Introduction to PCB material
Printed Circuit Boards (PCBs) are essential components in modern electronics, providing a platform for interconnecting electronic components and creating complex circuits. The choice of PCB material is crucial as it determines the performance, reliability, and durability of the final product. Among various PCB materials available, FR4 has emerged as the most widely used and preferred choice for many applications. In this article, we will explore the reasons behind the popularity of FR4 material in PCB manufacturing and its key properties that make it suitable for a wide range of electronic applications.
What is FR4 Material?
FR4 (Flame Retardant 4) is a composite material composed of woven fiberglass cloth reinforced with an epoxy resin binder. The fiberglass provides mechanical strength and dimensional stability, while the epoxy resin offers excellent insulation properties and resistance to moisture and chemicals. FR4 is a type of laminate material that belongs to the family of glass-reinforced epoxy (GRE) laminates.
History and Development of FR4
The development of FR4 material can be traced back to the 1960s when the electronics industry was seeking a reliable and cost-effective PCB material. Prior to FR4, PCBs were commonly made using phenolic paper or other materials that had limitations in terms of performance and reliability. The introduction of FR4 revolutionized the PCB industry by offering a material with superior mechanical, electrical, and thermal properties.
Properties of FR4 Material
Mechanical Properties
One of the key reasons for the widespread use of FR4 in PCBs is its excellent mechanical properties. The combination of woven fiberglass and epoxy resin provides a strong and rigid structure that can withstand various mechanical stresses encountered during manufacturing, assembly, and operation. FR4 exhibits high tensile strength, flexural strength, and impact resistance, making it suitable for applications that require durability and reliability.
Property | Value |
---|---|
Tensile Strength | 310 MPa |
Flexural Strength | 415 MPa |
Compressive Strength | 415 MPa |
Density | 1.85 g/cm³ |
Electrical Properties
FR4 material possesses excellent electrical insulation properties, making it ideal for use in PCBs. The epoxy resin in FR4 acts as an effective insulator, preventing unwanted electrical conductivity between different layers and traces of the PCB. FR4 has a high dielectric strength, which means it can withstand high voltages without breakdown. Additionally, FR4 has a relatively low dielectric constant and dissipation factor, minimizing signal loss and ensuring signal integrity.
Property | Value |
---|---|
Dielectric Strength | 20 kV/mm |
Dielectric Constant (1 MHz) | 4.5 |
Dissipation Factor (1 MHz) | 0.02 |
Volume Resistivity | 10^14 Ω·cm |
Thermal Properties
FR4 material exhibits good thermal stability and resistance to high temperatures. It has a glass transition temperature (Tg) of around 130°C to 180°C, depending on the specific formulation. This means that FR4 can maintain its structural integrity and electrical properties even at elevated temperatures encountered during soldering and other manufacturing processes. FR4 also has a low coefficient of thermal expansion (CTE), reducing the risk of thermal stress and warpage in the PCB.
Property | Value |
---|---|
Glass Transition Temperature (Tg) | 130°C – 180°C |
Thermal Conductivity | 0.3 W/m·K |
Coefficient of Thermal Expansion (CTE) | 14 ppm/°C |
Maximum Operating Temperature | 130°C |
Chemical Resistance
FR4 material exhibits excellent chemical resistance, making it suitable for use in harsh environmental conditions. It is resistant to a wide range of chemicals, including acids, alkalis, solvents, and oils. This chemical resistance ensures that the PCB can withstand exposure to various substances during manufacturing, assembly, and operation without degradation or loss of performance.
Advantages of Using FR4 in PCBs
Cost-Effectiveness
One of the primary reasons for the widespread adoption of FR4 in PCB manufacturing is its cost-effectiveness. FR4 is readily available and can be produced in large quantities at a relatively low cost compared to other specialized PCB materials. The raw materials used in FR4 production, such as fiberglass and epoxy resin, are abundant and economical. Additionally, the well-established manufacturing processes for FR4 PCBs contribute to its cost-effectiveness.
Versatility and Compatibility
FR4 material is highly versatile and compatible with a wide range of electronic components and manufacturing processes. It can accommodate various copper thicknesses and trace widths, enabling the design of complex circuits with high component density. FR4 is compatible with standard PCB fabrication techniques, including drilling, etching, and plating. It also works well with different surface finishes, such as HASL (Hot Air Solder Leveling), ENIG (Electroless Nickel Immersion Gold), and OSP (Organic Solderability Preservative).
Reliability and Durability
FR4 PCBs are known for their reliability and durability, making them suitable for a wide range of applications. The combination of strong mechanical properties, excellent electrical insulation, and thermal stability ensures that FR4 PCBs can withstand the rigors of manufacturing, assembly, and long-term operation. FR4 PCBs have a proven track record of reliability in various industries, including consumer electronics, automotive, aerospace, and medical devices.
Flame Retardancy
The “FR” in FR4 stands for “Flame Retardant,” indicating that the material has inherent flame-retardant properties. FR4 is designed to meet the UL94 V-0 flammability rating, which means it has excellent resistance to ignition and flame spread. This flame retardancy is achieved through the use of brominated epoxy resins or other flame-retardant additives. The flame-retardant properties of FR4 are crucial for ensuring the safety and reliability of electronic devices, particularly in applications where fire hazards are a concern.
