What is a PCB?
A Printed Circuit Board (PCB) is a flat board made of insulating material, such as fiberglass or composite epoxy, with conductive copper tracks printed or etched onto its surface. These copper tracks form the electrical connections between the various components mounted on the board, such as resistors, capacitors, integrated circuits, and connectors.
PCBs come in various types, depending on the number of conductive layers and the manufacturing process used:
PCB Type | Description |
---|---|
Single-sided | Has conductive tracks on one side of the board |
Double-sided | Has conductive tracks on both sides of the board |
Multi-layer | Has multiple layers of conductive tracks separated by insulating layers |
Flexible | Made of flexible materials, allowing the board to bend and flex |
Rigid-Flex | Combines rigid and flexible sections in a single board |
Benefits of Using PCBs
1. Compact and Space-saving Design
One of the primary advantages of using PCBs is their ability to accommodate a large number of electronic components in a compact space. By using a PCB, designers can create smaller, more streamlined devices that are easier to manufacture and transport. This is particularly important in today’s world, where consumers demand smaller, more portable electronic devices.
2. Increased Reliability
PCBs offer a much higher level of reliability compared to traditional point-to-point wiring methods. The copper tracks on a PCB are designed to maintain their integrity even under harsh environmental conditions, such as high temperatures, humidity, and vibration. Additionally, the use of automated manufacturing processes ensures consistent quality and reduces the risk of human error.
3. Improved Signal Integrity
PCBs are designed to minimize signal interference and crosstalk between different components. By carefully routing the copper tracks and using appropriate shielding techniques, designers can ensure that signals remain clear and undistorted. This is particularly important in high-frequency applications, such as wireless communication devices and high-speed digital circuits.
4. Simplified Assembly and Maintenance
Using PCBs greatly simplifies the assembly process for electronic devices. Components can be easily soldered onto the board using automated pick-and-place machines, reducing the time and labor required for manual assembly. Furthermore, PCBs make it easier to locate and replace faulty components during maintenance, as each component has a designated location on the board.
5. Cost-effective Mass Production
PCBs are ideal for mass production, as the manufacturing process can be automated and optimized for high volumes. Once the initial design and setup costs are covered, the cost per unit decreases significantly as production volume increases. This makes PCBs an economical choice for large-scale electronic projects.
Production Volume | Cost per Unit |
---|---|
Low (1-100) | High |
Medium (101-1000) | Moderate |
High (1000+) | Low |
6. Customizable and Flexible Design
PCBs offer a high degree of design flexibility, allowing engineers to create custom layouts tailored to their specific requirements. With the help of advanced PCB design software, designers can easily create complex multi-layer boards, incorporate unique shapes and sizes, and optimize component placement for optimal performance.
7. Enhanced Thermal Management
PCBs play a crucial role in managing the heat generated by electronic components. By using thermally conductive materials and incorporating heat-dissipating features such as thermal vias and heat sinks, PCBs can effectively transfer heat away from sensitive components, ensuring stable operation and prolonging the lifespan of the device.
8. Reduced Electromagnetic Interference (EMI)
Properly designed PCBs can help minimize electromagnetic interference (EMI) emitted by electronic devices. By incorporating shielding techniques, such as ground planes and proper trace routing, designers can reduce the amount of EMI radiated by the board, ensuring compliance with electromagnetic compatibility (EMC) regulations.
9. Facilitates Automated Testing
PCBs are designed with testability in mind, making it easier to perform automated testing during the manufacturing process. Test points and pads can be incorporated into the board layout, allowing for quick and efficient testing of the assembled board using automated test equipment (ATE). This helps identify and rectify any manufacturing defects early in the production process, reducing the overall cost and time to market.
10. Enables Modular Design
PCBs facilitate modular design approaches, where complex systems are broken down into smaller, more manageable subsystems. Each subsystem can be designed and tested independently, allowing for parallel development and easier troubleshooting. Modular design also makes it easier to upgrade or replace specific subsystems without affecting the entire device.
FAQ
1. What materials are PCBs typically made of?
PCBs are typically made of an insulating substrate material, such as fiberglass (FR-4), composite epoxy, or polyimide. The conductive tracks are usually made of copper, which is laminated onto the substrate.
