Introduction
In the world of electronics manufacturing, two terms that often cause confusion are Solder Mask and Solder Paste. While they both play crucial roles in the production of printed circuit boards (PCBs), they serve very different purposes. Understanding the distinction between solder mask and solder paste is essential for anyone involved in the design, fabrication, or assembly of electronic devices.
What is Solder Mask?
Definition and Purpose
Solder mask, also known as solder resist or solder stop, is a protective coating applied to the copper traces of a PCB. Its primary purpose is to prevent solder from adhering to areas where it is not intended to be during the soldering process. By selectively covering certain regions of the board, solder mask helps to ensure that solder only bonds to the exposed metal pads and component leads.
Composition and Application
Solder mask is typically made of a polymer-based material, such as epoxy or acrylic, that is mixed with pigments to give it color. The most common colors for solder mask are green, red, blue, and black, although other colors are available for specific applications. The solder mask is applied to the PCB using various methods, including screen printing, liquid photoimaging, or dry film photoimaging.
Benefits of Solder Mask
- Insulation: Solder mask acts as an insulating layer, preventing short circuits between adjacent traces and components.
- Protection: The coating shields the copper traces from oxidation, corrosion, and mechanical damage.
- Aesthetics: Solder mask gives the PCB a professional and finished appearance, making it easier to identify components and traces.
- Solder Control: By restricting solder to specific areas, solder mask reduces the risk of solder bridges and other defects.
What is Solder Paste?
Definition and Purpose
Solder paste is a suspension of tiny solder particles in a flux medium. It is used to form electrical and mechanical connections between components and the PCB during the surface mount assembly process. Solder paste is applied to the exposed metal pads on the board, and then the components are placed on top of the paste. When heated, the solder particles melt and bond the components to the board.
Composition and Application
Solder paste consists of two main ingredients: solder alloy and flux. The solder alloy is typically a mixture of tin, lead, and sometimes silver, although lead-free alternatives are becoming increasingly common due to environmental and health concerns. The flux helps to remove oxides from the metal surfaces, promoting better wetting and bonding of the solder.
Solder paste is applied to the PCB using a stencil, which is a thin metal sheet with openings that correspond to the desired solder paste locations. The stencil is placed over the board, and the paste is spread across the surface using a squeegee or automated dispensing equipment.
Benefits of Solder Paste
- Precision: Solder paste allows for the accurate placement of small amounts of solder on specific areas of the PCB.
- Efficiency: Using solder paste streamlines the assembly process, as components can be placed directly onto the paste and soldered in a single reflow operation.
- Reliability: The flux in solder paste helps to create strong, reliable solder joints by removing oxides and promoting proper wetting.
- Versatility: Solder paste is suitable for a wide range of surface mount components, from tiny chip resistors to large ball grid array (BGA) packages.
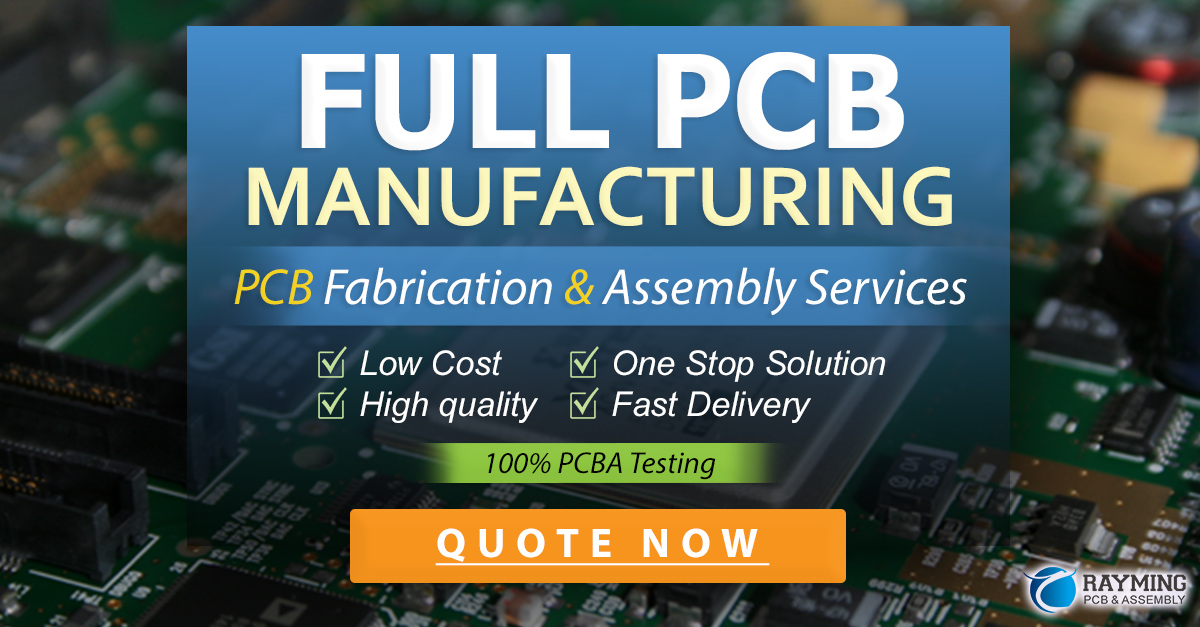
