FR1 vs FR4: Understanding the Key Differences
When it comes to printed circuit boards (PCBs), the choice of material is crucial for ensuring optimal performance and reliability. Two of the most commonly used materials in PCB fabrication are FR1 and FR4. While both are flame-retardant (FR) grades, they have distinct characteristics that make them suitable for different applications. In this article, we will delve into the key differences between FR1 and FR4 PCBs, helping you make an informed decision for your next project.
What is FR1?
FR1, also known as phenolic paper, is a composite material made from paper impregnated with a phenolic resin. It is one of the earliest materials used in PCB fabrication and is still widely used today due to its low cost and ease of manufacturing.
Characteristics of FR1:
- Composition: Paper base impregnated with phenolic resin
- Flame Retardancy: Rated as flame-retardant, but not as effective as FR4
- Dielectric Constant: Typically around 4.5 at 1 MHz
- Dissipation Factor: Relatively high, around 0.05 at 1 MHz
- Moisture Absorption: High, around 1.5% to 2.0%
- Thermal Expansion: High, around 20 to 30 ppm/°C
- Temperature Resistance: Limited, suitable for applications up to 130°C
- Mechanical Strength: Moderate, prone to warping and twisting
- Drilling: Easy to drill due to soft composition
- Cost: Low, making it an economical choice for basic applications
What is FR4?
FR4, also known as fiberglass-reinforced epoxy laminate, is a composite material made from woven fiberglass cloth impregnated with an epoxy resin. It is the most widely used material in PCB fabrication due to its excellent electrical, mechanical, and thermal properties.
Characteristics of FR4:
- Composition: Woven fiberglass cloth impregnated with epoxy resin
- Flame Retardancy: Excellent, meeting UL 94 V-0 standards
- Dielectric Constant: Typically around 4.5 at 1 MHz
- Dissipation Factor: Low, around 0.02 at 1 MHz
- Moisture Absorption: Low, around 0.1% to 0.2%
- Thermal Expansion: Low, around 12 to 16 ppm/°C
- Temperature Resistance: High, suitable for applications up to 170°C
- Mechanical Strength: Excellent, resistant to warping and twisting
- Drilling: More difficult to drill compared to FR1 due to harder composition
- Cost: Higher than FR1, but still cost-effective for most applications
Comparing FR1 and FR4
Now that we have a basic understanding of FR1 and FR4, let’s compare their properties side by side:
Property | FR1 | FR4 |
---|---|---|
Composition | Paper + Phenolic | Fiberglass + Epoxy |
Flame Retardancy | Moderate | Excellent (UL 94 V-0) |
Dielectric Constant | ~4.5 at 1 MHz | ~4.5 at 1 MHz |
Dissipation Factor | ~0.05 at 1 MHz | ~0.02 at 1 MHz |
Moisture Absorption | 1.5% to 2.0% | 0.1% to 0.2% |
Thermal Expansion | 20 to 30 ppm/°C | 12 to 16 ppm/°C |
Temperature Resistance | Up to 130°C | Up to 170°C |
Mechanical Strength | Moderate | Excellent |
Drilling | Easy | More difficult |
Cost | Low | Higher than FR1 |
Choosing Between FR1 and FR4
When deciding between FR1 and FR4 for your PCB project, consider the following factors:
-
Application Requirements: Evaluate the electrical, thermal, and mechanical requirements of your application. If your project demands high performance, reliability, and durability, FR4 is the better choice. FR1 is suitable for basic, low-cost applications with less stringent requirements.
-
Environmental Factors: Consider the operating environment of your PCB. If the board will be exposed to high temperatures, humidity, or harsh conditions, FR4 is the preferred option due to its superior temperature resistance and lower moisture absorption.
-
Manufacturing Process: Take into account the manufacturing process and any specific requirements. FR4 is compatible with a wider range of fabrication techniques and is better suited for multilayer designs and high-density layouts. FR1 is easier to drill and cut, making it suitable for simple, single-layer boards.
-
Budget Constraints: Evaluate your budget and cost considerations. FR1 is generally more affordable than FR4, making it an attractive option for cost-sensitive projects. However, the long-term performance and reliability benefits of FR4 may outweigh the initial cost savings in certain applications.
Applications of FR1 and FR4
FR1 Applications:
- Simple, single-layer PCBs
- Low-cost consumer electronics
- Educational and hobby projects
- Prototyping and quick-turn PCBs
- Low-power, low-frequency circuits
FR4 Applications:
- High-performance, multilayer PCBs
- Industrial and automotive electronics
- Medical devices and equipment
- Aerospace and military systems
- Telecommunications and networking equipment
- High-speed digital circuits
- RF and microwave applications
Frequently Asked Questions (FAQ)
-
Q: Can FR1 be used for multilayer PCBs?
