What is FR4?
FR4 is a composite material composed of woven fiberglass cloth with an epoxy resin binder. The “FR” stands for “Flame Retardant,” indicating that the material is designed to be resistant to the spread of flames. The “4” denotes the specific grade of the material, which is determined by the type of resin used and the glass transition temperature (Tg) of the material.
FR4 is known for its excellent mechanical, thermal, and electrical properties, making it an ideal choice for PCB substrates. Some of the key properties of FR4 include:
- High strength and stiffness
- Good dimensional stability
- Excellent electrical insulation
- Resistance to moisture absorption
- Flame retardancy
What is Dielectric Rating?
The dielectric rating, also known as the dielectric strength, is a measure of a material’s ability to resist electrical breakdown under an applied electric field. In other words, it is the maximum voltage gradient that a material can withstand before it begins to conduct electricity. The dielectric rating is typically expressed in volts per meter (V/m) or kilovolts per millimeter (kV/mm).
When an electric field is applied to a dielectric material, such as FR4, the electrons within the material become displaced, creating an internal electric field that opposes the applied field. If the applied field is strong enough, it can cause the electrons to break free from their atomic bonds, resulting in electrical conduction and breakdown of the material.
The dielectric rating is an essential property for materials used in electrical insulation applications, as it determines the maximum voltage that can be safely applied to a system without causing failure.
Importance of Dielectric Rating in PCBs
In PCBs, the dielectric rating of the substrate material, such as FR4, plays a crucial role in determining the board’s performance and reliability. Some of the key reasons why the dielectric rating is important in PCBs include:
-
Insulation between conductors: The primary function of the PCB substrate is to provide electrical insulation between the conductive traces on the board. A high dielectric rating ensures that the substrate can withstand the voltage differences between adjacent traces without allowing current to flow between them.
-
High-voltage applications: In applications that involve high voltages, such as power electronics or automotive systems, the PCB substrate must have a high dielectric rating to prevent electrical breakdown and ensure safe operation.
-
Signal integrity: The dielectric rating of the substrate can also affect the signal integrity of the PCB. A low dielectric rating can lead to signal loss, crosstalk, and other issues that can degrade the performance of the circuit.
-
Reliability and longevity: A substrate with a high dielectric rating is less likely to suffer from electrical breakdown over time, which can help extend the lifespan of the PCB and improve its overall reliability.
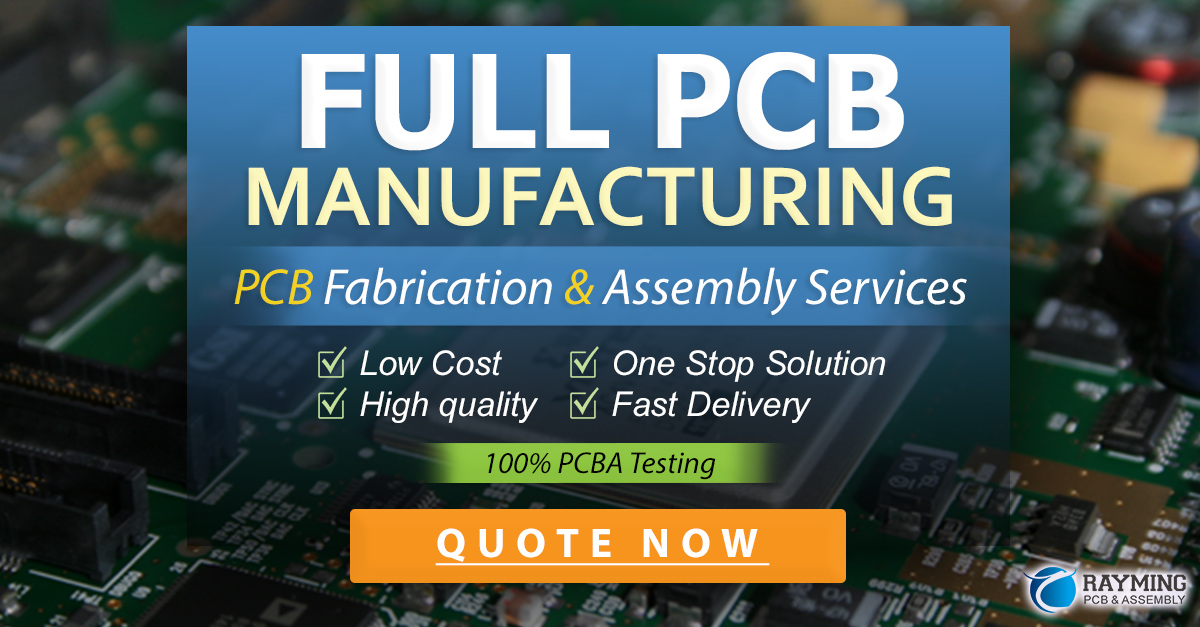
Factors Affecting the Dielectric Rating of FR4
The dielectric rating of FR4 can vary depending on several factors, including:
-
Thickness: The dielectric rating of FR4 is inversely proportional to its thickness. In other words, thinner FR4 laminates will have a higher dielectric rating compared to thicker ones. This is because the electric field strength decreases as the distance between the conductors increases.
