Understanding FR4 Material
FR4 is a composite material made from woven fiberglass cloth impregnated with an epoxy resin binder. The “FR” in FR4 stands for “Flame Retardant,” indicating that the material is designed to have excellent flame-resistant properties. The “4” represents the woven glass reinforcement used in the material.
Composition of FR4
The key components of FR4 material are:
- Fiberglass cloth: This is a woven fabric made from fine glass fibers, which provides the structural reinforcement for the material.
- Epoxy resin: A thermosetting polymer that binds the fiberglass cloth together and provides the material’s insulating and flame-retardant properties.
The combination of these two components results in a strong, rigid, and dimensionally stable material that is well-suited for use in electronics.
Mechanical Properties of FR4
To understand the strength of FR4 material, it is essential to examine its mechanical properties. These properties describe how the material responds to various forces and stresses.
Tensile Strength
Tensile strength is a measure of a material’s ability to resist breaking under tension. FR4 has a high tensile strength, which means it can withstand significant stretching forces before breaking. The tensile strength of FR4 is typically in the range of 310 to 380 MPa (45,000 to 55,000 psi), depending on the specific grade and thickness of the material.
Flexural Strength
Flexural strength, also known as bend strength, is a material’s ability to resist bending under load. FR4 exhibits excellent flexural strength, which is essential for PCBs that may be subjected to bending forces during installation or use. The flexural strength of FR4 is usually between 415 and 585 MPa (60,000 to 85,000 psi), depending on the grade and thickness.
Compressive Strength
Compressive strength measures a material’s ability to withstand compression forces without deforming or breaking. FR4 has a high compressive strength, typically ranging from 415 to 585 MPa (60,000 to 85,000 psi). This property is crucial for PCBs that may be subjected to compressive forces during the assembly process or in their final application.
Impact Strength
Impact strength is a material’s ability to absorb sudden, high-energy impacts without breaking. FR4 has a relatively good impact strength, which is important for PCBs that may be exposed to shock or vibration during use. The impact strength of FR4 is typically around 7.5 kJ/m² (3.6 ft-lbs/in²) for a 1.6 mm (0.063 inch) thick sample.
Factors Affecting FR4 Strength
Several factors can influence the strength of FR4 material, including:
Manufacturing Process
The manufacturing process used to produce FR4 can significantly impact its strength. Factors such as the quality of the raw materials, the ratio of fiberglass to epoxy resin, and the curing process can all affect the final properties of the material.
Thickness
The thickness of the FR4 material can also influence its strength. In general, thicker FR4 sheets will have higher absolute strength values compared to thinner sheets. However, the strength-to-weight ratio may be lower for thicker materials.
Temperature
FR4 material properties can be affected by temperature. At elevated temperatures, the material may experience a reduction in strength and stiffness. The glass transition temperature (Tg) of FR4 is typically around 130°C to 140°C (266°F to 284°F), above which the material’s properties begin to degrade.
Moisture
Exposure to moisture can also impact the strength of FR4 material. Water absorption can lead to swelling, reduced mechanical properties, and decreased electrical insulation. However, FR4 is designed to have low moisture absorption rates, typically less than 0.1% by weight.
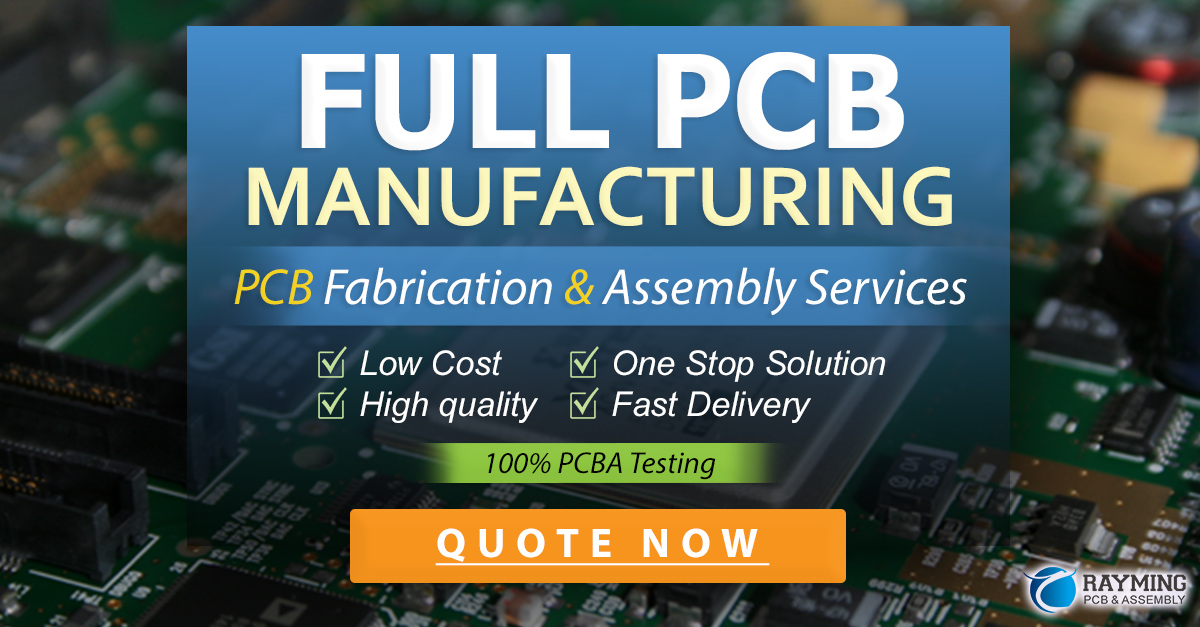
Comparison with Other PCB Materials
To put the strength of FR4 into perspective, it is helpful to compare it with other materials commonly used in PCB manufacturing.
