcement used in the material.
The composition of FR4 typically includes:
– Fiberglass cloth (E-glass)
– Epoxy resin
– Copper foil (for conductive layers)
– Other additives (for improved properties)
Properties of FR4
FR4 has several desirable properties that make it an excellent choice for PCB manufacturing:
Mechanical Properties
- High tensile strength
- Good flexural strength
- Excellent dimensional stability
- Resistant to cracking and delamination
- Lightweight yet sturdy
Electrical Properties
- Good dielectric constant (typically 4.5 at 1 MHz)
- Low dielectric loss tangent (0.02 at 1 MHz)
- High insulation resistance
- Suitable for high-frequency applications
Thermal Properties
- Flame retardant (self-extinguishing)
- Glass transition temperature (Tg) around 130°C to 140°C
- Thermal expansion coefficient similar to copper
- Suitable for lead-free soldering processes
Chemical Properties
- Resistant to various chemicals and solvents
- Resistant to moisture absorption
- Compatible with common PCB manufacturing processes
Advantages of using FR4 for PCBs
- Durability and Reliability
- FR4 is mechanically strong and can withstand stress and vibrations
- It is resistant to cracking and delamination, ensuring long-term reliability
-
FR4 PCBs can operate in a wide range of environmental conditions
-
Excellent Insulation
- FR4 provides excellent electrical insulation between conductive layers
- It has high insulation resistance, preventing current leakage and short circuits
-
FR4 is suitable for applications with high voltage requirements
-
Thermal Stability
- FR4 is flame retardant and self-extinguishing, enhancing safety
- It can withstand high temperatures during soldering and operation
-
The thermal expansion coefficient of FR4 is close to that of copper, minimizing stress due to temperature changes
-
Cost-effectiveness
- FR4 is widely available and relatively inexpensive compared to other PCB Materials
- It is compatible with standard PCB manufacturing processes, reducing production costs
-
FR4 PCBs can be mass-produced efficiently, making them economical for large-scale production
-
Versatility
- FR4 can be used for a wide range of PCB applications, from simple single-layer boards to complex multilayer designs
- It is suitable for both through-hole and surface-mount components
- FR4 PCBs can be manufactured in various thicknesses and copper weights to meet specific requirements
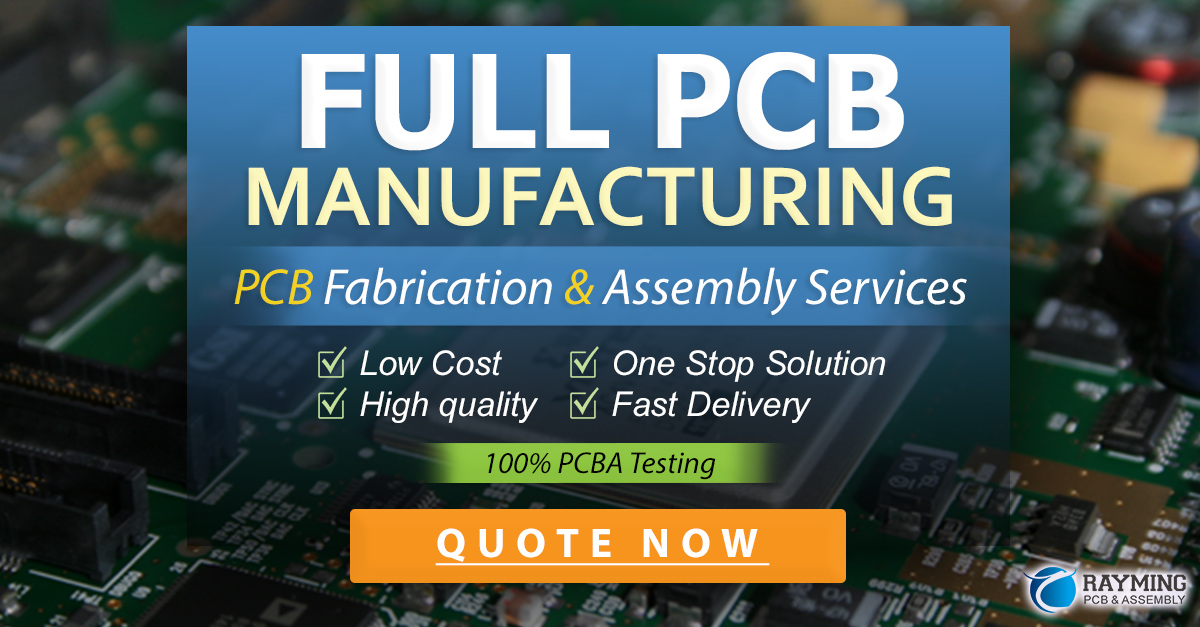
Applications of FR4 PCBs
FR4 PCBs are used in a wide range of industries and applications, including:
- Consumer electronics (smartphones, laptops, televisions)
- Automotive electronics (engine control units, infotainment systems)
- Industrial electronics (process control, automation systems)
- Medical devices (diagnostic equipment, monitoring systems)
- Aerospace and defense (avionics, communication systems)
- Telecommunications (routers, switches, base stations)
- Internet of Things (IoT) devices (sensors, smart home devices)
The versatility and reliability of FR4 make it a popular choice for many electronic products and systems.
