Key Components of FR4 Composition
FR4 is a composite material that consists of two main components: a glass fiber reinforcement and an epoxy resin matrix. Let’s take a closer look at each of these components.
Glass Fiber Reinforcement
The glass fiber reinforcement in FR4 is typically made from a type of glass called E-glass, which is known for its excellent electrical insulation properties and high mechanical strength. The glass fibers are woven into a fabric or mat, which provides the structural backbone of the PCB.
The glass fiber content in FR4 can vary depending on the specific application and desired properties. Generally, the glass fiber content ranges from 40% to 70% by weight. Higher glass fiber content results in improved mechanical strength, dimensional stability, and thermal resistance.
Epoxy Resin Matrix
The epoxy resin matrix in FR4 acts as a binder that holds the glass fibers together and provides the necessary insulation and chemical resistance. The most common type of epoxy resin used in FR4 is a bifunctional epoxy based on diglycidyl ether of bisphenol A (DGEBA).
The epoxy resin is mixed with a hardener, typically dicyandiamide (DICY), which initiates the cross-linking reaction during the curing process. The curing process involves exposing the PCB to heat and pressure, allowing the epoxy resin to polymerize and form a solid, durable matrix.
In addition to the base epoxy resin and hardener, various additives can be incorporated into the FR4 composition to enhance specific properties. These additives may include:
- Flame retardants: Brominated or phosphorus-based compounds are added to improve the flame retardancy of FR4.
- Fillers: Inorganic fillers, such as silica or aluminum hydroxide, can be added to improve thermal conductivity and reduce the coefficient of thermal expansion (CTE).
- Colorants: Pigments or dyes can be added to provide color coding or aesthetic appeal to the PCB.
Manufacturing Process of FR4 PCB
The manufacturing process of FR4 PCB involves several key steps that ensure the desired composition and properties are achieved. Let’s take a closer look at each step.
-
Preparing the Glass Fiber Reinforcement: The glass fibers are woven into a fabric or mat, which is then cut to the desired size and shape. The glass fiber reinforcement is then dried to remove any moisture that may interfere with the impregnation process.
-
Impregnation with Epoxy Resin: The glass fiber reinforcement is impregnated with the epoxy resin mixture, which typically consists of the base epoxy resin, hardener, and any necessary additives. This process is called “prepregging” and results in the formation of a prepreg sheet.
-
Layup and Lamination: Multiple prepreg sheets are stacked together, along with copper foils on the top and bottom layers, to form the desired thickness of the PCB. The stack is then placed in a lamination press, where heat and pressure are applied to cure the epoxy resin and bond the layers together.
-
Drilling and Plating: After lamination, holes are drilled through the PCB to accommodate component leads and vias. The holes are then plated with copper to establish electrical connections between layers.
-
Patterning and Etching: The copper foils on the outer layers of the PCB are patterned using photolithography and then etched to remove the unwanted copper, leaving behind the desired circuit pattern.
-
Surface Finishing: A surface finish, such as solder mask and silkscreen, is applied to the PCB to protect the circuitry and provide a visual reference for component placement.
Benefits of FR4 Composition
The unique composition of FR4 PCB offers several benefits that make it a popular choice for various applications. Some of the key benefits include:
-
Excellent Electrical Insulation: The epoxy resin matrix in FR4 provides excellent electrical insulation, preventing short circuits and ensuring reliable performance.
-
High Mechanical Strength: The glass fiber reinforcement in FR4 imparts high mechanical strength to the PCB, making it resistant to bending, twisting, and impact.
-
Flame Retardancy: The addition of flame retardants to the FR4 composition makes it resistant to ignition and flame propagation, enhancing the safety of the PCB in case of electrical faults or overheating.
-
Dimensional Stability: FR4 exhibits good dimensional stability over a wide range of temperatures, which is essential for maintaining the integrity of the circuit pattern and preventing warpage.
-
Chemical Resistance: The epoxy resin matrix in FR4 provides excellent chemical resistance, protecting the PCB from exposure to various solvents, acids, and oils that may be encountered during manufacturing or use.
-
Cost-Effectiveness: FR4 is a cost-effective material compared to other high-performance PCB substrates, making it a viable option for mass production and commercial applications.
