Introduction to PCB and its Benefits
Printed Circuit Boards (PCBs) have revolutionized the electronics industry since their inception in the 1930s. PCBs are the backbone of modern electronic devices, providing a reliable and efficient means of connecting electronic components. In this article, we will explore the various benefits of PCBs and why they are essential in today’s world.
What is a PCB?
A PCB is a flat board made of insulating material, typically fiberglass or composite epoxy, with conductive copper traces printed on one or both sides. These traces connect the various electronic components mounted on the board, such as resistors, capacitors, transistors, and integrated circuits. PCBs can be single-sided, double-sided, or multi-layered, depending on the complexity of the circuit.
The Evolution of PCBs
The first PCBs were developed in the 1930s by Austrian engineer Paul Eisler. However, it wasn’t until the 1950s that PCBs gained widespread adoption in the electronics industry. The introduction of through-hole technology, which involved drilling holes in the board and inserting component leads, made PCBs more reliable and easier to manufacture.
In the 1960s, surface-mount technology (SMT) was introduced, allowing components to be directly soldered onto the surface of the PCB. This development led to smaller, more compact PCBs and paved the way for the miniaturization of electronic devices.
Today, PCBs are an integral part of virtually every electronic device, from smartphones and laptops to medical equipment and aerospace systems.
The Key Benefits of PCBs
1. Compact and Space-saving Design
One of the primary advantages of PCBs is their ability to accommodate a large number of electronic components in a compact space. By utilizing both sides of the board and incorporating multi-layer designs, PCBs can significantly reduce the overall size of electronic devices. This space-saving feature is particularly important in applications where size and weight are critical factors, such as in mobile devices, wearables, and aerospace systems.
2. Enhanced Reliability and Durability
PCBs offer superior reliability and durability compared to traditional point-to-point wiring. The copper traces on a PCB are designed to withstand the stresses of everyday use, such as vibration, shock, and temperature fluctuations. Additionally, the insulating material used in PCBs provides excellent electrical insulation, preventing short circuits and other electrical faults.
The robust construction of PCBs also contributes to their longevity. With proper design and manufacturing techniques, PCBs can last for decades, even in harsh environmental conditions. This long-term reliability is essential in applications where failure is not an option, such as in medical devices, automotive systems, and industrial control equipment.
3. Improved Electrical Performance
PCBs offer several advantages in terms of electrical performance. The copper traces on a PCB are designed to minimize electrical resistance, ensuring efficient power distribution and signal integrity. This is particularly important in high-frequency applications, where signal loss and distortion can be significant issues.
PCBs also allow for the implementation of various techniques to improve electrical performance, such as:
- Ground planes: A continuous copper layer on one or both sides of the PCB that serves as a low-impedance return path for electrical currents, reducing electromagnetic interference (EMI) and improving signal quality.
- Controlled impedance: The ability to precisely control the impedance of the copper traces on a PCB, ensuring proper matching between the signal source and the load, minimizing reflections and signal distortion.
- Shielding: The use of conductive materials, such as copper or aluminum, to create barriers that protect sensitive electronic components from external electromagnetic interference (EMI) and radio frequency interference (RFI).
These techniques, along with careful PCB layout and design, can significantly enhance the electrical performance of electronic devices, resulting in better signal integrity, reduced noise, and improved overall system reliability.
4. Cost-effective Manufacturing
PCBs have made the mass production of electronic devices more cost-effective than ever before. The automated manufacturing processes used in PCB fabrication, such as pick-and-place machines and reflow soldering, allow for high-volume production at a relatively low cost per unit.
The use of standardized components and PCB design tools also contributes to cost savings. By utilizing off-the-shelf components and pre-designed PCB templates, manufacturers can reduce development time and costs, enabling faster time-to-market for new products.
Furthermore, the modular nature of PCBs allows for easy maintenance and repair. In the event of a component failure, the affected component can be easily replaced without the need to replace the entire PCB or device. This modularity not only reduces repair costs but also extends the overall lifespan of electronic devices.