Comparing FR4 with other PCB Materials
While FR4 is the most common PCB material, there are other materials available for specific applications and requirements. Some of these materials include:
Material | Characteristics | Applications |
---|---|---|
Polyimide | High temperature resistance, flexibility | Aerospace, military, high-temperature electronics |
Rogers | Low dielectric loss, high-frequency performance | RF/microwave devices, antennas, radars |
Ceramic | Excellent thermal conductivity, high-frequency performance | High-power electronics, LED lighting |
Aluminum | Good thermal conductivity, lightweight | Heat sinks, LED lighting, automotive electronics |
Compared to these materials, FR4 offers a balanced combination of properties, wide availability, and cost-effectiveness, making it suitable for a broad range of PCB applications.
Manufacturing Process of FR4 PCBs
The manufacturing process of FR4 PCBs typically involves the following steps:
- Designing the PCB layout using CAD software
- Printing the PCB artwork onto a photoresist film
- Laminating the FR4 substrate with copper foil
- Exposing the photoresist to UV light through the artwork
- Developing the photoresist to reveal the copper pattern
- Etching away the unwanted copper using a chemical solution
- Drilling holes for through-hole components and vias
- Applying solder mask and silkscreen for protection and labeling
- Surface finishing (e.g., HASL, ENIG, OSP) for improved solderability
- Electrical testing and quality inspection
By following these steps, manufacturers can produce high-quality FR4 PCBs that meet the required specifications and standards.
Choosing the Right FR4 Grade
FR4 is available in different grades based on the specific requirements of the application. Some common FR4 Grades include:
- Standard FR4: Suitable for general-purpose PCBs with operating temperatures up to 130°C
- High Tg FR4: Offers better thermal stability and higher glass transition temperature (up to 170°C)
- Halogen-free FR4: Environmentally friendly option without halogenated flame retardants
- Controlled impedance FR4: Designed for high-speed digital and RF applications with specific impedance requirements
When selecting the appropriate FR4 grade, consider factors such as the operating temperature range, environmental conditions, electrical requirements, and regulatory compliance.
FAQ
- Is FR4 suitable for high-frequency applications?
-
Yes, FR4 is suitable for many high-frequency applications up to several gigahertz. However, for extremely high frequencies or low-loss requirements, specialized materials like Rogers may be more appropriate.
-
Can FR4 PCBs be used in harsh environments?
-
FR4 PCBs can withstand a wide range of environmental conditions, including temperature variations, humidity, and vibrations. However, for extreme conditions, such as high temperatures or exposure to harsh chemicals, other materials like polyimide may be more suitable.
-
How does the thickness of FR4 affect PCB performance?
-
The thickness of FR4 can impact the mechanical strength, thermal dissipation, and electrical properties of the PCB. Thicker FR4 boards offer better mechanical stability and thermal dissipation but may increase the overall weight and cost. Thinner FR4 boards are lighter and more flexible but may be more susceptible to warping and damage.
-
Can FR4 PCBs be recycled?
-
Yes, FR4 PCBs can be recycled to recover valuable materials like copper and precious metals. However, the recycling process is complex and requires specialized facilities to properly separate and process the materials.
-
What are the limitations of using FR4 for PCBs?
- While FR4 is a versatile and reliable material, it does have some limitations. FR4 may not be suitable for extremely high-temperature applications (above 130°C) or applications that require very low dielectric loss or high thermal conductivity. In such cases, alternative materials like polyimide, ceramic, or metal-core PCBs may be more appropriate.
Conclusion
FR4 is the most widely used material for PCB manufacturing due to its excellent combination of mechanical, electrical, and thermal properties. Its durability, reliability, cost-effectiveness, and versatility make it suitable for a wide range of applications across various industries. When selecting FR4 for your PCB project, consider the specific requirements of your application, such as operating temperature, environmental conditions, and electrical performance, to choose the appropriate grade and thickness. By understanding the properties and advantages of FR4, you can make informed decisions and create high-quality, reliable PCBs for your electronic products and systems.
No responses yet