Why Look for PCB Alternatives?
Traditional PCBs are made from a combination of materials, including copper, fiberglass, and epoxy resin. While these materials have served the industry well, they have some drawbacks:
-
Environmental Impact: The production and disposal of traditional PCBs can have a significant environmental impact. The process involves the use of hazardous chemicals and generates waste that can be difficult to dispose of safely.
-
Limited Flexibility: Traditional PCBs are rigid and cannot be easily bent or shaped to fit into certain devices or applications.
-
High Cost: The production of traditional PCBs can be costly, especially for small-scale production or prototyping.
Alternative Materials for PCBs
1. Polyimide PCBs
Polyimide is a high-performance polymer that offers excellent thermal stability, chemical resistance, and mechanical strength. Polyimide PCBs are made by laminating polyimide films with copper foil and are often used in applications that require high reliability and durability.
Advantages of Polyimide PCBs:
– High temperature resistance (up to 400°C)
– Excellent chemical resistance
– Good mechanical strength and flexibility
– Low Dielectric constant and dissipation factor
Applications of Polyimide PCBs:
– Aerospace and defense electronics
– High-temperature electronics
– Flexible electronics
– Medical devices
2. Liquid Crystal Polymer (LCP) PCBs
Liquid Crystal Polymer (LCP) is a high-performance thermoplastic material that offers excellent electrical and mechanical properties. LCP PCBs are made by laminating LCP films with copper foil and are often used in high-frequency applications.
Advantages of LCP PCBs:
– Low dielectric constant and dissipation factor
– Excellent high-frequency performance
– Good thermal stability and chemical resistance
– Low moisture absorption
Applications of LCP PCBs:
– High-frequency electronics (e.g., 5G, radar, and satellite communication)
– Automotive electronics
– Medical devices
– Wearable electronics
3. Biodegradable PCBs
Biodegradable PCBs are made from materials that can be broken down by microorganisms in the environment. These PCBs are designed to reduce the environmental impact of electronics waste and are often made from natural materials such as paper, wood, or biodegradable polymers.
Advantages of Biodegradable PCBs:
– Reduced environmental impact
– Made from renewable resources
– Can be composted or recycled
– Lower production costs compared to traditional PCBs
Applications of Biodegradable PCBs:
– Disposable electronics (e.g., single-use sensors or wearables)
– Eco-friendly packaging
– Educational and hobby projects
4. Flexible PCBs
Flexible PCBs are made from thin, flexible materials such as polyimide or polyester. These PCBs can be bent, twisted, or folded to fit into tight spaces or conform to curved surfaces.
Advantages of Flexible PCBs:
– Increased design flexibility
– Reduced weight and space requirements
– Improved reliability due to reduced connectors and solder joints
– Suitable for wearable and implantable devices
Applications of Flexible PCBs:
– Wearable electronics
– Medical devices and implants
– Automotive electronics
– Consumer electronics (e.g., smartphones, tablets)
5. 3D Printed PCBs
3D printing technology has enabled the production of PCBs with complex geometries and embedded components. 3D printed PCBs are made by depositing conductive and insulating materials layer by layer using additive manufacturing techniques.
Advantages of 3D Printed PCBs:
– Rapid prototyping and customization
– Ability to create complex geometries and embedded components
– Reduced waste and production costs for small-scale production
– Potential for multi-material printing (e.g., conductive and insulating materials)
Applications of 3D Printed PCBs:
– Rapid prototyping and proof-of-concept designs
– Customized and low-volume production
– Education and research
– Aerospace and defense applications
Comparison of PCB Alternatives
Material | Advantages | Disadvantages | Applications |
---|---|---|---|
Polyimide | High temperature resistance, excellent chemical resistance, good mechanical strength and flexibility | Higher cost compared to traditional PCBs, limited availability | Aerospace and defense electronics, high-temperature electronics, flexible electronics, medical devices |
LCP | Low dielectric constant and dissipation factor, excellent high-frequency performance, good thermal stability and chemical resistance | Higher cost compared to traditional PCBs, limited availability, more challenging to process | High-frequency electronics (e.g., 5G, radar, and satellite communication), automotive electronics, medical devices, wearable electronics |
