What is FR4?
FR4 (Flame Retardant 4) is a composite material composed of woven fiberglass cloth with an epoxy resin binder. It is the most widely used insulating substrate material for PCBs due to its excellent mechanical, electrical, and thermal properties. Key characteristics of FR4 include:
- High strength and stiffness
- Good electrical insulation
- Flame retardant
- Resistant to moisture absorption
- Suitable for multi-layer PCBs
- Cost-effective
FR4 is available in various grades and thicknesses to suit different applications. The grade is determined by the glass transition temperature (Tg) – the temperature at which the material transitions from a rigid, glassy state to a softer state. Standard FR4 has a Tg around 130°C while high Tg FR4 is rated for 170°C.
Advantages of FR4
- Versatile and widely available
- Excellent mechanical strength
- Good electrical insulator
- Flame retardant for safety
- Suitable for complex, multi-layer designs
- Lower cost than specialty materials
Disadvantages of FR4
- Higher loss tangent than some other materials, which can limit high frequency performance
- Moisture absorption can degrade performance in high humidity
- Thermal expansion mismatch with copper can cause reliability issues with many thermal cycles
- Requires careful process control in fabrication and assembly
What is Polyamide?
Polyamide, also known as nylon, is a thermoplastic polymer material sometimes used as an Alternative to FR4 in PCBs. It offers some unique properties that can be advantageous in certain applications. Characteristics of polyamide include:
- Lightweight and flexible
- Excellent mechanical toughness
- Good chemical resistance
- Low moisture absorption
- Stable dielectric properties
- Suitable for high frequency applications
Polyamide is available in pure polymer form as well as glass-reinforced grades for improved mechanical properties. It can be used to make thin, flexible circuit boards as well as molded 3D circuits.
Advantages of Polyamide
- Lightweight for portable/wearable devices
- Flexible for curved surfaces and dynamic applications
- Tougher and more impact resistant than FR4
- Very low moisture absorption maintains stable performance
- Good high frequency/microwave dielectric properties
- Resistant to many solvents and chemicals
Disadvantages of Polyamide
- More expensive than FR4
- Lower strength and stiffness than glass-reinforced materials
- Requires specialized processing equipment and techniques
- Limited availability and longer lead times
- Less suitable for complex multi-layer boards
FR4 vs Polyamide Comparison
Now that we’ve looked at each material individually, let’s make a direct comparison of FR4 vs polyamide in several key properties:
Property | FR4 | Polyamide |
---|---|---|
Density | 1.85 g/cm³ | 1.14 g/cm³ |
Dielectric Constant @ 1 MHz | 4.5 | 3.5 |
Dissipation Factor @ 1 MHz | 0.02 | 0.003 |
Moisture Absorption | 0.15% | 0.04% |
Tensile Strength | 415 MPa | 85 MPa |
Flexural Strength | 485 MPa | 115 MPa |
Glass Transition Temperature | 130-170°C | 50°C |
Flammability Rating | V-0 | HB |
Typical Applications | High density interconnect, multi-layer boards, general purpose | RF/microwave circuits, flexible circuits, portable devices |
As you can see, polyamide has the advantages of lower weight, lower loss tangent, and less moisture absorption, while FR4 offers superior strength, stiffness, and thermal stability. The choice between the two depends on the specific requirements and constraints of your application.
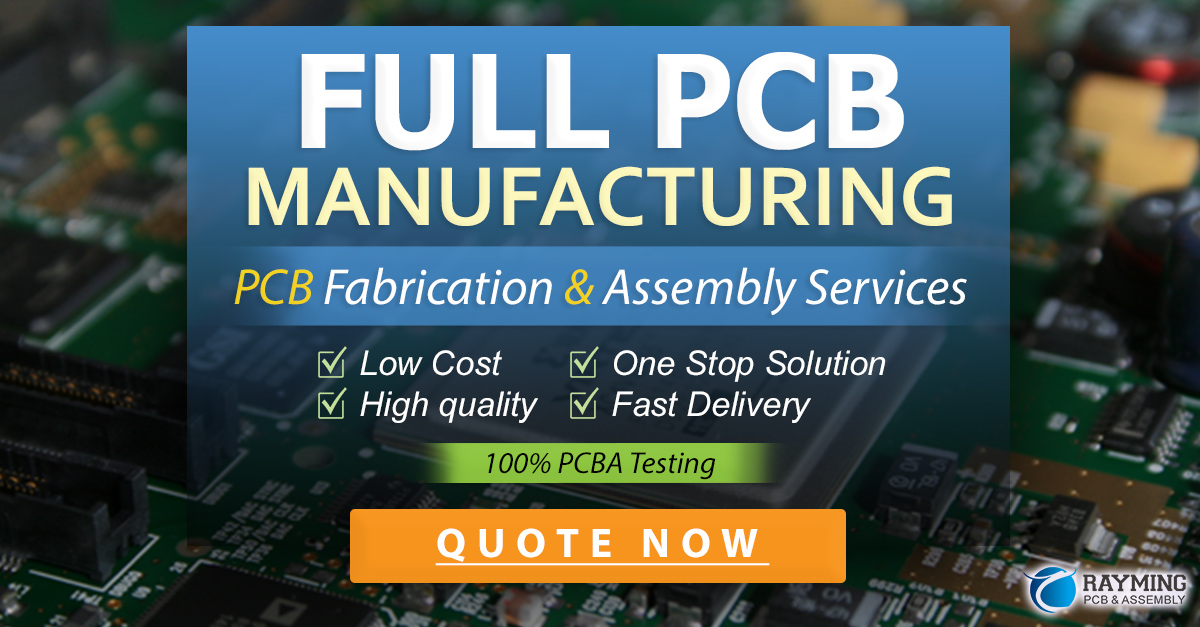
Typical Applications
FR4 PCBs
FR4 is the go-to material for the vast majority of printed circuit board applications across consumer, commercial, and industrial markets. Typical uses include:
- Computer motherboards and expansion cards
- Telecommunications equipment
- Automotive electronics
- Industrial control systems
- Medical devices
- Aerospace and defense systems
The versatility, reliability, and cost-effectiveness of FR4 make it suitable for a wide range of general purpose and high-density PCB designs. High Tg FR4 is often used in more demanding applications with greater thermal stress, such as automotive and aerospace systems.