-
Resin composition: The type and composition of the epoxy resin used in FR4 can influence its dielectric rating. Some resin formulations are specifically designed to provide enhanced electrical insulation properties.
-
Glass fabric: The type and weave of the fiberglass fabric used in FR4 can also affect its dielectric rating. Tighter weaves and higher glass content can improve the material’s insulation properties.
-
Environmental factors: The dielectric rating of FR4 can be affected by environmental factors such as temperature, humidity, and altitude. Higher temperatures and humidity levels can degrade the material’s insulation properties, while higher altitudes can increase the risk of electrical discharge.
-
Frequency: The dielectric rating of FR4 can also vary with the frequency of the applied electric field. At higher frequencies, the dielectric losses in the material can increase, leading to a reduction in its effective dielectric rating.
Typical Dielectric Rating Values for FR4
The dielectric rating of FR4 can vary depending on the specific grade and manufacturer of the material. However, some typical values for the dielectric rating of FR4 are:
Thickness (mm) | Dielectric Rating (kV/mm) |
---|---|
0.8 | 20-30 |
1.6 | 15-20 |
2.4 | 10-15 |
3.2 | 8-12 |
It’s important to note that these values are approximate and can vary depending on the specific test conditions and standards used. When selecting an FR4 laminate for a particular application, it’s crucial to consult the manufacturer’s data sheets and specifications to ensure that the material meets the required dielectric rating and other performance criteria.
Testing and Certification of FR4 Dielectric Rating
To ensure that FR4 laminates meet the required dielectric rating and other performance specifications, they are subjected to various testing and certification procedures. Some of the common standards and tests used to evaluate the dielectric properties of FR4 include:
-
ASTM D149: This standard test method covers the determination of the Dielectric breakdown voltage and dielectric strength of solid electrical insulating materials at commercial power frequencies.
-
IPC-TM-650 2.5.6.1: This test method, developed by the Association Connecting Electronics Industries (IPC), covers the measurement of the dielectric breakdown voltage and dielectric strength of thin printed wiring board materials.
-
UL 746E: This standard, developed by Underwriters Laboratories (UL), covers the evaluation of printed wiring boards for electrical and flammability properties.
These tests typically involve applying a high voltage across a sample of the FR4 material and measuring the voltage at which electrical breakdown occurs. The results are then used to calculate the dielectric rating of the material in kV/mm.
In addition to these tests, FR4 laminates may also be certified to meet specific industry standards, such as:
- IPC-4101: Specification for Base Materials for Rigid and Multilayer Printed Boards
- MIL-I-24768: Insulating Materials, Plastic, Laminated, Copper-Clad (For Printed Wiring Boards)
- NEMA LI 1: Industrial Laminated Thermosetting Products
These standards provide detailed requirements for the physical, mechanical, and electrical properties of FR4 laminates, including their dielectric rating.
Designing with FR4: Considerations for Dielectric Rating
When designing PCBs using FR4 substrates, there are several considerations related to the dielectric rating that designers should keep in mind:
-
Voltage and spacing requirements: The maximum voltage between conductors on the PCB should not exceed the dielectric rating of the FR4 material, taking into account the thickness of the substrate. Designers should also ensure that there is sufficient spacing between conductors to prevent electrical breakdown.
-
Layer stack-up: In multi-layer PCBs, the arrangement of the layers can affect the overall dielectric performance of the board. Designers should consider the thickness and dielectric rating of each layer, as well as the spacing between layers, to ensure that the board can withstand the required voltages.
-
Material selection: When selecting an FR4 laminate for a particular design, designers should consider the specific requirements for dielectric rating, as well as other factors such as the operating temperature range, humidity exposure, and mechanical stress.
