Understanding the Factors Contributing to PCB cost
Printed Circuit Boards (PCBs) are essential components in modern electronics, forming the backbone of countless devices we use every day. However, the cost of PCBs can vary significantly depending on various factors, leaving many wondering why they can be so expensive. In this article, we will explore the key elements that contribute to the cost of PCBs and provide insights into how these factors influence the final price.
The Complexity of PCB Design
One of the primary factors affecting PCB cost is the complexity of the design. As electronic devices become more sophisticated and compact, the demand for intricate PCB designs increases. Complex designs often require more layers, smaller trace widths, and tighter tolerances, which can drive up the cost of production.
Design Complexity | Impact on Cost |
---|---|
Simple (1-2 layers) | Low |
Moderate (4-6 layers) | Medium |
Complex (8+ layers) | High |
Creating a complex PCB design requires skilled engineers and advanced design software, both of which contribute to the overall cost. Additionally, the time and effort invested in the design process, including prototyping and testing, can further increase expenses.
Material Selection and Quality
The choice of materials used in PCB fabrication plays a significant role in determining the cost. High-quality materials, such as high-grade copper, specialized substrates, and advanced laminates, are more expensive than their standard counterparts. However, these premium materials offer superior performance, reliability, and durability, which are essential for critical applications.
Material | Cost | Performance |
---|---|---|
FR-4 | Low | Standard |
High-Tg FR-4 | Medium | Improved |
Polyimide | High | High-temperature |
Rogers | Very High | High-frequency |
Choosing the right materials for a PCB requires careful consideration of the intended application, environmental factors, and performance requirements. While opting for high-end materials can increase the cost, it is often necessary to ensure the long-term reliability and functionality of the final product.
Manufacturing Process and Technology
The manufacturing process and technology employed in PCB fabrication significantly influence the cost. Advanced manufacturing techniques, such as high-density interconnect (HDI) and microvia technology, enable the production of more complex and compact PCBs. However, these technologies require specialized equipment and expertise, leading to higher production costs.
Manufacturing Technology | Cost Impact |
---|---|
Through-hole | Low |
Surface Mount (SMT) | Medium |
High-Density Interconnect (HDI) | High |
Microvia | Very High |
Additionally, the level of automation in the manufacturing process can affect the cost. Highly automated production lines are more efficient and can handle larger volumes, but they require substantial initial investments. On the other hand, manual assembly and soldering processes are more labor-intensive and can increase labor costs, particularly in regions with higher wage rates.
Order Quantity and Economies of Scale
The quantity of PCBs ordered plays a crucial role in determining the cost per unit. Manufacturers often offer lower prices for larger order quantities due to economies of scale. The fixed costs associated with setting up the production line, such as tooling and programming, can be spread across a larger number of units, resulting in a lower cost per PCB.
Order Quantity | Cost per Unit |
---|---|
Prototype (1-10) | High |
Low Volume (100-500) | Medium |
High Volume (1000+) | Low |
For low-volume or prototype orders, the cost per PCB can be significantly higher due to the lack of economies of scale. In contrast, high-volume orders benefit from reduced fixed costs and can achieve much lower prices per unit.
Quality Control and Testing
Ensuring the quality and reliability of PCBs requires rigorous quality control measures and extensive testing. These processes add to the overall cost of PCB production. Quality control procedures may include visual inspections, automated optical inspection (AOI), X-ray inspection, and electrical testing.
Testing Method | Cost Impact |
---|---|
Visual Inspection | Low |
Automated Optical Inspection (AOI) | Medium |
X-ray Inspection | High |
Electrical Testing | Medium to High |
Thorough testing helps identify defects and ensures that the PCBs meet the required specifications and standards. While these quality control measures increase the cost, they are essential for preventing failures and ensuring the long-term reliability of the final product.
Lead Time and Expedited Services
The lead time, or the time required to manufacture and deliver the PCBs, can also impact the cost. Standard lead times for PCB production can range from several days to weeks, depending on the complexity of the design and the manufacturer’s workload.
Lead Time | Cost Impact |
---|---|
Standard (2-3 weeks) | Low |
Expedited (1 week) | Medium |
Rush (24-48 hours) | High |
Expedited or rush services, which prioritize the production and delivery of PCBs, often come at a premium price. These services are typically requested when time is of the essence, such as in urgent prototyping or product launches. The additional cost associated with expedited services reflects the resource allocation and prioritization required to meet the tight deadlines.
FAQ
-
Q: Why are complex PCB designs more expensive?
A: Complex PCB designs often require more layers, smaller trace widths, and tighter tolerances, which increase the manufacturing challenges and costs. Additionally, the design process itself is more time-consuming and requires skilled engineers and advanced software. -
Q: Can I reduce the cost of PCBs by using cheaper materials?
