Composition of FR4 PCB substrate
The FR in FR4 stands for “Flame Retardant”, while the 4 refers to woven glass reinforced epoxy resin. The primary components that make up FR4 are:
-
Fiberglass: Fiberglass provides mechanical strength and electrical insulation to the PCB. It is made from extremely fine fibers of glass woven into a cloth.
-
Epoxy Resin: The epoxy resin acts as a binder, holding the glass fibers together and providing additional insulation and heat resistance.
-
Copper Foil: Thin layers of copper foil are laminated to one or both sides of the FR4 core. The copper foil is etched to create the conductive traces, pads, and planes of the circuit board.
-
Additional Additives: Other additives such as flame retardants, fillers, and coloring may be incorporated into the epoxy resin to enhance specific properties.
Manufacturing Process of FR4 Laminates
The process of manufacturing FR4 laminates typically involves the following steps:
-
Impregnation: Sheets of fiberglass cloth are dipped in a bath of liquid epoxy resin, ensuring thorough saturation.
-
Drying: The resin-impregnated fiberglass sheets are then passed through a series of rollers and ovens to remove excess resin and partially cure (B-stage) the epoxy.
-
Cutting: The B-staged sheets are cut to the desired size.
-
Layup: The cut sheets are stacked in alternating layers with sheets of copper foil.
-
Lamination: The stacked layers are placed in a laminating press, where high temperature and pressure fully cure the epoxy resin, bonding the layers together.
-
Cooling: The laminated board is cooled and then ready for further processing, such as drilling, etching, and plating.
Properties and Characteristics of FR4
FR4 has become the most widely used PCB substrate material due to its excellent balance of mechanical, electrical, and thermal properties. Some key characteristics of FR4 include:
Mechanical Properties
- High tensile and flexural strength
- Good dimensional stability
- Resistant to impact and vibration
- Suitable for machining and drilling
Electrical Properties
- Good Dielectric constant (typically 4.3-4.8 at 1 MHz)
- Low dielectric loss (dissipation factor of 0.02 at 1 MHz)
- High insulation resistance (>10^12 ohms)
- Suitable for high-frequency applications
Thermal Properties
- Glass transition temperature (Tg) around 130-140°C
- Thermal expansion coefficient similar to copper
- Flame resistant and self-extinguishing
- Resistant to heat and cold
Comparison of FR4 to Other PCB Substrates
While FR4 is the most common PCB substrate, there are other materials used for specific applications:
Material | Advantages | Disadvantages |
---|---|---|
Polyimide | Higher temperature resistance, flexible | More expensive, lower dielectric constant |
PTFE | Excellent high-frequency performance, low loss | Expensive, difficult to process |
Aluminum | Excellent Thermal Conductivity, rigid | Requires insulation layer, higher cost |
Ceramic | High thermal conductivity, low CTE | Brittle, expensive |
FR4 offers a good balance of properties and cost-effectiveness for most general-purpose PCB applications.
Grades and Variations of FR4
There are several grades and variations of FR4 available, each with slightly different properties tailored for specific applications:
Standard FR4
The most common grade of FR4, suitable for the majority of PCB applications. It has a glass transition temperature (Tg) of around 130-140°C.
High Tg FR4
Formulated with a higher glass transition temperature, typically 170-180°C. This grade offers improved thermal resistance and stability for more demanding applications.
Halogen-Free FR4
Traditional FR4 uses brominated flame retardants, which can release toxic compounds during combustion. Halogen-free FR4 uses alternative flame retardants to reduce environmental impact.
Low-Loss FR4
Engineered to have lower dielectric loss and a more consistent dielectric constant over a wider frequency range. This grade is suitable for high-speed digital and RF applications.
High-Reliability FR4
Manufactured with stricter controls and higher-quality materials to ensure consistent performance in critical applications, such as aerospace and military.