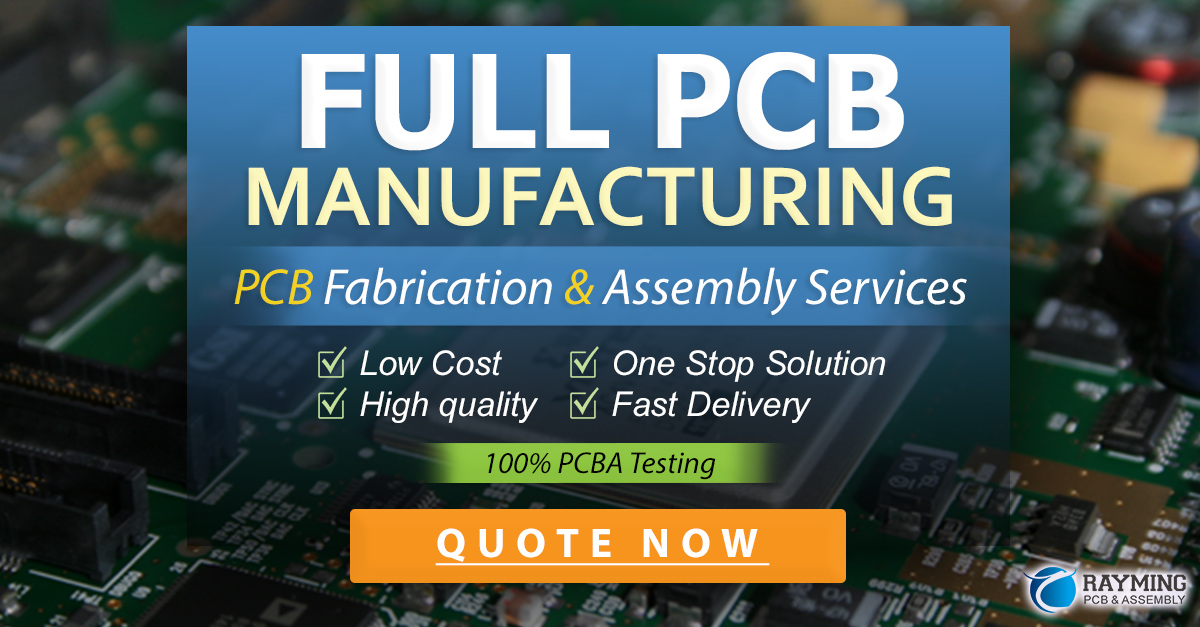
Applications of FR4 PCBs
Consumer Electronics
FR4 PCBs are extensively used in consumer electronics, such as smartphones, tablets, laptops, televisions, and home appliances. The cost-effectiveness, reliability, and versatility of FR4 make it an ideal choice for mass-produced consumer products. FR4 PCBs can handle the high-density interconnects and complex circuitry required in modern electronic devices while providing the necessary mechanical strength and durability.
Industrial Electronics
FR4 PCBs find wide applications in industrial electronics, including control systems, automation equipment, power supplies, and instrumentation. The robustness and reliability of FR4 make it suitable for harsh industrial environments where the PCBs may be exposed to vibrations, shock, and extreme temperatures. FR4 PCBs can withstand the demands of continuous operation and provide long-term reliability in industrial settings.
Automotive Electronics
The automotive industry relies heavily on FR4 PCBs for various electronic systems, such as engine control units (ECUs), infotainment systems, and advanced driver assistance systems (ADAS). FR4 PCBs offer the necessary reliability, thermal stability, and vibration resistance required in automotive applications. They can withstand the harsh environmental conditions encountered in vehicles, including temperature fluctuations, humidity, and exposure to chemicals and fluids.
Medical Devices
FR4 PCBs are commonly used in medical devices, including diagnostic equipment, patient monitoring systems, and implantable devices. The biocompatibility, reliability, and electrical insulation properties of FR4 make it suitable for medical applications. FR4 PCBs can meet the stringent regulatory requirements and standards for medical devices, ensuring patient safety and device performance.
Aerospace and Defense
FR4 PCBs find applications in aerospace and defense systems, such as avionics, communication equipment, and military electronics. The thermal stability, mechanical strength, and flame retardancy of FR4 are crucial for these demanding applications. FR4 PCBs can withstand the harsh environmental conditions encountered in aerospace and defense systems, including high altitudes, extreme temperatures, and exposure to radiation.
Challenges and Limitations of FR4
While FR4 is widely used and offers numerous advantages, it also has some limitations and challenges that need to be considered when designing and manufacturing PCBs.
High-Frequency Performance
FR4 material has limitations in terms of high-frequency performance. As the operating frequencies of electronic devices continue to increase, the dielectric properties of FR4 can lead to signal integrity issues and higher losses. For high-frequency applications, such as RF (radio frequency) and microwave circuits, specialized PCB materials with lower dielectric constants and dissipation factors, such as Rogers or Teflon, may be preferred over FR4.