Biodegradable | Reduced environmental impact, made from renewable resources, can be composted or recycled, lower production costs | Limited performance compared to traditional PCBs, not suitable for high-reliability applications | Disposable electronics (e.g., single-use sensors or wearables), eco-friendly packaging, educational and hobby projects |
Flexible | Increased design flexibility, reduced weight and space requirements, improved reliability | Higher cost compared to traditional PCBs, more challenging to manufacture and assemble | Wearable electronics, medical devices and implants, automotive electronics, consumer electronics (e.g., smartphones, tablets) |
3D Printed | Rapid prototyping and customization, ability to create complex geometries and embedded components, reduced waste and production costs for small-scale production | Limited performance compared to traditional PCBs, higher cost for large-scale production, limited material options | Rapid prototyping and proof-of-concept designs, customized and low-volume production, education and research, aerospace and defense applications |
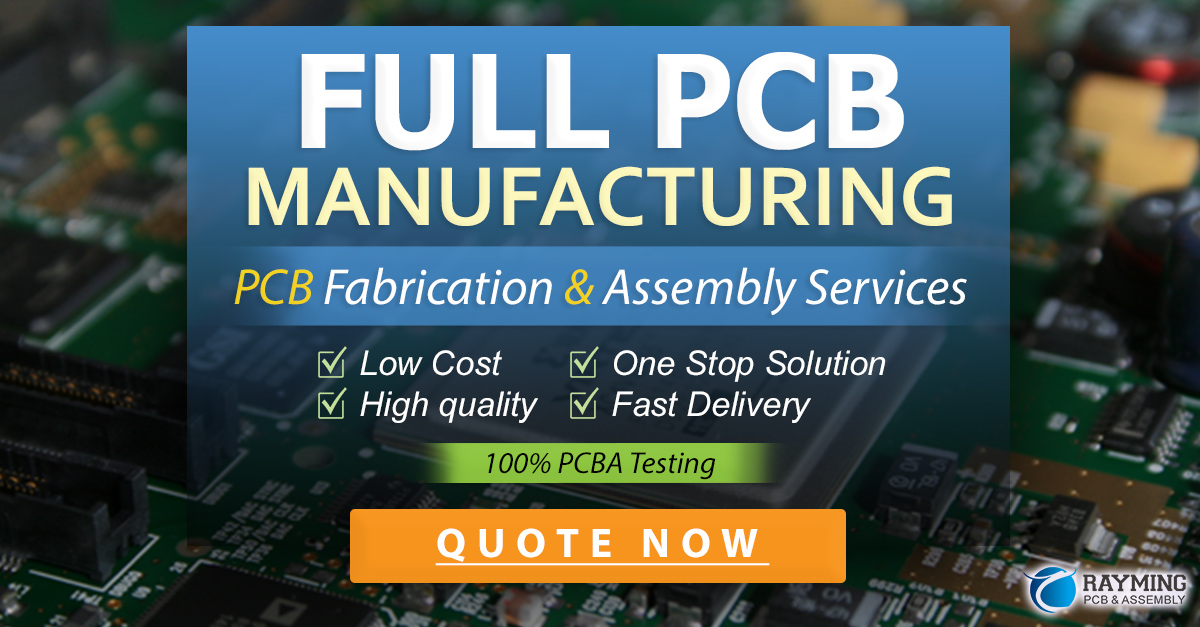
FAQ
-
Q: Are alternative PCB materials as reliable as traditional PCBs?
A: Some alternative materials, such as polyimide and LCP, offer excellent reliability and performance in specific applications. However, other alternatives, such as biodegradable PCBs, may have limited performance compared to traditional PCBs and are not suitable for high-reliability applications. -
Q: Are alternative PCB Materials more expensive than traditional PCBs?
A: The cost of alternative PCB materials varies depending on the specific material and application. Some materials, such as polyimide and LCP, can be more expensive than traditional PCBs due to their higher performance and limited availability. However, other alternatives, such as biodegradable PCBs, can have lower production costs compared to traditional PCBs. -
Q: Can alternative PCB materials be used for high-frequency applications?
A: Yes, some alternative materials, such as LCP, are specifically designed for high-frequency applications due to their low dielectric constant and dissipation factor. These materials offer excellent high-frequency performance and are suitable for applications such as 5G, radar, and satellite communication. -
Q: Are alternative PCB materials environmentally friendly?
A: Some alternative PCB materials, such as biodegradable PCBs, are designed to be more environmentally friendly than traditional PCBs. These materials can be made from renewable resources, can be composted or recycled, and have a reduced environmental impact. However, not all alternative materials are inherently more environmentally friendly than traditional PCBs. -
Q: Can alternative PCB materials be used for flexible electronics?
A: Yes, some alternative materials, such as polyimide and flexible PCBs, are specifically designed for use in flexible electronics applications. These materials offer increased design flexibility, reduced weight and space requirements, and improved reliability compared to traditional rigid PCBs. They are suitable for applications such as wearable electronics, medical devices, and consumer electronics.
Conclusion
As the electronics industry continues to evolve, the demand for alternative materials for PCBs is growing. Alternative materials offer unique advantages over traditional PCBs, such as increased design flexibility, improved high-frequency performance, and reduced environmental impact. While some alternative materials may have higher costs or limited availability compared to traditional PCBs, they can be the preferred choice for specific applications and industries.
The selection of an alternative PCB material depends on the specific requirements of the application, such as thermal stability, chemical resistance, mechanical strength, and environmental impact. By understanding the advantages and limitations of each alternative material, designers and manufacturers can make informed decisions when selecting the most suitable PCB material for their projects.
As research and development in alternative PCB materials continue, we can expect to see more innovative solutions that address the challenges faced by the electronics industry. The adoption of alternative PCB materials will not only lead to more sustainable and environmentally friendly electronics but also enable the development of new and innovative applications in various fields, such as wearable technology, medical devices, and high-frequency communication systems.
No responses yet