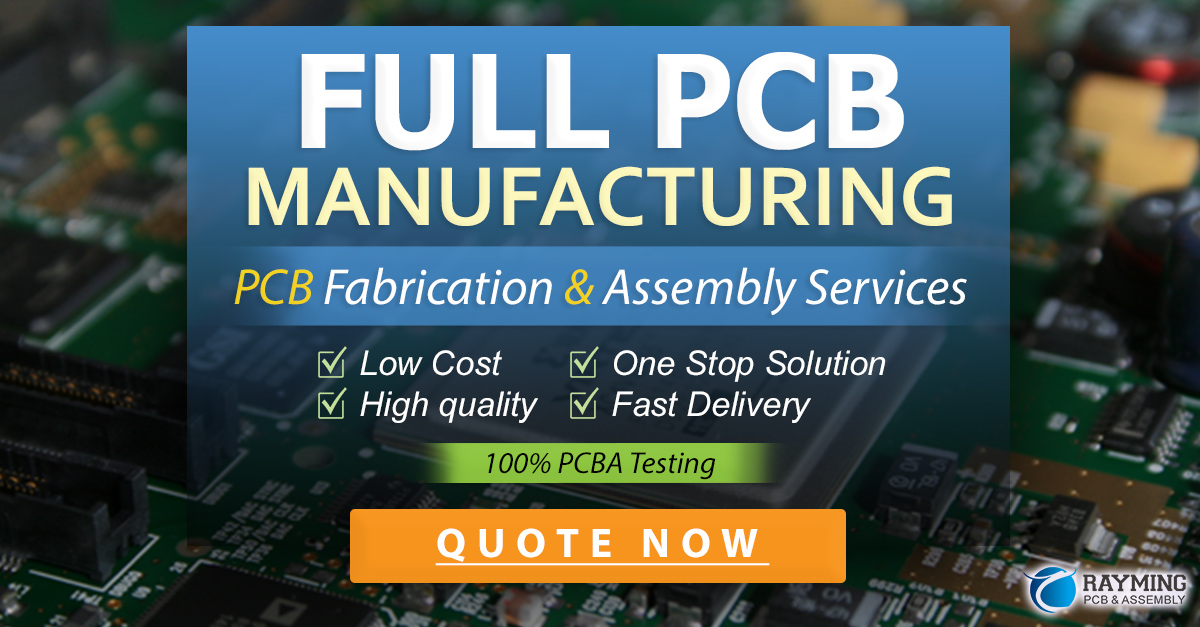
FAQ
-
What does FR4 stand for?
FR4 stands for Flame Retardant 4, indicating that it is a flame-retardant grade of PCB material. -
Is FR4 the only material used for PCBs?
No, while FR4 is the most common material used for PCBs, other materials such as polyimide, ceramic, and metal-core substrates are also used for specific applications. -
Can the composition of FR4 be customized?
Yes, the composition of FR4 can be customized to some extent by adjusting the glass fiber content, resin formulation, and additives to meet specific requirements. -
How does the glass fiber content affect the properties of FR4?
Higher glass fiber content in FR4 generally results in improved mechanical strength, dimensional stability, and thermal resistance, but may also increase the brittleness and weight of the PCB. -
What is the typical operating temperature range for FR4 PCBs?
FR4 PCBs are typically rated for an operating temperature range of -40°C to +130°C, although the exact range may vary depending on the specific formulation and glass transition temperature (Tg) of the epoxy resin used.
Conclusion
FR4 PCB is a versatile and widely used material in the electronics industry, owing to its unique composition and desirable properties. The combination of glass fiber reinforcement and epoxy resin matrix, along with various additives, enables FR4 to offer excellent electrical insulation, high mechanical strength, flame retardancy, dimensional stability, and chemical resistance.
Understanding the composition of FR4 and its manufacturing process is crucial for designers, engineers, and manufacturers to make informed decisions when selecting materials for their PCB applications. By leveraging the benefits of FR4, they can create reliable, high-performance electronic devices that meet the demanding requirements of today’s market.
As technology continues to advance, the composition of FR4 may evolve to incorporate new materials and additives that further enhance its properties and expand its range of applications. However, the fundamental principles of glass fiber reinforcement and epoxy resin matrix will likely remain the cornerstone of FR4 composition for the foreseeable future.
Component | Description |
---|---|
Glass Fiber Reinforcement | Woven glass fibers (E-glass) that provide structural strength and stability to the PCB. Typical content ranges from 40% to 70% by weight. |
Epoxy Resin Matrix | A thermoset polymer, usually based on diglycidyl ether of bisphenol A (DGEBA), that binds the glass fibers together and provides electrical insulation and chemical resistance. |
Hardener | A curing agent, typically dicyandiamide (DICY), that initiates the cross-linking reaction of the epoxy resin during the curing process. |
Flame Retardants | Brominated or phosphorus-based compounds added to improve the flame retardancy of FR4. |
Fillers | Inorganic materials, such as silica or aluminum hydroxide, added to enhance thermal conductivity and reduce the coefficient of thermal expansion (CTE). |
Colorants | Pigments or dyes added to provide color coding or aesthetic appeal to the PCB. |
No responses yet