5. Facilitates Miniaturization and Integration
PCBs have played a crucial role in the miniaturization of electronic devices. The ability to accommodate a large number of components in a compact space has enabled the development of ever-smaller and more powerful devices, such as smartphones, smartwatches, and medical implants.
In addition to miniaturization, PCBs also facilitate the integration of multiple functions into a single device. By combining various electronic subsystems, such as power management, wireless communication, and sensor interfaces, onto a single PCB, designers can create highly integrated and multifunctional devices. This integration not only saves space but also improves overall system reliability and performance.
The trend towards miniaturization and integration is expected to continue as PCB technology advances. The development of embedded components, such as passive components and active devices, directly integrated into the PCB substrate, will further push the boundaries of miniaturization and enable the creation of even smaller and more sophisticated electronic devices.
6. Enables Rapid Prototyping and Iteration
PCBs have revolutionized the product development process by enabling rapid prototyping and iteration. With the help of PCB design software and rapid prototyping services, designers can quickly create and test new PCB designs, allowing for faster identification and resolution of design issues.
The availability of low-cost, quick-turn PCB fabrication services has made it possible for even small businesses and individual inventors to bring their ideas to life. By iterating through multiple PCB revisions, designers can refine their designs and optimize performance, ensuring that the final product meets or exceeds the desired specifications.
This rapid prototyping capability has also accelerated innovation in the electronics industry. By reducing the time and cost associated with product development, PCBs have lowered the barriers to entry for new players and encouraged experimentation with novel designs and technologies.
PCB Design Considerations and Best Practices
To fully realize the benefits of PCBs, it is essential to follow best practices in PCB design and manufacturing. Some key considerations include:
1. Component Placement and Routing
Proper component placement and routing are critical for ensuring optimal electrical performance and manufacturability. Components should be placed in a logical and organized manner, with consideration for signal integrity, power distribution, and thermal management. Routing should be designed to minimize signal crosstalk, impedance mismatch, and electromagnetic interference (EMI).
2. Material Selection
The choice of PCB material can have a significant impact on the performance and reliability of the final product. Factors to consider when selecting PCB materials include:
- Dielectric constant: The ability of the material to store electrical energy, which affects signal propagation speed and impedance.
- Loss tangent: A measure of the material’s ability to dissipate energy, which affects signal attenuation and heat generation.
- Thermal conductivity: The ability of the material to conduct heat, which is important for thermal management and preventing component overheating.
- Mechanical strength: The material’s ability to withstand physical stresses, such as vibration and impact.
Common PCB materials include FR-4, a glass-reinforced epoxy laminate, and high-frequency laminates, such as Rogers and Isola materials, which offer superior electrical performance for high-speed applications.
3. Design for Manufacturing (DFM)
Design for Manufacturing (DFM) is a set of guidelines and best practices that ensure PCBs can be efficiently and reliably manufactured. DFM considerations include:
- Minimum trace width and spacing: Ensuring that the copper traces on the PCB are wide enough and spaced far enough apart to be reliably manufactured and to prevent short circuits.
- Drill hole size and spacing: Specifying the minimum drill hole size and spacing to ensure proper plating and prevent drill breakage during manufacturing.
- Solder mask and silkscreen: Properly designing the solder mask and silkscreen layers to protect the PCB from environmental factors and provide clear component labeling.
By adhering to DFM guidelines, designers can minimize manufacturing defects, improve yields, and reduce overall production costs.
4. Testing and Quality Control
Rigorous testing and quality control are essential for ensuring the reliability and performance of PCBs. Common testing methods include:
- In-circuit testing (ICT): A method of testing the functionality of individual components and the interconnections between them using a bed-of-nails fixture.
- Flying probe testing: A non-contact testing method that uses movable probes to test the electrical continuity and functionality of the PCB.
