Teflon’s generic name: Polytetrafluoroethylene (PTFE)
The generic chemical name for Teflon is polytetrafluoroethylene, or PTFE for short. PTFE is a synthetic fluoropolymer of tetrafluoroethylene, with the chemical formula (C2F4)n.
PTFE Chemical Structure
PTFE is composed of carbon and fluorine atoms bonded together in a chain, with two fluorine atoms attached to each carbon:
F F
| |
–C – C–
| |
F F
The carbon-fluorine bonds in PTFE are extremely strong, making it a very stable and inert material. The fluorine atoms also surround the carbon backbone, shielding it and giving PTFE its non-stick and hydrophobic properties.
Discovery and Development of PTFE
PTFE was accidentally discovered in 1938 by Roy Plunkett, a chemist at DuPont. Plunkett was attempting to make a new chlorofluorocarbon refrigerant when he noticed that the tetrafluoroethylene gas in a pressurized cylinder had polymerized into a white, waxy solid inside the container.
Recognizing that this substance had unique properties, Plunkett and his colleagues at DuPont investigated further. In 1941, they patented PTFE and registered it under the Teflon brand name in 1945. DuPont first used Teflon commercially in 1946 as a coating for valves and seals in the Manhattan Project to develop the atomic bomb.
In the 1950s and 60s, DuPont introduced Teflon-coated non-stick cookware, which became widely popular. Since then, PTFE has found many more applications across various industries.
Properties of PTFE
PTFE has a combination of useful physical, chemical, electrical, and thermal properties that make it valuable for many applications:
Physical Properties
- Low friction coefficient (slippery, non-stick surface)
- Hydrophobic (repels water)
- High flexibility
- Resistant to adhesion
- Resistant to weathering and UV radiation
- Translucent or opaque white solid
Chemical Properties
- Chemically inert and resistant to most chemicals
- Resistant to acids, bases, solvents, oxidizers
- Only reactive with molten alkali metals and elemental fluorine
- Insoluble in water and organic solvents
Thermal Properties
- High melting point (327°C / 620°F)
- Remains stable up to 260°C (500°F)
- Low thermal conductivity
- Resistant to extreme cold
Electrical Properties
- Excellent electrical insulator
- High dielectric strength
- Low dielectric constant
- Dissipates static charge
Property | Value |
---|---|
Density | 2.2 g/cm3 |
Melting Point | 327°C (620°F) |
Thermal Conductivity | 0.25 W/(m·K) |
Coefficient of Friction | 0.05-0.10 |
Dielectric Constant | 2.1 (at 1 MHz) |
Dielectric Strength | 24 MV/m |
These properties remain very stable over a wide temperature range from -270 to 260 °C (-454 to 500 °F). PTFE’s low reactivity also allows it to be used with corrosive chemicals and in harsh environments. Its low friction and non-stick surface make it ideal for reducing wear, friction, and adhesion.
Applications of PTFE
PTFE’s unique properties make it useful across many industries for various applications:
Cookware and Food Processing
- Non-stick coating for pots, pans, and appliances
- Coating for conveyor belts, rollers, and molds
- Tubing for beverage and food processing
Chemical Processing
- Lining for pipes, valves, and containers
- Gaskets and seals for pumps and compressors
- Filter membranes for acids, gases, solvents
- Non-reactive labware (beakers, bottles, trays)
Automotive and Aerospace
- Wiring and cables insulation
- Bearing and bushing liners
- Gaskets and O-rings for engines, hydraulics
- Anti-icing coating for aircraft
Electronics
- Insulation for wires and cables
- Printed circuit board coating
- Semiconductor manufacturing components
Textiles and Apparel
- Breathable, waterproof fabrics (Gore-Tex)
- Stain-resistant upholstery and carpet
- Sewing thread
Medical and Pharmaceutical
- Surgical grafts and sutures
- Coating for catheters and guidewires
- Pharmaceutical processing components
Other applications include lubricants, dental floss, tape, composites, and more. PTFE’s low friction also allows it to be used as a dry lubricant in the form of powder or tape.
