Introduction to CEM-1 and FR-4 Materials
CEM-1 (Composite Epoxy Material) and FR-4 (Flame Retardant 4) are two commonly used materials for manufacturing printed circuit boards (PCBs). Both materials are composed of woven fiberglass cloth impregnated with an epoxy resin binder. However, there are several key differences between CEM-1 and FR-4 in terms of their composition, properties, applications, and costs.
Understanding the distinctions between CEM-1 and FR-4 is crucial for selecting the appropriate material for your PCB project. In this comprehensive article, we will delve into the details of CEM-1 and FR-4, comparing their characteristics, advantages, disadvantages, and typical use cases. By the end of this article, you will have a clear understanding of the differences between these two materials and be able to make an informed decision when choosing between CEM-1 and FR-4 for your PCB design.
CEM-1: Composition and Properties
Composition of CEM-1
CEM-1 is a composite material made up of a woven fiberglass cloth substrate combined with an epoxy resin binder. The fiberglass cloth provides mechanical strength and dimensional stability to the material, while the epoxy resin acts as an insulator and binds the fiberglass together.
One of the defining characteristics of CEM-1 is its composition ratio. CEM-1 typically consists of a single layer of fiberglass cloth, which is then impregnated with a flame-retardant epoxy resin. The proportion of fiberglass to epoxy resin in CEM-1 is lower compared to FR-4, resulting in a material that is less expensive to produce but also less robust.
Physical and Mechanical Properties of CEM-1
CEM-1 exhibits several physical and mechanical properties that make it suitable for certain PCB applications:
-
Thermal Expansion: CEM-1 has a higher coefficient of thermal expansion (CTE) compared to FR-4. This means that CEM-1 is more prone to expansion and contraction when subjected to temperature changes, which can lead to warping or deformation of the PCB.
-
Glass Transition Temperature (Tg): The glass transition temperature of CEM-1 is lower than that of FR-4. Tg is the temperature at which the material transitions from a rigid, glassy state to a softer, rubbery state. A lower Tg indicates that CEM-1 may not perform as well as FR-4 in high-temperature environments.
-
Moisture Absorption: CEM-1 has a higher moisture absorption rate compared to FR-4. This can lead to dimensional instability and reduced electrical performance in humid environments.
-
Mechanical Strength: Due to its lower fiberglass content, CEM-1 has lower mechanical strength and stiffness compared to FR-4. This can result in reduced durability and increased susceptibility to damage during handling and assembly.
Electrical Properties of CEM-1
CEM-1 possesses electrical properties that are suitable for certain PCB applications, but may not be ideal for high-frequency or high-speed designs:
-
Dielectric Constant (Dk): The dielectric constant of CEM-1 is typically higher than that of FR-4. A higher Dk value indicates that CEM-1 has a greater capacity to store electrical energy, which can lead to increased signal propagation delay and reduced signal integrity.
-
Dissipation Factor (Df): CEM-1 has a higher dissipation factor compared to FR-4. A higher Df value means that CEM-1 has greater dielectric losses, which can result in increased signal attenuation and reduced signal quality.
-
Electrical Strength: The electrical strength of CEM-1 is lower than that of FR-4. This implies that CEM-1 may be more susceptible to electrical breakdown or arcing when subjected to high voltages.
Advantages and Disadvantages of CEM-1
Advantages:
- Lower cost compared to FR-4
- Suitable for low-frequency and low-speed PCB designs
- Adequate for applications with less demanding thermal and mechanical requirements
Disadvantages:
- Higher thermal expansion and lower glass transition temperature
- Higher moisture absorption rate
- Lower mechanical strength and stiffness
- Higher dielectric constant and dissipation factor
- Lower electrical strength
Typical Applications of CEM-1
CEM-1 is commonly used in PCB applications where cost is a primary concern and the performance requirements are not as stringent. Some typical applications of CEM-1 include:
- Consumer electronics
- Low-frequency and low-speed digital circuits
- Single-sided or double-sided PCBs
- Prototyping and small-scale production runs
FR-4: Composition and Properties
Composition of FR-4
FR-4 is a composite material consisting of multiple layers of woven fiberglass cloth impregnated with a flame-retardant epoxy resin. The “FR” in FR-4 stands for “Flame Retardant,” indicating that the material has been treated to reduce its flammability.
Compared to CEM-1, FR-4 has a higher proportion of fiberglass to epoxy resin. This composition ratio contributes to FR-4’s superior mechanical, thermal, and electrical properties. The multiple layers of fiberglass cloth in FR-4 provide increased strength and dimensional stability, making it a more robust material overall.
Physical and Mechanical Properties of FR-4
FR-4 exhibits several physical and mechanical properties that make it a preferred choice for many PCB applications:
-
Thermal Expansion: FR-4 has a lower coefficient of thermal expansion (CTE) compared to CEM-1. This means that FR-4 is less prone to expansion and contraction when subjected to temperature changes, resulting in better dimensional stability and reduced warping of the PCB.
