Introduction to CEM vs FR4
When it comes to printed circuit board (PCB) materials, two of the most common types are CEM (Composite Epoxy Material) and FR4 (Flame Retardant 4). Both are widely used as insulating substrates and have their own unique properties, advantages, and disadvantages. Understanding the differences between CEM and FR4 is crucial for designers and manufacturers to select the most suitable material for their specific applications.
In this comprehensive article, we will delve into the details of CEM and FR4, comparing their composition, physical properties, thermal and electrical characteristics, as well as their applications and cost considerations. By the end of this article, you will have a clear understanding of the key differences between CEM and FR4, enabling you to make informed decisions when choosing PCB Materials for your projects.
What is CEM?
CEM, short for Composite Epoxy Material, is a type of PCB material that consists of a composite of woven glass fabric impregnated with epoxy resin. It is a cost-effective Alternative to FR4 and is commonly used in consumer electronics, appliances, and low-end industrial applications.
Composition of CEM
CEM is made by combining woven glass fabric with epoxy resin under heat and pressure. The glass fabric provides mechanical strength and dimensional stability, while the epoxy resin acts as a binder and insulator. The specific composition of CEM can vary depending on the grade and manufacturer, but it generally contains the following components:
- Woven glass fabric (E-glass)
- Epoxy resin
- Flame retardants (optional)
- Fillers and additives (optional)
Grades of CEM
There are several grades of CEM available, each with slightly different properties and applications:
Grade | Description |
---|---|
CEM-1 | Single-sided PCB material with paper core and epoxy resin |
CEM-2 | Double-sided PCB material with paper core and epoxy resin |
CEM-3 | Single-sided PCB material with woven glass fabric and epoxy resin |
CEM-4 | Double-sided PCB material with woven glass fabric and epoxy resin |
CEM-5 | Double-sided PCB material with woven glass fabric, polyester resin, and epoxy resin |
Among these grades, CEM-3 and CEM-4 are the most commonly used due to their balanced properties and cost-effectiveness.
Advantages of CEM
- Lower cost compared to FR4
- Good mechanical strength and dimensional stability
- Adequate electrical insulation properties
- Suitable for low-end and consumer applications
Disadvantages of CEM
- Lower thermal resistance compared to FR4
- Higher moisture absorption than FR4
- Limited high-frequency performance
- Not suitable for high-reliability and harsh environment applications
What is FR4?
FR4, or Flame Retardant 4, is a high-performance PCB material that consists of woven glass fabric impregnated with epoxy resin. It is the most widely used PCB material and is known for its excellent mechanical, thermal, and electrical properties. FR4 is commonly used in a wide range of applications, including telecommunications, automotive, aerospace, and industrial electronics.
Composition of FR4
FR4 is made by impregnating woven glass fabric with epoxy resin under heat and pressure. The glass fabric provides mechanical strength and dimensional stability, while the epoxy resin acts as a binder, insulator, and flame retardant. The specific composition of FR4 can vary depending on the grade and manufacturer, but it generally contains the following components:
- Woven glass fabric (E-glass)
- Epoxy resin
- Brominated flame retardants
- Fillers and additives (optional)
Grades of FR4
There are several grades of FR4 available, each with slightly different properties and applications:
Grade | Description |
---|---|
FR4 standard | General-purpose PCB material with good thermal and mechanical properties |
FR4 High Tg | PCB material with higher glass transition temperature (Tg) for improved thermal stability |
FR4 Halogen-Free | PCB material with non-brominated flame retardants for environmental compliance |
FR4 High-Speed | PCB material with optimized dielectric properties for high-frequency applications |
Among these grades, FR4 Standard is the most commonly used due to its balanced properties and wide availability.
Advantages of FR4
- Excellent mechanical strength and dimensional stability
- High thermal resistance and glass transition temperature (Tg)
- Good electrical insulation and dielectric properties
- Wide operating temperature range
- Flame retardant properties
- Suitable for high-reliability and harsh environment applications
Disadvantages of FR4
- Higher cost compared to CEM
- Higher weight and density than some alternative materials
- Moderate moisture absorption
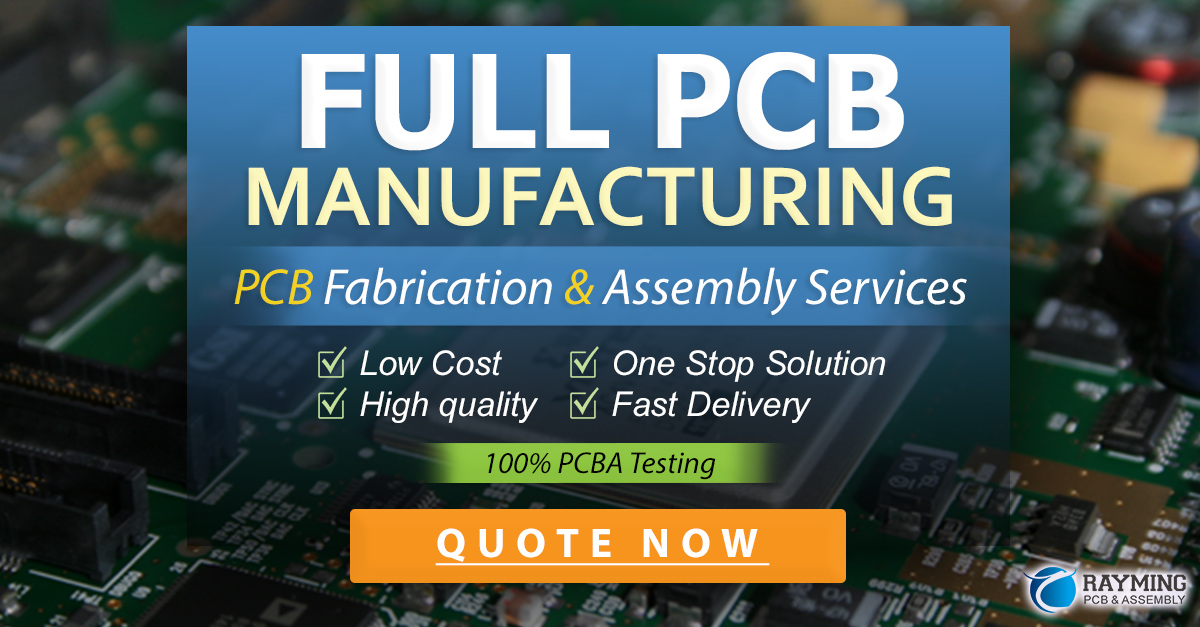
Comparison of CEM and FR4
Now that we have a basic understanding of CEM and FR4, let’s compare their key properties and characteristics in detail.
