Introduction to FR4 and FR5 Materials
FR4 and FR5 are two popular materials used in the manufacturing of printed circuit boards (PCBs). These materials are essential for creating reliable and durable electronic components that can withstand various environmental conditions. In this article, we will explore the differences between FR4 and FR5 materials, their properties, applications, and the factors to consider when choosing between them.
What is FR4 Material?
FR4 (Flame Retardant 4) is a type of glass-reinforced epoxy laminate material commonly used in the production of PCBs. It is made by combining woven fiberglass cloth with an epoxy resin binder under high pressure and temperature. The resulting material is strong, rigid, and has excellent electrical insulation properties.
Properties of FR4 Material
Property | Value |
---|---|
Dielectric Constant | 4.5 @ 1 MHz |
Dissipation Factor | 0.02 @ 1 MHz |
Moisture Absorption | 0.125% |
Thermal Conductivity | 0.25 W/m·K |
Tensile Strength | 415 MPa |
Flexural Strength | 620 MPa |
Glass Transition Temperature | 135°C |
FR4 exhibits several advantageous properties that make it a popular choice for PCB manufacturing:
- High mechanical strength and rigidity
- Excellent electrical insulation
- Good thermal stability
- Flame retardant properties
- Relatively low cost
Applications of FR4 Material
FR4 is widely used in various industries for the production of PCBs, including:
- Consumer electronics (smartphones, laptops, tablets)
- Automotive electronics
- Industrial control systems
- Medical devices
- Telecommunications equipment
What is FR5 Material?
FR5 (Flame Retardant 5) is another glass-reinforced epoxy laminate material used in PCB manufacturing. It is similar to FR4 but has a higher glass transition temperature (Tg) and better thermal performance. FR5 is made by combining woven fiberglass cloth with a high-temperature epoxy resin binder under high pressure and temperature.
Properties of FR5 Material
Property | Value |
---|---|
Dielectric Constant | 4.5 @ 1 MHz |
Dissipation Factor | 0.02 @ 1 MHz |
Moisture Absorption | 0.125% |
Thermal Conductivity | 0.25 W/m·K |
Tensile Strength | 415 MPa |
Flexural Strength | 620 MPa |
Glass Transition Temperature | 170°C |
FR5 shares many properties with FR4 but has some key advantages:
- Higher glass transition temperature (Tg)
- Better thermal stability and performance
- Improved resistance to thermal cycling
- Enhanced durability in harsh environments
Applications of FR5 Material
FR5 is commonly used in applications that require higher thermal stability and reliability, such as:
- Aerospace and defense electronics
- High-temperature industrial applications
- Automotive electronics (under-the-hood components)
- Power electronics and LED lighting
- Oil and gas industry equipment
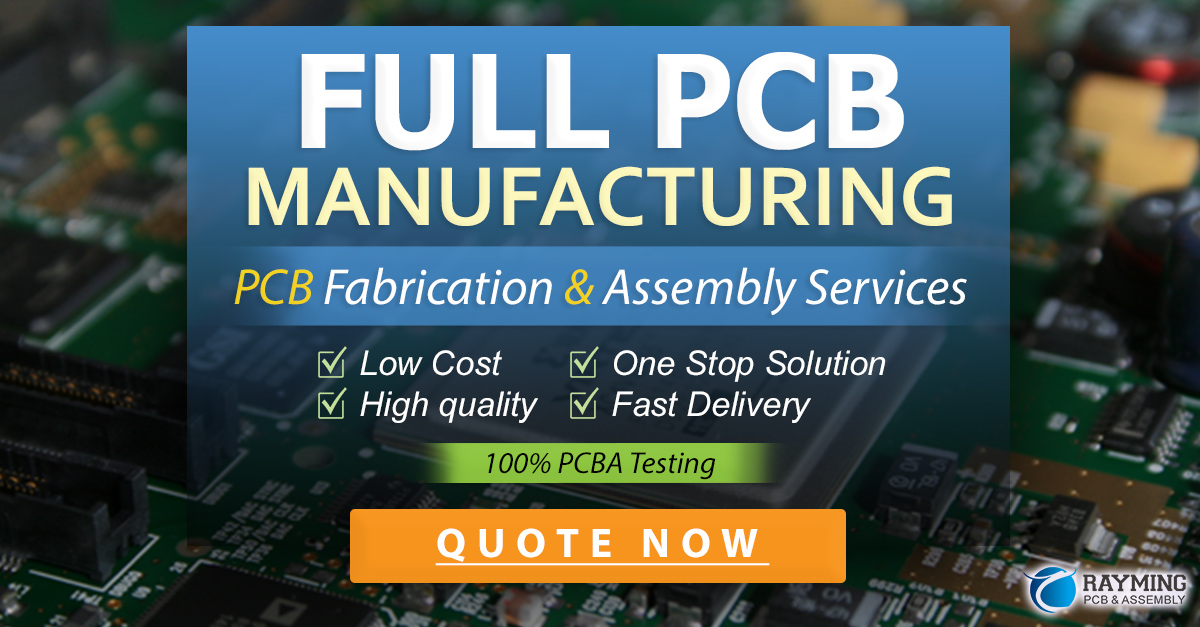
FR4 vs FR5: Key Differences
While FR4 and FR5 share many similarities, there are some key differences between the two materials:
-
Glass Transition Temperature (Tg): FR5 has a higher Tg (170°C) compared to FR4 (135°C), making it more suitable for high-temperature applications.
