Introduction to PCB Material
Printed Circuit Boards (PCBs) are the backbone of modern electronics. They provide a platform for electronic components to be mounted and interconnected, enabling the creation of complex circuits and devices. The choice of material used for PCBs is crucial, as it directly impacts the performance, reliability, and durability of the final product. In this article, we will explore the various materials used for PCBs, their properties, and their applications.
Types of PCB Material
There are several types of materials used for PCBs, each with its own unique set of properties and characteristics. The most common PCB materials include:
1. FR-4
FR-4 is the most widely used PCB material. It is a composite material made of woven fiberglass cloth impregnated with an epoxy resin. FR-4 offers excellent mechanical strength, good electrical insulation, and reasonable thermal stability. It is suitable for a wide range of applications, from consumer electronics to industrial equipment.
2. Polyimide
Polyimide is a high-performance polymer that offers exceptional thermal stability and mechanical strength. It can withstand temperatures up to 400°C, making it ideal for applications that require high-temperature operation, such as aerospace and military electronics. Polyimide PCBs are also known for their flexibility, allowing them to be used in flexible and rigid-flex PCB designs.
3. Teflon
Teflon, also known as PTFE (Polytetrafluoroethylene), is a highly resistant and stable material. It offers excellent dielectric properties, low dissipation factor, and high thermal stability. Teflon PCBs are commonly used in high-frequency applications, such as radar systems and wireless communication devices, due to their ability to minimize signal loss and maintain signal integrity.
4. Ceramic
Ceramic PCBs are made from a mixture of ceramic powders and organic binders. They offer excellent thermal conductivity, high dielectric strength, and low thermal expansion. Ceramic PCBs are often used in high-power applications, such as power electronics and LED lighting, where efficient heat dissipation is crucial.
5. Aluminum
Aluminum PCBs consist of an aluminum substrate with a dielectric layer and copper traces on top. They provide excellent thermal conductivity, allowing for efficient heat dissipation. Aluminum PCBs are commonly used in high-power applications, such as motor drives and power converters, where heat management is a critical factor.
Properties of PCB Material
When selecting a PCB material, several key properties must be considered to ensure optimal performance and reliability. These properties include:
1. Dielectric constant (Dk)
The dielectric constant is a measure of a material’s ability to store electrical energy. It determines the speed at which signals propagate through the PCB. Materials with a lower dielectric constant allow for faster signal propagation, making them suitable for high-speed applications.
2. Dissipation Factor (Df)
The dissipation factor, also known as loss tangent, represents the amount of energy lost as heat when an alternating current passes through the material. Materials with a lower dissipation factor exhibit less signal loss and are preferred for high-frequency applications.
3. Thermal Conductivity
Thermal conductivity is a measure of a material’s ability to conduct heat. PCBs with high thermal conductivity can efficiently dissipate heat generated by electronic components, preventing overheating and ensuring reliable operation.
4. Coefficient of Thermal Expansion (CTE)
The coefficient of thermal expansion describes how much a material expands or contracts with changes in temperature. It is important for PCBs to have a CTE that closely matches the CTE of the components mounted on them to minimize stress and prevent cracking or delamination.
5. Mechanical Strength
PCBs must possess sufficient mechanical strength to withstand the stresses encountered during manufacturing, assembly, and operation. Materials with high mechanical strength, such as FR-4 and polyimide, are preferred for applications that require durability and reliability.
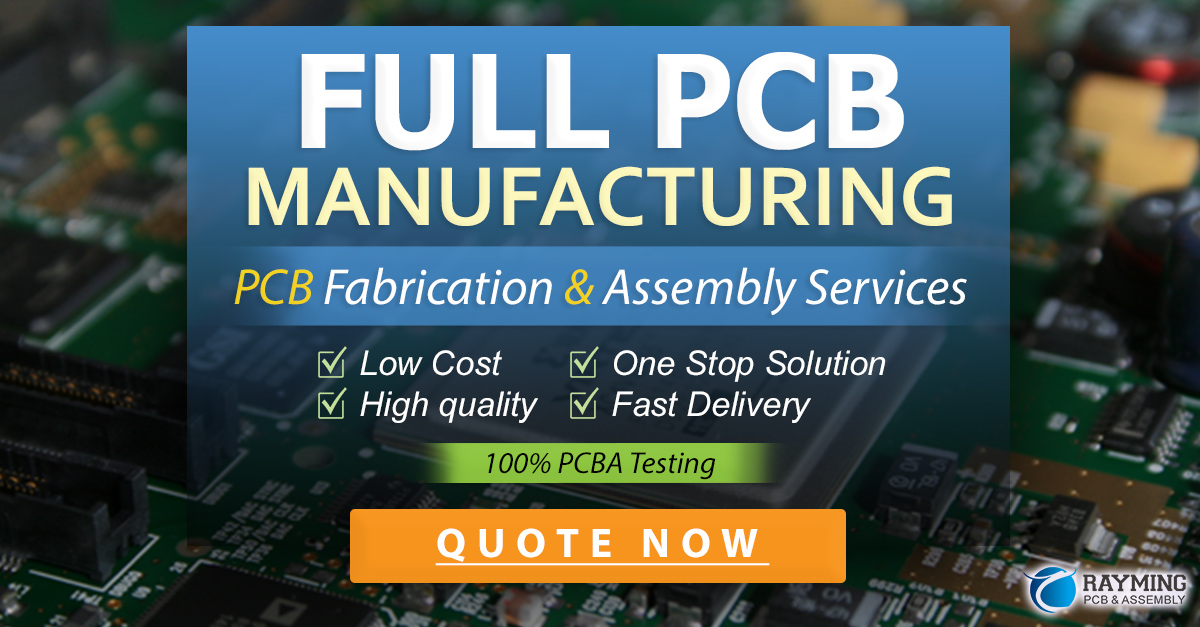
PCB Material Selection
Choosing the right PCB material depends on the specific requirements of the application. Here are some factors to consider when selecting a PCB material:
- Operating Environment
- Temperature range
- Humidity
-
Vibration and shock
-
Electrical Requirements
- Signal speed and frequency
- Dielectric constant and dissipation factor
-
Impedance control
-
Thermal Management
- Heat generation and dissipation
- Thermal conductivity
-
Coefficient of thermal expansion
-
Mechanical Requirements
- Flexibility
- Mechanical strength
-
Dimensional stability
-
Cost and Availability
- Material cost
- Manufacturing complexity
- Lead time and availability
By carefully evaluating these factors and understanding the properties of different PCB materials, designers can select the most suitable material for their specific application.
