Introduction to Laminate substrate
Laminate substrate is a versatile and widely used material in various industries, including electronics, construction, and manufacturing. It is a composite material that consists of multiple layers bonded together to form a single, durable sheet. The layers typically include a core material, such as particleboard or fiberboard, and a decorative layer, such as melamine or high-pressure laminate (HPL).
Key Components of Laminate Substrate
- Core Material
- Decorative Layer
- Bonding Agents
Core Materials Used in Laminate Substrate
The core material is the foundation of the laminate substrate and provides its structural integrity. Several materials can be used as the core, each with its own unique properties and benefits.
Particleboard
Particleboard is one of the most common core materials used in laminate substrate. It is made from wood chips, sawmill shavings, or sawdust mixed with a resin binder and compressed under high pressure and heat. Particleboard is relatively inexpensive, lightweight, and has good dimensional stability.
Advantages of Particleboard Core
- Cost-effective
- Lightweight
- Good dimensional stability
Disadvantages of Particleboard Core
- Lower moisture resistance compared to other core materials
- Lower strength and durability compared to other core materials
Medium Density Fiberboard (MDF)
Medium Density Fiberboard (MDF) is another popular core material for laminate substrate. It is made from wood fibers that are broken down, mixed with resin, and compressed under high pressure and heat. MDF has a smooth, consistent surface and is denser than particleboard.
Advantages of MDF Core
- Smooth, consistent surface
- Higher density than particleboard
- Good machinability
Disadvantages of MDF Core
- Heavier than particleboard
- Higher cost than particleboard
Plywood
Plywood is a core material made from thin layers of wood veneer glued together with the grain of each layer perpendicular to the adjacent layer. This cross-grain construction gives plywood excellent strength, stiffness, and dimensional stability.
Advantages of Plywood Core
- High strength and stiffness
- Excellent dimensional stability
- Good moisture resistance
Disadvantages of Plywood Core
- Higher cost than particleboard and MDF
- Heavier than particleboard and MDF
Decorative Layers Used in Laminate Substrate
The decorative layer is the top layer of the laminate substrate and provides its aesthetic appeal and surface properties. There are several types of decorative layers used in laminate substrate, each with its own unique characteristics.
Melamine
Melamine is a synthetic resin that is often used as a decorative layer in laminate substrate. It is a cost-effective option that provides a smooth, durable surface resistant to scratches, stains, and moisture.
Advantages of Melamine Decorative Layer
- Cost-effective
- Smooth, durable surface
- Resistant to scratches, stains, and moisture
Disadvantages of Melamine Decorative Layer
- Limited design options compared to other decorative layers
- Lower heat resistance compared to other decorative layers
High-Pressure Laminate (HPL)
High-Pressure Laminate (HPL) is a decorative layer made from multiple layers of kraft paper impregnated with resins and fused together under high pressure and heat. HPL offers a wide range of design options, including wood grains, solid colors, and patterns.
Advantages of HPL Decorative Layer
- Wide range of design options
- Excellent durability and wear resistance
- Good heat and moisture resistance
Disadvantages of HPL Decorative Layer
- Higher cost than melamine
- Thicker than melamine, which may affect overall substrate thickness
Veneer
Veneer is a thin layer of real wood that is bonded to the core material to create a natural wood look. Veneer offers the beauty and warmth of real wood while maintaining the stability and durability of the laminate substrate.
Advantages of Veneer Decorative Layer
- Natural wood appearance
- Unique grain patterns
- Can be sanded and refinished
Disadvantages of Veneer Decorative Layer
- Higher cost than melamine and HPL
- More susceptible to damage and wear than melamine and HPL
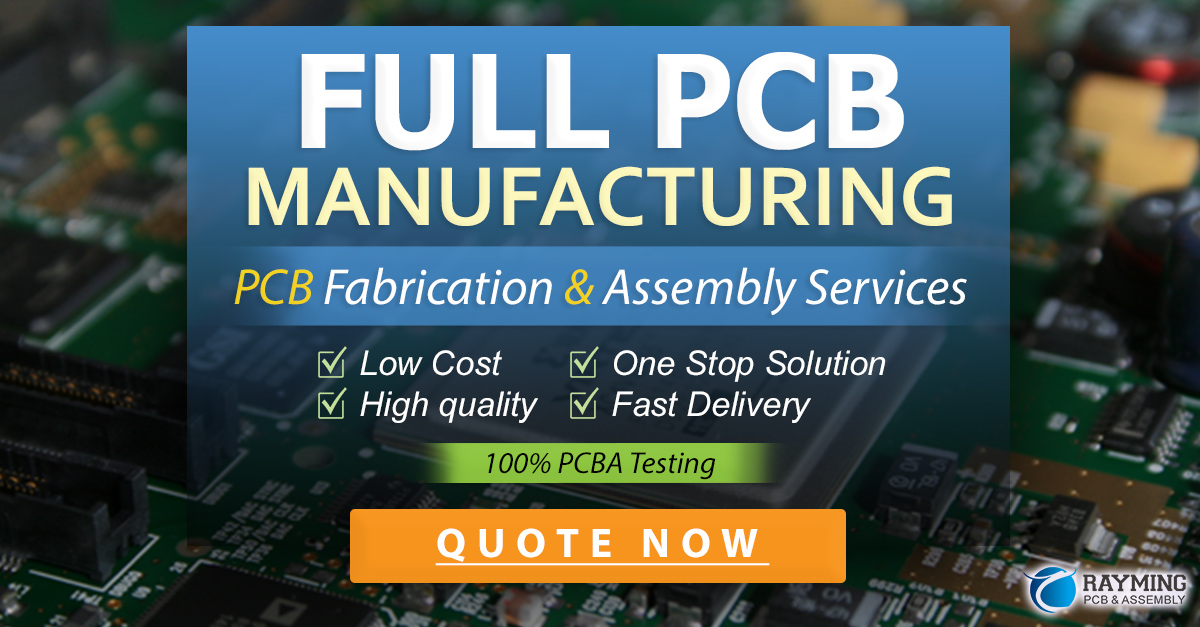
Bonding Agents Used in Laminate Substrate
Bonding agents are used to adhere the decorative layer to the core material and to bond the layers of the core material together. The most common bonding agents used in laminate substrate are resins.
