Introduction to PCBs and Their Purpose
A printed circuit board, or PCB, is the backbone of nearly all modern electronic devices. PCBs are used to mechanically support and electrically connect electronic components using conductive pathways, tracks or signal traces etched from copper sheets laminated onto a non-conductive substrate.
The main purpose of a PCB is to provide a means to electrically connect various components together in a controlled manner to create an electronic circuit that performs a specific function. PCBs offer many advantages over other wiring methods such as point-to-point construction or wire wrap, including:
- Compact size
- Reduced electronic noise
- Lower assembly costs
- Improved reliability and consistency
- Easier troubleshooting and repair
In this article, we will explore the purpose of PCBs in more depth, including their role in electronic design, manufacturing, and assembly. We will also discuss the different types of PCBs, their applications, and the benefits they offer over other wiring methods.
The Role of PCBs in Electronic Design
PCB Design Process
The PCB design process is a critical step in the development of any electronic product. It involves creating a schematic diagram that shows the electrical connections between components, then laying out the physical board with the appropriate copper traces, vias, and other features.
PCB design software is used to create the schematic and layout files, which are then sent to a PCB manufacturer for fabrication. Some common PCB design software packages include:
Software | Vendor |
---|---|
Altium Designer | Altium |
Eagle | Autodesk |
KiCad | KiCad |
OrCAD | Cadence |
PADS | Mentor Graphics |
The PCB design process typically involves the following steps:
- Schematic capture: Creating a diagram showing the electrical connections between components.
- Component placement: Arranging the components on the board for optimal performance and manufacturability.
- Routing: Drawing the copper traces that connect the components together.
- Design rule checking (DRC): Verifying that the design meets the manufacturer’s specifications and industry standards.
- Output generation: Creating the files needed for PCB fabrication, such as Gerber files, drill files, and bill of materials (BOM).
PCB Design Considerations
When designing a PCB, there are several key factors to consider to ensure optimal performance, reliability, and manufacturability:
- Component selection: Choosing components that are compatible with the PCB manufacturing process and meet the electrical and environmental requirements of the application.
- Signal integrity: Ensuring that signals are transmitted accurately and reliably between components, without excessive noise, crosstalk, or reflections.
- Power distribution: Providing adequate power to all components while minimizing voltage drop and heat generation.
- Thermal management: Designing the PCB to dissipate heat effectively to prevent component damage and ensure reliable operation.
- Electromagnetic compatibility (EMC): Minimizing electromagnetic interference (EMI) and ensuring compliance with relevant EMC standards.
- Manufacturability: Designing the PCB to be easy to manufacture and assemble, with appropriate tolerances, clearances, and design for manufacturing (DFM) guidelines.
By carefully considering these factors during the design process, PCB designers can create boards that are optimized for performance, reliability, and cost-effectiveness.
PCB Manufacturing Process
PCB Fabrication Steps
Once the PCB design is finalized, the files are sent to a PCB manufacturer for fabrication. The PCB manufacturing process typically involves the following steps:
- Printing the circuit pattern: The copper traces and pads are printed onto the substrate material using a photolithographic process.
- Etching: The unwanted copper is chemically removed, leaving only the desired traces and pads.
- Lamination: Multiple layers of the PCB are bonded together using heat and pressure.
- Drilling: Holes are drilled through the PCB for through-hole components and vias.
- Plating: A thin layer of copper is deposited onto the drilled holes to create electrical connections between layers.
- Solder mask application: A protective layer is applied over the copper traces to prevent short circuits and oxidation.
- Silkscreen printing: Text and symbols are printed onto the PCB for component identification and assembly instructions.
- Surface finish application: A protective coating, such as HASL, ENIG, or OSP, is applied to the exposed copper to prevent oxidation and improve solderability.
- Electrical testing: The PCB is tested for continuity, shorts, and opens to ensure it meets the design specifications.
PCB Materials and Substrates
PCBs can be made from a variety of materials, each with its own advantages and disadvantages. The most common PCB substrate materials are:
Material | Advantages | Disadvantages |
---|---|---|
FR-4 | Low cost, good mechanical strength, flame retardant | Limited high-frequency performance, higher dielectric loss |
Rogers | Excellent high-frequency performance, low dielectric loss | Higher cost, more difficult to process |
Polyimide | High temperature resistance, flexible | Higher cost, lower mechanical strength |
Aluminum | Excellent thermal conductivity, rigid | Higher cost, limited electrical properties |
The choice of substrate material depends on the specific requirements of the application, such as operating frequency, temperature range, and mechanical stress.
