Understanding PCB Materials
What is a PCB?
A printed circuit board (PCB) is a fundamental component in electronic devices that provides mechanical support and electrical connectivity for electronic components. It consists of a non-conductive substrate, typically made of fiberglass or other composite materials, with conductive copper traces etched onto its surface. These copper traces form the electrical pathways that connect various components, such as resistors, capacitors, and integrated circuits, to create a functional electronic circuit.
Importance of PCB Material Selection
The choice of PCB material plays a crucial role in the performance, reliability, and cost of the final product. Different materials exhibit varying properties, such as dielectric constant, thermal conductivity, and mechanical strength, which can significantly impact the circuit’s behavior. Therefore, selecting the appropriate PCB material depends on factors such as the intended application, operating frequency, environmental conditions, and budget constraints.
Rogers PCB
What is Rogers Material?
Rogers is a brand name for a family of high-frequency laminate materials used in PCB fabrication. These materials are engineered to provide excellent electrical and mechanical properties, making them suitable for applications that require high-speed, low-loss signal transmission. Rogers materials are composed of a ceramic-filled PTFE (Polytetrafluoroethylene) composite, which offers a unique combination of low dielectric constant, low dissipation factor, and high thermal conductivity.
Advantages of Rogers PCB
-
Low Dielectric Constant: Rogers materials have a low dielectric constant, typically ranging from 2.2 to 3.5, depending on the specific grade. A low dielectric constant minimizes signal distortion and allows for faster signal propagation, making Rogers PCBs ideal for high-frequency applications.
-
Low Loss Tangent: The loss tangent, or dissipation factor, of Rogers materials is extremely low, often below 0.002. This property ensures minimal signal loss and attenuation, enabling efficient power transmission and reducing heat generation.
-
High Thermal Conductivity: Rogers materials exhibit excellent thermal conductivity, efficiently dissipating heat generated by electronic components. This characteristic helps maintain a stable operating temperature and prevents thermal stress on the PCB and its components.
-
Dimensional Stability: Rogers materials have a low coefficient of thermal expansion (CTE), ensuring minimal dimensional changes under varying temperature conditions. This stability is crucial for maintaining the integrity of the circuit and preventing mechanical stress on components.
-
High-Frequency Performance: The combination of low dielectric constant, low loss tangent, and high thermal conductivity makes Rogers PCBs excel in high-frequency applications, such as RF and microwave circuits, radar systems, and wireless communication devices.
Applications of Rogers PCB
Rogers PCBs find extensive use in various high-frequency and high-performance applications, including:
-
Wireless Communication: Rogers materials are widely used in the manufacturing of PCBs for wireless communication devices, such as cellular phones, Wi-Fi routers, and Bluetooth modules.
-
Aerospace and Defense: The reliability and performance of Rogers PCBs make them suitable for aerospace and defense applications, including radar systems, satellite communication, and avionics.
-
Automotive Electronics: Rogers materials are employed in automotive electronic systems, such as advanced driver assistance systems (ADAS), radar sensors, and vehicle-to-vehicle communication.
-
Medical Equipment: The low-loss properties of Rogers PCBs are beneficial in medical equipment, such as MRI machines, ultrasound devices, and medical implants.
-
Industrial Automation: Rogers materials are used in industrial automation systems that require high-speed data transmission and reliable performance in harsh environments.
FR4 PCB
What is FR4 material?
FR4 (Flame Retardant 4) is a widely used PCB material that consists of a woven fiberglass cloth impregnated with an epoxy resin. It is a cost-effective and versatile material that offers good mechanical and electrical properties. FR4 has become the standard material for most general-purpose PCBs due to its balanced characteristics and wide availability.
Advantages of FR4 PCB
-
Cost-Effectiveness: FR4 is relatively inexpensive compared to other PCB materials, making it an economical choice for many applications. Its widespread availability and manufacturing processes contribute to its cost-effectiveness.
-
Mechanical Strength: FR4 offers excellent mechanical strength and durability. The fiberglass reinforcement provides rigidity and resistance to bending and twisting, making FR4 PCBs suitable for applications that require structural integrity.
-
Flame Retardancy: As the name suggests, FR4 is a flame-retardant material. It has good fire resistance properties, reducing the risk of ignition and the spread of flames in case of a short circuit or overheating.