Urea-Formaldehyde (UF) Resin
Urea-Formaldehyde (UF) resin is a thermosetting resin that is widely used in the production of laminate substrate. It is cost-effective, has good adhesive properties, and provides excellent dimensional stability.
Advantages of UF Resin
- Cost-effective
- Good adhesive properties
- Excellent dimensional stability
Disadvantages of UF Resin
- Emits formaldehyde, which may be a health concern
- Lower moisture resistance compared to other resins
Phenol-Formaldehyde (PF) Resin
Phenol-Formaldehyde (PF) resin is another thermosetting resin used in laminate substrate production. It offers better moisture resistance and durability than UF resin but is more expensive.
Advantages of PF Resin
- Better moisture resistance than UF resin
- Higher durability than UF resin
- Lower formaldehyde emissions than UF resin
Disadvantages of PF Resin
- Higher cost than UF resin
- Darker color than UF resin, which may affect the appearance of the laminate substrate
Applications of Laminate Substrate
Laminate substrate is used in a wide range of applications due to its versatility, durability, and cost-effectiveness. Some common applications include:
-
Furniture: Laminate substrate is widely used in the production of furniture, such as tables, shelves, and cabinets, due to its durability and resistance to scratches and stains.
-
Flooring: Laminate flooring is a popular choice for residential and commercial spaces because of its affordability, ease of installation, and variety of design options.
-
Countertops: Laminate countertops are a cost-effective alternative to natural stone or solid surface countertops and offer a wide range of colors and patterns.
-
Wallcoverings: Laminate panels can be used as decorative wallcoverings in commercial and residential settings, providing a durable and easy-to-clean surface.
-
Electronics: Laminate substrate is used in the production of printed circuit boards (PCBs) for electronic devices due to its excellent electrical insulation properties and dimensional stability.
Comparison of Laminate Substrate Materials
Material | Advantages | Disadvantages |
---|---|---|
Particleboard | – Cost-effective – Lightweight – Good dimensional stability |
– Lower moisture resistance – Lower strength and durability |
MDF | – Smooth, consistent surface – Higher density than particleboard – Good machinability |
– Heavier than particleboard – Higher cost than particleboard |
Plywood | – High strength and stiffness – Excellent dimensional stability – Good moisture resistance |
– Higher cost than particleboard and MDF – Heavier than particleboard and MDF |
Melamine | – Cost-effective – Smooth, durable surface – Resistant to scratches, stains, and moisture |
– Limited design options – Lower heat resistance |
HPL | – Wide range of design options – Excellent durability and wear resistance – Good heat and moisture resistance |
– Higher cost than melamine – Thicker than melamine |
Veneer | – Natural wood appearance – Unique grain patterns – Can be sanded and refinished |
– Higher cost than melamine and HPL – More susceptible to damage and wear |
Frequently Asked Questions (FAQ)
-
Q: What is the difference between particleboard and MDF?
A: Particleboard is made from wood chips, sawmill shavings, or sawdust, while MDF is made from wood fibers that are broken down into a fine consistency. MDF is denser and has a smoother surface than particleboard, but it is also heavier and more expensive. -
Q: Is laminate substrate waterproof?
A: Laminate substrate is not completely waterproof, but it does offer varying degrees of moisture resistance depending on the core material and bonding agents used. Plywood and MDF cores with PF resin offer better moisture resistance than particleboard with UF resin. -
Q: Can laminate substrate be used outdoors?
A: Most laminate substrates are not suitable for outdoor use as they are susceptible to moisture damage and UV degradation. However, some specialty laminate substrates are designed for outdoor applications, such as compact laminate panels. -
Q: How do I clean laminate substrate surfaces?
A: Laminate substrate surfaces can be easily cleaned using a damp cloth or sponge and a mild detergent. Avoid using abrasive cleaners or scrubbers, as they may damage the surface. Always wipe up spills promptly to prevent moisture from penetrating the substrate. -
Q: Can laminate substrate be recycled?
A: The recyclability of laminate substrate depends on the specific materials used in its production. Some laminate substrates, such as those with particleboard or MDF cores, can be recycled by chipping and reusing the material in new panels. However, the presence of resins and other additives may complicate the recycling process.
Conclusion
Laminate substrate is a versatile and widely used composite material that consists of a core material bonded to a decorative layer. The choice of core material, decorative layer, and bonding agent depends on the specific application and desired properties of the laminate substrate.
Particleboard, MDF, and plywood are common core materials, each with its own advantages and disadvantages in terms of cost, weight, strength, and moisture resistance. Melamine, HPL, and veneer are popular decorative layer options, offering varying levels of durability, design versatility, and aesthetic appeal.
Understanding the materials used in laminate substrate production is essential for selecting the right product for a given application and ensuring its longevity and performance.
No responses yet