Physical Properties of FR4
To understand the strength of FR4, it’s important to first examine its physical properties. FR4 is a composite material, meaning it is made up of multiple substances. The base material is a flame-resistant epoxy resin that is reinforced with a woven fiberglass cloth. The combination of the epoxy and fiberglass creates a lightweight yet rigid material with excellent mechanical and electrical properties.
Property | Value |
---|---|
Density | 1.85 g/cm³ |
Water Absorption | 0.15% |
Rockwell Hardness | 110 M Scale |
Thermal Conductivity | 0.81 W/(m·K) |
Coefficient of Thermal Expansion | 11-14 ppm/°C |
Dielectric Constant @1MHz | 4.8 |
Dielectric Strength | 20 kV/mm |
Volume Resistivity | 6×10^14 ohm·cm |
As we can see from the table above, FR4 has a relatively high density for a polymer material, contributing to its sturdy feel. It also has very low water absorption, meaning it maintains its strength and dimensions even in humid environments. The high dielectric strength and volume resistivity showcase FR4’s excellent insulating properties.
Mechanical Strength of FR4
One of the standout attributes of FR4 is its mechanical strength. The reinforcing fiberglass cloth gives FR4 a high strength-to-weight ratio, allowing it to withstand significant stresses and loads without breaking.
Tensile Strength
Tensile strength measures a material’s ability to resist breaking under tension (being pulled apart). FR4 boasts an impressive tensile strength, as shown in the table below:
Thickness | Tensile Strength |
---|---|
1.6 mm | 310 MPa |
3.2 mm | 290 MPa |
To put those numbers in perspective, the tensile strength of mild steel is around 370 MPa. So while FR4 may not be quite as strong as steel, it is remarkably strong for a rigid polymer material. This high tensile strength allows FR4 to withstand the stresses of manufacturing processes like drilling and milling without cracking or delaminating.
Flexural Strength
Flexural strength, also known as bend strength, measures a material’s ability to resist bending under load. This is an important property for materials like FR4 that may be subject to bending forces during installation or use.
Thickness | Flexural Strength |
---|---|
1.6 mm | 380 MPa |
3.2 mm | 340 MPa |
As we can see, FR4 demonstrates excellent flexural strength, actually exceeding its tensile strength. This means FR4 is more likely to break under pure tension than from bending. The high flexural strength allows FR4 to maintain its shape and structural integrity even when subjected to flexing and bending.
Impact Strength
Impact strength represents a material’s toughness and ability to absorb sudden impacts without breaking. While FR4 is a rigid material, it does exhibit respectable impact strength due to the woven glass fabric reinforcement.
The Izod notched impact strength of 1.6mm FR4 is around 13 kJ/m². This means FR4 can withstand a decent amount of impact energy before fracturing, though it is not as impact-resistant as more ductile materials like metals. The impact strength contributes to FR4’s durability and damage resistance.
Thermal Strength of FR4
In addition to mechanical strength, thermal strength is a critical consideration for many applications. Electronics, in particular, can generate significant heat that the PCB substrate must withstand. FR4 offers commendable thermal performance.
Glass Transition Temperature (Tg)
The glass transition temperature (Tg) is the temperature range where a polymer transitions from a hard, glassy state to a soft, rubbery state. For FR4, the Tg is around 135°C. This means FR4 maintains its mechanical strength and rigidity up to this temperature.
Decomposition Temperature (Td)
The decomposition temperature (Td) is the temperature at which a material starts to chemically decompose and lose mass. For FR4, the Td is approximately 300°C. This high decomposition temperature, combined with FR4’s flame-resistant properties, makes it well-suited for applications where fire safety is a concern.
Coefficient of Thermal Expansion (CTE)
The coefficient of thermal expansion (CTE) quantifies how much a material expands with increasing temperature. A low CTE is desirable for maintaining dimensional stability under temperature fluctuations. FR4 has a CTE of 11-14 ppm/°C, which is quite low for a polymer material. This dimensional stability is crucial for the precision required in PCB applications.
