Understanding PCB dimensions
PCB dimensions refer to the physical measurements of a printed circuit board, specifically its length and width. These dimensions are typically expressed in inches or millimeters and can vary greatly depending on the specific application and design requirements of the PCB.
Standard PCB Sizes
While PCBs can be custom-designed to fit specific dimensions, there are several standard sizes that are commonly used in the electronics industry. These standard sizes help ensure compatibility with existing components and enclosures, and can often lead to cost savings due to their widespread availability.
Some of the most common standard PCB sizes include:
Size | Dimensions (mm) | Dimensions (inches) |
---|---|---|
Credit Card Size | 85.60 x 53.98 | 3.370 x 2.125 |
Business Card Size | 88.9 x 50.8 | 3.5 x 2.0 |
Raspberry Pi Size | 85 x 56 | 3.35 x 2.20 |
Arduino Uno Size | 68.58 x 53.34 | 2.7 x 2.1 |
Breadboard Size | 165 x 55 | 6.5 x 2.17 |
It’s important to note that these are just a few examples of standard PCB sizes, and there are many other sizes available depending on the specific industry and application.
Factors Influencing PCB Dimensions
Several factors can influence the dimensions of a PCB, including:
-
Component Size and Placement: The size and placement of components on the PCB will directly impact its overall dimensions. Larger components or a higher number of components will require a larger PCB to accommodate them.
-
Functionality and Complexity: The functionality and complexity of the PCB’s design will also play a role in determining its dimensions. More complex designs with a greater number of layers and connections will typically require larger PCBs.
-
Enclosure and Mounting Requirements: If the PCB needs to fit within a specific enclosure or be mounted in a particular way, this will influence its dimensions. The PCB must be designed to fit within the available space and accommodate any necessary mounting holes or connectors.
-
Manufacturing Constraints: The capabilities and constraints of the PCB manufacturing process can also impact the dimensions of the board. Certain manufacturing techniques may have limitations on the minimum or maximum sizes that can be produced.
Designing PCBs with Specific Dimensions
When designing a PCB with specific dimensions, there are several key considerations to keep in mind:
Board Shape and Routing
The shape of the PCB and the routing of traces and components can have a significant impact on its dimensions. When designing a PCB with specific size requirements, it’s important to carefully plan the placement of components and the routing of traces to ensure that everything fits within the available space.
In some cases, it may be necessary to use creative routing techniques or multi-layer designs to accommodate all of the necessary components and connections within a limited space.
Clearance and Tolerances
When designing a PCB with specific dimensions, it’s important to consider the clearance and tolerances required for proper functionality and manufacturability. This includes ensuring adequate spacing between components and traces, as well as accounting for any necessary edge clearance or mounting hole tolerances.
Failure to properly account for clearance and tolerances can result in a PCB that doesn’t fit within its intended enclosure or fails to function properly due to short circuits or other issues.
Panelization and Breakout Tabs
If the PCB will be manufactured in a panel with multiple boards, it’s important to consider the panelization and breakout tab requirements when determining the dimensions of the individual boards.
Panelization refers to the process of grouping multiple PCBs together on a single panel for manufacturing purposes. This can help reduce costs and improve efficiency, but it also requires careful planning to ensure that each individual board meets its specified dimensions after being separated from the panel.
Breakout tabs are small sections of the PCB that are designed to be broken off after manufacturing, typically to separate individual boards from a panel or to remove any unused portions of the board. When designing a PCB with specific dimensions, it’s important to account for any necessary breakout tabs and ensure that they don’t interfere with the final dimensions of the board.
Common PCB Dimension Challenges and Solutions
Designing and manufacturing PCBs with specific dimensions can present several challenges, but there are often solutions available to overcome these challenges.
Limited Space
One of the most common challenges when designing PCBs with specific dimensions is limited space. When the available space is limited, it can be difficult to accommodate all of the necessary components and connections while still maintaining the desired dimensions.
To overcome this challenge, designers can use several techniques, such as:
- Using smaller components or miniaturized versions of components
- Implementing multi-layer designs to increase the available routing space
- Utilizing creative routing techniques, such as diagonal traces or via-in-pad designs
- Prioritizing the placement of critical components and connections
High Component Density
Another challenge that can arise when designing PCBs with specific dimensions is high component density. When a large number of components need to be placed on a small board, it can be difficult to maintain proper spacing and clearance while still meeting the desired dimensions.
To address this challenge, designers can:
- Use smaller-pitch components, such as fine-pitch QFP or BGA packages
- Implement high-density interconnect (HDI) techniques, such as blind and buried vias
- Utilize advanced manufacturing techniques, such as 3D printing or embedded components
- Carefully plan the placement and orientation of components to maximize available space
Manufacturing Limitations
In some cases, the desired dimensions of a PCB may push the limits of what is possible with current manufacturing techniques. This can present challenges in terms of manufacturability, reliability, and cost.