In addition to the substrate, PCBs also use copper foil for the conductive traces and pads. The thickness of the copper foil is typically measured in ounces per square foot (oz/ft²), with common thicknesses ranging from 0.5 oz/ft² to 2.0 oz/ft².
PCB Surface Finishes
The exposed copper on a PCB is prone to oxidation, which can degrade its solderability and electrical performance over time. To prevent this, a surface finish is applied to the copper after the etching process. Some common PCB Surface Finishes include:
Finish | Advantages | Disadvantages |
---|---|---|
HASL (Hot Air Solder Leveling) | Low cost, good solderability, easy to inspect | Uneven surface, limited fine-pitch capability |
ENIG (Electroless Nickel Immersion Gold) | Flat surface, excellent solderability, good shelf life | Higher cost, possibility of “black pad” defect |
OSP (Organic Solderability Preservative) | Low cost, flat surface, easy to apply | Limited shelf life, incompatible with some fluxes |
Immersion Silver | Flat surface, good solderability, lower cost than ENIG | Limited shelf life, possibility of tarnishing |
The choice of surface finish depends on the specific requirements of the application, such as shelf life, solderability, and cost.
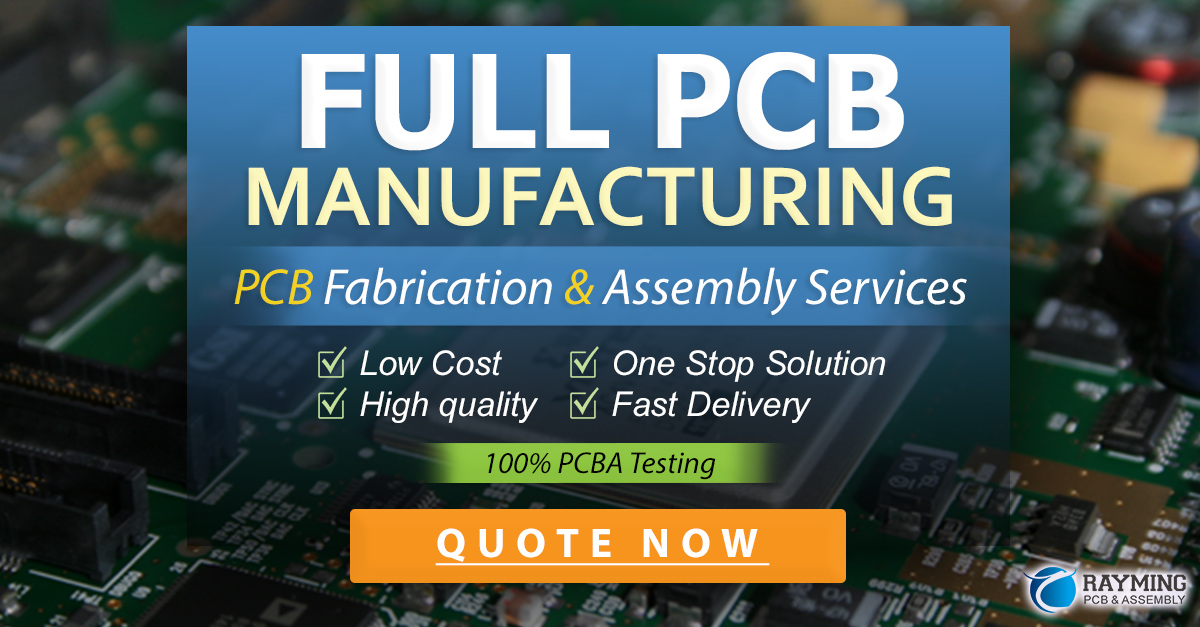
PCB Assembly Process
Through-Hole vs. Surface Mount Technology
PCBs can be assembled using two main methods: through-hole technology (THT) and surface mount technology (SMT). THT involves inserting component leads through holes drilled in the PCB and soldering them on the opposite side. SMT involves placing components directly onto pads on the surface of the PCB and soldering them in place.
