Introduction to PCB Thickness and Variation
Printed Circuit Board (PCB) thickness is a crucial parameter that affects the mechanical, electrical, and thermal properties of the board. The thickness of a PCB is determined by the number of layers, the thickness of each layer, and the thickness of the substrate material. PCB thickness variation refers to the deviation of the actual thickness from the nominal or specified thickness.
Importance of PCB Thickness Control
Maintaining consistent PCB thickness is essential for several reasons:
- Mechanical stability: Thicker PCBs are generally more rigid and less prone to warping or bending, which is crucial for applications that require high mechanical stability.
- Electrical performance: The thickness of the PCB affects its electrical properties, such as impedance, capacitance, and resistance. Consistent thickness ensures consistent electrical performance across the board.
- Thermal management: Thicker PCBs have better thermal conductivity, which helps dissipate heat more efficiently. This is particularly important for high-power applications or boards with densely packed components.
- Manufacturing process: PCB thickness variation can affect the manufacturing process, such as drilling, plating, and soldering. Consistent thickness ensures better manufacturability and reduces the risk of defects.
Factors Affecting PCB Thickness Variation
Several factors can contribute to PCB thickness variation, including:
- Material properties: The properties of the substrate material, such as glass transition temperature, thermal expansion coefficient, and moisture absorption, can affect the thickness uniformity.
- Manufacturing process: The manufacturing process, including lamination, drilling, and plating, can introduce thickness variations. Poorly controlled processes or equipment can result in inconsistent thickness.
- Environmental factors: Environmental factors, such as temperature, humidity, and pressure, can cause the PCB to expand or contract, leading to thickness variation.
- Design factors: The design of the PCB, including the layer stack-up, copper weight, and via structure, can affect the thickness variation. Improper design can result in uneven thickness distribution.
PCB Thickness Specifications and Standards
IPC Standards for PCB Thickness
The IPC (Association Connecting Electronics Industries) is a global trade association that develops standards for the electronic interconnect industry. The IPC has several standards that specify the requirements for PCB thickness and thickness variation.
IPC-6012: Qualification and Performance Specification for Rigid Printed Boards
IPC-6012 is the most widely used standard for rigid PCBs. It specifies the requirements for the qualification and performance of rigid PCBs, including thickness and thickness variation. The standard defines three classes of PCBs based on their intended end-use:
Class | Description | Thickness Tolerance |
---|---|---|
1 | General Electronic Products | ±10% |
2 | Dedicated Service Electronic Products | ±10% |
3 | High Reliability Electronic Products | ±10% |
IPC-6013: Qualification and Performance Specification for Flexible Printed Boards
IPC-6013 is the standard for flexible PCBs. It specifies the requirements for the qualification and performance of flexible PCBs, including thickness and thickness variation. The standard defines three classes of PCBs based on their intended end-use:
Class | Description | Thickness Tolerance |
---|---|---|
1 | General Electronic Products | ±10% |
2 | Dedicated Service Electronic Products | ±10% |
3 | High Reliability Electronic Products | ±10% |
IPC-6018: Qualification and Performance Specification for High Frequency (Microwave) Printed Boards
IPC-6018 is the standard for high-frequency PCBs. It specifies the requirements for the qualification and performance of high-frequency PCBs, including thickness and thickness variation. The standard defines three classes of PCBs based on their intended end-use:
Class | Description | Thickness Tolerance |
---|---|---|
1 | General Electronic Products | ±10% |
2 | Dedicated Service Electronic Products | ±10% |
3 | High Reliability Electronic Products | ±10% |
Other Standards for PCB Thickness
In addition to the IPC standards, there are other standards that specify requirements for PCB thickness and thickness variation, such as:
- MIL-P-50884: Military specification for rigid PCBs
- MIL-P-50884: Military specification for flexible PCBs
- JPCA-PE01: Japanese standard for rigid PCBs
- JPCA-PE02: Japanese standard for flexible PCBs
Measuring PCB Thickness Variation
Methods for Measuring PCB Thickness
There are several methods for measuring PCB thickness, including:
- Micrometer: A micrometer is a mechanical device that measures thickness by applying a constant force between a spindle and an anvil. It is a simple and reliable method but requires manual operation.
- Caliper: A caliper is a mechanical device that measures thickness by sliding two jaws along a scale. It is a quick and easy method but may not be as accurate as a micrometer.