2. How are PCBs manufactured?
The PCB manufacturing process involves several steps, including:
1. Designing the PCB layout using specialized software
2. Printing the circuit pattern onto the substrate using photolithography
3. Etching away the unwanted copper to create the desired tracks
4. Drilling holes for component mounting and vias
5. Applying a protective solder mask and silkscreen layer
6. Testing the finished board for defects
3. What is the difference between through-hole and surface-mount PCBs?
Through-hole PCBs have components with long leads that are inserted into drilled holes in the board and soldered on the opposite side. Surface-mount PCBs have components that are soldered directly onto pads on the surface of the board. Surface-mount technology allows for smaller components and higher component density compared to through-hole mounting.
4. Can PCBs be recycled?
Yes, PCBs can be recycled to recover valuable materials such as copper, gold, and palladium. However, the recycling process is complex and requires specialized facilities to properly handle the hazardous materials present in PCBs, such as lead and brominated flame retardants.
5. What are the environmental concerns associated with PCBs?
The main environmental concerns associated with PCBs include:
– The use of hazardous materials, such as lead and brominated flame retardants
– The energy consumption and greenhouse gas emissions associated with PCB manufacturing
– The potential for improper disposal of end-of-life PCBs, leading to environmental contamination
To mitigate these concerns, the electronics industry is working towards developing more eco-friendly PCB Materials and processes, as well as improving PCB recycling infrastructure.
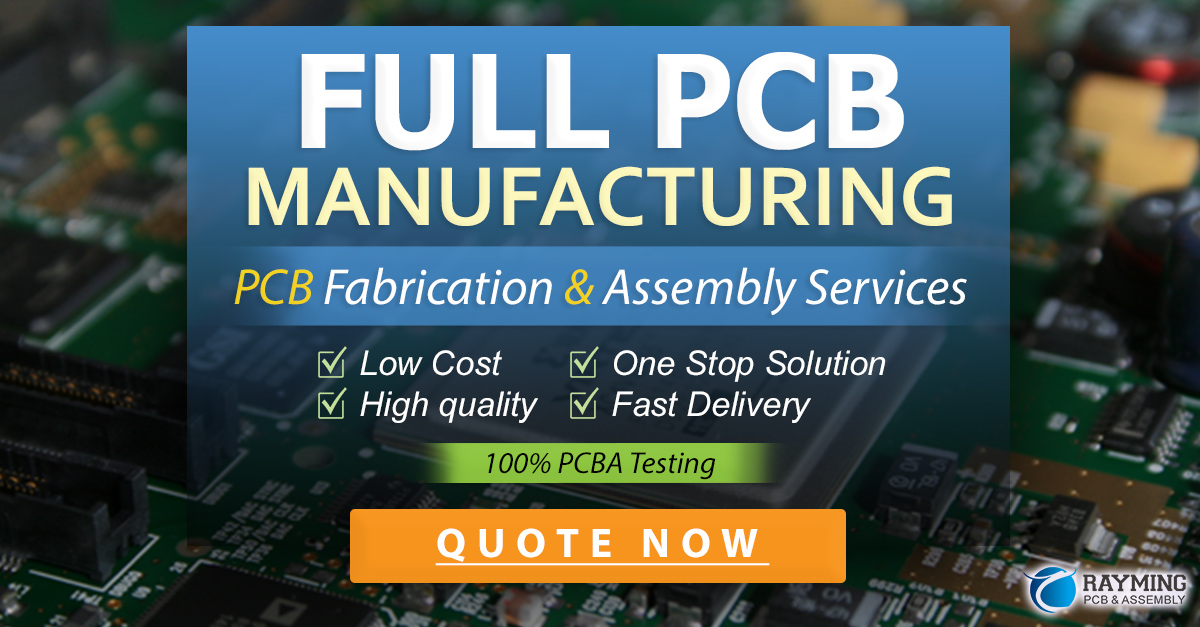
Conclusion
In conclusion, PCBs offer numerous benefits that make them an essential component in modern electronics. From their compact and reliable design to their cost-effectiveness in mass production, PCBs have revolutionized the way we design and manufacture electronic devices. As technology continues to advance, the importance of PCBs in enabling innovative and efficient electronic solutions will only continue to grow.
No responses yet