What is a PCB?
A Printed Circuit Board (PCB) is a thin board made of insulating materials, such as fiberglass or composite epoxy, with conductive copper traces printed onto its surface. These traces connect various electronic components, such as resistors, capacitors, and integrated circuits (ICs), to form a complete electronic circuit. PCBs can be single-sided, double-sided, or multi-layered, depending on the complexity of the circuit and the space constraints of the device.
Advantages of PCBs over Regular Wiring
1. Compact Size and Space Efficiency
One of the most significant advantages of PCBs is their ability to accommodate complex circuits in a compact space. With the use of surface mount technology (SMT) and miniaturized components, PCBs can be designed to fit within the tight confines of modern electronic devices, such as smartphones, tablets, and wearables. In contrast, point-to-point wiring requires more space due to the need for individual wire connections between components, making it less suitable for space-constrained applications.
Component Packaging | Size Comparison |
---|---|
Through-hole | Larger |
Surface Mount (SMT) | Smaller |
2. Improved Reliability and Durability
PCBs offer superior reliability and durability compared to regular wiring. The copper traces on a PCB are firmly bonded to the insulating substrate, making them less susceptible to physical damage, vibration, and environmental factors such as temperature and humidity. Additionally, PCBs can be coated with protective layers, such as conformal coatings or potting compounds, to further enhance their durability in harsh environments.
In contrast, point-to-point wiring is more vulnerable to physical damage, as the wires can become loose or disconnected over time due to vibration or mechanical stress. This can lead to intermittent faults or complete circuit failure, compromising the reliability of the device.
3. Enhanced Electrical Performance
PCBs provide better electrical performance compared to regular wiring in several ways:
- Reduced crosstalk: The precise layout and routing of traces on a PCB minimize the risk of crosstalk between signals, ensuring cleaner and more stable signal transmission.
- Controlled impedance: PCBs allow for the design of controlled impedance traces, which is essential for high-speed digital circuits and RF applications.
- Reduced electromagnetic interference (EMI): Proper PCB design techniques, such as ground planes and shielding, can help minimize EMI, ensuring the device meets regulatory requirements and performs reliably in the presence of external electromagnetic fields.
4. Faster and More Consistent Manufacturing
PCBs enable faster and more consistent manufacturing compared to point-to-point wiring. The use of automated assembly processes, such as pick-and-place machines and reflow soldering, allows for high-volume production with minimal human intervention. This results in lower manufacturing costs, reduced assembly time, and improved product quality and consistency.
In contrast, point-to-point wiring is a more labor-intensive process that relies on manual soldering and wire routing. This approach is prone to human error, leading to inconsistencies in the final product and longer assembly times.
Manufacturing Method | Speed | Consistency |
---|---|---|
PCB Assembly | Fast | High |
Point-to-Point Wiring | Slow | Low |
5. Simplified Troubleshooting and Repair
PCBs simplify troubleshooting and repair processes compared to regular wiring. The standardized layout and labeling of components on a PCB make it easier for technicians to identify and replace faulty components. Additionally, PCBs often include test points and debugging interfaces, which facilitate the use of automated testing equipment and diagnostic tools.
With point-to-point wiring, troubleshooting can be more challenging, as the technician must manually trace the wires to identify the source of the problem. This process can be time-consuming and requires a higher level of expertise, leading to increased repair costs and longer downtime.
6. Scalability and Adaptability
PCBs offer excellent scalability and adaptability, allowing designers to easily modify and upgrade circuits as needed. With the use of modular design approaches and standardized interfaces, PCBs can be designed to accommodate future expansions or changes in functionality without requiring a complete redesign of the device.
Regular wiring, on the other hand, is less adaptable to changes in the circuit design. Modifying a point-to-point wired circuit often requires significant rework, including the removal and re-routing of wires, which can be time-consuming and prone to errors.
