Introduction to Teflon PCB
Teflon PCB, also known as PTFE (Polytetrafluoroethylene) based PCB, is a type of printed circuit board that uses Teflon as the primary substrate material. Teflon is a synthetic fluoropolymer of tetrafluoroethylene, known for its excellent electrical insulation properties, high heat resistance, and low dielectric constant. These unique properties make Teflon PCBs ideal for high-frequency applications, such as those found in the aerospace, military, and telecommunications industries.
Advantages of Teflon PCB
- Low Dielectric Constant: Teflon has a low dielectric constant (2.1), which minimizes signal loss and allows for higher signal speeds.
- High Heat Resistance: Teflon can withstand temperatures up to 260°C (500°F), making it suitable for high-temperature applications.
- Excellent Electrical Insulation: Teflon provides superior electrical insulation, reducing the risk of short circuits and signal interference.
- Low Moisture Absorption: Teflon has a low moisture absorption rate, ensuring stable performance in humid environments.
- Chemical Resistance: Teflon is resistant to most chemicals, making it suitable for use in harsh industrial environments.
PTFE Based Laminates
PTFE based laminates are the foundation of Teflon PCBs. These laminates consist of a PTFE substrate with copper foil bonded to one or both sides. The most common PTFE based laminates used in PCB manufacturing include:
Rogers Corporation Laminates
Rogers Corporation is a leading manufacturer of high-performance PTFE based laminates for PCB manufacturing. Some of their popular laminates include:
- RT/duroid® 5870 – 5880: These laminates offer a low dielectric constant (2.33 – 2.2) and low dissipation factor, making them suitable for high-frequency applications.
- RO3000® Series: This series offers a lower cost alternative to RT/duroid® while maintaining good electrical properties and ease of fabrication.
- RO4000® Series: These laminates provide a balance of cost and performance, with a low dielectric constant (3.3 – 3.48) and low loss tangent.
Taconic Laminates
Taconic is another well-known manufacturer of PTFE based laminates for PCB manufacturing. Some of their popular laminates include:
- TLY: A low-loss, high-performance laminate with a dielectric constant of 2.2 and a low dissipation factor.
- TLX: A high-performance laminate with a dielectric constant of 2.45 and a low dissipation factor, suitable for high-frequency applications.
- RF-35: A cost-effective laminate with a dielectric constant of 3.5, ideal for less demanding RF applications.
Laminate | Manufacturer | Dielectric Constant | Dissipation Factor | Thermal Conductivity (W/m·K) |
---|---|---|---|---|
RT/duroid® 5870 | Rogers Corp. | 2.33 | 0.0012 | 0.22 |
RT/duroid® 5880 | Rogers Corp. | 2.20 | 0.0009 | 0.20 |
RO3003™ | Rogers Corp. | 3.00 | 0.0013 | 0.50 |
RO4003C™ | Rogers Corp. | 3.38 | 0.0027 | 0.71 |
TLY | Taconic | 2.20 | 0.0009 | 0.26 |
TLX | Taconic | 2.45 | 0.0019 | 0.26 |
RF-35 | Taconic | 3.50 | 0.0018 | 0.26 |
PCB Manufacturing Process with Teflon
The manufacturing process for Teflon PCBs is similar to that of standard PCBs, with a few key differences due to the unique properties of PTFE based laminates.
Design and Preparation
- PCB Design: The PCB design is created using CAD software, taking into account the specific requirements of the Teflon laminate.
- Gerber File Generation: The CAD design is converted into Gerber files, which are used to guide the PCB manufacturing process.
- Material Selection: The appropriate Teflon laminate is selected based on the application’s requirements.
Fabrication
- Laminate Cutting: The Teflon laminate is cut to the desired size using specialized cutting tools.
- Drilling: Holes are drilled into the laminate for component placement and via creation.
- Plating: The drilled holes are plated with copper to establish electrical connections between layers.