To work around manufacturing limitations, designers can:
- Consult with the manufacturer early in the design process to understand their capabilities and constraints
- Consider alternative manufacturing techniques, such as flexible or rigid-flex PCBs
- Modify the design to better align with manufacturing capabilities, such as increasing trace widths or spacing
- Accept a slightly larger or smaller PCB size to accommodate manufacturing requirements
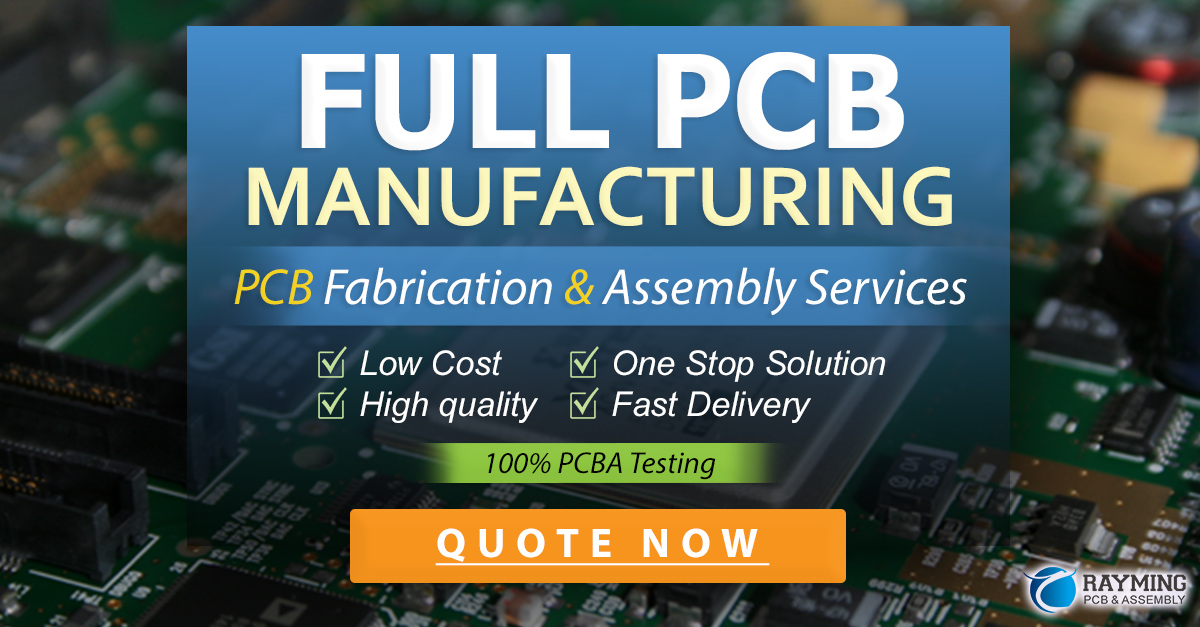
Frequently Asked Questions (FAQ)
- What is the minimum size PCB that can be manufactured?
The minimum size of a PCB that can be manufactured depends on the capabilities of the specific manufacturer and the complexity of the design. In general, most manufacturers can produce PCBs as small as 0.5 inches by 0.5 inches (12.7mm x 12.7mm). However, some specialized manufacturers may be able to produce even smaller PCBs, down to 0.3 inches by 0.3 inches (7.62mm x 7.62mm) or less.
- Can I design a PCB with non-standard dimensions?
Yes, PCBs can be designed with non-standard dimensions to fit specific application or enclosure requirements. However, it’s important to keep in mind that non-standard dimensions may increase manufacturing costs or lead times, as they may require specialized tooling or processing.
- How do I determine the appropriate dimensions for my PCB?
To determine the appropriate dimensions for your PCB, consider factors such as the size and number of components, the complexity of the design, any enclosure or mounting requirements, and manufacturing constraints. It’s also a good idea to consult with the PCB manufacturer early in the design process to ensure that your desired dimensions are feasible and cost-effective.
- What is the maximum size PCB that can be manufactured?
The maximum size of a PCB that can be manufactured depends on the capabilities of the specific manufacturer and the manufacturing process being used. In general, most manufacturers can produce PCBs up to 24 inches by 36 inches (609.6mm x 914.4mm) or larger. However, very large PCBs may require specialized equipment or processing, which can increase costs and lead times.
- How can I reduce the size of my PCB while still maintaining functionality?
To reduce the size of your PCB while still maintaining functionality, consider using smaller components, implementing multi-layer designs, utilizing advanced manufacturing techniques, and carefully planning the placement and routing of components and traces. It may also be necessary to prioritize certain functions or components over others to achieve the desired size reduction.
Conclusion
PCB dimensions play a critical role in the design and functionality of electronic devices. By understanding the factors that influence PCB dimensions, as well as the common challenges and solutions associated with designing boards with specific sizes, designers can create PCBs that meet their unique requirements while still being manufacturable and cost-effective.
When designing a PCB with specific dimensions, it’s important to consider factors such as component size and placement, functionality and complexity, enclosure and mounting requirements, and manufacturing constraints. By carefully planning the placement and routing of components and traces, utilizing advanced design and manufacturing techniques, and working closely with the PCB manufacturer, designers can overcome common challenges and create PCBs that meet their exact specifications.
Ultimately, the key to success when designing PCBs with specific dimensions is careful planning, attention to detail, and close collaboration with the manufacturing team. By following best practices and leveraging the latest technologies and techniques, designers can create PCBs that are both functional and cost-effective, while still meeting their unique size and shape requirements.
No responses yet