Polyamide PCBs
Polyamide is a more specialized material that excels in applications which take advantage of its unique properties. Common uses include:
- High frequency RF and microwave circuits
- Flexible and rigid-flex PCBs
- Wearable electronics
- Portable devices and antennas
- Molded interconnect devices (3D circuits)
- High speed digital circuits
The light weight, flexibility, and low loss of polyamide make it an attractive choice for designs that require these attributes. However, the higher cost and limited availability compared to FR4 mean that polyamide is usually reserved for applications that specifically benefit from its properties.
Manufacturing Considerations
The choice between FR4 and polyamide also has implications for PCB manufacturing. Here are some key considerations:
FR4 Fabrication
- Well-established processes and supply chain
- Can be fabricated by most PCB shops
- Multi-layer designs up to 40+ layers
- Requires careful process control for high yield
- Compatible with standard lead-free assembly
Polyamide Fabrication
- Requires specialized equipment and processes
- Limited number of qualified suppliers
- Typically limited to 4 layers or less
- Multilayer bonding can be challenging
- May require specialized assembly techniques
In general, FR4 is easier and more cost-effective to work with for PCB fabrication and assembly. The well-established FR4 ecosystem and knowledge base make it a lower-risk choice for most designs. Polyamide requires more specialized capabilities which may lead to higher costs and longer lead times.
Frequently Asked Questions
What is the main difference between FR4 and polyamide?
FR4 is a composite material made of woven fiberglass and epoxy resin, while polyamide is a thermoplastic polymer. FR4 offers superior mechanical and thermal properties, while polyamide provides benefits in weight, flexibility, and high frequency performance.
Can FR4 be used for flexible PCBs?
Standard rigid FR4 is not suitable for flexible circuits. However, there are variations like FR4 High Pressure Laminate (HPL) that can be used to create thin, somewhat flexible PCBs. For truly flexible circuits, polyamide or other polymer materials are preferred.
Is polyamide more expensive than FR4?
Yes, polyamide is typically more expensive than FR4 on a per-unit-area basis. The higher cost is due to the specialized raw materials, processing, and more limited supply chain compared to FR4. However, for applications that require the unique properties of polyamide, the added cost may be justified.
Can I use FR4 for high frequency circuits?
FR4 can be used for high frequency applications up to a point, but it has limitations. The relatively high dielectric loss tangent of FR4 can lead to signal loss and degradation at microwave frequencies. For the most demanding high frequency designs, lower loss materials like polyamide are often preferred.
Are there any safety concerns with polyamide?
Polyamide PCBs are generally safe to use, but there are a few considerations. Polyamide is flammable, so it may not be suitable for applications with strict flame retardancy requirements. Also, some individuals may have skin sensitization to certain polyamide compounds. Always refer to the material safety data sheet and follow good hygiene practices when handling.
Conclusion
In summary, FR4 and polyamide are two distinct materials used in PCB substrates, each with its own set of benefits and drawbacks. FR4 is the most common choice, offering a good balance of mechanical, thermal, and electrical properties at a reasonable cost. Polyamide excels in specialized applications that require light weight, flexibility, chemical resistance, and low loss at high frequencies.
When choosing between FR4 and polyamide, carefully consider the specific requirements of your application as well as the implications for manufacturing and assembly. In most cases, FR4 will be the preferred choice due to its versatility and extensive ecosystem. However, polyamide can be a valuable option for designs that play to its unique strengths.
As with any engineering decision, the choice between FR4 and polyamide involves trade-offs. By understanding the properties, advantages, and disadvantages of each material, you can make an informed selection that balances performance, reliability, manufacturability, and cost for your specific application.
No responses yet