7. Cost-Effectiveness
While the initial design and setup costs for PCBs may be higher compared to regular wiring, the long-term cost-effectiveness of PCBs is significantly better. The automated manufacturing processes, improved reliability, and reduced assembly time associated with PCBs contribute to lower overall production costs, especially for high-volume production.
Additionally, the compact size and improved performance of PCB-based devices can lead to cost savings in terms of reduced material usage, lower power consumption, and smaller packaging requirements.
PCB Design Considerations
To fully realize the advantages of PCBs, designers must consider several key factors during the design process:
- Component selection and placement: Choosing the right components and optimizing their placement on the PCB is crucial for achieving the desired performance, reliability, and manufacturability.
- Signal integrity: Ensuring proper signal integrity through careful trace routing, impedance control, and termination techniques is essential for maintaining the integrity of high-speed digital and analog signals.
- Thermal management: Designing adequate thermal management solutions, such as heatsinks and thermal vias, is necessary to dissipate heat generated by components and prevent thermal-related failures.
- EMI/EMC compliance: Incorporating EMI/EMC mitigation techniques, such as shielding and filtering, is crucial for meeting regulatory requirements and ensuring reliable operation in the presence of electromagnetic interference.
By addressing these design considerations, PCB designers can create high-quality, reliable, and cost-effective electronic devices that leverage the full potential of PCB technology.
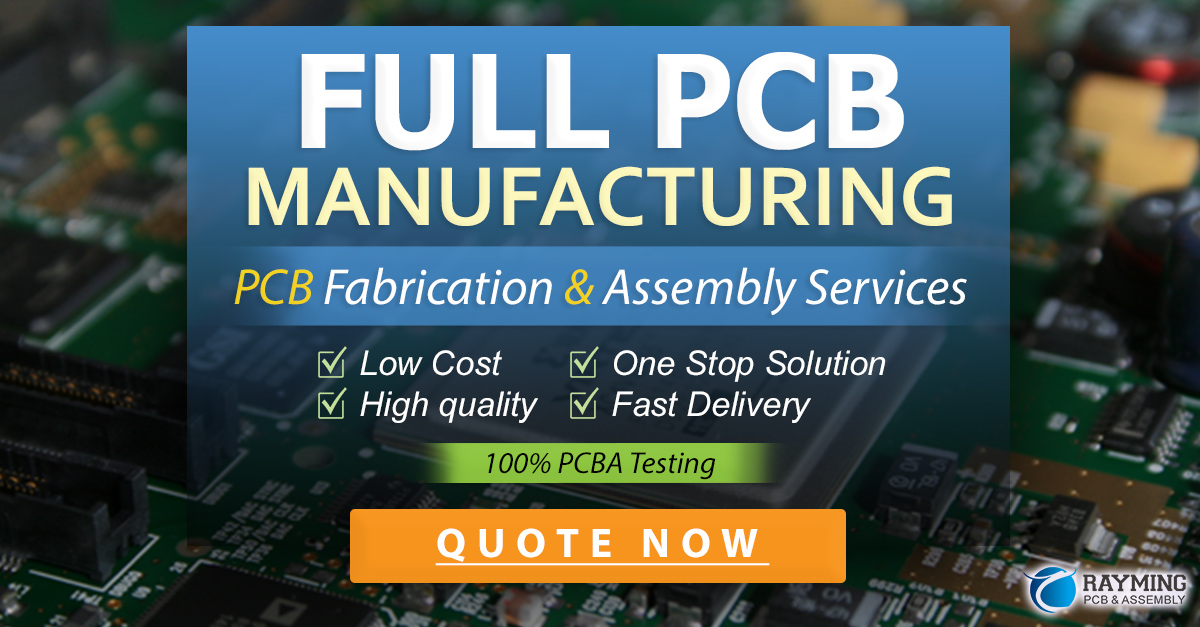
Frequently Asked Questions (FAQ)
- What are the different types of PCBs?
PCBs can be classified based on the number of conductive layers and the type of construction. The most common types include: - Single-sided PCBs: These have conductive traces on only one side of the board.