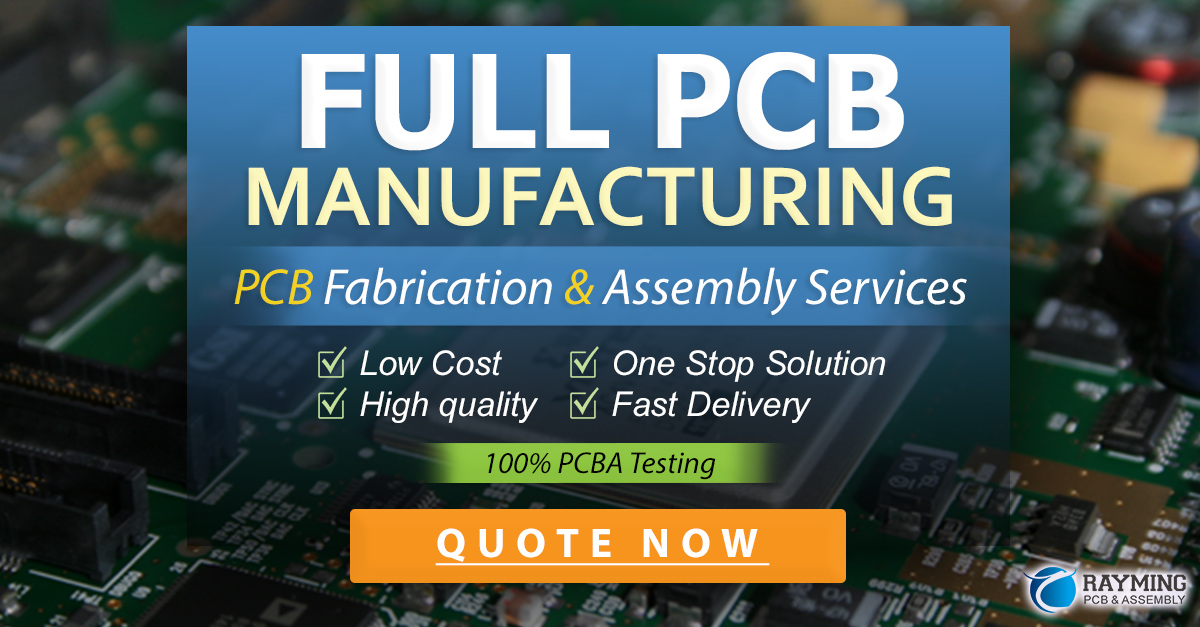
Applications of FR4 PCBs
FR4 is used in a wide range of electronic applications across various industries:
Consumer Electronics
- Smartphones, tablets, and laptops
- Home appliances and smart home devices
- Gaming consoles and peripherals
Industrial Electronics
- Process control systems
- Automation and robotics
- Power electronics and motor drives
Automotive Electronics
- Engine control units (ECUs)
- Infotainment and navigation systems
- Advanced driver assistance systems (ADAS)
Medical Electronics
- Diagnostic and imaging equipment
- Patient monitoring systems
- Implantable devices
Aerospace and Defense
- Avionics systems
- Radar and communication equipment
- Satellite and spacecraft electronics
FAQs about FR4 PCB Substrate
1. What does FR stand for in FR4?
FR stands for “Flame Retardant”. FR4 is formulated with additives that make it resistant to catching fire and self-extinguishing if ignited.
2. Is FR4 suitable for high-frequency applications?
Standard FR4 can be used for frequencies up to a few gigahertz. For higher frequencies or more demanding RF applications, low-loss grades of FR4 or other specialized materials like PTFE may be more suitable.
3. What is the maximum operating temperature for FR4?
The maximum operating temperature for FR4 depends on the specific grade. Standard FR4 has a glass transition temperature (Tg) around 130-140°C, while high Tg grades can operate up to 170-180°C.
4. Can FR4 be used for flexible PCBs?
FR4 is a rigid material and not suitable for flexible PCBs. For flexible applications, materials like polyimide or flexible polyester are commonly used.
5. How does the cost of FR4 compare to other PCB substrates?
FR4 is generally less expensive than specialized materials like polyimide, PTFE, or ceramic. Its balance of good performance and lower cost makes it a popular choice for a wide range of applications.
Conclusion
FR4 is a versatile and widely used PCB substrate material, offering an excellent combination of mechanical, electrical, and thermal properties. Its flame resistance, dielectric performance, and cost-effectiveness make it suitable for a broad spectrum of electronic applications, from consumer gadgets to industrial control systems.
As PCB technology continues to advance, the demand for high-performance materials like FR4 will only increase. By understanding the composition, properties, and variations of FR4, engineers and designers can make informed decisions when selecting the most appropriate substrate for their specific application requirements.
No responses yet