Introduction to High TG FR4 and Polyimide
High TG FR4 and polyimide are two popular materials used in the manufacturing of printed circuit boards (PCBs). Both materials offer unique properties that make them suitable for various applications. In this article, we will explore the differences between high TG FR4 and polyimide, their characteristics, applications, and factors to consider when choosing between the two.
What is High TG FR4?
High TG FR4 is a type of flame-retardant (FR) glass-reinforced epoxy laminate. The term “high TG” refers to the high glass transition temperature of the material, which is typically above 170°C. FR4 is a popular choice for PCBs due to its excellent mechanical and electrical properties, as well as its cost-effectiveness.
What is Polyimide?
Polyimide is a high-performance polymer material known for its exceptional thermal stability, mechanical strength, and chemical resistance. It is often used in applications that require high reliability and the ability to withstand extreme conditions, such as aerospace, automotive, and medical industries.
Properties of High TG FR4 and Polyimide
To understand the differences between high TG FR4 and polyimide, it is essential to examine their properties in detail.
Thermal Properties
One of the most significant differences between high TG FR4 and polyimide is their thermal properties. The table below compares the thermal properties of the two materials:
Property | High TG FR4 | Polyimide |
---|---|---|
Glass Transition Temperature (Tg) | 170-180°C | 260-400°C |
Continuous Operating Temperature | 130-140°C | 240-260°C |
Thermal Conductivity | 0.3-0.4 W/mK | 0.2-0.3 W/mK |
Coefficient of Thermal Expansion (CTE) | 12-16 ppm/°C | 20-60 ppm/°C |
As seen in the table, polyimide has a significantly higher glass transition temperature and continuous operating temperature compared to high TG FR4. This makes polyimide suitable for applications that require exposure to high temperatures for extended periods.
Mechanical Properties
Both high TG FR4 and polyimide exhibit excellent mechanical properties, making them suitable for various applications. The table below compares the mechanical properties of the two materials:
Property | High TG FR4 | Polyimide |
---|---|---|
Tensile Strength | 310-380 MPa | 140-230 MPa |
Flexural Strength | 415-550 MPa | 140-210 MPa |
Compressive Strength | 415-550 MPa | 190-260 MPa |
Young’s Modulus | 18-24 GPa | 2.5-4.5 GPa |
High TG FR4 has higher tensile, flexural, and compressive strength compared to polyimide. However, polyimide has a lower Young’s modulus, which indicates that it is more flexible than high TG FR4.
Electrical Properties
Electrical properties are crucial when selecting materials for PCBs. The table below compares the electrical properties of high TG FR4 and polyimide:
Property | High TG FR4 | Polyimide |
---|---|---|
Dielectric Constant @ 1 MHz | 4.5-4.9 | 3.4-3.8 |
Dissipation Factor @ 1 MHz | 0.02-0.03 | 0.002-0.008 |
Volume Resistivity | 10^8-10^10 Ω·cm | 10^16-10^18 Ω·cm |
Surface Resistivity | 10^5-10^7 Ω | 10^16-10^18 Ω |
Polyimide has a lower dielectric constant and dissipation factor compared to high TG FR4, which makes it suitable for high-frequency applications. Additionally, polyimide has higher volume and surface resistivity, indicating better insulation properties.
Chemical Resistance
Chemical resistance is another important factor to consider when choosing between high TG FR4 and polyimide. Both materials exhibit good chemical resistance, but polyimide is known for its exceptional resistance to a wide range of chemicals, including acids, bases, and organic solvents.
Applications of High TG FR4 and Polyimide
High TG FR4 Applications
High TG FR4 is widely used in various industries, including:
- Telecommunications
- Automotive electronics
- Industrial control systems
- Consumer electronics
- Medical devices
Its excellent mechanical and electrical properties, combined with its cost-effectiveness, make high TG FR4 a popular choice for many PCB applications.
Polyimide Applications
Polyimide is often used in applications that require high reliability and the ability to withstand extreme conditions. Some common applications include:
- Aerospace electronics
- Automotive electronics (e.g., under-the-hood components)
- High-temperature industrial systems
- Medical devices (e.g., implantable devices)
- Flexible electronics
Polyimide’s unique properties, such as high thermal stability, chemical resistance, and flexibility, make it an ideal choice for these demanding applications.