- Boundary scan testing: A testing method that uses a special test access port (TAP) to test the interconnections and functionality of complex digital circuits, such as microprocessors and FPGAs.
- Functional testing: A method of testing the overall functionality of the PCB and ensuring that it meets the desired specifications.
By implementing a comprehensive testing and quality control program, manufacturers can identify and correct defects early in the production process, reducing the risk of field failures and improving overall product quality.
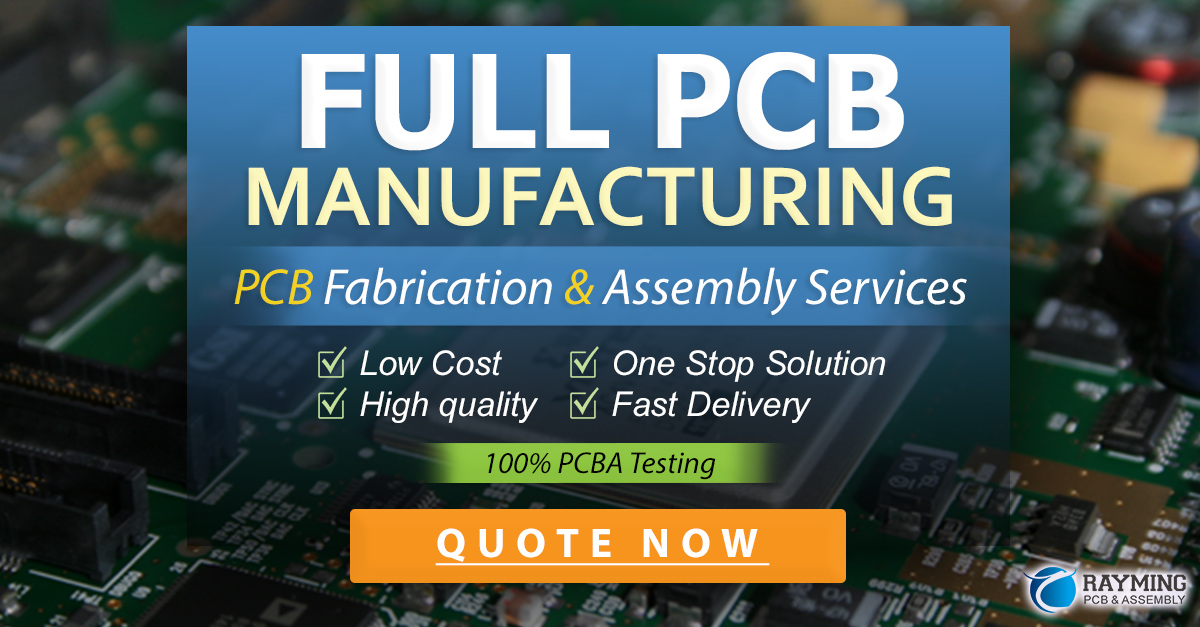
The Future of PCB Technology
As the electronics industry continues to evolve, so too will PCB technology. Some of the key trends and developments shaping the future of PCBs include:
1. Advanced Materials
The development of new, advanced materials is expected to drive innovation in PCB technology. These materials, such as graphene, carbon nanotubes, and ceramic composites, offer unique properties that can enhance the electrical, thermal, and mechanical performance of PCBs.
For example, graphene, a two-dimensional form of carbon, has exceptional electrical and thermal conductivity, making it a promising material for high-speed, low-loss PCBs. Similarly, ceramic composites offer excellent thermal stability and low dielectric loss, making them ideal for high-temperature and high-frequency applications.
2. 3D Printing
3D printing technology has the potential to revolutionize PCB manufacturing by enabling the creation of complex, three-dimensional PCB structures. By using conductive and insulating materials, 3D printers can fabricate PCBs with intricate geometries, embedded components, and customized form factors.
This technology could lead to the development of highly integrated, multifunctional devices that combine electronic, mechanical, and even biological components. 3D-printed PCBs could also enable faster prototyping and more agile manufacturing, allowing for greater customization and shorter lead times.
