Introduction
Rogers FR4 is a widely used printed circuit board (PCB) material known for its excellent mechanical and electrical properties. One of the key characteristics of Rogers FR4 is its Dielectric constant, which plays a crucial role in determining the material’s performance in high-frequency applications. In this article, we will delve into the dielectric constant of Rogers FR4, its significance, and how it compares to other PCB materials.
Understanding Dielectric Constant
Definition of Dielectric Constant
The dielectric constant, also known as relative permittivity (εr), is a dimensionless quantity that measures a material’s ability to store electrical energy in an electric field. It represents the ratio of the material’s permittivity (ε) to the permittivity of free space (ε0):
εr = ε / ε0
A higher dielectric constant indicates that a material has a greater capacity to store electrical energy, while a lower dielectric constant implies a reduced ability to store energy.
Importance of Dielectric Constant in PCB Design
The dielectric constant is a critical parameter in PCB design, particularly for high-frequency applications such as radio frequency (RF) and microwave circuits. The dielectric constant affects several aspects of PCB performance:
-
Signal propagation speed: The dielectric constant influences the speed at which signals propagate through the PCB. A higher dielectric constant results in slower signal propagation, while a lower dielectric constant allows for faster signal transmission.
-
Characteristic impedance: The characteristic impedance of a transmission line on a PCB is determined by the dielectric constant of the substrate material. Maintaining a consistent characteristic impedance is essential for preventing signal reflections and ensuring proper impedance matching.
-
Crosstalk: The dielectric constant affects the coupling between adjacent traces on a PCB. A higher dielectric constant can lead to increased crosstalk, which can cause signal integrity issues and degrade the overall performance of the circuit.
-
Wavelength: The wavelength of a signal propagating through a PCB is inversely proportional to the square root of the dielectric constant. A higher dielectric constant results in a shorter wavelength, which can impact the design of RF and microwave circuits.
Dielectric Constant of Rogers FR4
Typical Values
Rogers FR4 is a composite material consisting of a woven fiberglass fabric impregnated with an epoxy resin. The dielectric constant of Rogers FR4 can vary depending on the specific formulation and the frequency of operation. Typical values for the dielectric constant of Rogers FR4 are:
Frequency | Dielectric Constant (εr) |
---|---|
1 MHz | 4.34 |
10 MHz | 4.34 |
100 MHz | 4.34 |
1 GHz | 4.34 |
10 GHz | 4.28 |
As evident from the table, the dielectric constant of Rogers FR4 remains relatively stable across a wide frequency range, with only a slight decrease at higher frequencies (e.g., 10 GHz).
Factors Affecting Dielectric Constant
Several factors can influence the dielectric constant of Rogers FR4:
-
Resin content: The ratio of epoxy resin to fiberglass in the composite material can affect the dielectric constant. A higher resin content typically results in a slightly higher dielectric constant.
-
Moisture absorption: Rogers FR4 can absorb moisture from the environment, which can lead to an increase in the dielectric constant. Proper storage and handling of the material are essential to minimize moisture absorption.
-
Temperature: The dielectric constant of Rogers FR4 exhibits a slight temperature dependence. As the temperature increases, the dielectric constant tends to decrease slightly.
-
Frequency: As mentioned earlier, the dielectric constant of Rogers FR4 remains relatively stable across a wide frequency range, with a slight decrease at higher frequencies.
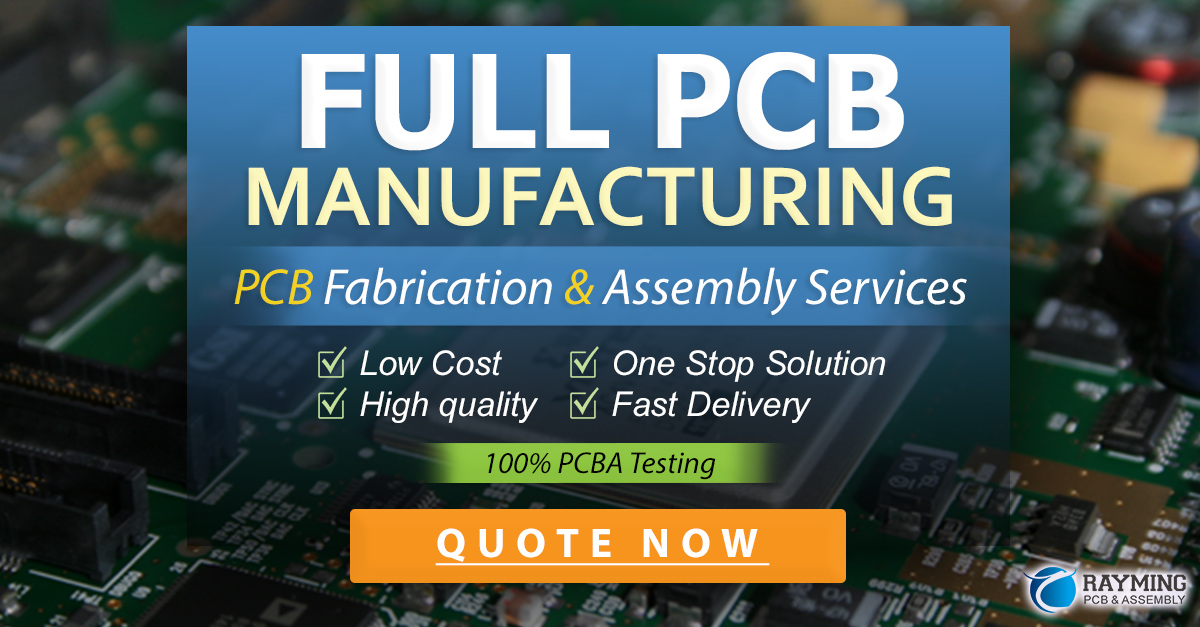
Comparison with Other PCB Materials
To better understand the dielectric constant of Rogers FR4, it is helpful to compare it with other commonly used PCB materials:
FR-4
Standard FR-4 is the most widely used PCB material and serves as a benchmark for comparison. The typical dielectric constant of FR-4 is around 4.5 at 1 MHz, slightly higher than that of Rogers FR4. FR-4 is suitable for general-purpose applications but may not be ideal for high-frequency designs due to its higher dielectric constant and higher loss tangent.
