What is a Countersink?
A countersink is a conical recess created at the top of a drilled hole in a PCB. The primary purpose of a countersink is to allow the head of a fastener, such as a screw, to sit flush with or below the surface of the board. This is particularly important in applications where a smooth, even surface is required, such as in the case of a PCB that will be subjected to high-speed airflow or where a low-profile design is necessary.
Countersinks are typically created using a specialized drill bit called a countersink bit, which features a conical cutting edge that matches the desired angle of the recess. The most common angles for countersinks are 60°, 82°, 90°, and 100°, with 82° being the most widely used in PCB manufacturing.
Advantages of Countersinking
- Allows for flush-mounted fasteners, reducing the overall height of the assembled PCB
- Provides a smooth, aerodynamic surface for improved airflow and reduced turbulence
- Enhances the aesthetic appearance of the PCB by concealing fastener heads
- Prevents fastener heads from interfering with other components or connectors on the board
Disadvantages of Countersinking
- Reduces the thickness of the PCB-Material-in-your-electronic-project/”>PCB material around the hole, potentially weakening the board’s structural integrity
- May cause delamination of the PCB Layers if not performed carefully
- Requires additional processing time and specialized equipment, increasing manufacturing costs
What is a Counterbore?
A counterbore is a cylindrical recess created at the top of a drilled hole in a PCB, with a diameter larger than the hole itself. The primary purpose of a counterbore is to create a pocket for the head of a fastener or to accommodate a component that requires a specific mounting depth.
Counterbores are typically created using a specialized drill bit called a counterbore bit, which features a pilot tip to guide the bit through the pre-drilled hole and a larger cutting edge to create the cylindrical recess. The depth of the counterbore is carefully controlled to ensure that the fastener head or component is seated at the correct level within the PCB.
Advantages of Counterboring
- Allows for precise control over the mounting depth of fasteners or components
- Provides a secure, stable seating for fastener heads or component leads
- Reduces stress on the PCB material by distributing the load over a larger area
- Enables the use of larger fastener heads or components without increasing the overall height of the assembled PCB
Disadvantages of Counterboring
- Requires additional processing time and specialized equipment, increasing manufacturing costs
- May weaken the PCB’s structural integrity if the counterbore depth is too great relative to the board thickness
- Can create challenges for automated assembly processes, as the counterbores must be precisely aligned with the pre-drilled holes
Comparing Countersinks and Counterbores
Characteristic | Countersink | Counterbore |
---|---|---|
Shape | Conical | Cylindrical |
Purpose | Allow fastener heads to sit flush or below the PCB surface | Create a pocket for fastener heads or components |
Drill Bit Type | Countersink bit with conical cutting edge | Counterbore bit with pilot tip and larger cutting edge |
Common Angles | 60°, 82°, 90°, 100° | Not applicable |
Depth Control | Determined by the angle and depth of the countersink | Precisely controlled to accommodate specific fastener heads or components |
Effect on PCB Strength | Reduces material thickness around the hole, potentially weakening the board | Distributes load over a larger area, reducing stress on the PCB material |
Manufacturing Cost | Increases due to additional processing time and specialized equipment | Increases due to additional processing time and specialized equipment |
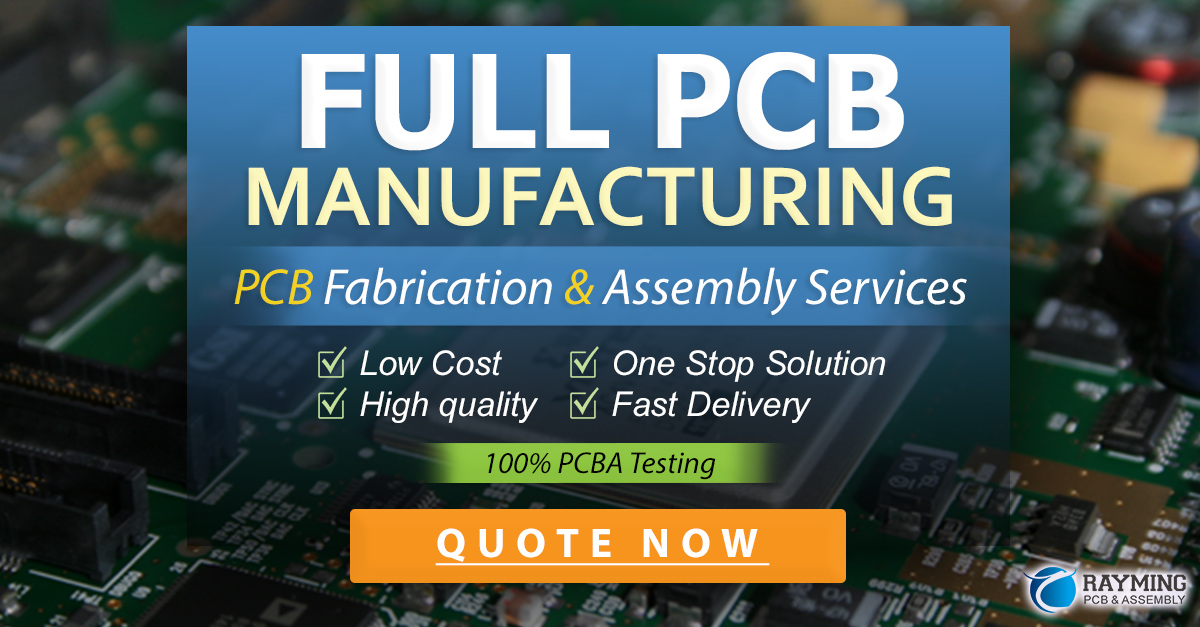
Applications of Countersinks and Counterbores in PCBs
Countersinks and counterbores are used in various aspects of PCB design and assembly, depending on the specific requirements of the application. Some common applications include:
Countersink Applications
- Mounting PCBs to enclosures or chassis using flush-mounted screws
- Creating a smooth surface for improved airflow in high-speed applications, such as in aerospace or automotive electronics
- Enhancing the aesthetic appearance of consumer electronics by concealing fastener heads
- Ensuring a low-profile design for space-constrained applications, such as in wearable devices or smartphones
Counterbore Applications
- Accommodating components with specific mounting depth requirements, such as connectors or switches
- Providing a secure, stable seating for fastener heads in applications subjected to vibration or mechanical stress
- Allowing for the use of larger fastener heads or components without increasing the overall height of the assembled PCB
- Creating recesses for component leads or pins to ensure proper alignment and prevent damage during assembly
Design Considerations for Countersinks and Counterbores
When incorporating countersinks or counterbores into a PCB design, several factors must be considered to ensure the optimal performance and reliability of the final product.