Thermal Management
Although FR4 has good thermal stability, it has relatively low thermal conductivity compared to other PCB materials like aluminum or copper. This can pose challenges in applications with high power dissipation or heat generation. Proper thermal management techniques, such as using thermal vias, heatsinks, or fans, may be necessary to dissipate heat effectively and prevent thermal-related failures in FR4 PCBs.
Moisture Absorption
FR4 material can absorb moisture from the environment, which can lead to various issues. Moisture absorption can cause the PCB to expand and contract, resulting in warpage or dimensional changes. It can also degrade the electrical properties of the PCB and potentially lead to delamination or other reliability issues. Proper handling, storage, and moisture control measures are essential to mitigate the effects of moisture absorption in FR4 PCBs.
Thickness Limitations
FR4 PCBs have limitations in terms of the minimum achievable thickness. While thin FR4 laminates are available, they may not be suitable for certain applications that require extreme thinness or flexibility. In such cases, alternative PCB materials like polyimide or flexible substrates may be more appropriate.
Future Trends and Developments
As the electronics industry continues to evolve, there is ongoing research and development to improve the performance and capabilities of FR4 PCBs. Some of the future trends and developments in FR4 technology include:
High-Speed Materials
Efforts are being made to develop FR4 variants with improved high-frequency performance. This includes the development of low-loss FR4 materials with lower dielectric constants and dissipation factors. These materials aim to address the limitations of standard FR4 in high-speed applications and enable the design of PCBs for higher operating frequencies.
Halogen-Free FR4
There is a growing trend towards the use of halogen-free FR4 materials in response to environmental and health concerns. Traditional FR4 laminates often contain brominated flame retardants, which can release harmful substances during manufacturing or disposal. Halogen-free FR4 alternatives use non-halogenated flame retardants, providing a more environmentally friendly option without compromising the flame-retardant properties.
Embedded Components
The integration of embedded components within the FR4 PCB substrate is an emerging trend. Embedded components, such as resistors, capacitors, and inductors, are placed inside the PCB Layers instead of being mounted on the surface. This approach offers several advantages, including reduced board size, improved signal integrity, and enhanced reliability. Embedded component technology in FR4 PCBs is expected to gain traction in the coming years.
Advanced Manufacturing Techniques
Advancements in PCB manufacturing techniques are also influencing the future of FR4 PCBs. technologies like 3D printing, laser drilling, and plasma etching are being explored to enhance the capabilities and precision of FR4 PCB fabrication. These advanced manufacturing techniques can enable the creation of complex structures, finer features, and higher-density interconnects in FR4 PCBs.
Frequently Asked Questions (FAQ)
-
What does FR4 stand for?
FR4 stands for “Flame Retardant 4,” indicating that the material has inherent flame-retardant properties and meets the UL94 V-0 flammability rating. -
Is FR4 suitable for high-frequency applications?
While FR4 is widely used, it has limitations in terms of high-frequency performance. For high-frequency applications, specialized PCB materials with lower dielectric constants and dissipation factors may be preferred over FR4. -
Can FR4 PCBs be used in harsh environmental conditions?
Yes, FR4 PCBs are known for their reliability and durability. They can withstand various environmental conditions, including temperature fluctuations, humidity, and exposure to chemicals and fluids, making them suitable for applications in harsh environments. -
How does moisture affect FR4 PCBs?
Moisture absorption can cause FR4 PCBs to expand and contract, resulting in warpage or dimensional changes. It can also degrade the electrical properties of the PCB and potentially lead to delamination or other reliability issues. Proper handling and storage measures are necessary to mitigate the effects of moisture absorption. -
Are there environmentally friendly alternatives to traditional FR4?
Yes, there is a growing trend towards the use of halogen-free FR4 materials. These alternatives use non-halogenated flame retardants, providing a more environmentally friendly option without compromising the flame-retardant properties of the PCB.
Conclusion
FR4 material has become the de facto standard for PCB manufacturing due to its excellent combination of mechanical, electrical, and thermal properties. Its cost-effectiveness, versatility, and reliability have made it the preferred choice for a wide range of electronic applications, from consumer electronics to industrial systems and beyond.
The advantages of FR4, including its strength, dimensional stability, electrical insulation, and flame retardancy, have contributed to its widespread adoption in the electronics industry. However, it is important to consider the limitations and challenges associated with FR4, such as its high-frequency performance and thermal management considerations.
As the electronics landscape continues to evolve, ongoing research and development efforts are focused on improving the performance and capabilities of FR4 PCBs. Developments in high-speed materials, halogen-free alternatives, embedded components, and advanced manufacturing techniques are shaping the future of FR4 technology.
By understanding the properties, advantages, and limitations of FR4 material, engineers and designers can make informed decisions when selecting PCB materials for their specific applications. The versatility and reliability of FR4 have made it a cornerstone of the electronics industry, and it is likely to continue playing a vital role in the development of innovative and reliable electronic products in the years to come.
No responses yet