Rogers RO4000 Series
The Rogers RO4000 series is a family of high-performance PCB materials designed for RF and microwave applications. These materials have lower dielectric constants compared to Rogers FR4, typically ranging from 3.3 to 3.7. The lower dielectric constant allows for faster signal propagation and improved high-frequency performance.
PTFE (Polytetrafluoroethylene)
PTFE, also known as Teflon, is a popular PCB material for high-frequency applications due to its low dielectric constant. The dielectric constant of PTFE is approximately 2.1, significantly lower than that of Rogers FR4. PTFE-based materials offer excellent high-frequency performance but are more expensive and challenging to process compared to Rogers FR4.
Applications of Rogers FR4
Rogers FR4 finds applications in various industries and domains:
-
Consumer electronics: Rogers FR4 is commonly used in the manufacturing of PCBs for consumer electronic devices, such as smartphones, laptops, and tablets.
-
Automotive: The automotive industry utilizes Rogers FR4 for PCBs in vehicle electronic systems, including infotainment, navigation, and advanced driver assistance systems (ADAS).
-
Industrial: Rogers FR4 is employed in industrial applications, such as process control, automation, and instrumentation.
-
Medical: Medical devices and equipment often rely on Rogers FR4 for their PCBs due to its reliability and cost-effectiveness.
-
Telecommunications: While Rogers FR4 may not be the optimal choice for high-frequency telecommunications applications, it is still used in some lower-frequency communication systems.
Frequently Asked Questions (FAQ)
1. What is the difference between dielectric constant and dielectric strength?
Dielectric constant and dielectric strength are two different properties of a material. The dielectric constant measures a material’s ability to store electrical energy in an electric field, while dielectric strength refers to the maximum electric field a material can withstand before breaking down and becoming conductive.
2. Can the dielectric constant of Rogers FR4 change over time?
Yes, the dielectric constant of Rogers FR4 can change over time due to factors such as moisture absorption and aging. Proper storage and handling of the material can help minimize these changes.
3. Is Rogers FR4 suitable for high-frequency applications?
Rogers FR4 can be used for some high-frequency applications, but it may not be the optimal choice for very high frequencies or applications that require the lowest possible dielectric constant. Materials like Rogers RO4000 series or PTFE may be more suitable for such applications.
4. How does the dielectric constant of Rogers FR4 compare to that of standard FR-4?
The dielectric constant of Rogers FR4 is slightly lower than that of standard FR-4. Typical values for Rogers FR4 range from 4.28 to 4.34, while standard FR-4 has a dielectric constant around 4.5 at 1 MHz.
5. Can the dielectric constant of Rogers FR4 be customized?
To some extent, the dielectric constant of Rogers FR4 can be customized by adjusting the ratio of epoxy resin to fiberglass in the composite material. However, significant customization may require a specialized formulation and may not be readily available from suppliers.
Conclusion
The dielectric constant of Rogers FR4 is a crucial parameter that influences the material’s performance in PCB applications. With a typical dielectric constant ranging from 4.28 to 4.34, Rogers FR4 offers a balance between cost, reliability, and performance. While it may not be the optimal choice for the most demanding high-frequency applications, Rogers FR4 remains a popular and versatile PCB material for a wide range of industries and applications.
Understanding the dielectric constant of Rogers FR4, its influencing factors, and how it compares to other PCB materials is essential for designers and engineers to make informed decisions when selecting materials for their projects. By considering the specific requirements of the application, such as frequency range, signal integrity, and cost, designers can choose the most suitable PCB material, whether it be Rogers FR4 or an alternative like Rogers RO4000 series or PTFE.
As technology advances and new applications emerge, the demand for high-performance PCB materials will continue to grow. While Rogers FR4 has been a reliable choice for many years, ongoing research and development efforts aim to create new materials with even better dielectric properties, thermal stability, and processing characteristics. These advancements will enable the design of more compact, efficient, and reliable electronic devices across various industries.
In summary, the dielectric constant of Rogers FR4 is a fundamental property that plays a significant role in PCB design and performance. By understanding its value, influencing factors, and comparing it with other materials, designers can make informed choices and optimize their PCB layouts for specific applications. As the electronics industry continues to evolve, the importance of dielectric constant and other material properties will remain at the forefront of PCB design and innovation.
No responses yet