PCB Substrate Materials
The substrate is the foundation of a PCB, providing a stable base for the copper traces and components. The choice of substrate material depends on the specific requirements of the application, such as thermal stability, dielectric constant, and mechanical strength. Some common PCB substrate materials include:
FR-4
FR-4 is the most widely used PCB substrate material. It is a composite material made of woven fiberglass cloth impregnated with an epoxy resin. FR-4 offers good mechanical strength, electrical insulation, and thermal stability. It is suitable for a wide range of applications, from consumer electronics to industrial equipment.
High-Tg FR-4
High-Tg FR-4 is a variant of standard FR-4 that offers improved thermal stability. It has a higher glass transition temperature (Tg), which allows it to maintain its mechanical and electrical properties at higher temperatures. High-Tg FR-4 is often used in automotive, aerospace, and military applications where the PCB may be exposed to extreme temperatures.
Polyimide
Polyimide is a high-performance polymer that offers excellent thermal stability, chemical resistance, and mechanical strength. It is often used in flexible PCBs due to its ability to withstand repeated bending and flexing. Polyimide PCBs are commonly found in aerospace, medical, and wearable electronics applications.
Ceramic
Ceramic substrates, such as alumina and beryllia, offer exceptional thermal conductivity and electrical insulation properties. They are often used in high-power electronic applications, such as power amplifiers and high-brightness LEDs. Ceramic PCBs can dissipate heat efficiently, ensuring the reliable operation of components.
Copper Traces and Pads
Copper is the primary conductive material used in PCBs. It is used to create the traces, pads, and vias that form the electrical connections between components. Copper is chosen for its excellent electrical conductivity, thermal conductivity, and ease of processing.
Electrodeposited Copper
Electrodeposited copper is the most common type of copper used in PCBs. It is deposited onto the substrate using an electroplating process, which involves submerging the substrate in a copper sulfate solution and applying an electric current. The thickness of the copper layer can be precisely controlled, allowing for the creation of fine traces and high-density layouts.
Rolled Annealed Copper
Rolled annealed copper is a type of copper foil that is produced by rolling and annealing (heat treating) pure copper. It offers higher ductility and tensile strength compared to electrodeposited copper. Rolled annealed copper is often used in flexible PCBs and high-reliability applications.
Copper Thickness
The thickness of the copper layer in a PCB is measured in ounces per square foot (oz/ft²). Common copper thicknesses include:
Copper Weight (oz/ft²) | Thickness (mm) |
---|---|
0.5 | 0.0175 |
1 | 0.035 |
2 | 0.07 |
3 | 0.105 |
The choice of copper thickness depends on the current carrying requirements, trace width, and manufacturing constraints of the PCB.
Solder Mask
Solder mask is a thin layer of polymer that is applied over the copper traces on a PCB. It serves several purposes:
- Insulation: Solder mask provides electrical insulation between adjacent copper traces, preventing short circuits.
- Protection: It protects the copper traces from oxidation, contamination, and mechanical damage.
- Solderability: Solder mask defines the areas where solder can be applied, such as component pads and vias.
Solder mask is typically applied using a screen printing or photoimaging process. It is available in various colors, with green being the most common. Other colors, such as blue, red, and black, are used for aesthetic or functional purposes.
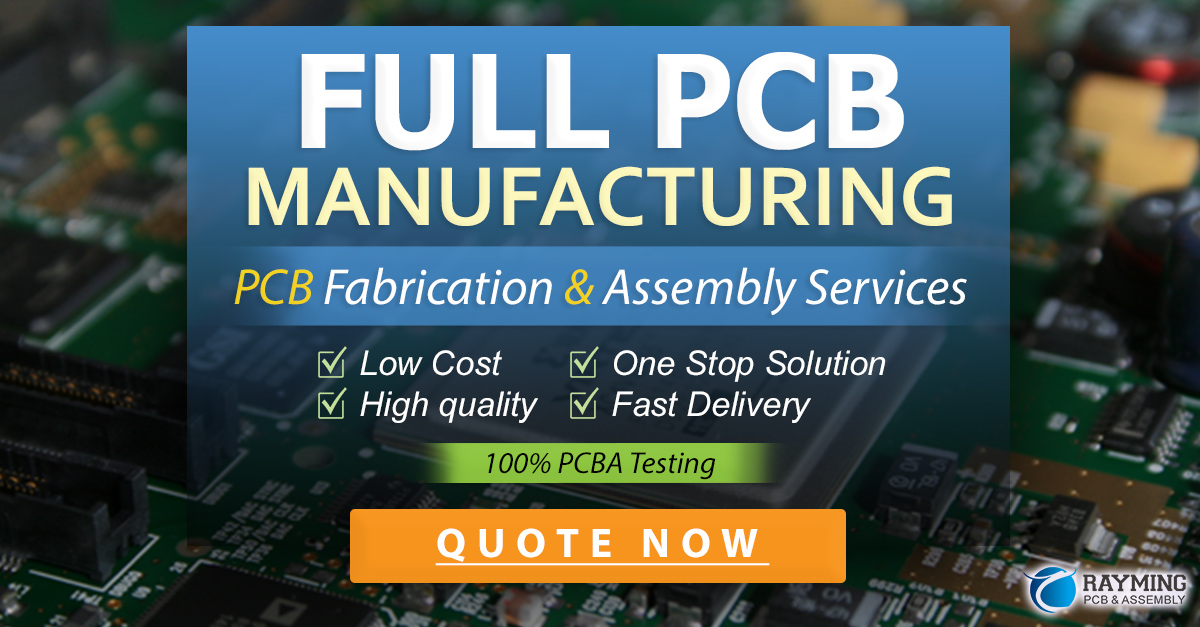
Silkscreen
Silkscreen is a layer of ink that is printed on top of the solder mask. It is used to add text, logos, and component identifiers to the PCB. Silkscreen helps in the assembly process by providing visual guidance for component placement.