- Patterning: The copper foil is patterned using photolithography and etching techniques to create the desired circuit layout.
- Solder Mask Application: A solder mask is applied to protect the copper traces and prevent short circuits.
- Surface Finish Application: A surface finish, such as ENIG (Electroless Nickel Immersion Gold) or HASL (Hot Air Solder Leveling), is applied to protect the exposed copper and improve solderability.
Assembly
- Component Placement: Electronic components are placed on the PCB using automated pick-and-place machines or manual placement techniques.
- Soldering: The components are soldered onto the PCB using reflow soldering or wave soldering techniques.
- Inspection and Testing: The assembled PCB undergoes visual inspection and electrical testing to ensure proper functionality and adherence to specifications.
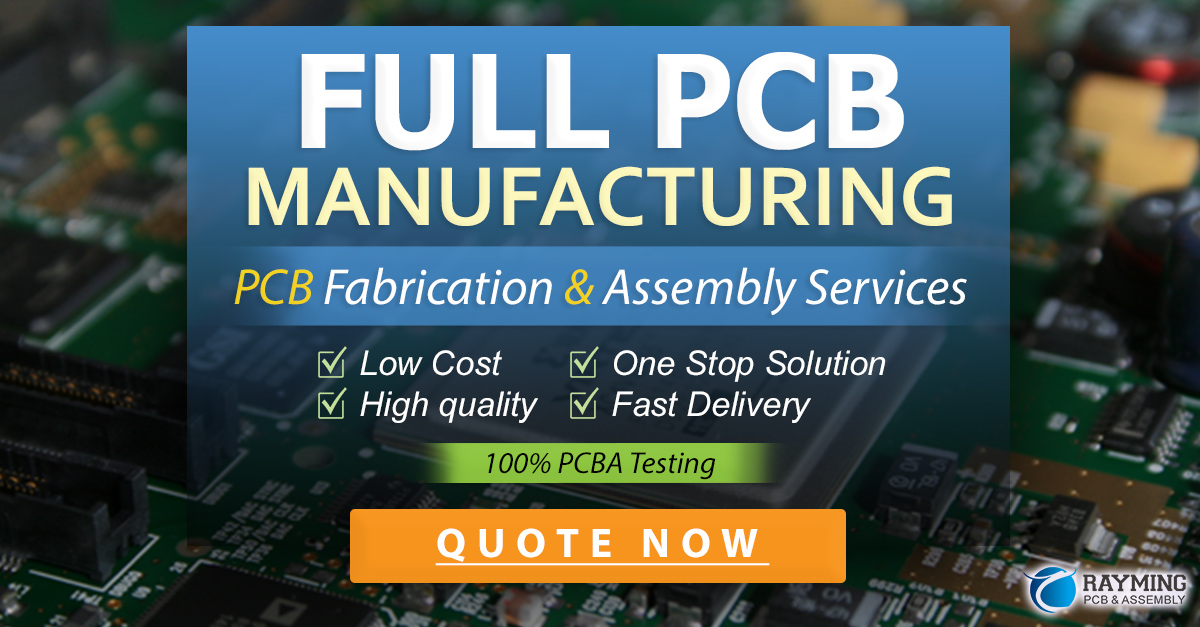
Costs Associated with Teflon PCB Manufacturing
The cost of manufacturing Teflon PCBs is generally higher compared to standard FR-4 PCBs due to the specialized materials and processing techniques required.
Factors Affecting Teflon PCB Costs
- Laminate Material: PTFE based laminates are more expensive than standard FR-4 laminates.
- Layer Count: Higher layer count Teflon PCBs are more expensive due to the increased complexity of manufacturing.
- Manufacturing Process: The specialized processing techniques required for Teflon PCBs, such as high-temperature pressing and drilling, contribute to higher manufacturing costs.
- Order Quantity: Larger order quantities can help reduce the per-unit cost of Teflon PCBs.
