Chemical Formula and Structure of PTFE
The chemical formula for PTFE is (C2F4)n, where n represents the number of monomer units that make up the polymer chain. Each monomer unit consists of two carbon atoms bonded to four fluorine atoms.
The structural formula of the PTFE monomer is:
F F
\ /
C-C
/ \
F F
The carbon-carbon and carbon-fluorine bonds in PTFE are extremely strong, contributing to the material’s exceptional stability and resistance to chemical attack. The fluorine atoms form a protective sheath around the carbon backbone, making it virtually inert to most chemicals.
Physical Properties of PTFE
PTFE exhibits several unique physical properties due to its chemical composition and structure:
1. High Melting Point
PTFE has one of the highest melting points among thermoplastics, around 327°C (620°F). This high melting point is attributed to the strong carbon-fluorine bonds and the polymer’s crystalline structure.
2. Low Coefficient of Friction
PTFE has one of the lowest coefficients of friction of any solid material. This slippery surface is a result of the tightly packed fluorine atoms, which create a smooth, non-stick surface. The static and dynamic coefficients of friction for PTFE against polished steel are approximately 0.04 and 0.03, respectively.
3. Excellent Dielectric Properties
PTFE is an excellent electrical insulator with a high dielectric strength and low dielectric constant. These properties make it suitable for use in high-frequency electronic applications and as an insulating material in cables and connectors.
Property | Value |
---|---|
Dielectric Constant (1 MHz) | 2.1 |
Dielectric Strength | 60-173 MV/m |
Volume Resistivity | 10^18 ohm·cm |
4. Low Water Absorption
PTFE has a very low water absorption rate, typically less than 0.01% by weight. This hydrophobic nature is due to the fluorine atoms’ ability to repel water molecules, preventing moisture from penetrating the material.
5. Thermal Stability
PTFE maintains its properties over a wide temperature range, from -200°C to 260°C (-328°F to 500°F). It has a low thermal conductivity, making it an effective thermal insulator. Additionally, PTFE does not become brittle at low temperatures, unlike many other polymers.
Manufacturing Process of PTFE
PTFE is produced through the polymerization of tetrafluoroethylene (TFE) monomer. There are two main methods for manufacturing PTFE:
1. Suspension Polymerization
In suspension polymerization, TFE monomer is dispersed in water along with a surfactant and initiator. The mixture is agitated and heated to around 60-100°C, causing the monomer to polymerize into small beads of PTFE. The beads are then separated, washed, and dried.
2. Emulsion Polymerization
Emulsion polymerization involves dispersing the TFE monomer in water with the help of a surfactant. An initiator is added, and the mixture is agitated and heated to around 50-80°C. The resulting PTFE particles are much smaller than those produced by suspension polymerization, typically in the range of 0.1-0.3 μm.
After polymerization, the PTFE can be further processed into various forms, such as granules, fine powder, or dispersions, depending on the intended application.