-
Electrical Insulation: FR4 provides good electrical insulation, preventing current leakage between conductive traces. Its dielectric constant is relatively stable over a wide range of frequencies, making it suitable for many general-purpose applications.
-
Wide Temperature Range: FR4 can operate in a temperature range of -50°C to +130°C, making it suitable for most industrial and consumer applications. It maintains its mechanical and electrical properties within this temperature range.
Applications of FR4 PCB
FR4 PCBs find applications in a wide range of industries and products, including:
-
Consumer Electronics: FR4 is commonly used in the manufacturing of PCBs for consumer electronic devices, such as smartphones, laptops, televisions, and home appliances.
-
Industrial Control Systems: FR4 PCBs are employed in industrial control systems, such as programmable logic controllers (PLCs), human-machine interfaces (HMIs), and process control equipment.
-
Automotive Electronics: FR4 is used in the production of PCBs for various automotive electronic systems, including engine control units (ECUs), infotainment systems, and power distribution modules.
-
Medical Devices: FR4 PCBs are found in medical devices, such as patient monitors, diagnostic equipment, and imaging systems.
-
Telecommunications: FR4 is used in the fabrication of PCBs for telecommunications equipment, such as switches, routers, and network interface cards (NICs).
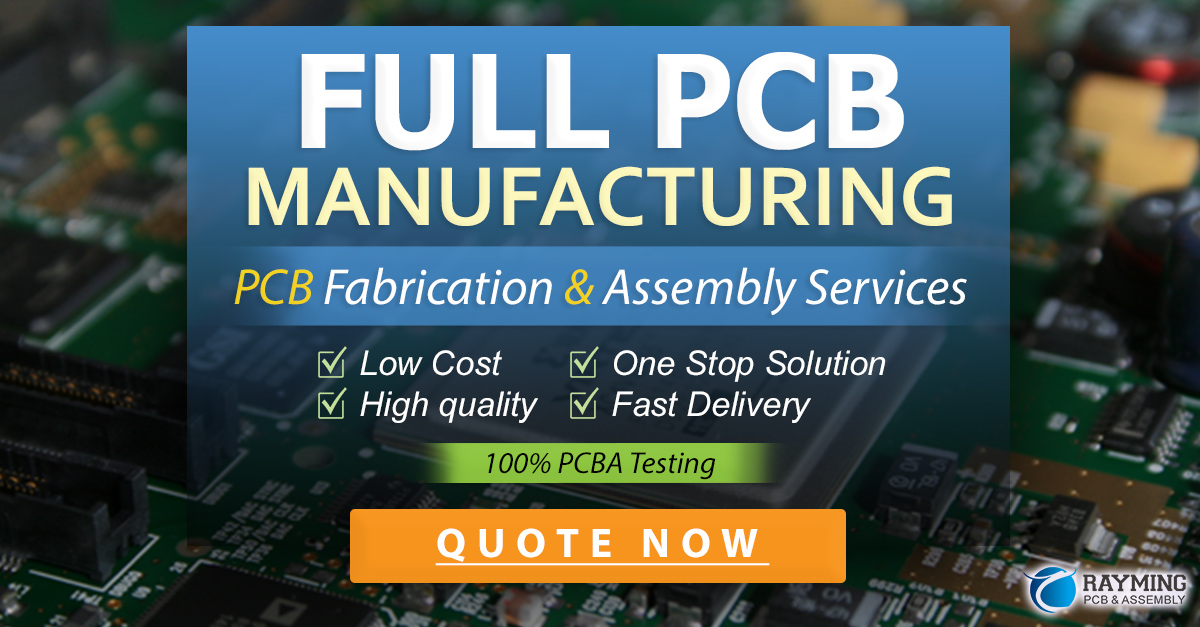
Comparison of Rogers vs FR4
Dielectric Constant
Material | Dielectric Constant |
---|---|
Rogers | 2.2 – 3.5 |
FR4 | 4.2 – 4.8 |
Rogers materials have a lower dielectric constant compared to FR4. A lower dielectric constant results in faster signal propagation and reduced signal distortion, making Rogers PCBs more suitable for high-frequency applications.
Loss Tangent
Material | Loss Tangent |
---|---|
Rogers | < 0.002 |
FR4 | 0.02 – 0.03 |
Rogers materials exhibit a significantly lower loss tangent compared to FR4. A lower loss tangent translates to minimal signal loss and attenuation, ensuring efficient power transmission and reduced heat generation. This property makes Rogers PCBs ideal for applications that require low-loss signal transmission.
