What is CEM?
CEM, which stands for Composite Epoxy Material, is a type of PCB substrate made from a combination of woven glass fabric and epoxy resin. The glass fabric provides mechanical strength, while the epoxy resin acts as a binder and insulator. CEM is available in different grades, with CEM-1 and CEM-3 being the most common.
CEM-1
CEM-1 is the most basic grade of CEM, consisting of a single layer of woven glass fabric impregnated with epoxy resin. It is lightweight, cost-effective, and suitable for low-end applications that do not require high mechanical strength or thermal stability.
CEM-3
CEM-3 is an upgraded version of CEM-1, featuring a double-sided woven glass fabric impregnated with epoxy resin. This additional layer of glass fabric provides increased mechanical strength and better electrical properties compared to CEM-1. CEM-3 is commonly used in consumer electronics, telecommunications, and industrial applications.
What is FR4?
FR4, short for Flame Retardant 4, is a high-performance PCB substrate made from woven glass fabric impregnated with an epoxy resin system. The “4” in FR4 refers to the flammability rating of the material, indicating that it is self-extinguishing and does not easily catch fire. FR4 is the most widely used PCB substrate in the electronics industry due to its excellent mechanical, electrical, and thermal properties.
Key Differences between CEM and FR4
Composition
The main difference between CEM and FR4 lies in their composition. While both materials use woven glass fabric and epoxy resin, FR4 uses a higher-grade epoxy resin system that provides superior performance characteristics.
Material | Composition |
---|---|
CEM | Woven glass fabric + epoxy resin |
FR4 | Woven glass fabric + high-grade epoxy resin system |
Mechanical Strength
FR4 exhibits higher mechanical strength compared to CEM due to its superior epoxy resin system and the use of higher-quality woven glass fabric. This makes FR4 more suitable for applications that require greater durability and resistance to mechanical stress.
Material | Mechanical Strength |
---|---|
CEM | Lower |
FR4 | Higher |
Thermal Stability
FR4 has better thermal stability than CEM, meaning it can withstand higher temperatures without degrading or losing its properties. This is particularly important in applications where the PCB is exposed to high operating temperatures or requires soldering.
Material | Thermal Stability |
---|---|
CEM | Lower |
FR4 | Higher |
Electrical Properties
FR4 offers superior electrical properties compared to CEM, including better dielectric strength, lower dielectric constant, and lower dissipation factor. These properties make FR4 more suitable for high-frequency and high-speed applications.
Material | Dielectric Strength | Dielectric Constant | Dissipation Factor |
---|---|---|---|
CEM | Lower | Higher | Higher |
FR4 | Higher | Lower | Lower |
Moisture Resistance
FR4 has better moisture resistance than CEM due to its higher-grade epoxy resin system. This makes FR4 more suitable for applications where the PCB may be exposed to humid environments or requires protection against moisture-related issues such as delamination and warping.
Material | Moisture Resistance |
---|---|
CEM | Lower |
FR4 | Higher |
Cost
CEM is generally less expensive than FR4 due to its simpler composition and lower-grade materials. This makes CEM a more cost-effective option for low-end applications where high performance is not a critical requirement.
Material | Cost |
---|---|
CEM | Lower |
FR4 | Higher |
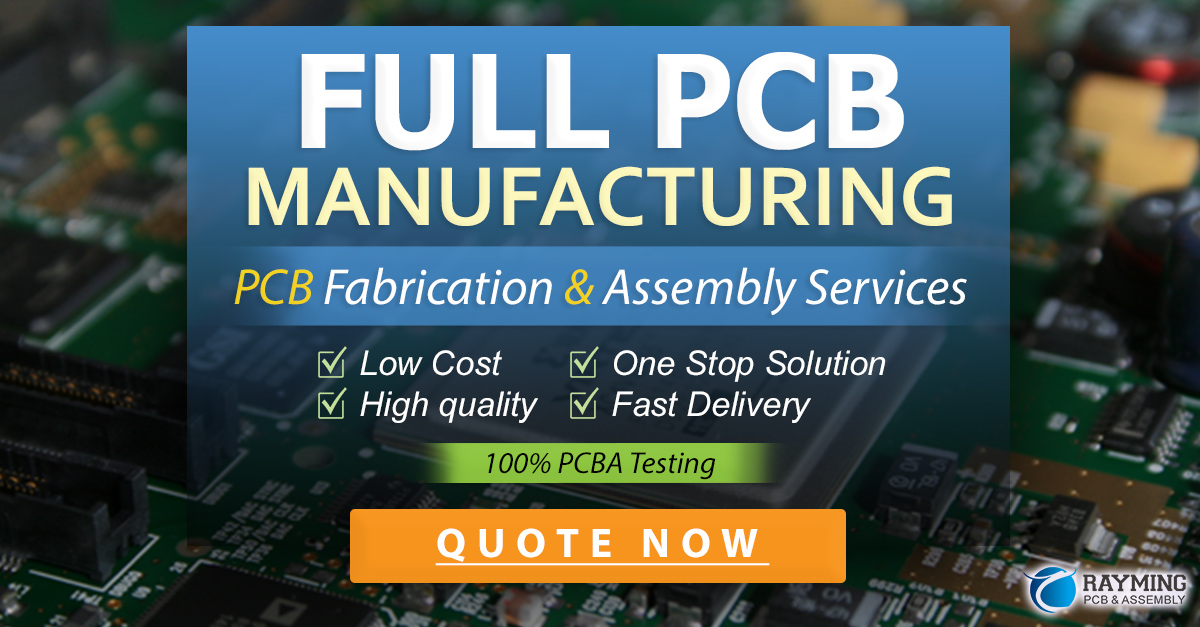
Applications
CEM Applications
CEM is commonly used in low-end and cost-sensitive applications where high performance is not a primary concern. Some typical applications of CEM include:
- Consumer electronics (e.g., toys, calculators, remote controls)
- Low-power telecommunications equipment