Physical Properties
Property | CEM | FR4 |
---|---|---|
Density (g/cm³) | 1.7-1.9 | 1.8-2.0 |
Water Absorption (%) | 0.1-0.3 | 0.1-0.2 |
Flexural Strength (MPa) | 200-400 | 400-600 |
Tensile Strength (MPa) | 200-300 | 300-400 |
Compressive Strength (MPa) | 300-500 | 500-700 |
As seen in the table above, FR4 generally exhibits better physical properties compared to CEM, with higher strength and lower water absorption.
Thermal Properties
Property | CEM | FR4 |
---|---|---|
Glass Transition Temperature (Tg) (°C) | 130-140 | 130-180 |
Thermal Conductivity (W/m·K) | 0.2-0.3 | 0.3-0.4 |
Coefficient of Thermal Expansion (CTE) (ppm/°C) | 12-16 | 12-14 |
Operating Temperature Range (°C) | -40 to +125 | -55 to +125 |
FR4 has a higher glass transition temperature (Tg) and thermal conductivity compared to CEM, making it more suitable for applications with higher thermal requirements.
Electrical Properties
Property | CEM | FR4 |
---|---|---|
Dielectric Constant (1 MHz) | 4.0-4.5 | 4.2-4.8 |
Dissipation Factor (1 MHz) | 0.02-0.03 | 0.01-0.02 |
Surface Resistivity (MΩ) | 10⁵-10⁷ | 10⁶-10⁸ |
Volume Resistivity (MΩ·cm) | 10⁷-10⁹ | 10⁸-10¹⁰ |
Dielectric Breakdown Strength (kV/mm) | 15-20 | 20-30 |
FR4 has slightly better electrical properties compared to CEM, with lower dissipation factor, higher surface and volume resistivity, and higher dielectric breakdown strength.
Applications
CEM is commonly used in:
1. Consumer electronics
2. Appliances
3. Low-end industrial applications
4. Cost-sensitive projects
FR4 is widely used in:
1. Telecommunications
2. Automotive electronics
3. Aerospace and defense
4. Industrial control systems
5. Medical devices
6. High-reliability applications
Cost Considerations
CEM is generally less expensive than FR4 due to its simpler composition and manufacturing process. The cost difference between CEM and FR4 can vary depending on the specific grade, thickness, and copper cladding, but CEM is typically 20-30% cheaper than FR4.
However, it is essential to consider the total cost of ownership (TCO) when selecting PCB materials. While CEM may have a lower initial cost, FR4 may offer better long-term value in terms of reliability, performance, and durability, especially for high-end applications.
Frequently Asked Questions (FAQ)
1. Can CEM be used as a substitute for FR4 in all applications?
No, CEM is not a direct substitute for FR4 in all applications. While CEM can be used in cost-sensitive and low-end applications, it may not meet the performance requirements of high-reliability and harsh environment applications where FR4 excels.
2. Is FR4 always the best choice for PCB materials?
FR4 is a versatile and widely used PCB material, but it may not always be the best choice for every application. Other materials, such as polyimide, PTFE, or high-frequency laminates, may be more suitable for specific requirements like extreme temperatures, high frequencies, or flexible circuits.
3. Can CEM and FR4 be mixed in the same PCB stack-up?
While it is technically possible to mix CEM and FR4 in the same PCB stack-up, it is generally not recommended due to their different thermal and mechanical properties. Mixing materials can lead to reliability issues and manufacturing challenges.
4. How do I choose between CEM and FR4 for my project?
When choosing between CEM and FR4, consider the following factors:
1. Performance requirements (thermal, mechanical, electrical)
2. Operating environment (temperature, humidity, vibration)
3. Reliability expectations (product lifespan, failure rate)
4. Cost constraints (initial cost, total cost of ownership)
5. Manufacturing capabilities (available processes, equipment)
5. Are there any environmental concerns with using CEM or FR4?
Both CEM and FR4 can contain flame retardants, which may have environmental and health concerns. Some FR4 Grades use brominated flame retardants, which can be harmful if not properly managed. Halogen-free and eco-friendly alternatives are available for both CEM and FR4, but they may come with a higher cost or limited availability.
Conclusion
CEM and FR4 are two common PCB materials with distinct properties and applications. CEM offers a cost-effective solution for low-end and consumer applications, while FR4 provides superior performance and reliability for high-end and demanding applications.
When selecting between CEM and FR4, it is crucial to consider the specific requirements of your project, including performance, environment, reliability, and cost factors. By understanding the differences between these materials, you can make an informed decision and choose the most suitable PCB material for your application.
As technology advances and new materials emerge, it is essential to stay updated on the latest developments in PCB materials and manufacturing processes. This knowledge will enable you to design and manufacture high-quality, reliable, and cost-effective PCBs that meet the evolving needs of the electronics industry.
No responses yet