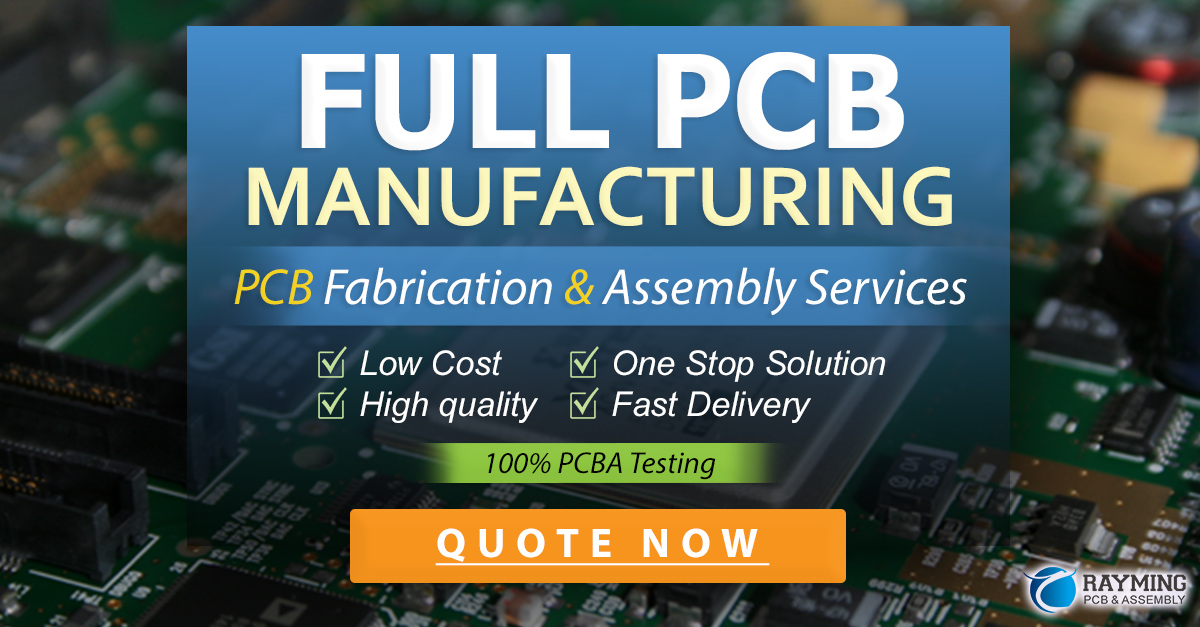
Applications of PTFE
The unique properties of PTFE make it suitable for a wide range of applications across various industries:
1. Non-Stick Coatings
PTFE is famously used as a non-stick coating for cookware, thanks to its low coefficient of friction and excellent heat resistance. It prevents food from sticking to the surface, making cooking and cleaning easier.
2. Seals and Gaskets
PTFE’s chemical inertness and thermal stability make it an ideal material for seals and gaskets in chemical processing, automotive, and aerospace applications. It can withstand harsh chemicals and extreme temperatures without degrading.
3. Electrical Insulation
The excellent dielectric properties of PTFE are utilized in electronic applications, such as insulation for wires and cables, printed circuit boards, and high-frequency components.
4. Medical Devices
PTFE’s biocompatibility and non-reactive nature make it suitable for use in medical devices, such as catheters, vascular grafts, and implantable devices. It minimizes the risk of allergic reactions or infections.
5. Filtration Membranes
PTFE membranes are used in filtration applications, particularly in the chemical, pharmaceutical, and food processing industries. The material’s chemical resistance and non-stick properties help prevent fouling and maintain consistent filtration performance.
FAQ
1. Is PTFE safe for use in cooking?
Yes, PTFE is generally considered safe for use in cooking when used as intended. However, it is important to avoid overheating PTFE-coated cookware, as it can release harmful fumes at temperatures above 260°C (500°F).
2. Can PTFE be recycled?
PTFE is not easily recyclable due to its high melting point and chemical inertness. However, some companies have developed methods to recycle PTFE waste by grinding it into a fine powder and using it as a filler in other materials.
3. Is PTFE resistant to all chemicals?
While PTFE is resistant to most chemicals, it can be affected by some highly reactive substances, such as molten alkali metals, elemental fluorine at high temperatures, and some halogenated compounds.
4. Can PTFE be used in high-temperature applications?
PTFE can be used in applications with temperatures up to 260°C (500°F) continuously. For short periods, it can withstand temperatures up to 300°C (572°F). Above these temperatures, PTFE may start to decompose and release harmful fumes.
5. How does PTFE compare to other fluoropolymers?
PTFE is one of the most well-known and widely used fluoropolymers. Other fluoropolymers, such as FEP (fluorinated ethylene propylene) and PFA (perfluoroalkoxy alkane), have similar properties to PTFE but may offer advantages in certain applications. For example, FEP has a lower melting point and better transparency than PTFE, while PFA has better high-temperature performance and resistance to creep.
In conclusion, the composition of PTFE, with its strong carbon-fluorine bonds and tightly packed fluorine atoms, gives rise to a material with exceptional properties. Its chemical inertness, thermal stability, low friction, and excellent dielectric properties make it a valuable material in numerous applications, from non-stick coatings to electrical insulation and medical devices.
No responses yet