Dielectric constant Definition
The dielectric constant, also known as relative permittivity (εr), is a dimensionless value that indicates how easily a material can become polarized and store electrical energy when subjected to an electric field, relative to the permittivity of free space (ε0). It is an essential parameter in PCB design as it affects signal propagation speed, impedance, and other characteristics.
The dielectric constant can be expressed as:
εr = ε / ε0
Where:
– εr is the relative permittivity or dielectric constant
– ε is the permittivity of the material
– ε0 is the permittivity of free space (8.854 × 10⁻¹² F/m)
Rogers 5880 Properties and Applications
Rogers 5880 is a glass microfiber reinforced PTFE (polytetrafluoroethylene) composite high frequency laminate with the following key properties:
- Low dielectric constant (εr = 2.20 at 10 GHz)
- Low dissipation factor (tan δ = 0.0009 at 10 GHz)
- Excellent thermal stability
- Low moisture absorption
- Tight dielectric constant and thickness control
- Excellent dimensional stability
These properties make Rogers 5880 well-suited for various RF and microwave applications, including:
- Wireless communication systems
- Radar and sensing
- Satellite and space
- Military and defense
- Automotive radar
- High-speed digital
Dielectric Constant of Rogers 5880
The dielectric constant of Rogers 5880 is one of its most critical properties. At 10 GHz, Rogers 5880 has a dielectric constant of 2.20, which is relatively low compared to many other PCB materials. This low dielectric constant provides several benefits, such as:
-
Faster signal propagation: A lower dielectric constant allows signals to travel more quickly through the substrate, reducing signal delay and enabling higher operating frequencies.
-
Reduced signal loss: Materials with lower dielectric constants generally have lower dissipation factors (tan δ), which means less energy is lost as heat when signals pass through the substrate.
-
Improved impedance control: The dielectric constant directly affects the characteristic impedance of transmission lines on the PCB. A lower and more stable dielectric constant makes it easier to achieve consistent impedance matching, minimizing signal reflections and distortions.
-
Thinner substrates: For a given characteristic impedance, a lower dielectric constant allows for thinner substrates, which can be advantageous in space-constrained designs or for reducing overall PCB thickness.
Dielectric Constant vs. Frequency
It is important to note that the dielectric constant of Rogers 5880, like most materials, is not constant across all frequencies. The dielectric constant tends to decrease slightly as frequency increases. Table 1 shows the dielectric constant of Rogers 5880 at various frequencies.
Frequency (GHz) | Dielectric Constant (εr) |
---|---|
1 | 2.20 |
5 | 2.20 |
10 | 2.20 |
20 | 2.20 |
30 | 2.19 |
40 | 2.19 |
50 | 2.18 |
60 | 2.18 |
As evident from the table, the dielectric constant of Rogers 5880 remains relatively stable across a wide frequency range, with only a slight decrease at higher frequencies. This stability is crucial for maintaining consistent performance in broadband applications.
Dielectric Constant vs. Temperature
The dielectric constant of Rogers 5880 also exhibits excellent stability over a wide temperature range. Table 2 shows the dielectric constant of Rogers 5880 at different temperatures, measured at 10 GHz.
Temperature (°C) | Dielectric Constant (εr) |
---|---|
-50 | 2.20 |
-25 | 2.20 |
0 | 2.20 |
25 | 2.20 |
50 | 2.20 |
75 | 2.20 |
100 | 2.20 |
125 | 2.20 |
150 | 2.20 |
The stable dielectric constant across a wide temperature range is advantageous for applications exposed to varying environmental conditions, ensuring consistent performance and reliability.
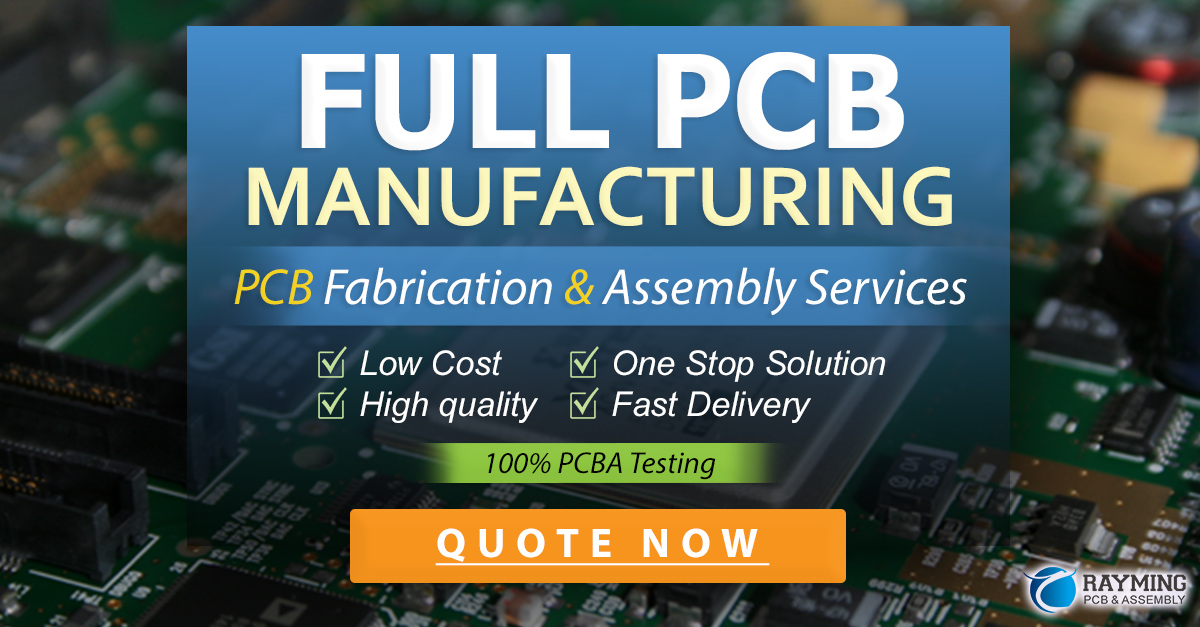
Impact of Dielectric Constant on PCB Design
The dielectric constant of the substrate material significantly impacts various aspects of PCB design, particularly in high-frequency applications. Some of the key considerations include:
Transmission Line Design
In high-frequency PCBs, signals are typically transmitted using controlled impedance transmission lines, such as microstrip or stripline. The characteristic impedance (Z0) of these transmission lines depends on the dielectric constant of the substrate, along with other factors like conductor width, substrate thickness, and trace thickness.
