Introduction to FR4 PCB and Mcpcb
Printed Circuit Boards (PCBs) are essential components in modern electronic devices. They provide a platform for mounting and interconnecting electronic components, ensuring reliable and efficient operation. Two common types of PCBs are FR4 PCB and Mcpcb (Metal Core PCB). While both serve similar purposes, they have distinct characteristics and are suited for different applications.
What is FR4 PCB?
FR4 PCB, also known as Flame Retardant 4 PCB, is the most widely used type of PCB substrate material. It is a composite material made of woven fiberglass cloth impregnated with an epoxy resin binder. The “FR” stands for Flame Retardant, indicating its inherent flame-resistant properties. FR4 PCBs offer excellent electrical insulation, mechanical strength, and thermal stability.
What is Mcpcb?
Mcpcb, or Metal Core PCB, is a specialized type of PCB that features a metal substrate, typically aluminum or copper, as its base material. The metal core provides excellent thermal conductivity, allowing for efficient heat dissipation from the mounted electronic components. Mcpcbs are commonly used in applications that generate significant heat, such as high-power LEDs, power electronics, and automotive systems.
Key Differences between FR4 PCB and Mcpcb
Substrate Material
- FR4 PCB: FR4 PCBs use a composite material made of woven fiberglass cloth and epoxy resin as the substrate. This combination offers good electrical insulation and mechanical stability.
- Mcpcb: Mcpcbs utilize a metal substrate, usually aluminum or copper, as the base material. The metal core provides excellent thermal conductivity for heat dissipation.
Thermal Management
- FR4 PCB: FR4 PCBs have limited thermal conductivity due to the insulating nature of the fiberglass and epoxy resin. They rely on additional heat dissipation methods, such as heatsinks or thermal vias, to manage heat generated by components.
- Mcpcb: The metal core in Mcpcbs acts as a built-in heatsink, efficiently spreading and dissipating heat away from the electronic components. This superior thermal management allows for better performance and reliability in heat-sensitive applications.
Electrical Insulation
- FR4 PCB: FR4 PCBs provide excellent electrical insulation due to the dielectric properties of the fiberglass and epoxy resin. This insulation prevents short circuits and ensures proper signal integrity.
- Mcpcb: Mcpcbs require an additional dielectric layer between the metal core and the copper traces to provide electrical insulation. This dielectric layer is typically made of a thin, thermally conductive material to maintain the thermal benefits of the metal core.
Applications
- FR4 PCB: FR4 PCBs are versatile and widely used in a variety of electronic devices, including consumer electronics, telecommunications equipment, industrial controls, and more. They are suitable for general-purpose applications where thermal management is not a critical concern.
- Mcpcb: Mcpcbs are primarily used in applications that generate significant heat and require efficient thermal management. Examples include high-power LED lighting, automotive electronics, power converters, and motor drives. Mcpcbs are also used in applications where space is limited, and a compact design with integrated heat dissipation is desired.
Cost
- FR4 PCB: FR4 PCBs are generally more cost-effective compared to Mcpcbs. The materials and manufacturing processes for FR4 PCBs are well-established and widely available, resulting in lower production costs.
- Mcpcb: Mcpcbs tend to be more expensive than FR4 PCBs due to the specialized materials and manufacturing processes involved. The metal core and additional dielectric layer add to the overall cost of production.
Parameter | FR4 PCB | Mcpcb |
---|---|---|
Substrate Material | Fiberglass and epoxy resin | Metal core (aluminum or copper) |
Thermal Management | Limited, relies on additional methods | Excellent, built-in heatsink |
Electrical Insulation | Excellent | Requires additional dielectric layer |
Applications | General-purpose electronics | Heat-sensitive and space-constrained applications |
Cost | More cost-effective | Higher cost due to specialized materials and processes |
Choosing between FR4 PCB and Mcpcb
When deciding between FR4 PCB and Mcpcb for a specific application, consider the following factors:
-
Thermal Requirements: If your application generates significant heat or requires efficient heat dissipation, Mcpcb is the preferred choice. The metal core in Mcpcbs provides superior thermal management compared to FR4 PCBs.
-
Electrical Insulation: FR4 PCBs offer excellent electrical insulation by default, whereas Mcpcbs require an additional dielectric layer. If your application demands high electrical insulation, FR4 PCBs may be more suitable.
-
Cost Considerations: FR4 PCBs are generally more cost-effective than Mcpcbs. If your application does not have stringent thermal requirements, using FR4 PCBs can help reduce overall costs.
-
Space Constraints: Mcpcbs can offer a more compact design solution by integrating the heatsink functionality into the PCB itself. If space is limited and efficient heat dissipation is crucial, Mcpcbs can be a viable option.
-
Manufacturing Capabilities: Consider the availability of manufacturing capabilities for FR4 PCBs and Mcpcbs. FR4 PCBs are more widely manufactured, while Mcpcbs may require specialized facilities and processes.