- Design Complexity: More complex PCB designs with fine pitch components and high-density layouts may increase manufacturing costs.
Cost Comparison: Teflon PCB vs. Standard FR-4 PCB
To illustrate the cost difference between Teflon PCBs and standard FR-4 PCBs, consider the following example:
PCB Type | Layer Count | Size (mm) | Quantity | Lead Time | Estimated Cost per Unit |
---|---|---|---|---|---|
Teflon PCB | 2 | 100 x 100 | 100 | 3-4 weeks | $30 – $40 |
FR-4 PCB | 2 | 100 x 100 | 100 | 1-2 weeks | $5 – $10 |
As seen in the table, the estimated cost per unit for a Teflon PCB can be 3 to 8 times higher than that of a standard FR-4 PCB with similar specifications.
Applications of Teflon PCB
Teflon PCBs are used in various industries and applications where high-frequency performance, low signal loss, and high temperature resistance are critical. Some common applications include:
- Aerospace and Defense:
- Radar systems
- Satellite communication equipment
- Avionics
-
Military communication devices
-
Telecommunications:
- 5G networks
- Microwave antennas
- Base stations
-
High-speed data transmission equipment
-
Medical Equipment:
- MRI machines
- High-frequency medical imaging devices
-
Ultrasound equipment
-
Industrial:
- High-temperature sensors
- Oil and gas exploration equipment
-
Microwave heating systems
-
Automotive:
- Radar sensors for advanced driver assistance systems (ADAS)
- Vehicle-to-vehicle (V2V) communication systems
- Autonomous driving technology
Frequently Asked Questions (FAQ)
- What is the main difference between Teflon PCB and standard FR-4 PCB?
-
The main difference is the substrate material. Teflon PCBs use PTFE based laminates, while standard PCBs use FR-4 laminates. Teflon PCBs offer superior high-frequency performance, low dielectric constant, and high temperature resistance compared to FR-4 PCBs.
-
Can Teflon PCBs be used for low-frequency applications?
-
While Teflon PCBs excel in high-frequency applications, they can also be used for low-frequency applications. However, the higher cost of Teflon PCBs may not be justified for low-frequency applications where standard FR-4 PCBs can suffice.
-
How do I select the right Teflon laminate for my application?
-
The selection of the appropriate Teflon laminate depends on factors such as the desired dielectric constant, dissipation factor, thermal conductivity, and cost. Consult with your PCB manufacturer or laminate supplier to determine the best laminate for your specific application.
-
Are Teflon PCBs suitable for high-volume production?
-
Teflon PCBs can be manufactured in high volumes, but the cost per unit may be higher compared to standard FR-4 PCBs. The suitability for high-volume production depends on the specific application, budget, and performance requirements.
-
What are the lead times for Teflon PCB manufacturing?
- Lead times for Teflon PCB manufacturing are typically longer than those for standard FR-4 PCBs due to the specialized materials and processing techniques required. Expect lead times of 3-4 weeks or more, depending on the complexity of the design and the manufacturer’s workload.
Conclusion
Teflon PCBs offer unique advantages over standard FR-4 PCBs in high-frequency applications, thanks to their low dielectric constant, high temperature resistance, and excellent electrical insulation properties. PTFE based laminates from manufacturers like Rogers Corporation and Taconic form the foundation of Teflon PCBs, providing a range of options to suit various application requirements.
While the manufacturing process for Teflon PCBs is similar to that of standard PCBs, the specialized materials and processing techniques involved contribute to higher manufacturing costs. Despite the higher costs, Teflon PCBs find extensive use in industries such as aerospace, telecommunications, medical equipment, and automotive, where high-frequency performance and reliability are paramount.
When considering Teflon PCBs for your application, it is essential to weigh the performance benefits against the increased costs and lead times. Collaborating with experienced PCB manufacturers and laminate suppliers can help you make informed decisions and ensure the success of your high-frequency projects.
No responses yet