A: While using cheaper materials may lower the initial cost, it can compromise the performance, reliability, and durability of the PCBs. It is essential to choose materials that meet the specific requirements of the application to ensure long-term functionality and avoid costly failures. -
Q: How does the order quantity affect the cost of PCBs?
A: Larger order quantities generally result in lower costs per unit due to economies of scale. The fixed costs associated with setting up the production line can be spread across more units, reducing the cost per PCB. Prototype or low-volume orders typically have higher costs per unit. -
Q: Are there any ways to reduce the cost of PCBs without compromising quality?
A: Some strategies to reduce PCB costs include optimizing the design for manufacturability, choosing cost-effective materials that still meet performance requirements, and considering larger order quantities when feasible. Working closely with the PCB manufacturer and discussing cost-saving options can also help identify opportunities for cost reduction. -
Q: Why are expedited or rush services more expensive?
A: Expedited or rush services prioritize the production and delivery of PCBs, requiring manufacturers to allocate resources and prioritize the order over others. This special treatment and the need to meet tight deadlines often result in higher costs compared to standard lead times.
Conclusion
The cost of PCBs is influenced by a combination of factors, including design complexity, material selection, manufacturing technology, order quantity, quality control measures, and lead times. Understanding these factors allows designers and purchasers to make informed decisions when balancing cost, performance, and reliability.
While it may be tempting to opt for cheaper options to reduce costs, it is crucial to consider the long-term implications. Investing in high-quality materials, advanced manufacturing processes, and thorough testing can help ensure the durability and functionality of the final product, ultimately saving costs associated with failures and repairs.
By working closely with PCB manufacturers, optimizing designs for manufacturability, and carefully selecting materials and components, it is possible to strike a balance between cost and quality. Open communication and collaboration between designers, manufacturers, and stakeholders can lead to cost-effective solutions that meet the specific requirements of each project.
As technology continues to advance and the demand for high-performance electronics grows, the PCB industry will continue to evolve. Innovations in materials, manufacturing processes, and design tools may help drive down costs while maintaining or improving quality. Staying informed about these advancements and adapting to new technologies will be key to achieving cost-effective and reliable PCB solutions in the future.
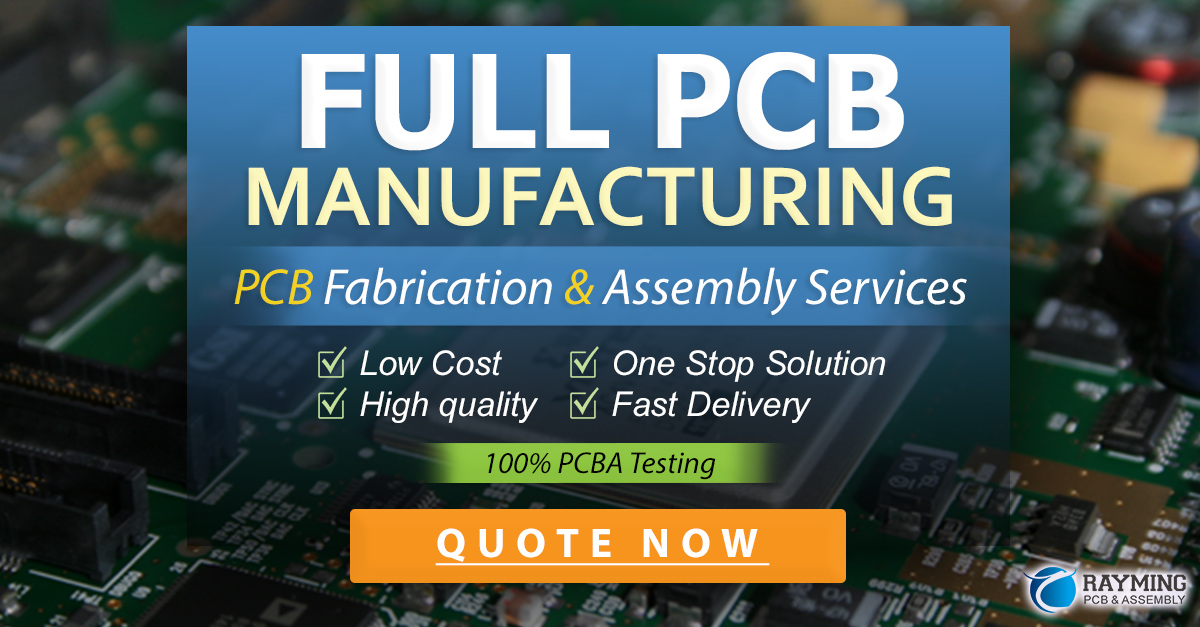
No responses yet