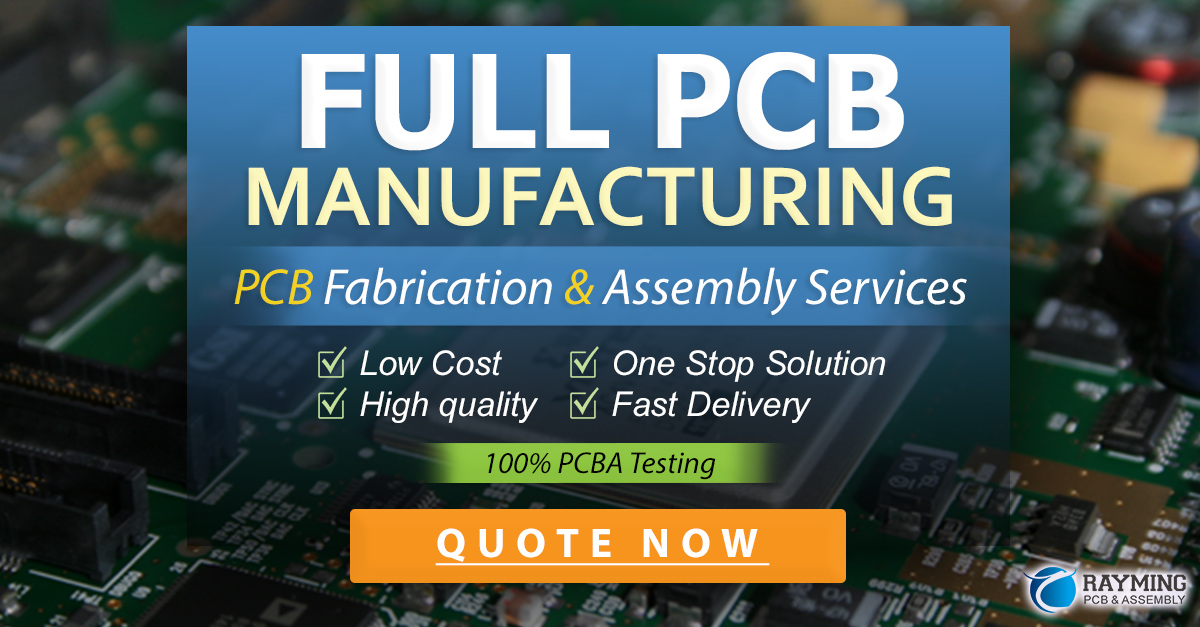
Processing and Fabrication of PTFE
PTFE is typically processed and fabricated using techniques different from other polymers due to its high melting temperature and resistance to dissolving:
Molding
-
Compression molding: PTFE powder is compressed into a preform shape and then sintered (heated below melting point) to fuse it into a solid.
-
Ram extrusion: Molten PTFE is forced through a die to create rods, tubes, and profiles. The extruded part is then sintered.
Machining
- PTFE can be machined by sawing, turning, milling, or drilling in a similar way to soft metals. Tools must be sharp and cooling is necessary to prevent overheating.
Skiving
- Thin PTFE film is skived (shaved or split) from a thicker block using a sharp blade. The film can be used for tape, gaskets, and liners.
Dispersion Coating
- An aqueous dispersion of PTFE particles is used to impregnate or coat materials like fabric and metal. The coating is then dried and fused.
Post-processing techniques like surface etching and metallization can also be used to modify the surface properties of PTFE for bonding or printing.
Advantages and Disadvantages of PTFE
PTFE has many advantages stemming from its unique properties, but also some disadvantages and limitations.
Advantages
- Excellent non-stick properties reduce adhesion and fouling
- Low friction reduces wear and energy loss
- High chemical resistance allows use with reactive media
- Wide temperature range from cryogenic to 260°C (500°F)
- Excellent electrical insulator with low dielectric loss
- Low flammability and smoke generation
- Physiologically inert (non-toxic, biologically compatible)
Disadvantages
- High cost compared to other polymers
- Difficult to process due to high melting point
- Cannot be melt-processed like other thermoplastics
- Limited mechanical strength and wear-resistance
- Creeps (deforms) under load, especially at high temperature
- Attacked by molten alkali metals and elemental fluorine
- Can decompose at temperatures above 260°C (500°F)
Despite these limitations, the advantages of PTFE make it an essential material for many critical applications where its unique properties are needed.
Safety and Environmental Considerations
PTFE is generally considered safe and inert in its solid form. It is approved for use in food contact and medical implants. However, there are some safety and environmental considerations:
Thermal Decomposition
- PTFE can start to decompose above 260°C (500°F), releasing toxic fumes. Overheated PTFE from unattended cookware can cause polymer fume fever, a temporary flu-like condition.
PFOA and Environmental Concerns
-
Perfluorooctanoic acid (PFOA) was historically used as a surfactant during PTFE manufacturing. PFOA is a persistent pollutant and is linked to health issues. Since 2015, PTFE is manufactured using alternative surfactants.
-
PTFE and other fluoropolymers are extremely persistent in the environment and can accumulate in organisms. Proper disposal and incineration above 800°C is recommended.
With proper use and handling, PTFE remains a safe and valuable material. Continuing research aims to develop more sustainable and environmentally-friendly fluoropolymers.
Frequently Asked Questions (FAQ)
- Is Teflon the same as PTFE?
-
Teflon is a brand name for PTFE-based products made by Chemours (formerly DuPont). While “Teflon” is often used synonymously with PTFE, not all PTFE products are Teflon.
-
Is PTFE safe for cookware?
-
PTFE-coated non-stick cookware is safe when used properly below 260°C (500°F). Overheating PTFE can cause decomposition and release of toxic fumes.
-
How long does PTFE last?
-
The lifespan of PTFE depends on the application and conditions. A PTFE coating may last 3-5 years with normal use, while PTFE parts can last decades under the right conditions.
-
Can PTFE be recycled?
-
PTFE is difficult to recycle because it cannot be remelted or dissolved. Recycled PTFE is usually downcycled into lower-grade products. Proper disposal through landfill or high-temperature incineration is recommended.
-
Are there alternatives to PTFE?
- Other fluoropolymers like PFA and FEP have similar properties to PTFE. Some non-fluoropolymer alternatives include ceramics, silicone, and sol-gel coatings, but may not match PTFE’s performance.
In conclusion, PTFE, the generic name for Teflon, is a unique and versatile fluoropolymer with a wide range of applications. Its non-stick, low-friction, heat-resistant, and chemically inert properties make it valuable in cookware, chemical processing, electronics, textiles, and more. While PTFE has some limitations and environmental concerns, it remains an essential material for many industries. Ongoing research continues to improve the safety, sustainability, and performance of PTFE and related fluoropolymers.
No responses yet