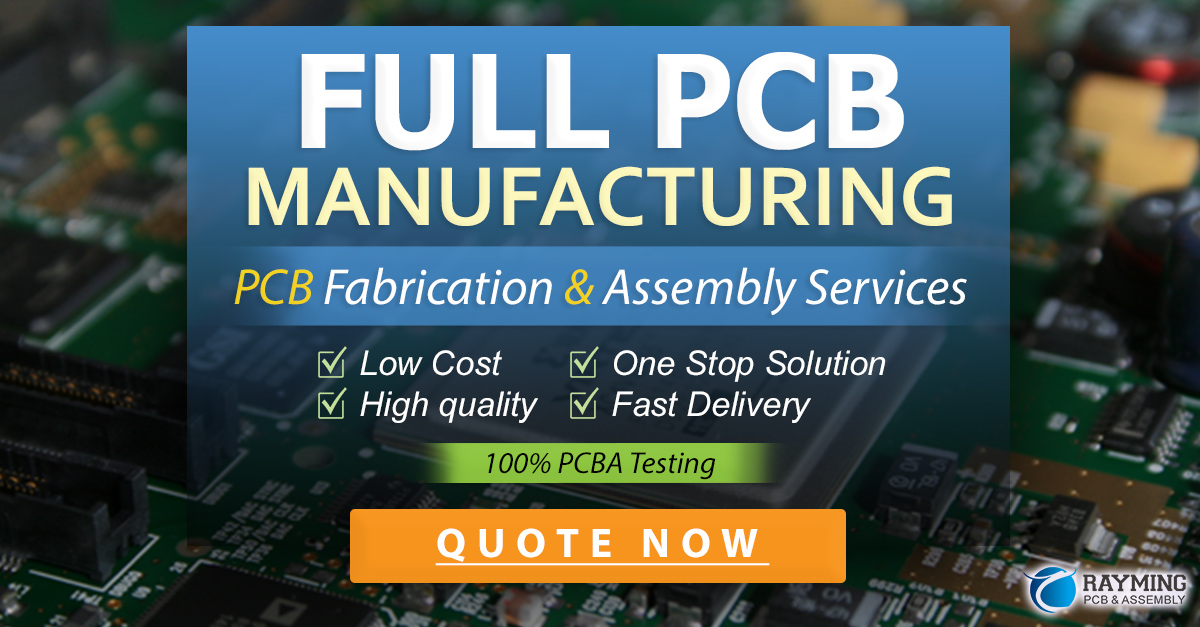
Factors to Consider When Choosing Between High TG FR4 and Polyimide
When deciding between high TG FR4 and polyimide for your PCB application, consider the following factors:
-
Operating temperature: If your application requires exposure to high temperatures for extended periods, polyimide may be the better choice due to its higher glass transition temperature and continuous operating temperature.
-
Mechanical requirements: High TG FR4 offers higher tensile, flexural, and compressive strength, while polyimide is more flexible. Choose the material that best suits your application’s mechanical requirements.
-
Electrical requirements: For high-frequency applications, polyimide’s lower dielectric constant and dissipation factor may make it a more suitable choice.
-
Chemical exposure: If your application involves exposure to harsh chemicals, polyimide’s exceptional chemical resistance may be advantageous.
-
Cost: High TG FR4 is generally more cost-effective than polyimide. Consider your budget and the overall cost implications when making your decision.
FAQ
1. Can high TG FR4 be used in high-temperature applications?
While high TG FR4 has a higher glass transition temperature compared to standard FR4, it may not be suitable for applications that require continuous exposure to temperatures above 140°C. In such cases, polyimide may be a better choice.
2. Is polyimide more expensive than high TG FR4?
Yes, polyimide is generally more expensive than high TG FR4 due to its high-performance properties and the more complex manufacturing process.
3. Can polyimide be used in flexible PCBs?
Yes, polyimide is an excellent choice for flexible PCBs due to its high flexibility and ability to withstand repeated bending without damage.
4. Is high TG FR4 suitable for high-frequency applications?
While high TG FR4 can be used in high-frequency applications, polyimide may be a better choice due to its lower dielectric constant and dissipation factor.
5. Can high TG FR4 and polyimide be used together in a PCB stackup?
Yes, it is possible to use both high TG FR4 and polyimide in a PCB stackup, depending on the specific requirements of the application. This can help balance the advantages of both materials while optimizing cost and performance.
Conclusion
In summary, high TG FR4 and polyimide are two popular materials used in the manufacturing of PCBs, each with its own unique properties and advantages. High TG FR4 offers excellent mechanical and electrical properties at a lower cost, making it suitable for a wide range of applications. Polyimide, on the other hand, excels in high-temperature environments, has exceptional chemical resistance, and is more flexible, making it ideal for demanding applications in aerospace, automotive, and medical industries.
When choosing between high TG FR4 and polyimide, consider factors such as operating temperature, mechanical and electrical requirements, chemical exposure, and cost. By understanding the differences between these two materials and their respective strengths, you can make an informed decision that best suits your PCB application’s needs.
No responses yet