Key Differences Between Solder Mask and Solder Paste
Aspect | Solder Mask | Solder Paste |
---|---|---|
Purpose | Protects and insulates copper traces | Forms electrical and mechanical connections |
Composition | Polymer-based material with pigments | Solder alloy particles suspended in flux |
Application | Screen printing, liquid or dry film photoimaging | Stencil printing or automated dispensing |
Timing | Applied during RAYPCB/”>PCB fabrication | Applied during PCB Assembly |
Location | Covers most of the PCB surface, except pads and vias | Only applied to exposed metal pads |
Visibility | Visible on the finished PCB | Not visible after soldering |
Solder Mask vs Paste: Which One to Use?
It is important to note that solder mask and solder paste are not interchangeable; they serve different purposes and are used at different stages of the PCB manufacturing process. Solder mask is applied during the fabrication of the bare PCB, while solder paste is used during the assembly stage when components are attached to the board.
In most cases, a PCB will have both solder mask and solder paste. The solder mask is applied first to protect the copper traces and define the solderable areas. Then, during assembly, solder paste is applied to the exposed pads, and the components are placed and soldered onto the board.
FAQ
-
Can solder paste be applied directly to solder mask?
No, solder paste should only be applied to the exposed metal pads on the PCB. Solder mask is designed to prevent solder from adhering to covered areas. -
Is it possible to have a PCB without solder mask?
Yes, some PCBs may not have solder mask, especially in low-cost or prototype applications. However, the absence of solder mask increases the risk of short circuits, oxidation, and mechanical damage. -
Can solder paste be used for through-hole components?
While solder paste is primarily used for surface mount components, it can be used for through-hole components in some cases. This technique is called intrusive reflow, where the paste is applied to the holes, and the components are inserted before the reflow process. -
What happens if solder paste is applied too thickly?
Applying too much solder paste can lead to solder bridges, tombstoning (when a component stands up on one end), or other defects. It is essential to control the amount of solder paste applied using a properly designed stencil and appropriate printing parameters. -
How does solder mask affect the soldering process?
Solder mask plays a crucial role in the soldering process by defining the solderable areas and preventing solder from spreading to unintended locations. It helps to ensure that solder only bonds to the exposed metal pads and component leads, reducing the risk of short circuits and other defects.
Conclusion
Solder mask and solder paste are two essential materials in the world of electronics manufacturing, but they serve very different purposes. Solder mask is a protective coating that insulates and shields the copper traces on a PCB, while solder paste is a mixture of solder alloy and flux used to form electrical and mechanical connections between components and the board.
Understanding the difference between solder mask and solder paste is crucial for anyone involved in the design, fabrication, or assembly of electronic devices. By recognizing their distinct roles and properties, you can ensure that your PCBs are manufactured and assembled correctly, resulting in reliable and high-quality electronic products.
No responses yet