Thermal Conductivity
Material | Thermal Conductivity (W/mK) |
---|---|
Rogers | 0.6 – 1.0 |
FR4 | 0.3 – 0.4 |
Rogers materials have higher thermal conductivity compared to FR4. Higher thermal conductivity allows for better heat dissipation, preventing thermal stress on the PCB and its components. This characteristic is particularly important in high-power and high-density applications.
Cost Comparison
Material | Relative Cost |
---|---|
Rogers | High |
FR4 | Low |
Rogers materials are generally more expensive than FR4 due to their specialized composition and superior performance characteristics. The cost of Rogers PCBs can be several times higher than FR4 PCBs, depending on the specific grade and thickness of the material.
Application Suitability
Material | Suitable Applications |
---|---|
Rogers | High-frequency, low-loss, and high-performance applications |
FR4 | General-purpose, cost-sensitive, and moderate-performance applications |
Rogers PCBs are primarily used in applications that demand high-frequency operation, low signal loss, and excellent thermal management. These include wireless communication devices, aerospace and defense systems, and automotive electronics.
FR4 PCBs, on the other hand, are widely used in general-purpose applications where cost-effectiveness and moderate performance are the main considerations. These include consumer electronics, industrial control systems, and telecommunications equipment.
Frequently Asked Questions (FAQ)
-
Q: Can FR4 be used for high-frequency applications?
A: While FR4 can be used in some high-frequency applications, it may not provide the same level of performance as Rogers materials. FR4 has a higher dielectric constant and loss tangent, which can lead to signal distortion and loss at higher frequencies. For demanding high-frequency applications, Rogers materials are generally preferred. -
Q: Are Rogers PCBs more expensive than FR4 PCBs?
A: Yes, Rogers PCBs are typically more expensive than FR4 PCBs due to the specialized composition and superior performance characteristics of Rogers materials. The cost difference can be significant, depending on the specific grade and thickness of the material. However, the higher cost is often justified for applications that require the unique properties offered by Rogers materials. -
Q: Can Rogers materials be used for multilayer PCBs?
A: Yes, Rogers materials can be used for multilayer PCB construction. In fact, multilayer Rogers PCBs are commonly used in complex high-frequency designs to achieve optimal signal integrity and power distribution. The low dielectric constant and low loss tangent of Rogers materials make them suitable for multilayer structures, minimizing signal interference and crosstalk between layers. -
Q: What are the limitations of FR4 PCBs?
A: FR4 PCBs have certain limitations, particularly in high-frequency and high-speed applications. The higher dielectric constant and loss tangent of FR4 can result in signal distortion, attenuation, and increased power consumption. Additionally, FR4 has lower thermal conductivity compared to Rogers materials, which can lead to thermal management challenges in high-power applications. -
Q: How do I choose between Rogers and FR4 for my PCB design?
A: The choice between Rogers and FR4 depends on several factors, including the intended application, operating frequency, required performance, and budget constraints. If your design involves high-frequency signals, low-loss requirements, and demanding thermal management, Rogers materials may be the better choice. However, if your application has moderate performance requirements and cost is a primary concern, FR4 can be a suitable option. It’s recommended to consult with PCB design experts and material suppliers to make an informed decision based on your specific needs.
Conclusion
Rogers and FR4 are two distinct PCB materials that cater to different application requirements. Rogers materials, with their low dielectric constant, low loss tangent, and high thermal conductivity, excel in high-frequency and high-performance applications. They are the preferred choice for wireless communication devices, aerospace and defense systems, and automotive electronics.
On the other hand, FR4 is a cost-effective and versatile material that finds widespread use in general-purpose applications. Its balanced mechanical and electrical properties make it suitable for consumer electronics, industrial control systems, and telecommunications equipment.
When selecting between Rogers and FR4, it is essential to consider factors such as the intended application, operating frequency, required performance, and budget constraints. By understanding the unique characteristics and advantages of each material, designers can make informed decisions and optimize their PCB designs for specific requirements.
As technology advances and new applications emerge, the choice between Rogers and FR4 will continue to be a critical consideration in PCB design and manufacturing. By leveraging the strengths of each material and staying informed about the latest advancements, engineers and designers can create innovative and reliable electronic products that meet the ever-evolving demands of the industry.
No responses yet