Aluminum
Aluminum is sometimes used as a substrate material for PCBs due to its excellent thermal conductivity. However, aluminum has a lower tensile strength compared to FR4, typically around 90 to 150 MPa (13,000 to 22,000 psi), depending on the alloy. Aluminum also has a lower flexural strength, usually between 100 and 200 MPa (14,500 to 29,000 psi).
Polyimide
Polyimide is another material used in PCBs, particularly for high-temperature applications. Polyimide has a higher tensile strength than FR4, typically ranging from 350 to 450 MPa (51,000 to 65,000 psi). However, its flexural strength is generally lower than FR4, usually between 300 and 400 MPa (43,500 to 58,000 psi).
Ceramics
Ceramic materials, such as alumina (Al₂O₃) and aluminum nitride (AlN), are sometimes used in specialized PCB applications. These materials have very high compressive strengths, often exceeding 1,000 MPa (145,000 psi). However, their tensile and flexural strengths are typically lower than FR4, and they are more brittle, making them less suitable for applications with bending or impact loads.
Applications of FR4 Material
The strength and other desirable properties of FR4 make it a popular choice for various applications, including:
PCBs for Consumer Electronics
FR4 is widely used in the production of PCBs for consumer electronics, such as smartphones, laptops, and televisions. Its high strength and excellent electrical properties make it well-suited for these applications.
Industrial and Automotive Electronics
FR4 is also used in the manufacturing of PCBs for industrial and automotive applications, where reliability and durability are critical. Its strength and flame-retardant properties make it a good choice for these demanding environments.
Aerospace and Military Applications
In aerospace and military applications, where high performance and reliability are essential, FR4 is often used for PCBs. Its strength, combined with its good electrical and thermal properties, make it suitable for these stringent applications.
FR4 Strength Data
To provide a clearer understanding of FR4’s strength, the following table summarizes some of the key mechanical properties of the material:
Property | Value Range | Units |
---|---|---|
Tensile Strength | 310 – 380 | MPa |
Flexural Strength | 415 – 585 | MPa |
Compressive Strength | 415 – 585 | MPa |
Impact Strength (1.6 mm thickness) | ~7.5 | kJ/m² |
It is important to note that these values can vary depending on the specific grade and manufacturer of the FR4 material.
Frequently Asked Questions (FAQ)
-
Q: Is FR4 strong enough for my PCB application?
A: In most cases, yes. FR4 has high tensile, flexural, and compressive strengths, making it suitable for a wide range of PCB applications. However, it is essential to consider the specific requirements of your application and consult with a PCB manufacturer to ensure that FR4 is the best choice. -
Q: How does the strength of FR4 compare to other PCB materials?
A: FR4 has higher tensile and flexural strengths compared to aluminum but lower than polyimide. Ceramics have higher compressive strengths but lower tensile and flexural strengths and are more brittle. Overall, FR4 offers a good balance of strength properties for most PCB applications. -
Q: Can the strength of FR4 be affected by environmental factors?
A: Yes, factors such as high temperatures and moisture exposure can negatively impact the strength of FR4. However, FR4 is designed to have good thermal stability and low moisture absorption, making it suitable for a wide range of operating environments. -
Q: Does the thickness of FR4 material affect its strength?
A: Yes, thicker FR4 sheets generally have higher absolute strength values compared to thinner sheets. However, the strength-to-weight ratio may be lower for thicker materials. -
Q: Can the manufacturing process influence the strength of FR4?
A: Yes, factors such as the quality of raw materials, the ratio of fiberglass to epoxy resin, and the curing process can all impact the final strength properties of FR4. It is important to work with a reputable PCB manufacturer to ensure consistent, high-quality FR4 material.
Conclusion
FR4 is a strong and versatile material that is widely used in the electronics industry for PCBs. Its high tensile, flexural, and compressive strengths, combined with its excellent electrical and thermal properties, make it a popular choice for a wide range of applications, from consumer electronics to aerospace and military systems.
When considering the strength of FR4, it is important to understand its mechanical properties, the factors that can affect its strength, and how it compares to other PCB materials. By taking these aspects into account, designers and engineers can make informed decisions about whether FR4 is the best choice for their specific application.
As the electronics industry continues to evolve, with increasingly complex and demanding applications, the strength and reliability of PCB materials will remain a critical consideration. FR4, with its proven track record and desirable properties, is likely to continue playing a significant role in the development of new electronic devices and systems.
No responses yet