-
Safety factors: To ensure a robust and reliable design, it’s often necessary to apply safety factors when working with the dielectric rating of FR4. This means designing the PCB to withstand voltages significantly higher than the expected operating voltages, to account for variations in material properties and environmental conditions.
-
Simulation and testing: Before finalizing a PCB design, it’s often useful to perform simulations and tests to verify the dielectric performance of the board. This can include finite element analysis (FEA) to model the electric fields and potential breakdown regions, as well as physical testing of prototype boards to validate the design.
By considering these factors and working closely with material suppliers and PCB manufacturers, designers can ensure that their PCBs using FR4 substrates will meet the required dielectric rating and provide reliable performance in the intended application.
Alternatives to FR4 for High-Voltage Applications
While FR4 is a popular choice for many PCB applications, there are some cases where its dielectric rating may not be sufficient, particularly in high-voltage or harsh environmental conditions. In these situations, designers may need to consider alternative materials with higher dielectric ratings. Some common alternatives to FR4 include:
-
Polyimide: Polyimide laminates, such as Kapton, offer excellent thermal stability and a higher dielectric rating compared to FR4. They are often used in high-temperature and high-voltage applications, such as aerospace and automotive electronics.
-
PTFE: Polytetrafluoroethylene (PTFE) laminates, also known as Teflon, have a very high dielectric rating and low dielectric loss, making them suitable for high-frequency and high-voltage applications. However, they are more expensive and harder to process compared to FR4.
-
Ceramic: Ceramic substrates, such as alumina or beryllium oxide, have very high dielectric ratings and excellent thermal conductivity. They are often used in high-power and high-frequency applications, such as RF and microwave circuits.
-
High-Tg FR4: Some manufacturers offer FR4 laminates with enhanced properties, such as higher glass transition temperatures (Tg) and improved dielectric ratings. These materials, often referred to as “high-performance” or “high-speed” FR4, can provide a cost-effective alternative to more expensive substrates in some applications.
When selecting an alternative material for high-voltage applications, designers should carefully consider the specific requirements of the application, including the operating voltage, temperature range, and environmental conditions. They should also work closely with material suppliers and PCB manufacturers to ensure that the chosen material is compatible with the manufacturing process and can meet the required performance and reliability standards.
FAQ
-
What is the typical dielectric rating of FR4?
The dielectric rating of FR4 can vary depending on the thickness of the material, but typical values range from 20-30 kV/mm for 0.8 mm thickness to 8-12 kV/mm for 3.2 mm thickness. -
Can FR4 be used for high-voltage applications?
FR4 can be used for some high-voltage applications, but its suitability depends on the specific voltage requirements and environmental conditions. For very high-voltage applications, alternative materials with higher dielectric ratings, such as polyimide or PTFE, may be necessary. -
How does the thickness of FR4 affect its dielectric rating?
The dielectric rating of FR4 is inversely proportional to its thickness. Thinner FR4 laminates will have a higher dielectric rating compared to thicker ones, because the electric field strength decreases as the distance between conductors increases. -
What factors can affect the dielectric rating of FR4?
The dielectric rating of FR4 can be affected by several factors, including the resin composition, glass fabric, environmental conditions (such as temperature and humidity), and the frequency of the applied electric field. -
How is the dielectric rating of FR4 tested and certified?
The dielectric rating of FR4 is typically tested according to industry standards such as ASTM D149, IPC-TM-650 2.5.6.1, and UL 746E. These tests involve applying a high voltage across a sample of the material and measuring the breakdown voltage. FR4 laminates can also be certified to meet specific industry standards, such as IPC-4101 and MIL-I-24768, which provide detailed requirements for their electrical and physical properties.
Conclusion
The dielectric rating is a critical property of FR4 that determines its ability to insulate and withstand electric fields. It is an essential consideration in the design and manufacturing of PCBs, particularly for high-voltage applications. The dielectric rating of FR4 can vary depending on factors such as thickness, resin composition, and environmental conditions, and is typically tested and certified according to industry standards.
When designing PCBs using FR4 substrates, it’s important to consider the specific voltage and spacing requirements, layer stack-up, material selection, and safety factors to ensure that the board can meet the required dielectric rating and provide reliable performance. In some cases, alternative materials with higher dielectric ratings, such as polyimide or PTFE, may be necessary for very high-voltage applications.
By understanding the dielectric rating of FR4 and its implications for PCB design and manufacturing, engineers and designers can make informed decisions and create products that meet the required performance and reliability standards.
No responses yet