PCB Substrate Materials
The substrate, or base material, of a PCB is typically made from a non-conductive and heat-resistant material. The most common substrate materials used in PCB manufacturing are:
- FR-4 (Flame Retardant 4)
- CEM (Composite Epoxy Material)
- PTFE (Polytetrafluoroethylene)
- Polyimide
FR-4 (Flame Retardant 4)
FR-4 is the most widely used PCB substrate material due to its excellent mechanical, electrical, and thermal properties. It is a composite material made from woven fiberglass cloth impregnated with an epoxy resin binder. The “FR” in FR-4 stands for “Flame Retardant,” indicating its ability to self-extinguish and resist the spread of flames in case of a fire.
Property | Value |
---|---|
Dielectric Constant | 4.2 – 4.6 |
Glass Transition Temperature | 130°C – 140°C |
Thermal Expansion Coefficient | 12 – 16 ppm/°C |
Moisture Absorption | 0.1 – 0.2% |
Flexural Strength | 500 – 600 MPa |
FR-4 is suitable for a wide range of applications, including:
- Consumer electronics
- Telecommunications equipment
- Automotive electronics
- Industrial control systems
- Medical devices
CEM (Composite Epoxy Material)
CEM is another popular PCB substrate material that offers a cost-effective alternative to FR-4. It is made from a composite of woven fiberglass and epoxy resin, with varying grades available based on the reinforcement content and type of filler used.
The most common CEM grades are:
- CEM-1: Composite of woven fiberglass and epoxy resin with no filler
- CEM-3: Composite of woven fiberglass and epoxy resin with a non-woven fiberglass filler
Property | CEM-1 | CEM-3 |
---|---|---|
Dielectric Constant | 4.5 – 4.7 | 4.5 – 4.7 |
Glass Transition Temperature | 110°C – 130°C | 110°C – 130°C |
Thermal Expansion Coefficient | 14 – 17 ppm/°C | 14 – 17 ppm/°C |
Moisture Absorption | 0.2 – 0.3% | 0.2 – 0.3% |
Flexural Strength | 300 – 400 MPa | 350 – 450 MPa |
CEM substrates are suitable for applications that require lower costs and have less demanding performance requirements compared to FR-4, such as:
- Consumer appliances
- Low-end electronics
- Toys and games
- Educational devices
PTFE (Polytetrafluoroethylene)
PTFE, also known by its trade name Teflon, is a high-performance PCB substrate material that offers excellent electrical and thermal properties. It is a fluoropolymer with a low dielectric constant, low dissipation factor, and high thermal stability, making it ideal for high-frequency and microwave applications.
Property | Value |
---|---|
Dielectric Constant | 2.0 – 2.1 |
Dissipation Factor | 0.0002 – 0.0005 |
Thermal Expansion Coefficient | 100 – 130 ppm/°C |
Moisture Absorption | <0.01% |
Operating Temperature Range | -65°C to 260°C |
PTFE PCBs are commonly used in applications such as:
- Radar systems
- Satellite communications
- Microwave antennas
- High-speed data transmission
- Aerospace and defense electronics
Polyimide
Polyimide is another high-performance PCB substrate material known for its excellent thermal stability, chemical resistance, and mechanical strength. It is a synthetic polymer that can withstand high temperatures and harsh environments, making it suitable for demanding applications.
Property | Value |
---|---|
Dielectric Constant | 3.2 – 3.6 |
Glass Transition Temperature | >250°C |
Thermal Expansion Coefficient | 12 – 20 ppm/°C |
Moisture Absorption | 0.4 – 0.8% |
Tensile Strength | 150 – 200 MPa |
Polyimide PCBs are used in applications that require high reliability and performance under extreme conditions, such as:
- Aerospace and defense electronics
- Automotive electronics
- High-temperature industrial sensors
- Medical implantable devices
- Downhole drilling equipment
Comparison of PCB Substrate Materials
Property | FR-4 | CEM | PTFE | Polyimide |
---|---|---|---|---|
Cost | Moderate | Low | High | High |
Dielectric Constant | 4.2 – 4.6 | 4.5 – 4.7 | 2.0 – 2.1 | 3.2 – 3.6 |
Thermal Stability | Moderate | Moderate | High | High |
Moisture Resistance | Good | Good | Excellent | Good |
High-Frequency Performance | Good | Fair | Excellent | Good |
Mechanical Strength | Good | Fair | Fair | Excellent |
When selecting a PCB substrate material, designers must consider factors such as the intended application, performance requirements, environmental conditions, and cost constraints. FR-4 remains the most popular choice for general-purpose electronics, while CEM provides a cost-effective alternative for less demanding applications. PTFE and polyimide are specialized materials used in high-performance and harsh environment applications.