SMT has largely replaced THT in modern PCB assembly due to its many advantages, including:
- Smaller component sizes
- Higher component density
- Faster assembly speeds
- Lower assembly costs
- Improved mechanical stability
However, THT is still used for certain components that are not available in SMT packages, or for applications that require higher mechanical strength or power handling capability.
PCB Assembly Steps
The PCB assembly process typically involves the following steps:
- Solder paste application: Solder paste is applied to the pads on the PCB using a stencil or syringe.
- Component placement: Components are placed onto the pads using a pick-and-place machine or by hand.
- Reflow soldering: The PCB is heated in a reflow oven to melt the solder paste and form a permanent electrical and mechanical connection between the components and the PCB.
- Inspection: The assembled PCB is visually inspected for defects such as misaligned components, solder bridges, or insufficient solder joints.
- Testing: The assembled PCB is electrically tested to ensure it functions as intended.
PCB Assembly Challenges
PCB assembly can be a complex and challenging process, particularly for high-density, fine-pitch designs. Some common challenges in PCB assembly include:
- Solder paste printing: Ensuring a consistent and accurate solder paste deposit can be difficult, particularly for fine-pitch components.
- Component placement: Accurate placement of small, closely-spaced components can be challenging, particularly for high-volume production.
- Reflow soldering: Achieving an optimal reflow profile that ensures complete solder joint formation without damaging components can be difficult, particularly for mixed-technology designs.
- Inspection: Detecting and diagnosing assembly defects can be challenging, particularly for hidden or inaccessible solder joints.
To overcome these challenges, PCB assemblers use a variety of techniques and technologies, such as:
- Automated solder paste inspection (SPI) systems to verify solder paste deposits
- High-precision pick-and-place machines with vision systems for accurate component placement
- Reflow ovens with precise temperature control and profiling capabilities
- Automated optical inspection (AOI) and X-ray inspection systems for detecting assembly defects
By using these tools and following best practices for PCB assembly, manufacturers can produce high-quality, reliable PCBs with minimal defects and rework.
Applications of PCBs
PCBs are used in a wide range of applications across many industries, including:
- Consumer electronics: Smartphones, laptops, televisions, gaming consoles, wearables
- Automotive: Engine control units, infotainment systems, sensors, power electronics
- Medical devices: Diagnostic equipment, monitoring systems, implantable devices
- Aerospace: Avionics, satellite systems, radar, communication equipment
- Industrial automation: Control systems, sensors, motors, power supplies
- Military: Communication systems, navigation equipment, weapons systems
- IoT: Smart home devices, wearables, sensors, gateways
In each of these applications, PCBs play a critical role in providing the electrical connectivity and mechanical support needed for the device to function properly. The specific requirements for each application can vary widely, such as the operating environment, power requirements, and signal integrity needs.
For example, PCBs used in aerospace applications may need to withstand extreme temperatures, vibration, and radiation, while PCBs used in medical devices may need to be biocompatible and meet strict regulatory requirements. PCBs used in high-speed digital applications may require careful signal integrity analysis and design techniques to ensure reliable data transmission.
By understanding the unique requirements of each application, PCB designers and manufacturers can create boards that are optimized for performance, reliability, and cost-effectiveness. This requires close collaboration between the PCB design team, the device manufacturer, and the end customer to ensure that all requirements are met and the final product meets or exceeds expectations.
Benefits of Using PCBs
Using PCBs offers many benefits over other wiring methods, such as point-to-point wiring or wire wrapping. Some of the key benefits of using PCBs include:
- Compact size: PCBs allow for high-density component placement and routing, enabling smaller and more compact device designs.
- Improved reliability: PCBs provide a stable and reliable means of connecting components, reducing the risk of wiring errors or loose connections.
- Lower assembly costs: PCBs can be assembled quickly and efficiently using automated equipment, reducing labor costs and improving consistency.
- Reduced electronic noise: PCBs provide a low-impedance path for signals and power, reducing the risk of electromagnetic interference (EMI) and signal integrity issues.
- Easier troubleshooting and repair: PCBs are designed with testability in mind, making it easier to diagnose and repair faults compared to other wiring methods.
In addition to these benefits, using PCBs also enables more advanced manufacturing techniques, such as automated optical inspection (AOI) and boundary scan testing, which can further improve quality and reduce defects.