-
Glass Transition Temperature (Tg): The glass transition temperature of FR-4 is higher than that of CEM-1. A higher Tg indicates that FR-4 can maintain its mechanical and electrical properties at higher temperatures, making it suitable for applications that require operation in elevated temperature environments.
-
Moisture Absorption: FR-4 has a lower moisture absorption rate compared to CEM-1. This property helps maintain the dimensional stability and electrical performance of FR-4 PCBs in humid conditions.
-
Mechanical Strength: Due to its higher fiberglass content and multiple layers, FR-4 exhibits superior mechanical strength and stiffness compared to CEM-1. This makes FR-4 PCBs more durable and resistant to damage during handling, assembly, and operation.
Electrical Properties of FR-4
FR-4 possesses excellent electrical properties that make it suitable for a wide range of PCB applications, including high-frequency and high-speed designs:
-
Dielectric Constant (Dk): The dielectric constant of FR-4 is lower than that of CEM-1. A lower Dk value indicates that FR-4 has a lower capacity to store electrical energy, which results in reduced signal propagation delay and improved signal integrity.
-
Dissipation Factor (Df): FR-4 has a lower dissipation factor compared to CEM-1. A lower Df value means that FR-4 has lower dielectric losses, resulting in reduced signal attenuation and better signal quality.
-
Electrical Strength: The electrical strength of FR-4 is higher than that of CEM-1. This implies that FR-4 is more resistant to electrical breakdown or arcing when subjected to high voltages.
Advantages and Disadvantages of FR-4
Advantages:
- Superior mechanical strength and stiffness
- Lower thermal expansion and higher glass transition temperature
- Lower moisture absorption rate
- Lower dielectric constant and dissipation factor
- Higher electrical strength
- Suitable for a wide range of PCB applications, including high-frequency and high-speed designs
Disadvantages:
- Higher cost compared to CEM-1
- May be overspecified for simple, low-frequency, and low-speed PCB designs
Typical Applications of FR-4
FR-4 is widely used in various PCB applications due to its excellent mechanical, thermal, and electrical properties. Some typical applications of FR-4 include:
- High-frequency and high-speed digital circuits
- Multilayer PCBs
- Industrial and automotive electronics
- Telecommunications equipment
- Medical devices
- Aerospace and defense systems
- Consumer electronics with demanding performance requirements
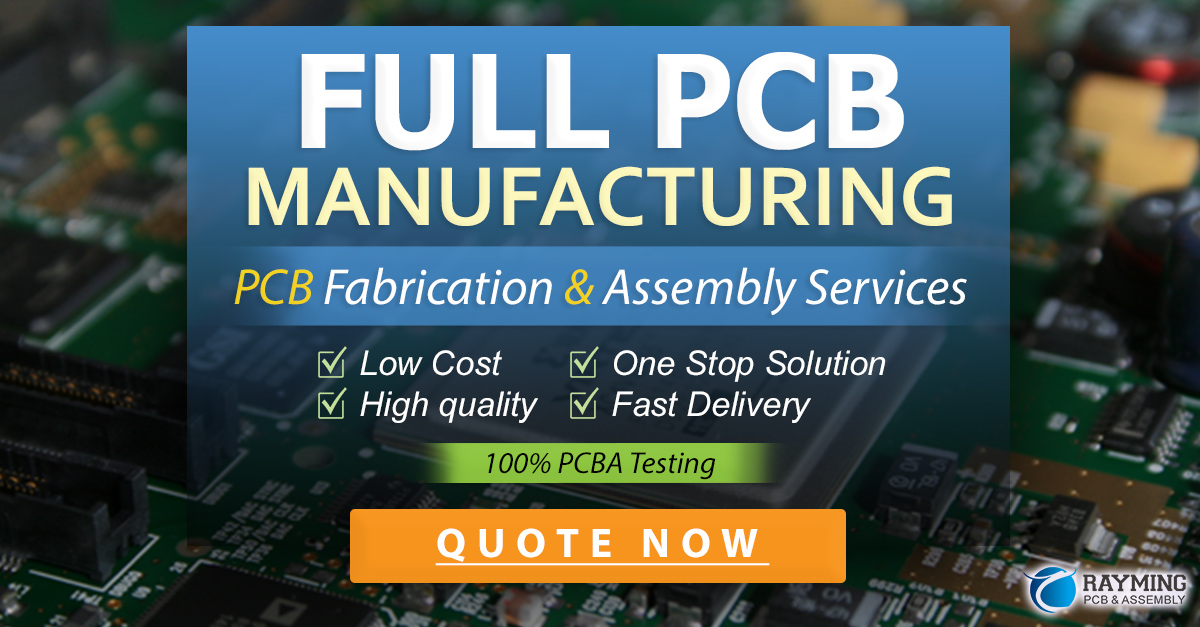
Comparison Table: CEM-1 vs. FR-4
Property | CEM-1 | FR-4 |
---|---|---|
Composition | Single layer of fiberglass cloth with epoxy resin | Multiple layers of fiberglass cloth with epoxy resin |
Fiberglass to Epoxy Ratio | Lower | Higher |
Thermal Expansion (CTE) | Higher | Lower |
Glass Transition Temperature (Tg) | Lower | Higher |
Moisture Absorption | Higher | Lower |
Mechanical Strength | Lower | Higher |
Dielectric Constant (Dk) | Higher | Lower |
Dissipation Factor (Df) | Higher | Lower |
Electrical Strength | Lower | Higher |
Cost | Lower | Higher |
Choosing Between CEM-1 and FR-4
When deciding between CEM-1 and FR-4 for your PCB project, consider the following factors:
-
Performance Requirements: Evaluate the electrical, thermal, and mechanical requirements of your application. If your design involves high-frequency signals, high-speed digital circuits, or demanding environmental conditions, FR-4 may be the better choice. For simpler, low-frequency, and low-speed designs, CEM-1 may suffice.