- Optical measurement: Optical measurement methods, such as laser triangulation or confocal microscopy, use light to measure the thickness of the PCB. They are non-contact methods that can provide high accuracy and resolution.
- X-ray measurement: X-ray measurement methods use X-rays to measure the thickness of the PCB. They can provide a cross-sectional view of the board and measure the thickness of individual layers.
Sampling and Measurement Locations
To accurately assess the thickness variation of a PCB, it is important to take measurements at multiple locations on the board. The IPC standards provide guidelines for sampling and measurement locations.
For rigid PCBs, IPC-6012 specifies the following sampling and measurement locations:
Board Size | Number of Measurements |
---|---|
< 100 cm² | 5 |
100-500 cm² | 10 |
> 500 cm² | 15 |
For flexible PCBs, IPC-6013 specifies the following sampling and measurement locations:
Board Size | Number of Measurements |
---|---|
< 100 cm² | 3 |
100-500 cm² | 5 |
> 500 cm² | 7 |
The measurements should be taken at evenly distributed locations on the board, including the corners, edges, and center.
Data Analysis and Reporting
After collecting the thickness measurements, the data should be analyzed to determine the thickness variation. The following statistical parameters are commonly used:
- Mean: The average thickness of all measurements
- Standard deviation: A measure of the spread of the thickness measurements
- Minimum and maximum: The lowest and highest thickness measurements
- Range: The difference between the minimum and maximum measurements
The results should be reported in a clear and concise manner, including the statistical parameters and any relevant charts or graphs.
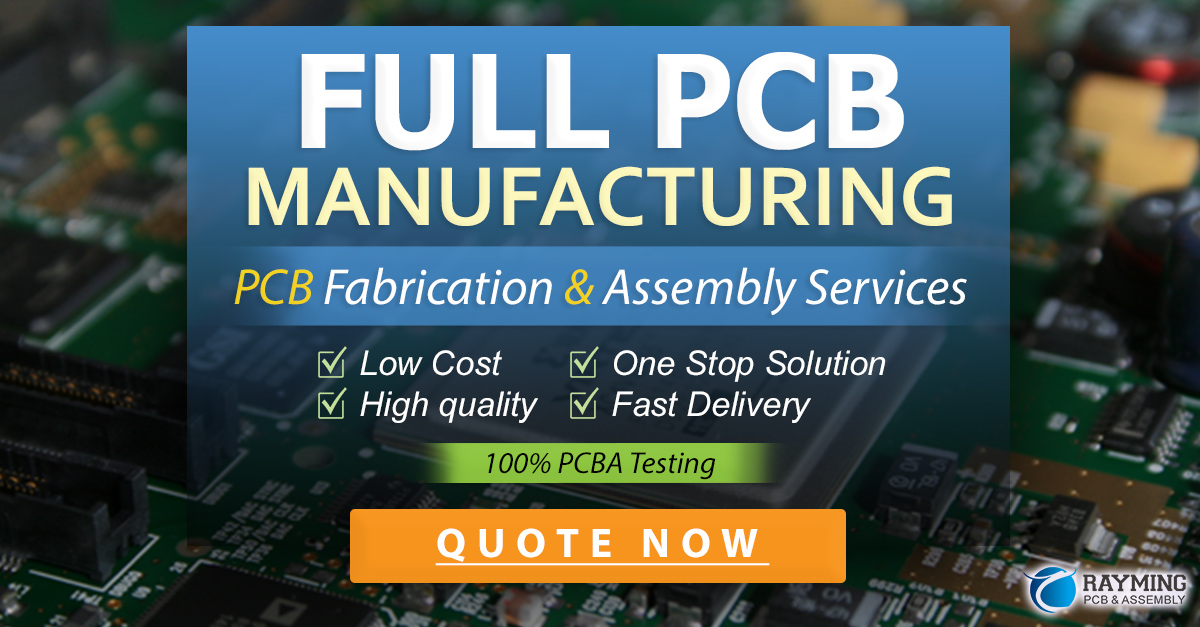
Controlling PCB Thickness Variation
Design Considerations
To minimize PCB thickness variation, the following design considerations should be taken into account:
- Layer stack-up: The layer stack-up should be designed to achieve the desired thickness and minimize variation. The thickness of each layer should be specified, and the total thickness should be within the tolerance limits.
- Copper weight: The copper weight of each layer should be specified and consistent across the board. Variations in copper weight can affect the thickness and electrical properties of the board.