By leveraging the benefits of PCBs, manufacturers can create more reliable, cost-effective, and high-performing electronic devices that meet the needs of their customers. As electronic devices continue to become more complex and sophisticated, the role of PCBs in enabling these advances will only continue to grow in importance.
FAQs
1. What is the difference between a PCB and a breadboard?
A breadboard is a prototyping tool used to temporarily connect electronic components together for testing and experimentation. It consists of a plastic board with rows of interconnected sockets that allow components to be inserted and removed easily. Breadboards are useful for quickly testing circuit designs and making changes on the fly.
In contrast, a PCB is a permanent, custom-designed board that provides a stable and reliable means of connecting components together. PCBs are fabricated using specialized equipment and materials, and are designed to meet specific performance and reliability requirements. Unlike breadboards, PCBs are not intended to be modified or reconfigured once they are manufactured.
2. Can PCBs be repaired if they are damaged?
In some cases, PCBs can be repaired if they are damaged, but the feasibility and cost-effectiveness of repair depends on the extent and nature of the damage. Minor damage, such as a broken trace or lifted pad, can often be repaired using soldering techniques or conductive epoxy. More extensive damage, such as a cracked or broken board, may require more complex repair techniques or may not be repairable at all.
In general, it is often more cost-effective to replace a damaged PCB rather than attempting to repair it, particularly for high-volume production or critical applications where reliability is paramount. However, for prototype or low-volume boards, repair may be a viable option if the damage is limited and the repair can be performed reliably.
3. What is the typical turnaround time for PCB fabrication and assembly?
The turnaround time for PCB fabrication and assembly can vary widely depending on the complexity of the design, the materials and processes used, and the workload of the manufacturer. In general, simple two-layer PCBs can be fabricated in as little as 24-48 hours, while more complex multi-layer boards may take several days or weeks to fabricate.
Assembly times can also vary depending on the complexity of the board and the number of components to be placed. Simple boards with a small number of components can often be assembled in a matter of hours, while more complex boards with hundreds or thousands of components may take several days or weeks to assemble.
To minimize turnaround times and ensure timely delivery, it is important to work closely with the PCB manufacturer and assembly provider to understand their capabilities, lead times, and requirements. Providing complete and accurate design files, bill of materials (BOM), and assembly instructions can also help to streamline the process and avoid delays.
4. What are some common PCB design software packages?
There are many PCB design software packages available, ranging from free and open-source tools to high-end commercial packages. Some of the most common PCB design software packages include:
- Altium Designer: A powerful and feature-rich PCB design package used by many professional designers and engineers.
- Eagle: A popular PCB design package that is available in both free and paid versions, with a large user community and extensive libraries.
- KiCad: A free and open-source PCB design package that is gaining popularity among hobbyists and small businesses.
- OrCAD: A widely-used PCB design package that is part of the Cadence design suite, with advanced features for high-speed and high-density designs.
- PADS: A PCB design package from Mentor Graphics that is known for its ease of use and integration with other tools in the Mentor Graphics suite.
Each of these packages has its own strengths and weaknesses, and the choice of software often depends on factors such as cost, ease of use, feature set, and compatibility with other tools and processes used in the design and manufacturing workflow.
5. What are some common PCB manufacturing defects to watch out for?
There are many potential defects that can occur during PCB manufacturing, some of which can be difficult to detect and can lead to reliability issues or failures in the field. Some of the most common PCB manufacturing defects to watch out for include:
- Shorts: Unintended electrical connections between traces, pads, or planes, often caused by manufacturing process issues such as overetching, underetching, or solder bridging.
- Opens: Missing or broken connections between traces, pads, or planes, often caused by manufacturing process issues such as underetching, overetching, or mechanical damage.
- Misregistration: Misalignment between layers of the PCB, often caused by issues with the registration or lamination process.
- Solder defects: Issues with the solder joints, such as insufficient solder, excess solder, or poor wetting, often caused by issues with the solder paste printing or reflow process.
- Contamination: Foreign material or residues on the PCB surface, often caused by issues with the cleaning or handling process.
To minimize the risk of these defects, it is important to work with a reputable PCB manufacturer that follows industry best practices and has robust quality control processes in place. Additionally, designing the PCB with manufacturability in mind, such as using appropriate trace widths and spacings, can help to reduce the risk of defects and improve yields.
Regular inspection and testing of the
No responses yet