- Simple industrial control systems
- Educational and hobby projects
FR4 Applications
FR4 is the preferred choice for a wide range of applications that demand high performance, reliability, and durability. Some common applications of FR4 include:
- High-speed digital electronics
- Automotive electronics
- Aerospace and defense systems
- Medical devices
- Industrial control and automation systems
- Telecommunications equipment
- Computer peripherals and networking devices
Advantages and Disadvantages
CEM Advantages
- Lower cost compared to FR4
- Lightweight
- Suitable for low-end applications
CEM Disadvantages
- Lower mechanical strength
- Reduced thermal stability
- Inferior electrical properties
- Lower moisture resistance
FR4 Advantages
- Excellent mechanical strength
- High thermal stability
- Superior electrical properties
- Good moisture resistance
- Wide range of applications
FR4 Disadvantages
- Higher cost compared to CEM
- Slightly heavier than CEM
Frequently Asked Questions (FAQ)
-
Q: Can CEM be used as a substitute for FR4 in high-performance applications?
A: While CEM can be used in some applications where FR4 is specified, it is not recommended for high-performance applications due to its inferior mechanical, thermal, and electrical properties. FR4 is the preferred choice for applications that demand high reliability and performance. -
Q: Is FR4 always the better choice compared to CEM?
A: Not necessarily. The choice between CEM and FR4 depends on the specific requirements of the application. For low-end applications where cost is a primary concern and high performance is not critical, CEM can be a suitable and more cost-effective option. -
Q: Can CEM and FR4 be used together in the same PCB?
A: While it is technically possible to use both CEM and FR4 in the same PCB, it is not a common practice. Mixing different substrate materials can lead to compatibility issues and may compromise the overall performance and reliability of the PCB. -
Q: How does the flammability rating of FR4 compare to CEM?
A: FR4 has a better flammability rating compared to CEM. The “4” in FR4 refers to the UL94 V-0 flammability rating, which means that the material is self-extinguishing and does not easily catch fire. CEM, on the other hand, has a lower flammability rating and may not be suitable for applications that require strict flame retardance. -
Q: Are there any environmental concerns associated with the use of CEM or FR4?
A: Both CEM and FR4 contain epoxy resins, which can have some environmental impact during production and disposal. However, many PCB manufacturers now use eco-friendly and RoHS-Compliant materials to minimize the environmental impact. It is important to choose a reputable PCB manufacturer that adheres to environmental regulations and standards.
Conclusion
In summary, CEM and FR4 are two distinct PCB substrate materials with different compositions, properties, and applications. CEM is a cost-effective option for low-end applications that do not require high performance, while FR4 is the preferred choice for high-performance applications that demand superior mechanical, thermal, and electrical properties.
When selecting between CEM and FR4, it is essential to consider the specific requirements of your application, such as the operating environment, electrical performance, and budget constraints. By understanding the key differences between these two materials, you can make an informed decision and choose the most suitable substrate for your PCB design.
As technology continues to advance, new materials and manufacturing techniques may emerge, offering even better performance and cost-effectiveness. However, for now, CEM and FR4 remain the two most widely used PCB substrate materials in the electronics industry, each with its own unique advantages and disadvantages.
No responses yet