- Via structure: The via structure should be designed to minimize thickness variation. Proper via fill and capping techniques should be used to ensure consistent thickness.
- Material selection: The substrate material should be selected based on its properties and compatibility with the manufacturing process. Materials with low thermal expansion and moisture absorption are preferred for minimizing thickness variation.
Manufacturing Process Control
The manufacturing process should be carefully controlled to minimize thickness variation. The following process parameters should be monitored and controlled:
- Lamination: The lamination process should be optimized to ensure consistent pressure and temperature across the board. The lamination press should be calibrated and maintained regularly.
- Drilling: The drilling process should be optimized to ensure consistent hole size and position. The drill bits should be sharp and replaced regularly to avoid drill wander or breakage.
- Plating: The plating process should be optimized to ensure consistent thickness and uniformity. The plating bath should be monitored and maintained regularly to ensure consistent composition and temperature.
- Etching: The etching process should be optimized to ensure consistent copper removal and line width. The etching solution should be monitored and maintained regularly to ensure consistent composition and temperature.
Quality Control and Inspection
Quality control and inspection procedures should be implemented to ensure that the PCB thickness variation is within the specified tolerance limits. The following quality control methods can be used:
- Incoming material inspection: The incoming materials, such as substrate and copper foil, should be inspected for thickness and uniformity before use.
- In-process inspection: The thickness of the PCB should be measured at various stages of the manufacturing process, such as after lamination, drilling, and plating. Any deviations should be corrected before proceeding to the next step.
- Final inspection: The finished PCB should be inspected for thickness variation using the methods and sampling locations specified in the relevant standards. Any boards that do not meet the specified tolerance limits should be rejected.
Frequently Asked Questions (FAQ)
1. What is the typical thickness of a PCB?
The typical thickness of a PCB ranges from 0.4 mm to 3.2 mm, depending on the number of layers and the application. Common thicknesses include:
- 0.4 mm: Used for flexible PCBs or high-density interconnect (HDI) boards
- 0.8 mm: Used for 1-2 layer boards for simple applications
- 1.6 mm: Used for 4-8 layer boards for general-purpose applications
- 2.4 mm: Used for 10-12 layer boards for complex applications
- 3.2 mm: Used for 14+ layer boards for high-end applications
2. What is the maximum allowable thickness variation for a PCB?
The maximum allowable thickness variation for a PCB depends on the applicable standard and the class of the board. According to IPC standards, the maximum allowable thickness variation is typically ±10% of the nominal thickness.
3. How does PCB thickness affect electrical performance?
PCB thickness affects electrical performance in several ways:
- Impedance: Thicker boards have lower impedance, which can affect signal integrity and power delivery.
- Capacitance: Thicker boards have higher capacitance, which can affect signal speed and power consumption.
- Resistance: Thicker boards have lower resistance, which can affect power delivery and heat generation.
4. How does PCB thickness affect thermal performance?
PCB thickness affects thermal performance by influencing the thermal conductivity and heat dissipation of the board. Thicker boards have better thermal conductivity, which helps dissipate heat more efficiently. This is particularly important for high-power applications or boards with densely packed components.
5. Can PCB thickness variation be completely eliminated?
While it is not possible to completely eliminate PCB thickness variation, it can be minimized through proper design, manufacturing process control, and quality control methods. By following the guidelines and best practices outlined in this article, PCB manufacturers can produce boards with consistent thickness and minimal variation.
Conclusion
PCB thickness variation is a critical parameter that affects the mechanical, electrical, and thermal performance of the board. Maintaining consistent thickness is essential for ensuring reliable operation and manufacturing yield. The IPC standards provide guidelines and specifications for PCB thickness and thickness variation, which should be followed by PCB designers and manufacturers.
To minimize PCB thickness variation, a combination of design considerations, manufacturing process control, and quality control methods should be employed. By carefully controlling the layer stack-up, copper weight, via structure, and material selection, designers can create boards with consistent thickness. By optimizing the lamination, drilling, plating, and etching processes, manufacturers can produce boards with minimal thickness variation. By implementing incoming material inspection, in-process inspection, and final inspection procedures, quality control teams can ensure that the finished boards meet the specified tolerance limits.
In conclusion, understanding and controlling PCB thickness variation is crucial for producing high-quality, reliable PCBs. By following the guidelines and best practices outlined in this article, PCB designers and manufacturers can minimize thickness variation and ensure consistent performance across the board.
No responses yet