-
Thermal Stability: FR5 exhibits better thermal stability and performance, allowing it to withstand more extreme temperature fluctuations and thermal cycling.
-
Durability: FR5 is more durable and resistant to harsh environments, making it a better choice for applications that require long-term reliability in challenging conditions.
-
Cost: FR5 is generally more expensive than FR4 due to its enhanced properties and the higher-temperature epoxy resin used in its production.
Factors to Consider When Choosing Between FR4 and FR5
When deciding between FR4 and FR5 for your PCB project, consider the following factors:
-
Application Requirements: Evaluate the specific requirements of your application, such as operating temperature range, environmental conditions, and expected product lifespan.
-
Cost: Consider the budget constraints of your project and the cost difference between FR4 and FR5. While FR5 may offer better performance, it may not always be necessary for your specific application.
-
Manufacturing Capabilities: Ensure that your PCB manufacturer has experience working with both FR4 and FR5 materials and can provide guidance on the most suitable option for your project.
-
Compliance and Certifications: Verify that the chosen material meets the necessary industry standards and certifications for your application, such as UL, IPC, or RoHS.
Frequently Asked Questions (FAQ)
-
Q: Can FR4 and FR5 be used interchangeably in PCB manufacturing?
A: While FR4 and FR5 share many similarities, they are not always interchangeable. FR5 is designed for higher-temperature applications and may not be necessary for projects with lower thermal requirements. Conversely, using FR4 in high-temperature environments may lead to reduced performance and reliability. -
Q: Is FR5 always more expensive than FR4?
A: In general, FR5 is more expensive than FR4 due to its enhanced properties and the higher-temperature epoxy resin used in its production. However, the cost difference may vary depending on the specific manufacturer and the volume of material required for your project. -
Q: Can FR4 and FR5 be combined in a single PCB?
A: While it is technically possible to combine FR4 and FR5 in a single PCB, it is not a common practice. Doing so may lead to manufacturing challenges and potential reliability issues due to the different thermal properties of the materials. It is generally recommended to use a single material throughout a PCB design. -
Q: What is the main advantage of using FR5 over FR4?
A: The main advantage of using FR5 over FR4 is its higher glass transition temperature (Tg) and better thermal stability. This makes FR5 more suitable for applications that require operation in high-temperature environments or exposure to extreme temperature fluctuations. -
Q: Are there any environmental concerns associated with using FR4 or FR5?
A: Both FR4 and FR5 materials are compliant with RoHS (Restriction of Hazardous Substances) regulations, which restrict the use of certain hazardous substances in electronic products. However, it is essential to verify that the specific FR4 or FR5 material used in your project meets the necessary environmental and safety standards for your application and target market.
Conclusion
Understanding the differences between FR4 and FR5 materials is crucial for selecting the most suitable option for your PCB project. While both materials offer excellent properties for PCB manufacturing, FR5 stands out for its higher glass transition temperature and better thermal stability, making it the preferred choice for high-temperature and harsh environment applications.
When choosing between FR4 and FR5, consider your application requirements, cost constraints, manufacturing capabilities, and compliance with relevant industry standards. By carefully evaluating these factors and consulting with your PCB manufacturer, you can ensure that your project uses the most appropriate material for optimal performance and reliability.
As technology continues to advance and new applications emerge, the demand for high-performance PCB materials like FR4 and FR5 will continue to grow. By staying informed about the latest developments in PCB materials and their properties, you can make informed decisions and create innovative electronic products that meet the evolving needs of your customers.
No responses yet