Introduction to PCA and PCB
In the world of electronics, two terms that are often used interchangeably are PCA (Printed Circuit Assembly) and PCB (Printed Circuit Board). While they may sound similar, there are some key differences between the two. In this article, we will explore the differences between PCA and PCB, their applications, and their manufacturing processes.
What is a PCB?
A Printed Circuit Board (PCB) is a flat board made of insulating material, such as fiberglass or plastic, with conductive copper traces printed on its surface. These traces are used to connect electronic components, such as resistors, capacitors, and integrated circuits, to form a complete electronic circuit.
PCBs are the foundation of modern electronics and are used in a wide range of applications, from simple electronic devices like calculators and remote controls to complex systems like computers and aerospace equipment.
Types of PCBs
There are several types of PCBs, each with its own unique characteristics and applications:
-
Single-sided PCBs: These PCBs have conductive traces on only one side of the board. They are the simplest and most cost-effective type of PCB, but they are limited in terms of circuit complexity and density.
-
Double-sided PCBs: These PCBs have conductive traces on both sides of the board, allowing for more complex circuits and higher component density. The two sides are connected using through-hole vias.
-
Multi-layer PCBs: These PCBs have multiple layers of conductive traces separated by insulating layers. They can have anywhere from four to over thirty layers, allowing for extremely complex circuits and high component density. Multi-layer PCBs are commonly used in advanced electronic systems, such as smartphones and medical devices.
-
Flexible PCBs: These PCBs are made from flexible materials, such as polyimide or PEEK, allowing them to bend and conform to different shapes. They are commonly used in applications where space is limited or where the PCB needs to fit into a curved or irregular space, such as in wearable devices or automotive electronics.
-
Rigid-Flex PCBs: These PCBs combine the benefits of both rigid and flexible PCBs. They have rigid sections for mounting components and flexible sections for connecting the rigid sections. Rigid-Flex PCBs are commonly used in applications where both high component density and flexibility are required, such as in aerospace and military equipment.
PCB Manufacturing Process
The manufacturing process for PCBs typically involves the following steps:
-
Design: The first step in PCB manufacturing is to design the circuit using specialized software. The design includes the placement of components, the routing of traces, and the creation of any necessary holes or vias.
-
Printing: Once the design is complete, it is printed onto a transparent film or directly onto the PCB substrate using a photoplotter or direct imaging machine.
-
Etching: The PCB substrate is then coated with a photoresist material and exposed to UV light through the printed film. The exposed areas of the photoresist are then removed, leaving behind a pattern of the circuit traces. The exposed copper is then etched away using a chemical solution, leaving behind the desired circuit pattern.
-
Drilling: Any necessary holes or vias are drilled into the PCB using a CNC drilling machine.
-
Plating: The holes and vias are then plated with copper to provide electrical connectivity between layers.
-
Solder Mask: A layer of solder mask is applied to the PCB to protect the copper traces from oxidation and to prevent solder bridging during assembly.
-
Silkscreen: A silkscreen layer is applied to the PCB to add labels, logos, and other identifying markings.
-
Testing: Finally, the PCB is tested for functionality and quality using automated testing equipment.
What is a PCA?
A Printed Circuit Assembly (PCA) is a PCB that has been populated with electronic components and is ready for use in an electronic device. In other words, a PCA is a fully assembled and functional electronic circuit.
PCAs are created by soldering electronic components, such as resistors, capacitors, and integrated circuits, onto a PCB. The components are typically placed on the PCB using automated pick-and-place machines, which can place hundreds of components per minute with high accuracy.
PCA Assembly Process
The assembly process for PCAs typically involves the following steps:
-
Solder Paste Application: A thin layer of solder paste is applied to the PCB using a stencil or screen printing process. The solder paste is a mixture of tiny solder particles suspended in a flux material.
-
Component Placement: The electronic components are placed onto the PCB using automated pick-and-place machines. The machines use computer vision and precision robotics to place the components accurately and quickly.
-
Reflow Soldering: The PCB with the placed components is then passed through a reflow oven, which heats the solder paste to its melting point, allowing it to flow and form a strong electrical and mechanical bond between the components and the PCB.
-
Inspection: After soldering, the PCA is inspected for quality using automated optical inspection (AOI) machines or manual inspection by trained technicians.
-
Testing: Finally, the PCA is tested for functionality using automated testing equipment or manual testing procedures.
