Understanding PCB Frequency
What is PCB Frequency?
PCB frequency, also known as the operating frequency, refers to the number of cycles per second at which a signal oscillates within a PCB. It is measured in Hertz (Hz), with one Hertz representing one cycle per second. The higher the frequency, the faster the signal oscillates, enabling faster data transmission and processing.
Why is PCB Frequency Important?
In today’s digital age, electronic devices are required to process and transmit data at ever-increasing speeds. High-speed PCBs are essential for applications such as high-speed communication systems, high-performance computing, and advanced medical equipment. The frequency of a PCB directly impacts its ability to handle high-speed signals and maintain signal integrity.
Factors Affecting PCB Frequency
Several factors influence the frequency of a high-speed PCB. Let’s explore some of the key factors:
1. Material Properties
The choice of substrate material plays a significant role in determining the frequency of a PCB. The dielectric constant (Dk) and dissipation factor (Df) of the material affect the signal propagation speed and loss. Materials with lower Dk and Df values, such as Rogers RO4003C or Isola IS410, are preferred for high-speed applications as they minimize signal loss and allow for higher frequencies.
2. Trace Geometry
The geometry of the traces on a PCB also impacts its frequency. Trace width, thickness, and spacing all contribute to the characteristic impedance and signal integrity. Narrower traces and tighter spacing enable higher frequencies but also introduce challenges in manufacturing and signal integrity management. Careful design and simulation are necessary to optimize trace geometry for the desired frequency.
3. Via Design
Vias are used to connect traces on different layers of a PCB. However, vias can introduce discontinuities and reflections that affect signal integrity at high frequencies. To mitigate these issues, techniques such as via stubs, back-drilling, and blind/buried vias are employed. Proper via design and placement are crucial for maintaining signal integrity and achieving high frequencies.
4. Power and Ground Planes
The design of power and ground planes is critical for high-speed PCBs. Inadequate power and ground distribution can lead to noise, crosstalk, and signal degradation. Techniques such as power plane segmentation, decoupling capacitors, and proper grounding strategies help to maintain a clean and stable power supply, enabling higher frequencies and better signal quality.
High-Speed PCB Design Considerations
Designing a high-speed PCB requires careful consideration of various factors to ensure optimal performance. Here are some key design considerations:
1. Signal Integrity Analysis
Signal integrity analysis is essential to evaluate the behavior of high-speed signals on a PCB. Tools such as time-domain reflectometry (TDR) and vector network analyzers (VNA) are used to measure and analyze signal integrity parameters such as impedance, reflection, and crosstalk. Simulation software can also be employed to predict and optimize signal integrity before fabrication.
2. Impedance Matching
Impedance matching is crucial for ensuring proper signal transmission and minimizing reflections. The characteristic impedance of the traces should match the impedance of the source and load to prevent signal degradation. Techniques such as controlled impedance routing and termination resistors are used to achieve impedance matching.
3. Electromagnetic Compatibility (EMC)
High-speed PCBs are susceptible to electromagnetic interference (EMI) and can also emit electromagnetic radiation. EMC considerations, such as proper shielding, grounding, and filtering, are necessary to minimize EMI and ensure compliance with regulatory standards. Techniques such as ground planes, shielding cans, and ferrite beads can be employed to mitigate EMC issues.
4. Thermal Management
High-speed PCBs generate significant heat due to the increased power consumption of the components. Proper thermal management is essential to prevent overheating and ensure reliable operation. Techniques such as thermal vias, heatsinks, and thermal interface materials can be used to dissipate heat effectively. Thermal simulation tools can help in identifying hot spots and optimizing the thermal design.