-
Cost Considerations: CEM-1 is generally less expensive than FR-4 due to its simpler composition and lower fiberglass content. If cost is a primary concern and your application does not require the superior properties of FR-4, CEM-1 can be a cost-effective option.
-
Reliability and Durability: Consider the expected lifespan and operating conditions of your PCB. If your application demands high reliability, durability, and resistance to environmental factors such as temperature fluctuations and humidity, FR-4 is likely the better choice.
-
Manufacturing Considerations: Discuss your material choice with your PCB manufacturer. They can provide guidance on the suitability of CEM-1 or FR-4 for your specific design and manufacturing process. Some manufacturers may have limitations or preferences regarding the use of certain materials.
FAQ
1. Can CEM-1 be used for multilayer PCBs?
While CEM-1 can be used for multilayer PCBs, it is not as common as using FR-4. CEM-1’s lower mechanical strength and higher thermal expansion can make it less suitable for complex, high-density multilayer designs. FR-4 is generally preferred for multilayer PCBs due to its superior properties and reliability.
2. Is FR-4 always the better choice for PCB designs?
Not necessarily. FR-4 offers superior mechanical, thermal, and electrical properties compared to CEM-1, but it also comes at a higher cost. For simple, low-frequency, and low-speed PCB designs with less demanding performance requirements, CEM-1 can be a cost-effective alternative. The choice between FR-4 and CEM-1 depends on the specific requirements and constraints of your application.
3. Can CEM-1 and FR-4 be used together in the same PCB?
While it is technically possible to use CEM-1 and FR-4 together in the same PCB, it is not a common practice. Mixing materials with different properties can lead to compatibility issues, such as mismatches in thermal expansion or mechanical stress. It is generally recommended to use a single material throughout a PCB design to ensure consistent performance and reliability.
4. How do CEM-1 and FR-4 compare in terms of environmental impact?
Both CEM-1 and FR-4 are composed of fiberglass and epoxy resin, which are derived from non-renewable resources. However, the production of FR-4 may have a slightly higher environmental impact due to its higher fiberglass content and the additional processing required to achieve its superior properties. Proper disposal and recycling of PCBs, regardless of the material used, are important to minimize environmental harm.
5. Are there any alternative materials to CEM-1 and FR-4?
Yes, there are several alternative materials available for PCB fabrication, each with its own set of properties and advantages. Some examples include:
- High-frequency laminates (e.g., Rogers RO4000 series, PTFE-based materials) for applications requiring low dielectric loss and stable performance at high frequencies.
- Metal core PCBs (MCPCBs) for applications requiring enhanced thermal management and heat dissipation.
- Flexible PCBs (FPCBs) made from materials such as polyimide or polyester for applications requiring flexibility and conformability.
The choice of material depends on the specific requirements of your application, such as frequency, speed, thermal management, flexibility, and cost.
Conclusion
CEM-1 and FR-4 are two commonly used materials for manufacturing printed circuit boards, each with its own set of characteristics, advantages, and disadvantages. CEM-1 is a cost-effective option for simple, low-frequency, and low-speed PCB designs, while FR-4 offers superior mechanical, thermal, and electrical properties, making it suitable for a wide range of applications, including high-frequency and high-speed designs.
When choosing between CEM-1 and FR-4, it is essential to consider the performance requirements, cost considerations, reliability, durability, and manufacturing constraints of your specific application. Consulting with your PCB manufacturer can help you make an informed decision and ensure the success of your PCB project.
By understanding the differences between CEM-1 and FR-4, you can select the most appropriate material for your PCB design, balancing cost, performance, and reliability to achieve the best possible outcome for your application.
No responses yet