Frequently Asked Questions (FAQ)
-
Q: What is the most commonly used PCB substrate material?
A: FR-4 (Flame Retardant 4) is the most widely used PCB substrate material due to its excellent balance of mechanical, electrical, and thermal properties. -
Q: What are the advantages of using PTFE as a PCB substrate material?
A: PTFE offers a low dielectric constant, low dissipation factor, and high thermal stability, making it ideal for high-frequency and microwave applications. -
Q: Can polyimide PCBs withstand high temperatures?
A: Yes, polyimide PCBs are known for their excellent thermal stability and can withstand temperatures above 250°C, making them suitable for high-temperature applications. -
Q: What is the difference between FR-4 and CEM PCB substrate materials?
A: FR-4 is a composite material made from woven fiberglass cloth impregnated with an epoxy resin binder, while CEM is a composite of woven fiberglass and epoxy resin with varying grades based on the reinforcement content and type of filler used. FR-4 generally offers better performance and reliability compared to CEM. -
Q: What factors should be considered when selecting a PCB substrate material?
A: When selecting a PCB substrate material, designers must consider factors such as the intended application, performance requirements, environmental conditions, and cost constraints. The choice of substrate material depends on the specific needs of the project.
In conclusion, the choice of plastic used in PCB manufacturing plays a critical role in determining the board’s performance, durability, and overall quality. FR-4 remains the most popular substrate material for general-purpose electronics, while CEM offers a cost-effective alternative for less demanding applications. PTFE and polyimide are specialized materials used in high-performance and harsh environment applications. By understanding the properties and characteristics of different PCB substrate materials, designers can make informed decisions and select the most suitable material for their specific project requirements.
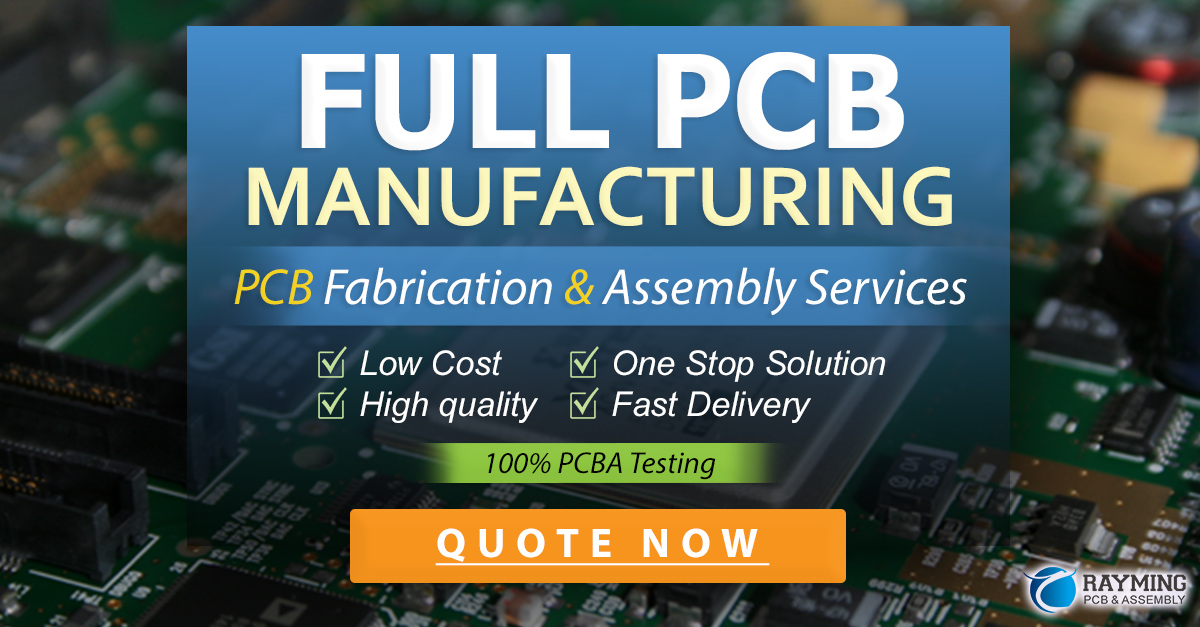
No responses yet