PCB Material Comparison
To help designers make informed decisions, the following table compares the key properties of common PCB materials:
Material | Dielectric Constant (Dk) | Dissipation Factor (Df) | Thermal Conductivity (W/mK) | Coefficient of Thermal Expansion (ppm/°C) | Mechanical Strength (MPa) |
---|---|---|---|---|---|
FR-4 | 4.3 – 4.8 | 0.02 – 0.03 | 0.3 – 0.4 | 12 – 16 | 400 – 500 |
Polyimide | 3.2 – 3.5 | 0.002 – 0.008 | 0.2 – 0.3 | 20 – 40 | 200 – 300 |
Teflon | 2.0 – 2.1 | 0.0002 – 0.0008 | 0.2 – 0.3 | 100 – 200 | 20 – 30 |
Ceramic | 6.0 – 10.0 | 0.001 – 0.005 | 20 – 30 | 5 – 7 | 300 – 400 |
Aluminum | – | – | 150 – 200 | 23 – 24 | 70 – 90 |
*Note: The values provided in the table are typical ranges and may vary depending on the specific formulation and manufacturing process.
PCB Material Applications
Different PCB materials find applications in various industries and products. Here are some common applications for each PCB material:
- FR-4
- Consumer electronics
- Industrial controls
- Automotive electronics
-
Medical devices
-
Polyimide
- Aerospace and military electronics
- High-temperature applications
- Flexible and rigid-flex PCBs
-
Wearable devices
-
Teflon
- High-frequency communication devices
- Radar systems
- Microwave circuits
-
Satellite equipment
-
Ceramic
- Power electronics
- LED lighting
- High-power RF circuits
-
Automotive engine control units
-
Aluminum
- Power converters
- Motor drives
- High-power LED lighting
- Automotive power electronics
Frequently Asked Questions (FAQ)
- What is the most commonly used PCB material?
-
FR-4 is the most widely used PCB material due to its good balance of properties, cost-effectiveness, and wide availability.
-
Which PCB material is best for high-frequency applications?
-
Teflon (PTFE) is the preferred material for high-frequency applications due to its low dielectric constant and low dissipation factor, which minimize signal loss and maintain signal integrity.
-
Which PCB material offers the best thermal conductivity?
-
Aluminum PCBs provide the highest thermal conductivity among common PCB materials, making them ideal for applications that require efficient heat dissipation.
-
Can FR-4 be used for flexible PCBs?
-
FR-4 is primarily used for rigid PCBs. For flexible PCB applications, materials like polyimide are more suitable due to their flexibility and ability to withstand repeated bending.
-
What is the main advantage of using ceramic PCBs?
- Ceramic PCBs offer excellent thermal conductivity and low thermal expansion, making them suitable for high-power applications where efficient heat dissipation is crucial.
Conclusion
The choice of material used for PCBs is a critical factor in determining the performance, reliability, and durability of electronic devices. Each PCB material has its own unique set of properties and characteristics, making it suitable for specific applications. FR-4 is the most widely used PCB material, offering a good balance of properties and cost-effectiveness. Polyimide excels in high-temperature and flexible applications, while Teflon is the preferred choice for high-frequency devices. Ceramic and aluminum PCBs are ideal for high-power applications that require efficient heat dissipation.
When selecting a PCB material, designers must consider factors such as the operating environment, electrical requirements, thermal management, mechanical requirements, and cost. By understanding the properties of different PCB materials and carefully evaluating the specific needs of the application, designers can make informed decisions and select the most suitable material for their projects.
As technology continues to advance, new PCB materials and manufacturing techniques may emerge, offering even better performance and capabilities. However, the fundamental understanding of PCB materials and their properties will remain essential for designing reliable and high-performance electronic devices.
Word count: 1,535 words
No responses yet