Material Thickness
The thickness of the PCB material must be sufficient to accommodate the depth of the countersink or counterbore without compromising the board’s structural integrity. As a general rule, the depth of the countersink or counterbore should not exceed 40-50% of the total board thickness.
Hole Diameter
The diameter of the drilled hole must be carefully selected to ensure a proper fit for the fastener or component lead. In the case of countersinks, the hole diameter should be slightly larger than the fastener shank to allow for easy insertion and removal. For counterbores, the hole diameter should match the diameter of the component lead or pin.
Recess Depth
The depth of the countersink or counterbore must be precisely controlled to ensure that the fastener head or component is seated at the correct level within the PCB. Insufficient depth may result in a protruding fastener head or component, while excessive depth may weaken the board’s structural integrity.
Alignment
Proper alignment of the countersink or counterbore with the pre-drilled hole is critical for ensuring a secure, stable connection. Misalignment can lead to difficulties in assembly, reduced mechanical strength, and potential damage to the PCB or components.
Manufacturing Processes
The choice of manufacturing processes for creating countersinks and counterbores will depend on factors such as the PCB material, the required precision, and the production volume. Common methods include drilling with specialized bits, milling, and laser cutting. Each method has its own advantages and limitations in terms of cost, speed, and accuracy.
FAQ
-
Can countersinks and counterbores be used together in the same PCB?
Yes, countersinks and counterbores can be used together in the same PCB, depending on the specific requirements of the application. For example, a PCB may have countersunk holes for mounting screws and counterbored holes for accommodating component leads. -
How do I select the appropriate angle for a countersink in a PCB?
The choice of countersink angle depends on the type of fastener being used and the desired appearance of the assembled PCB. The most common angles are 60°, 82°, 90°, and 100°, with 82° being the most widely used in PCB manufacturing. Consult with your fastener supplier or PCB manufacturer to determine the best angle for your specific application. -
Are there any special considerations for using countersinks or counterbores in multi-layer PCBs?
Yes, when using countersinks or counterbores in multi-layer PCBs, it is essential to ensure that the depth of the recess does not expose or damage any internal layers. The design must also account for the potential impact on signal integrity and impedance control, as the removal of material may affect the electrical properties of the board. -
Can countersinks and counterbores be created in PCBs with surface finishes such as ENIG or HASL?
Yes, countersinks and counterbores can be created in PCBs with various surface finishes, including Electroless Nickel Immersion Gold (ENIG) and Hot Air Solder Leveling (HASL). However, the design must take into account the thickness of the surface finish layer to ensure that the final depth of the recess is accurate. -
Are there any automated methods for creating countersinks or counterbores in high-volume PCB production?
Yes, automated methods such as CNC drilling and routing can be used to create countersinks and counterbores in high-volume PCB production. These methods offer improved speed, accuracy, and consistency compared to manual drilling or milling processes. Additionally, specialized equipment such as hydraulic press machines can be used to create large quantities of countersinks or counterbores simultaneously.
Conclusion
Countersinks and counterbores are essential features in PCB design and assembly, serving distinct purposes in creating recesses for fasteners and components. Understanding the differences between these two methods, their applications, and their design considerations is crucial for ensuring the optimal performance and reliability of the final product.
By carefully selecting the appropriate method for each application, controlling the depth and alignment of the recesses, and accounting for the impact on the PCB’s structural integrity and electrical properties, designers and manufacturers can create high-quality, functional PCBs that meet the demands of a wide range of industries and applications.
As PCB technology continues to evolve, the use of countersinks and counterbores will remain an essential aspect of the design and manufacturing process, enabling the development of increasingly complex, compact, and high-performance electronic devices.
No responses yet