3. Flexible and Stretchable PCBs
The growing demand for wearable devices and flexible electronics is driving the development of flexible and stretchable PCBs. These PCBs are designed to bend, twist, and stretch without losing their electrical functionality, making them ideal for applications such as smart clothing, medical sensors, and soft robotics.
Flexible and stretchable PCBs are typically made using polymeric substrates, such as polyimide or PEEK, and conductive inks or thin metal foils. The development of new materials and fabrication techniques, such as inkjet printing and laser sintering, is expected to further advance the capabilities of flexible and stretchable PCBs.
4. High-Frequency and High-Speed PCBs
As data rates continue to increase and wireless communication technologies advance, the demand for high-frequency and high-speed PCBs is expected to grow. These PCBs are designed to support the transmission of signals at frequencies in the gigahertz range, enabling faster data transfer and processing.
To achieve these high frequencies, PCBs must be designed with careful consideration for signal integrity, impedance matching, and loss minimization. The use of advanced materials, such as low-loss laminates and high-conductivity copper, along with sophisticated design techniques, such as microstrip and stripline routing, will be essential for the development of next-generation high-frequency PCBs.
Frequently Asked Questions (FAQ)
1. What is the difference between a single-sided, double-sided, and multi-layer PCB?
A single-sided PCB has conductive copper traces on only one side of the insulating substrate, while a double-sided PCB has traces on both sides. A multi-layer PCB consists of three or more conductive layers, separated by insulating layers, allowing for more complex routing and higher component density.
2. What is the purpose of a solder mask on a PCB?
A solder mask is a protective layer applied to the copper traces on a PCB. It serves to protect the traces from oxidation, prevent solder bridging during assembly, and provide electrical insulation. Solder masks also improve the aesthetics of the PCB and can be used to identify component placement and polarity.
3. What is the difference between through-hole and surface-mount components?
Through-hole components have long leads that are inserted into drilled holes in the PCB and soldered on the opposite side. Surface-mount components, on the other hand, are soldered directly onto the surface of the PCB. Surface-mount components are generally smaller and allow for higher component density, while through-hole components offer greater mechanical strength and are easier to replace.
4. How do I choose the right PCB material for my application?
The choice of PCB material depends on several factors, including the operating frequency, power requirements, environmental conditions, and cost constraints. For high-frequency applications, low-loss materials such as Rogers or Isola laminates are often used. For high-power applications, materials with good thermal conductivity, such as aluminum-backed PCBs or metal core PCBs, may be necessary. In general, FR-4 is a cost-effective and versatile material suitable for most standard applications.
5. What is the typical turnaround time for PCB fabrication?
The turnaround time for PCB fabrication varies depending on the complexity of the design, the chosen materials, and the manufacturing process. For standard PCBs, turnaround times can range from a few days to a few weeks. Rush services are often available for an additional cost, providing faster turnaround times for urgent projects. It is essential to work closely with your PCB manufacturer to understand their capabilities and lead times to ensure timely delivery of your PCBs.
Conclusion
PCBs have revolutionized the electronics industry, enabling the development of compact, reliable, and cost-effective electronic devices. From their humble beginnings in the 1930s to their ubiquitous presence in today’s world, PCBs have proven to be an indispensable technology.
The benefits of PCBs are numerous, from their space-saving design and enhanced reliability to their improved electrical performance and cost-effective manufacturing. As PCB technology continues to evolve, with advancements in materials, manufacturing processes, and design capabilities, we can expect to see even more innovative and transformative applications in the future.
To fully realize the potential of PCBs, it is essential for designers and manufacturers to stay informed about the latest developments in PCB technology and to adhere to best practices in PCB design and manufacturing. By doing so, they can create PCBs that not only meet the demands of today’s applications but also anticipate the needs of tomorrow’s innovations.
No responses yet