A: While it is technically possible to create multilayer PCBs using FR1, it is not recommended due to its inferior mechanical and thermal properties compared to FR4. FR1 is more prone to warping and delamination in multilayer constructions. -
Q: Is FR4 always the better choice for PCBs?
A: FR4 is the preferred choice for most PCB applications due to its superior properties. However, in certain cases where cost is a primary concern and the performance requirements are not stringent, FR1 can be a viable option. -
Q: Can FR1 and FR4 be mixed in the same PCB?
A: Mixing FR1 and FR4 in the same PCB is not a common practice and is generally not recommended. The different thermal expansion rates and mechanical properties of the two materials can lead to reliability issues and manufacturing challenges. -
Q: How does the flame retardancy of FR1 and FR4 compare?
A: FR4 offers better flame retardancy than FR1. FR4 is rated as UL 94 V-0, meaning it self-extinguishes within 10 seconds of removing the flame source. FR1, while still considered flame-retardant, does not meet the same level of performance as FR4. -
Q: Are there any environmental concerns with using FR1 or FR4?
A: Both FR1 and FR4 materials may contain certain substances that are regulated or restricted in some regions, such as brominated flame retardants (BFRs) and lead. It is important to ensure that the specific FR1 or FR4 material used complies with the relevant environmental regulations and directives, such as RoHS and REACH.
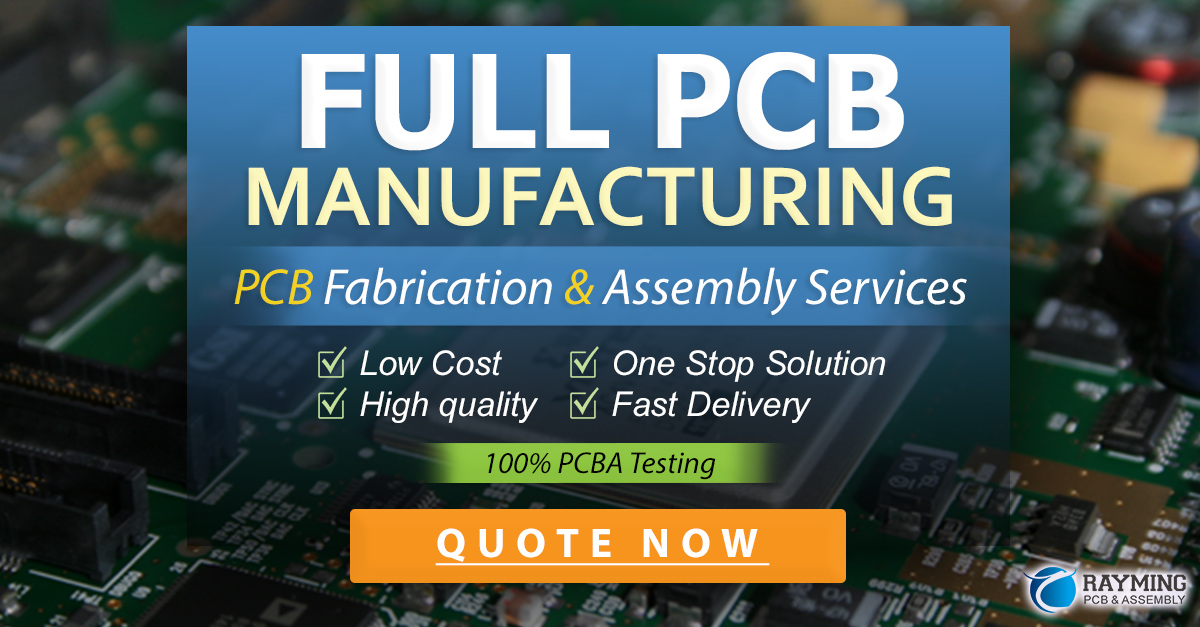
Conclusion
Understanding the differences between FR1 and FR4 PCB materials is crucial for making informed decisions in PCB design and fabrication. While FR1 offers a low-cost option for basic applications, FR4 provides superior performance, reliability, and versatility for a wide range of demanding applications. By considering factors such as application requirements, environmental conditions, manufacturing process, and budget constraints, you can select the most appropriate material for your PCB project.
Remember, the choice of PCB material is just one aspect of the overall design process. It is essential to work closely with experienced PCB designers and manufacturers to ensure that your PCB meets all the necessary requirements and standards for your specific application.
As technology continues to advance, new PCB materials and manufacturing techniques may emerge, offering even better performance and cost-effectiveness. Staying updated with the latest developments in PCB technology will help you make informed decisions and stay competitive in your industry.
No responses yet