Introduction to PCB substrates
Printed Circuit Boards (PCBs) are essential components in modern electronic devices, serving as the foundation for mounting and interconnecting electronic components. The choice of substrate material plays a crucial role in determining the performance, reliability, and cost of a PCB. Among the various substrate materials available, FR4 has emerged as the most widely used and preferred choice for PCB manufacturing. In this article, we will explore the reasons behind the popularity of FR4 as a PCB substrate and its key properties that make it suitable for a wide range of applications.
What is FR4?
FR4 (Flame Retardant 4) is a composite material composed of woven fiberglass cloth impregnated with an epoxy resin binder. The “FR” in FR4 stands for “Flame Retardant,” indicating its inherent property to resist the spread of flames and self-extinguish when exposed to fire. The number “4” represents the specific grade of flame retardancy, which is determined by the Underwriters Laboratories (UL) 94V-0 flammability test.
Composition of FR4
The two main components of FR4 are:
-
Fiberglass Cloth: The fiberglass cloth provides mechanical strength and dimensional stability to the substrate. It is typically woven in a plain or twill pattern, with the fibers oriented in a 0°/90° or 45°/45° configuration.
-
Epoxy Resin: The epoxy resin acts as a binder, holding the fiberglass cloth together and providing insulation between the conductive layers of the PCB. The epoxy resin is a thermosetting polymer that cures (hardens) when subjected to heat and pressure during the manufacturing process.
Manufacturing Process of FR4
The manufacturing process of FR4 involves several steps:
-
Impregnation: The fiberglass cloth is impregnated with the epoxy resin, ensuring thorough saturation and even distribution of the resin throughout the fabric.
-
Drying: The impregnated fiberglass cloth is then dried to remove excess moisture and solvents.
-
Cutting: The dried sheets are cut to the desired size and shape based on the PCB design requirements.
-
Lamination: Multiple layers of the impregnated fiberglass cloth are stacked together with copper foils on the top and bottom surfaces. The stack is then subjected to high temperature and pressure in a lamination press, causing the epoxy resin to flow and bond the layers together.
-
Curing: The laminated board undergoes a curing process, where the epoxy resin crosslinks and hardens, resulting in a solid and stable substrate.
Key Properties of FR4
FR4 possesses several key properties that make it an ideal choice for PCB substrates:
1. Electrical Properties
FR4 exhibits excellent electrical insulation properties, making it suitable for use in high-frequency and high-voltage applications. Its dielectric constant (Dk) typically ranges from 4.2 to 4.6 at 1 MHz, and its dissipation factor (Df) is usually below 0.02 at 1 MHz. These properties ensure minimal signal loss and distortion, especially in high-speed digital circuits.
Property | Value |
---|---|
Dielectric Constant (Dk) | 4.2 to 4.6 (at 1 MHz) |
Dissipation Factor (Df) | < 0.02 (at 1 MHz) |
Dielectric Strength | > 40 kV/mm |
Volume Resistivity | > 10^8 MΩ·cm |
Surface Resistivity | > 10^8 MΩ |
2. Mechanical Properties
FR4 offers excellent mechanical strength and dimensional stability, making it resistant to warping, twisting, and bending. Its high tensile strength and modulus of elasticity ensure that the PCB can withstand various mechanical stresses during assembly and operation. Additionally, FR4 has a low coefficient of thermal expansion (CTE), which minimizes the risk of thermal stress-induced failures.
Property | Value |
---|---|
Tensile Strength | 310 to 380 MPa |
Flexural Strength | 415 to 480 MPa |
Modulus of Elasticity | 17 to 24 GPa |
Compressive Strength | 415 to 480 MPa |
Coefficient of Thermal Expansion | 14 to 16 ppm/°C |
3. Thermal Properties
FR4 has good thermal stability and can withstand temperatures up to 130°C (266°F) continuously and 180°C (356°F) for short periods. This thermal resistance allows FR4 to be used in applications with high operating temperatures and enables it to withstand the soldering process during PCB Assembly.
Property | Value |
---|---|
Glass Transition Temperature (Tg) | 130 to 140°C |
Decomposition Temperature | > 300°C |
Thermal Conductivity | 0.3 to 0.4 W/(m·K) |
Specific Heat Capacity | 1.1 to 1.3 J/(g·K) |
4. Chemical Resistance
FR4 exhibits excellent chemical resistance, making it suitable for use in harsh environmental conditions. It is resistant to most acids, alkalis, and solvents commonly encountered in electronic applications. This chemical resistance ensures the long-term reliability and durability of the PCB.
5. Flame Retardancy
As mentioned earlier, FR4 is inherently flame retardant, meeting the UL 94V-0 flammability rating. This property is crucial for ensuring the safety of electronic devices and preventing the spread of fire in case of electrical faults or overheating.