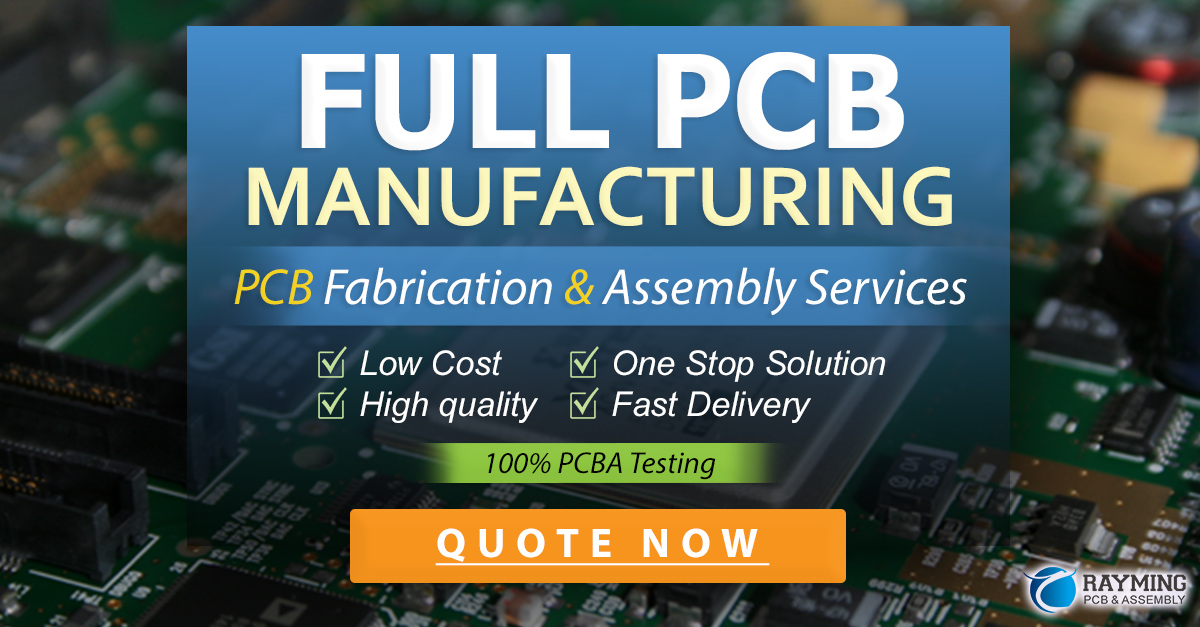
PCB Frequency Range and Applications
The frequency range of high-speed PCBs varies depending on the application and the specific requirements. Here are some common frequency ranges and their corresponding applications:
Frequency Range | Applications |
---|---|
100 MHz – 1 GHz | High-speed digital circuits, computer peripherals |
1 GHz – 10 GHz | Wireless communication systems, radar, satellite |
10 GHz – 100 GHz | Millimeter-wave applications, 5G networks, automotive radar |
As the frequency increases, the design challenges and manufacturing complexities also increase. PCBs operating at higher frequencies require advanced materials, precise manufacturing processes, and stringent quality control measures.
Frequently Asked Questions (FAQ)
-
Q: What is the typical frequency range for high-speed PCBs?
A: The typical frequency range for high-speed PCBs can vary from 100 MHz to 100 GHz, depending on the specific application and requirements. -
Q: What materials are commonly used for high-speed PCBs?
A: Materials with low dielectric constant and dissipation factor, such as Rogers RO4003C, Isola IS410, and Nelco N4000-13, are commonly used for high-speed PCBs to minimize signal loss and achieve higher frequencies. -
Q: How does trace geometry affect PCB frequency?
A: Trace geometry, including width, thickness, and spacing, influences the characteristic impedance and signal integrity of a PCB. Narrower traces and tighter spacing enable higher frequencies but also introduce challenges in manufacturing and signal integrity management. -
Q: What is the purpose of via stubs and back-drilling in high-speed PCBs?
A: Via stubs and back-drilling are techniques used to mitigate the discontinuities and reflections introduced by vias at high frequencies. Via stubs are shortened to reduce the stub length, while back-drilling removes the unused portion of the via to improve signal integrity. -
Q: Why is impedance matching important in high-speed PCB design?
A: Impedance matching is crucial for ensuring proper signal transmission and minimizing reflections in high-speed PCBs. Matching the characteristic impedance of the traces to the impedance of the source and load prevents signal degradation and ensures optimal performance.
Conclusion
The frequency of a high-speed PCB is a critical factor that determines its ability to handle high-speed signals and maintain signal integrity. Understanding the factors that influence PCB frequency, such as material properties, trace geometry, via design, and power and ground planes, is essential for designing and manufacturing high-performance PCBs.
Designing a high-speed PCB requires careful consideration of signal integrity, impedance matching, electromagnetic compatibility, and thermal management. By employing advanced materials, precise manufacturing processes, and rigorous testing and validation, designers can ensure the reliability and performance of high-speed PCBs across various applications.
As technology continues to evolve, the demand for higher frequencies and faster data transmission will only increase. Staying up-to-date with the latest advancements in materials, design techniques, and manufacturing processes will be crucial for engineers and manufacturers to meet the ever-growing demands of the electronics industry.
No responses yet