- Double-sided PCBs: These have conductive traces on both sides of the board, with through-hole connections between the layers.
- Multi-layer PCBs: These have three or more conductive layers, with insulating layers separating them. They are used for complex circuits that require high density and improved signal integrity.
- Rigid PCBs: These are the most common type, made from a solid substrate material such as fiberglass or epoxy.
-
Flexible PCBs: These are made from flexible materials, such as polyimide, and can be bent or folded to fit into tight spaces or conform to curved surfaces.
-
What are the main steps in the PCB manufacturing process?
The PCB manufacturing process typically involves the following steps: - Design: The circuit is designed using CAD software, and the PCB layout is created.
- Printing: The PCB design is printed onto the copper-clad board using a photoresist process.
- Etching: The unwanted copper is removed using a chemical etching process, leaving only the desired conductive traces.
- Drilling: Holes are drilled into the board for through-hole components and vias.
- Plating: The holes are plated with copper to create electrical connections between layers.
- Solder mask application: A protective solder mask is applied to the board to prevent short circuits and improve durability.
- Silkscreen printing: Labels and markings are printed onto the board for component identification and assembly guidance.
- Surface finish application: A surface finish, such as HASL or ENIG, is applied to the exposed copper to prevent oxidation and improve solderability.
- Assembly: The electronic components are placed and soldered onto the PCB using automated assembly processes.
-
Testing and inspection: The assembled PCB is tested and inspected to ensure proper functionality and quality.
-
What are the common materials used for PCB substrates?
The most common materials used for PCB substrates include: - FR-4: A fiberglass-reinforced epoxy laminate that offers good mechanical and electrical properties, making it the most widely used substrate material for rigid PCBs.
- Polyimide: A flexible polymer material used for flexible PCBs, offering high heat resistance and good mechanical stability.
- Ceramic: Used for high-frequency and high-temperature applications, ceramic substrates offer excellent thermal conductivity and low dielectric loss.
-
Metal core: Used for high-power applications that require efficient heat dissipation, metal core PCBs have a metal substrate, such as aluminum, with a thin dielectric layer and copper traces on top.
-
What is the difference between through-hole and surface mount components?
Through-hole components have long leads that are inserted into drilled holes on the PCB and soldered on the opposite side. They are typically larger and more mechanically stable than surface mount components, making them suitable for high-power and high-reliability applications.
Surface mount components have small leads or pads that are soldered directly onto the surface of the PCB. They are smaller and more compact than through-hole components, allowing for higher component density and improved high-frequency performance. Surface mount technology (SMT) is the most widely used component packaging method in modern PCB assembly.
- What are the advantages of using multi-layer PCBs?
Multi-layer PCBs offer several advantages over single- and double-sided PCBs: - Increased component density: The additional layers allow for more components to be placed on the board, enabling more complex circuits in a smaller footprint.
- Improved signal integrity: The use of dedicated power and ground planes, as well as the ability to route signals on different layers, helps reduce crosstalk and improve signal quality.
- Better EMI/EMC performance: The power and ground planes act as shields, reducing electromagnetic interference and improving electromagnetic compatibility.
- Enhanced thermal management: The increased number of layers allows for better heat distribution and the use of thermal vias to dissipate heat from components.
- Reduced size and weight: By accommodating more components in a smaller space, multi-layer PCBs enable the design of more compact and lightweight electronic devices.
Conclusion
Printed Circuit Boards (PCBs) have become an indispensable part of modern electronics manufacturing, offering numerous advantages over traditional point-to-point wiring methods. From their compact size and improved reliability to their enhanced electrical performance and cost-effectiveness, PCBs have revolutionized the way electronic devices are designed and manufactured.
As electronic devices continue to evolve and become more complex, the importance of PCBs in the industry will only continue to grow. By understanding the advantages of PCBs and the key design considerations involved in their development, engineers and manufacturers can create innovative, reliable, and cost-effective electronic products that meet the ever-increasing demands of the market.
No responses yet