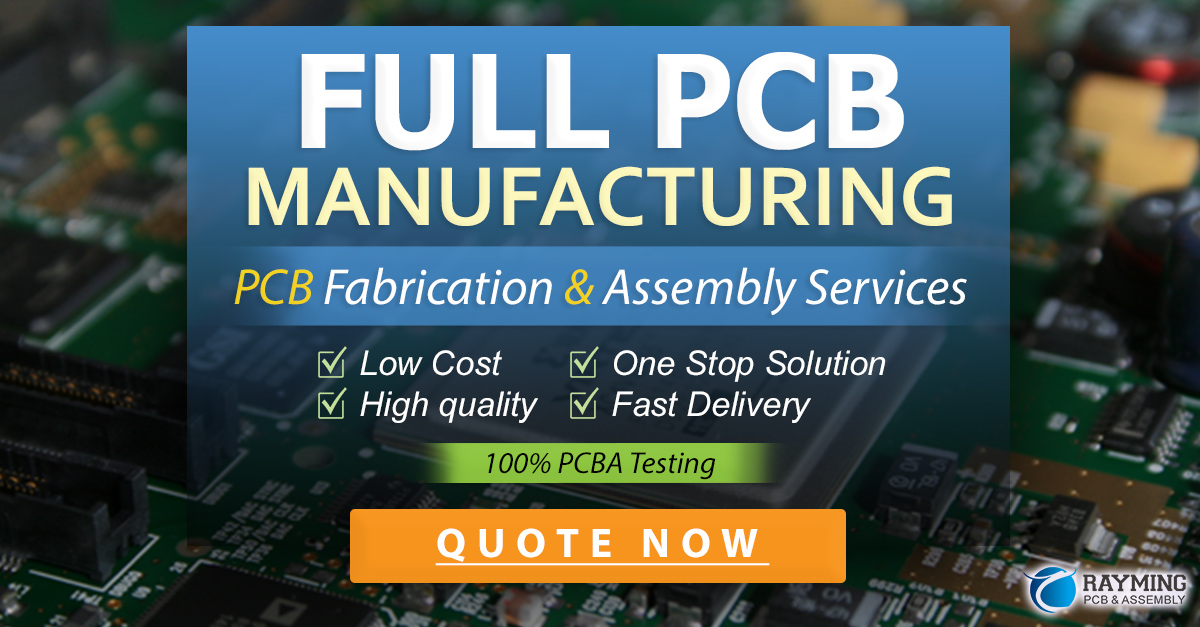
Applications of FR4 PCBs
FR4 PCBs find applications in a wide range of industries and electronic devices, including:
- Consumer Electronics: Smartphones, tablets, laptops, televisions, and home appliances.
- Automotive Electronics: Engine control units (ECUs), infotainment systems, and sensors.
- Telecommunications: Routers, switches, base stations, and networking equipment.
- Industrial Electronics: Process control systems, automation equipment, and power electronics.
- Medical Devices: Diagnostic equipment, patient monitoring systems, and implantable devices.
- Aerospace and Defense: Avionics systems, radar, and satellite communication equipment.
Advantages of Using FR4 as a PCB Substrate
- Cost-effective: FR4 is widely available and relatively inexpensive compared to other high-performance substrate materials.
- Versatile: FR4 can be used for a wide range of applications, from simple single-layer boards to complex multilayer PCBs.
- Reliable: FR4 offers excellent electrical, mechanical, and thermal properties, ensuring the reliability and durability of the PCB.
- Easy to manufacture: FR4 is compatible with standard PCB manufacturing processes, such as drilling, etching, and plating.
- Flame retardant: FR4’s inherent flame retardancy enhances the safety of electronic devices and complies with industry safety standards.
Limitations of FR4
While FR4 is an excellent choice for most PCB applications, it does have some limitations:
- High-frequency performance: FR4’s dielectric properties may not be suitable for extremely high-frequency applications (above 10 GHz) due to increased signal loss and dispersion.
- Thermal conductivity: FR4 has relatively low thermal conductivity compared to metal-core substrates, which can be a limitation in high-power applications that require efficient heat dissipation.
- Moisture absorption: FR4 can absorb moisture, which can lead to changes in its dielectric properties and dimensional stability over time. This can be mitigated by applying conformal coatings or using moisture-resistant variants of FR4.
Frequently Asked Questions (FAQ)
-
Q: What does FR4 stand for?
A: FR4 stands for “Flame Retardant 4,” indicating its inherent property to resist the spread of flames and self-extinguish when exposed to fire. -
Q: What is the difference between FR4 and other PCB substrate materials?
A: FR4 offers a balance of good electrical, mechanical, and thermal properties at a relatively low cost compared to other substrate materials. It is also widely available and compatible with standard PCB manufacturing processes. -
Q: Can FR4 be used for high-frequency applications?
A: FR4 is suitable for most high-frequency applications up to 10 GHz. However, for extremely high-frequency applications (above 10 GHz), other substrate materials with better high-frequency performance, such as Rogers or PTFE-based laminates, may be preferred. -
Q: Is FR4 environmentally friendly?
A: FR4 is made from fiberglass and epoxy resin, which are not biodegradable. However, efforts are being made to develop more environmentally friendly alternatives, such as halogen-free flame retardants and bio-based epoxy resins. -
Q: How does the thickness of FR4 affect PCB performance?
A: The thickness of FR4 influences the electrical, mechanical, and thermal properties of the PCB. Thinner FR4 substrates offer better high-frequency performance and flexibility but may be more susceptible to mechanical stress and warping. Thicker FR4 substrates provide better mechanical stability and thermal dissipation but may have higher signal loss and cost.
Conclusion
FR4 has become the most widely used PCB substrate material due to its excellent balance of electrical, mechanical, and thermal properties, coupled with its cost-effectiveness and wide availability. Its flame retardancy, chemical resistance, and compatibility with standard PCB manufacturing processes make it a versatile choice for a broad range of electronic applications.
While FR4 may have some limitations in terms of high-frequency performance and thermal conductivity, it remains the go-to choice for most PCB designs. As the electronics industry continues to evolve, FR4 is expected to maintain its dominant position as the primary PCB substrate material, with ongoing research and development efforts aimed at further enhancing its properties and addressing its limitations.
No responses yet