PCA vs PCB: Key Differences
While PCAs and PCBs are closely related, there are some key differences between the two:
Feature | PCB | PCA |
---|---|---|
Definition | A bare board with copper traces | A fully assembled and functional electronic circuit |
Components | None | Electronic components soldered onto the PCB |
Manufacturing Process | Design, printing, etching, drilling, plating, solder mask, silkscreen, testing | Solder paste application, component placement, reflow soldering, inspection, testing |
Applications | Foundation for electronic circuits | Ready-to-use electronic assemblies |
Cost | Lower | Higher |
Complexity | Can be simple or complex | Typically more complex due to the addition of components |
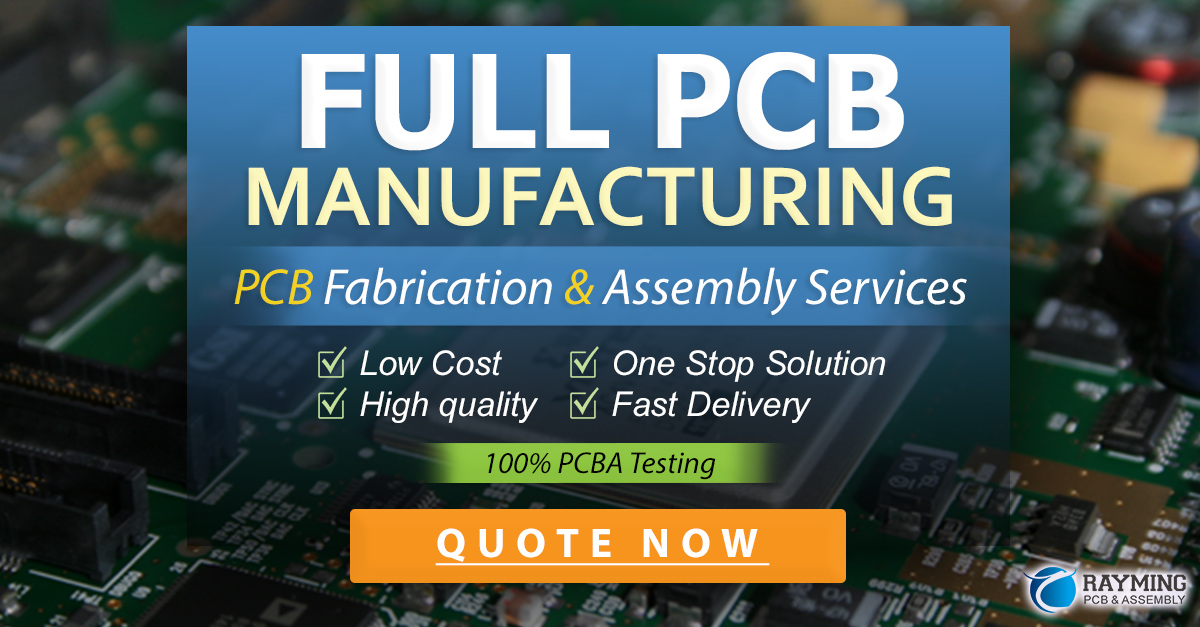
Applications of PCAs and PCBs
PCAs and PCBs are used in a wide range of electronic devices and systems, including:
- Consumer electronics (smartphones, laptops, televisions, etc.)
- Industrial equipment (sensors, controllers, automation systems, etc.)
- Medical devices (monitoring equipment, diagnostic tools, implantable devices, etc.)
- Automotive electronics (engine control units, infotainment systems, safety systems, etc.)
- Aerospace and defense systems (avionics, communication systems, radar, etc.)
- IoT devices (smart home devices, wearables, remote sensors, etc.)
The choice between using a PCB or a PCA in a particular application depends on several factors, such as the complexity of the circuit, the production volume, the available space, and the cost constraints.
Future Trends in PCA and PCB Technology
As electronic devices continue to become smaller, more powerful, and more complex, PCA and PCB technology is evolving to keep pace. Some of the key trends in PCA and PCB technology include:
-
Miniaturization: PCBs and PCAs are becoming smaller and more dense, with features sizes down to a few microns. This allows for more complex circuits to be packed into smaller spaces, enabling the development of smaller and more powerful electronic devices.
-
High-Speed Design: As electronic systems operate at higher and higher frequencies, PCB and PCA design must adapt to minimize signal integrity issues and electromagnetic interference (EMI). This involves the use of advanced materials, such as low-loss dielectrics and high-speed laminates, as well as specialized design techniques, such as controlled impedance routing and differential pair routing.
-
3D Printing: 3D printing technology is being applied to PCB and PCA manufacturing, allowing for the creation of complex, three-dimensional circuit structures. This enables the development of more compact and efficient electronic devices, as well as the integration of electronics into non-traditional form factors, such as clothing and medical implants.
-
Sustainable Materials: There is a growing trend towards the use of sustainable and eco-friendly materials in PCB and PCA manufacturing, such as biodegradable substrates and lead-free solders. This is driven by concerns over electronic waste and the environmental impact of electronics manufacturing.
-
Industry 4.0: The integration of advanced technologies, such as the Internet of Things (IoT), artificial intelligence (AI), and big data analytics, is transforming the PCB and PCA manufacturing industry. This includes the use of smart factories, automated quality control, and predictive maintenance, which can improve efficiency, reduce costs, and enhance product quality.
Frequently Asked Questions (FAQ)
- What is the main difference between a PCA and a PCB?
-
A PCB is a bare board with copper traces, while a PCA is a fully assembled and functional electronic circuit with components soldered onto the PCB.
-
Can a PCB function without components?
-
No, a PCB is just the foundation for an electronic circuit. It needs components to be soldered onto it to function as a complete circuit.
-
What are the advantages of using a PCA over a PCB?
-
PCAs are ready-to-use electronic assemblies that can be easily integrated into a device or system. They save time and effort compared to assembling components onto a PCB manually.
-
What are some common applications of PCAs and PCBs?
-
PCAs and PCBs are used in a wide range of electronic devices and systems, including consumer electronics, industrial equipment, medical devices, automotive electronics, aerospace and defense systems, and IoT devices.
-
What are some future trends in PCA and PCB technology?
- Some key trends in PCA and PCB technology include miniaturization, high-speed design, 3D printing, sustainable materials, and the integration of advanced technologies such as IoT, AI, and big data analytics.
Conclusion
In conclusion, while PCAs and PCBs may sound similar, they are distinct entities with different characteristics and applications. PCBs are the bare boards that form the foundation of electronic circuits, while PCAs are fully assembled and functional circuits ready for use in electronic devices.
Understanding the differences between PCAs and PCBs is essential for anyone involved in electronics design, manufacturing, or procurement. By knowing the capabilities and limitations of each, you can make informed decisions about which one to use in a particular application, and how to optimize their design and manufacturing for the best performance and cost-effectiveness.
As electronic devices continue to evolve and become more complex, PCA and PCB technology will play an increasingly critical role in enabling the development of smaller, faster, and more powerful systems. By staying up-to-date with the latest trends and innovations in this field, you can position yourself and your organization for success in the rapidly changing world of electronics.
No responses yet