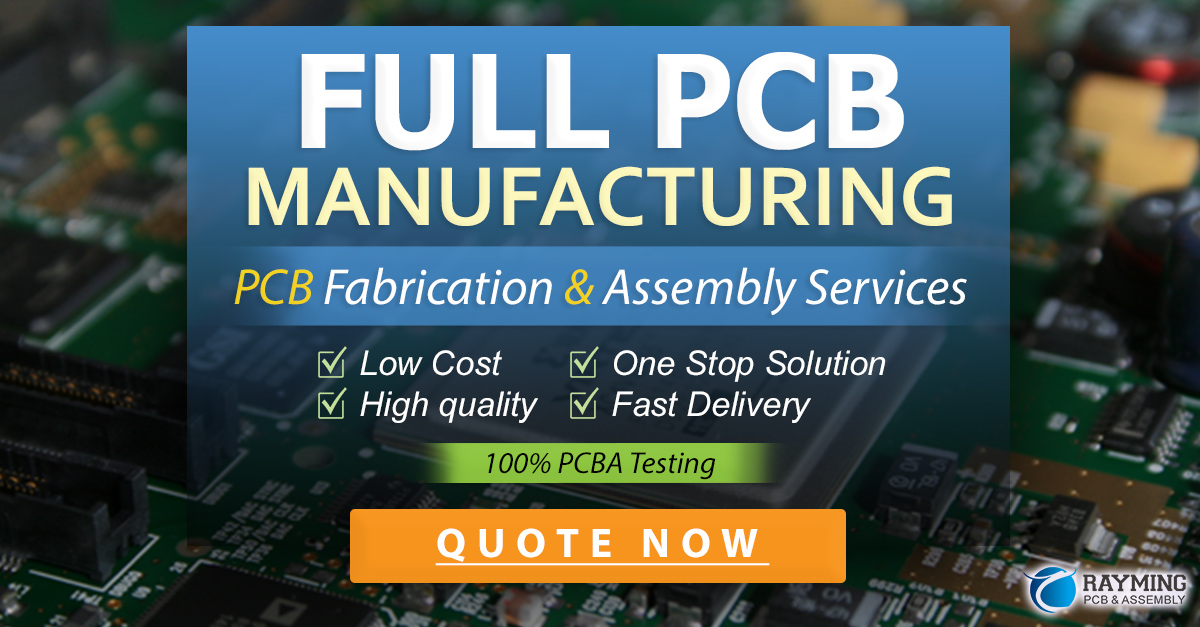
FAQ
-
Q: Can FR4 PCBs be used in high-temperature applications?
A: FR4 PCBs have a glass transition temperature (Tg) of around 130°C to 140°C. They can operate in temperatures up to their Tg, but prolonged exposure to high temperatures may degrade their performance and reliability. For high-temperature applications, Mcpcbs or other specialized PCB materials may be more suitable. -
Q: Are Mcpcbs suitable for high-frequency applications?
A: Mcpcbs can be used in high-frequency applications, but their performance may be affected by the metal core. The metal substrate can introduce capacitance and impact signal integrity at high frequencies. Proper design considerations, such as the use of a low-loss dielectric layer and controlled impedance traces, can help mitigate these effects. -
Q: Can Mcpcbs be used with surface-mount components?
A: Yes, Mcpcbs are compatible with surface-mount components. The copper traces on the Mcpcb provide a suitable surface for soldering and mounting surface-mount devices (SMDs). However, the thermal characteristics of the Mcpcb should be considered when selecting and placing components to ensure proper heat dissipation. -
Q: How does the thickness of the dielectric layer affect the thermal performance of Mcpcbs?
A: The thickness of the dielectric layer in Mcpcbs influences the thermal performance. A thinner dielectric layer allows for better heat transfer from the components to the metal core. However, a thinner layer also reduces the electrical insulation and may increase the risk of dielectric breakdown. The optimal dielectric layer thickness depends on the specific application requirements and the selected materials. -
Q: Can FR4 PCBs and Mcpcbs be combined in a single design?
A: Yes, it is possible to combine FR4 PCBs and Mcpcbs in a single design using a hybrid approach. This can be achieved by selectively using Mcpcbs for the heat-generating components while using FR4 PCBs for the rest of the circuitry. The hybrid design allows for optimal thermal management in specific areas while maintaining the cost-effectiveness of FR4 PCBs in other parts of the design.
Conclusion
Understanding the differences between FR4 PCBs and Mcpcbs is crucial when designing electronic devices. FR4 PCBs offer excellent electrical insulation, mechanical stability, and cost-effectiveness, making them suitable for a wide range of general-purpose applications. On the other hand, Mcpcbs excel in thermal management, making them ideal for heat-sensitive applications and designs with limited space.
When choosing between FR4 PCB and Mcpcb, consider factors such as thermal requirements, electrical insulation needs, cost constraints, space limitations, and manufacturing capabilities. By selecting the appropriate PCB type for your specific application, you can ensure optimal performance, reliability, and cost-effectiveness in your electronic designs.
As technology advances and new materials emerge, the PCB industry continues to evolve, offering designers and engineers a broader range of options to meet their unique requirements. Whether you choose FR4 PCB, Mcpcb, or a hybrid approach, understanding the strengths and limitations of each PCB type will help you make informed decisions and create successful electronic products.
No responses yet