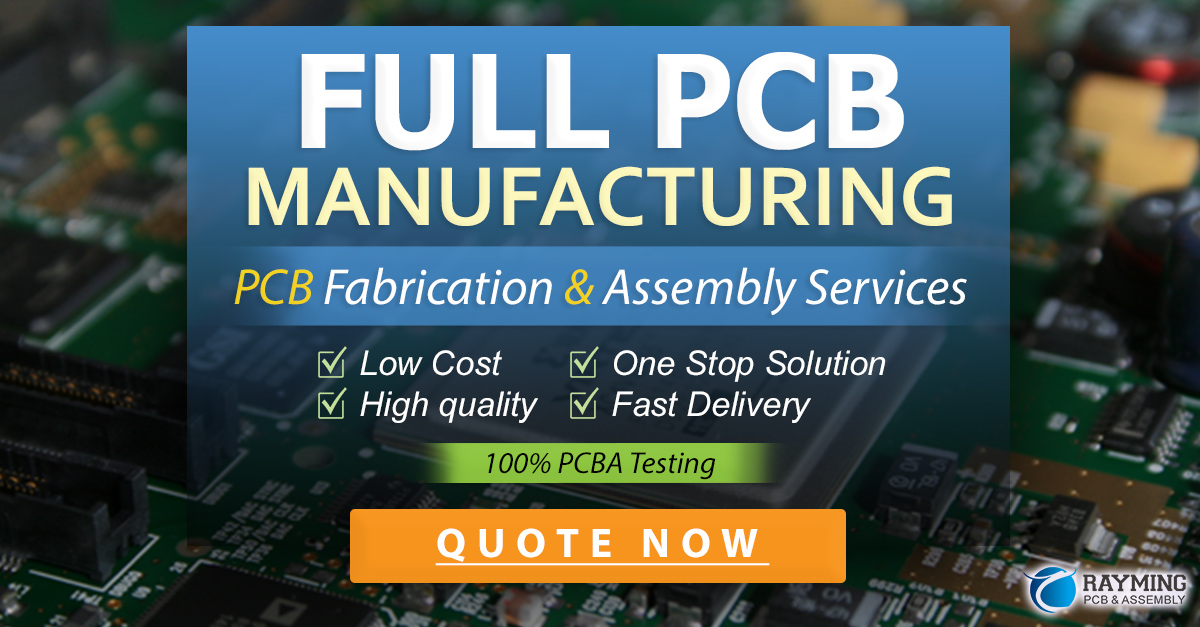
Factors Affecting FR4 Strength
While FR4 exhibits impressive strength overall, there are several factors that can influence its strength in practice:
Resin and Glass Content
The ratio of epoxy resin to glass fiber in FR4 can impact its final properties. Higher glass content generally leads to higher strength and stiffness, while higher resin content improves processability and insulation. The standard glass-to-resin ratio for FR4 is around 40-45% glass by weight.
Weave Style
The type of glass weave used in FR4 can also affect strength. The most common styles are plain weave and twill weave. Plain weave offers the highest strength and stiffness, while twill weave provides a smoother surface finish and slightly better drapeability.
Thickness
As we saw in the tables above, FR4 sheet thickness influences its strength properties. Thicker sheets generally have lower strength values compared to thinner ones. This is because thicker laminates are more susceptible to internal stresses and defects that can act as failure points.
Environmental Conditions
FR4’s strength properties can degrade under certain environmental conditions. High humidity can lead to moisture absorption, which reduces mechanical and insulating properties. Prolonged exposure to high temperatures above the Tg can also cause permanent degradation. For optimal strength, FR4 should be stored and used in a controlled environment.
Applications Leveraging FR4 Strength
FR4’s unique combination of high strength, excellent insulation, and good thermal stability makes it a preferred material for many demanding applications, such as:
Printed Circuit Boards (PCBs)
FR4 is the most widely used base material for rigid PCBs. Its mechanical strength allows it to withstand the rigors of PCB fabrication and assembly, including drilling, soldering, and component placement. The high dielectric strength and insulation resistance ensure reliable electrical performance.
Structural Insulation
In applications requiring both structural support and electrical insulation, such as motor housings or switchgear, FR4 provides an ideal solution. Its high mechanical strength can bear loads and stresses, while its insulating properties prevent electrical faults.
High-Temperature Electronics
For electronics operating in elevated temperature environments, like automotive or aerospace applications, FR4’s thermal stability is invaluable. It can maintain its strength and functionality even at temperatures exceeding 100°C.
Aerospace and Defense
FR4’s strength-to-weight ratio, combined with its flame resistance, makes it attractive for aerospace and defense applications. It is used in avionics, radar systems, and satellite components where reliability and durability are paramount.
FAQ
What is the difference between FR4 and G10?
FR4 and G10 are very similar materials, both being glass-reinforced epoxy laminates. The main difference is that FR4 has flame-retardant properties, while G10 does not. In terms of strength, they are nearly identical.
Can FR4 be used for structural applications?
Yes, FR4 can be used for certain structural applications where high strength and insulation are required. However, for pure structural use, there may be more suitable materials like metals or engineering plastics.
How does FR4 compare to other PCB materials in terms of strength?
FR4 is one of the strongest and most durable PCB substrate materials. It offers higher strength and thermal stability compared to cheaper alternatives like phenolic paper or CEM-1. However, for extremely high-frequency or low-loss applications, specialty materials like Rogers or Teflon may be preferred.
Is FR4 strength affected by the color of the laminate?
No, the color of the FR4 laminate is purely cosmetic and does not impact its strength properties. The most common colors are green and yellow, but black, red, and blue are also available.
What is the maximum operating temperature for FR4?
The maximum operating temperature for FR4 is typically around 130-140°C, close to its glass transition temperature. Prolonged exposure above this temperature can lead to permanent degradation of properties. For higher temperature applications, a different material like polyimide or ceramic may be required.
Conclusion
In conclusion, FR4 is a remarkably strong and versatile material that has rightfully earned its place as the workhorse of the electronics industry. Its high mechanical strength, excellent insulating properties, and good thermal stability make it a top choice for applications ranging from PCBs to structural insulation.
While no material is perfect for every use case, FR4 strikes a compelling balance of properties that make it suitable for a wide range of demanding applications. By understanding the various facets of FR4’s strength, designers and engineers can leverage its capabilities to create reliable, high-performance products.
As technology continues to advance, the strength and durability requirements for materials like FR4 will only increase. Fortunately, ongoing research and development in material science promise even stronger and more capable glass-reinforced laminates in the future. For now, FR4 remains a trusted and indispensable asset in the world of electronics and beyond.
No responses yet