Silkscreen ink is typically white, but other colors can be used for better visibility or branding purposes. The ink is applied using a screen printing process and is designed to withstand the high temperatures encountered during soldering.
Plating Finishes
Plating finishes are thin layers of metal that are applied to the exposed copper surfaces of a PCB, such as component pads and vias. They serve several purposes:
- Protection: Plating finishes protect the copper from oxidation and contamination, ensuring good solderability and long-term reliability.
- Solderability: Some plating finishes, such as HASL and ENIG, provide a surface that is easy to solder and forms reliable solder joints.
- Aesthetics: Plating finishes can enhance the appearance of the PCB and provide a professional look.
Some common plating finishes used in PCBs include:
HASL (Hot Air Solder Leveling)
HASL is a tin-lead alloy that is applied to the copper surfaces using a hot air leveling process. It provides excellent solderability and is one of the most cost-effective plating finishes.
ENIG (Electroless Nickel Immersion Gold)
ENIG is a two-layer plating finish consisting of a nickel layer and a thin gold layer. The nickel provides a barrier against copper diffusion, while the gold ensures good solderability and corrosion resistance. ENIG is popular in high-reliability applications.
OSP (Organic Solderability Preservative)
OSP is a thin, transparent organic coating that is applied to the copper surfaces. It provides temporary protection against oxidation and ensures good solderability. OSP is a cost-effective alternative to metallic plating finishes.
Advanced Materials
As electronics continue to evolve, new materials are being developed to meet the increasing demands for performance, reliability, and functionality. Some advanced materials used in PCBs include:
High-Frequency Laminates
High-frequency laminates are specialized substrate materials designed for use in high-speed digital and RF applications. They offer low dielectric loss, controlled impedance, and excellent signal integrity. Examples include Rogers RO4000 series, Isola I-Tera MT40, and Panasonic Megtron 6.
Metal Core PCBs
Metal core PCBs (MCPCBs) feature a metal substrate, typically aluminum, instead of the traditional FR-4. The metal core provides excellent thermal conductivity, allowing for efficient heat dissipation. MCPCBs are commonly used in high-power LED lighting applications.
Carbon Nanomaterials
Carbon nanomaterials, such as carbon nanotubes (CNTs) and graphene, are being explored for use in PCBs. These materials offer exceptional electrical and thermal conductivity, as well as mechanical strength. They have the potential to enable the development of ultra-thin, flexible, and high-performance electronic devices.
FAQ
-
Q: What is the most common PCB substrate material?
A: FR-4 is the most widely used PCB substrate material due to its good mechanical, electrical, and thermal properties, as well as its cost-effectiveness. -
Q: What is the purpose of solder mask on a PCB?
A: Solder mask provides electrical insulation between copper traces, protects the traces from oxidation and damage, and defines the areas where solder can be applied. -
Q: What is the difference between HASL and ENIG plating finishes?
A: HASL is a tin-lead alloy that provides good solderability and is cost-effective. ENIG is a two-layer plating finish consisting of nickel and gold, offering excellent solderability, corrosion resistance, and suitability for high-reliability applications. -
Q: What are metal core PCBs used for?
A: Metal core PCBs are used in applications that require efficient heat dissipation, such as high-power LED lighting. The metal substrate, typically aluminum, provides excellent thermal conductivity. -
Q: Why are carbon nanomaterials being explored for use in PCBs?
A: Carbon nanomaterials, such as carbon nanotubes and graphene, offer exceptional electrical and thermal conductivity, as well as mechanical strength. They have the potential to enable the development of ultra-thin, flexible, and high-performance electronic devices.
Conclusion
PCB Materials play a crucial role in determining the performance, reliability, and functionality of electronic devices. The choice of substrate, copper, solder mask, silkscreen, and plating finishes depends on the specific requirements of the application. As technology advances, new materials, such as high-frequency laminates and carbon nanomaterials, are being developed to meet the increasing demands of the electronics industry.
Understanding the properties and characteristics of PCB materials is essential for designing and manufacturing high-quality electronic products. By selecting the appropriate materials and processes, engineers can ensure that their PCBs meet the required electrical, thermal, and mechanical specifications while optimizing cost and manufacturability.
No responses yet