For a microstrip transmission line, the characteristic impedance can be approximated using the following equation:
Z0 = (87 / √(εr + 1.41)) × ln(5.98h / (0.8w + t))
Where:
– Z0 is the characteristic impedance (Ω)
– εr is the dielectric constant of the substrate
– h is the substrate thickness (mm)
– w is the conductor width (mm)
– t is the conductor thickness (mm)
A lower dielectric constant, like that of Rogers 5880, allows for wider trace widths for a given characteristic impedance and substrate thickness. This can be beneficial for reducing conductor losses and improving power handling capacity.
Signal Velocity and Propagation Delay
The dielectric constant also affects the velocity at which signals propagate through the substrate. The signal velocity (v) in a dielectric material is given by:
v = c / √εr
Where:
– v is the signal velocity (m/s)
– c is the speed of light in vacuum (≈ 3 × 10⁸ m/s)
– εr is the dielectric constant of the substrate
A lower dielectric constant results in a higher signal velocity, which means signals travel faster through the substrate. This is particularly important for high-speed digital designs, where reduced propagation delays can enable higher clock frequencies and improved timing margins.
The propagation delay (tp) for a given trace length (l) can be calculated as:
tp = l / v
Wavelength and Circuit Dimensions
The wavelength (λ) of a signal in a dielectric material is related to the signal frequency (f) and the dielectric constant of the substrate:
λ = v / f = c / (f × √εr)
At higher frequencies, the wavelength becomes smaller. This has implications for circuit dimensions, as features like trace lengths, stub lengths, and component spacing often need to be a fraction of the wavelength to maintain proper circuit behavior.
A lower dielectric constant, like that of Rogers 5880, results in longer wavelengths for a given frequency. This can provide more flexibility in circuit layout and make it easier to maintain proper dimensions relative to the wavelength.
FAQ
1. What is the dissipation factor (tan δ) of Rogers 5880, and how does it relate to the dielectric constant?
The dissipation factor (tan δ) is a measure of the energy loss in a dielectric material. For Rogers 5880, the dissipation factor is 0.0009 at 10 GHz, which is very low. A low dissipation factor indicates minimal energy loss and is often associated with materials having a low dielectric constant, like Rogers 5880. The low dielectric constant and dissipation factor make Rogers 5880 an excellent choice for low-loss, high-frequency applications.
2. How does the dielectric constant of Rogers 5880 compare to other common PCB substrates?
Rogers 5880 has one of the lowest dielectric constants among high-frequency PCB substrates. For comparison, FR-4, a common PCB material for lower frequencies, has a dielectric constant of about 4.5 at 1 MHz. Other high-frequency laminates, like Rogers 4003C and Rogers 4350B, have dielectric constants of 3.38 and 3.48 at 10 GHz, respectively. The lower dielectric constant of Rogers 5880 makes it a superior choice for many high-frequency applications.
3. Can the dielectric constant of Rogers 5880 be affected by moisture absorption?
Rogers 5880 has very low moisture absorption, typically less than 0.1% by weight. This low moisture absorption helps maintain a stable dielectric constant even in humid environments. In contrast, some other PCB materials, particularly those with higher dielectric constants, can be more sensitive to moisture absorption, which can cause changes in their dielectric constant and affect circuit performance.
4. How does the dielectric constant influence the choice of PCB thickness for a given characteristic impedance?
For a given characteristic impedance, a lower dielectric constant allows for a thinner PCB substrate. This is because the characteristic impedance of a transmission line is proportional to the square root of the dielectric constant. With Rogers 5880’s low dielectric constant of 2.20, designers can use thinner substrates while still achieving the desired characteristic impedance, which can be advantageous in applications where size and weight are critical factors.
5. What are some design considerations when using Rogers 5880 in high-frequency PCBs?
When designing high-frequency PCBs with Rogers 5880, some key considerations include:
-
Controlled impedance transmission lines: Ensure that the transmission line geometries (trace width, substrate thickness, etc.) are properly designed to achieve the desired characteristic impedance.
-
Circuit dimensions: Pay attention to the wavelength of the signals in the substrate and ensure that critical circuit dimensions, such as trace lengths and component spacing, are appropriately sized relative to the wavelength.
-
Grounding and shielding: Implement proper grounding and shielding techniques to minimize electromagnetic interference (EMI) and ensure signal integrity.
-
Thermal management: Although Rogers 5880 has excellent thermal stability, high-frequency circuits can still generate significant heat. Ensure adequate thermal management through proper heat sinking and airflow.
-
Manufacturing considerations: Work closely with your PCB manufacturer to ensure they have experience working with Rogers 5880 and can meet the necessary tolerances and design requirements for your high-frequency application.
By carefully considering these factors and leveraging the excellent properties of Rogers 5880, designers can create high-performance, reliable PCBs for demanding high-frequency applications.
No responses yet