Introduction to Teflon PCB
Teflon, also known as polytetrafluoroethylene (PTFE), is a synthetic fluoropolymer widely used in various industries due to its unique properties. In the world of printed circuit boards (PCBs), Teflon has gained significant attention for its excellent dielectric and thermal properties, making it an ideal choice for high-frequency and high-temperature applications. This article will delve into the characteristics, advantages, applications, and manufacturing process of Teflon PCBs.
What is Teflon?
Teflon is a synthetic fluoropolymer discovered by Roy J. Plunkett in 1938 while working for DuPont. It is a highly stable and inert material known for its low coefficient of friction, high melting point, and excellent chemical resistance. Teflon is composed of carbon and fluorine atoms arranged in a repeating pattern, forming a strong and stable molecular structure.
Properties of Teflon
Teflon possesses a unique combination of properties that make it highly desirable for various applications, including PCBs:
- Low Dielectric constant and loss tangent
- High thermal stability and resistance to extreme temperatures
- Excellent chemical resistance to acids, bases, and solvents
- Low coefficient of friction and non-stick surface
- High flexural strength and dimensional stability
- Low moisture absorption and permeability
Advantages of Teflon PCBs
Superior Dielectric Properties
One of the most significant advantages of Teflon PCBs is their excellent dielectric properties. Teflon has a low dielectric constant (2.1 at 1 MHz) and a low loss tangent (0.0002 at 1 MHz), which minimizes signal loss and distortion in high-frequency applications. This makes Teflon PCBs ideal for use in radio frequency (RF) and microwave devices, where signal integrity is crucial.
High Thermal Stability
Teflon PCBs offer exceptional thermal stability, with a continuous service temperature range of -200°C to +260°C. This wide temperature range allows Teflon PCBs to withstand extreme environments and maintain their performance under harsh conditions. The high melting point of Teflon (327°C) also ensures that the PCB substrate remains stable during the assembly process, minimizing the risk of deformation or damage.
Chemical Resistance
Teflon is renowned for its chemical inertness and resistance to a wide range of chemicals, including acids, bases, and solvents. This property makes Teflon PCBs suitable for use in corrosive environments and applications where exposure to aggressive chemicals is expected. The non-reactive nature of Teflon also prevents the formation of unwanted chemical byproducts that could compromise the performance of the PCB.
Low Moisture Absorption
Teflon has a very low moisture absorption rate, typically less than 0.01% by weight. This property is essential for maintaining the dimensional stability and performance of the PCB, especially in humid environments. Low moisture absorption minimizes the risk of delamination, warping, and other moisture-related failures, ensuring the long-term reliability of the PCB.
Applications of Teflon PCBs
High-Frequency and Microwave Devices
Teflon PCBs are extensively used in high-frequency and microwave applications due to their superior dielectric properties. These applications include:
- Radar systems
- Satellite communication devices
- Wireless communication equipment
- High-speed data transmission systems
- Antennas and wave guides
The low dielectric constant and loss tangent of Teflon minimize signal attenuation and distortion, enabling high-frequency signals to propagate with minimal losses.
Aerospace and Military Electronics
Teflon PCBs are well-suited for aerospace and military applications, where reliability and performance under extreme conditions are paramount. The high thermal stability and chemical resistance of Teflon make it an ideal choice for electronics exposed to harsh environments, such as:
- Avionics systems
- Missile guidance systems
- Satellite electronics
- Radar equipment
- Military communication devices
Teflon PCBs can withstand the rigors of aerospace and military applications, ensuring the proper functioning of critical electronic systems.
Medical Devices
Teflon PCBs find applications in medical devices due to their biocompatibility, chemical resistance, and ability to withstand sterilization processes. Some examples of medical applications include:
- Implantable devices
- Diagnostic equipment
- Surgical instruments
- Medical imaging systems
- Monitoring devices
The inert nature of Teflon minimizes the risk of adverse reactions and ensures the longevity of medical electronics.
Industrial and Scientific Instruments
Teflon PCBs are used in various industrial and scientific instruments that require high precision, stability, and resistance to harsh environments. These applications include:
- Process control systems
- Analytical instrumentation
- Sensors and transducers
- Oil and gas exploration equipment
- Environmental monitoring devices
The dimensional stability and low moisture absorption of Teflon contribute to the accurate and reliable performance of these instruments.
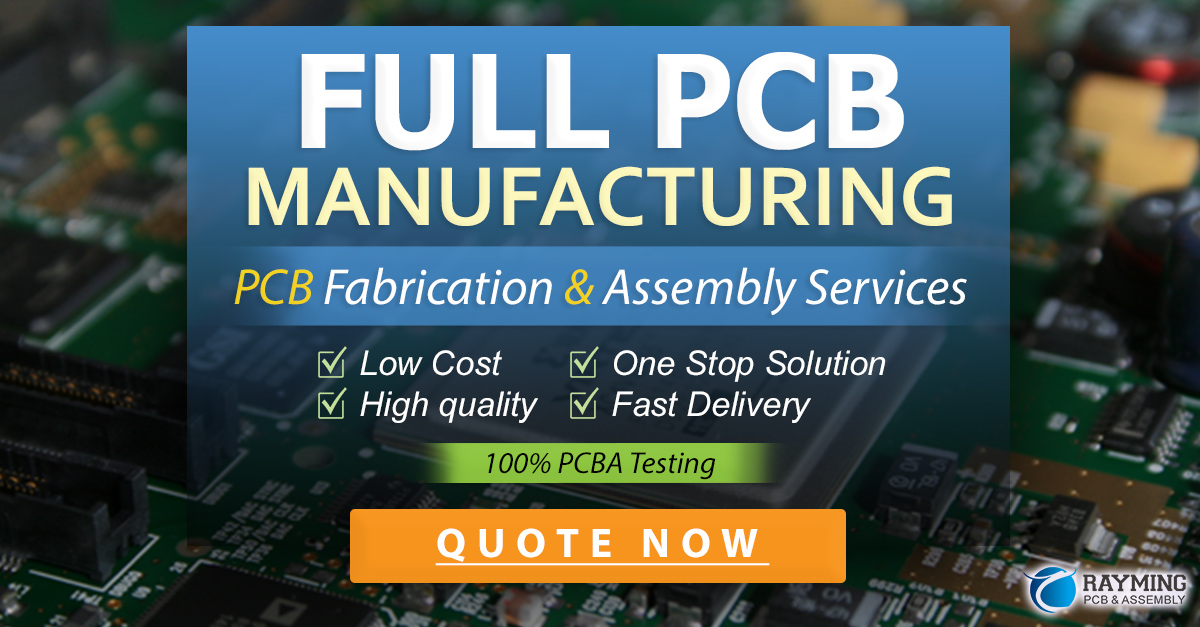
Manufacturing Process of Teflon PCBs
The manufacturing process of Teflon PCBs differs from that of traditional FR-4 PCBs due to the unique properties of Teflon. The main steps involved in the production of Teflon PCBs are:
-
Substrate preparation: Teflon laminates are cut to the desired size and shape, and the surface is cleaned to ensure proper adhesion of the conductor layer.
-
Conductor layer application: The conductor layer, typically copper, is applied to the Teflon substrate using a process called electroless plating or sputtering. This layer serves as the foundation for the circuit pattern.
-
Circuit pattern creation: The desired circuit pattern is created on the conductor layer using photolithography. A photoresist is applied, exposed to UV light through a mask, and developed to reveal the desired pattern.
-
Etching: The unwanted copper is removed using a chemical etching process, leaving behind the desired circuit pattern.
-
Drilling and plating: Holes are drilled through the PCB for component mounting and interconnections. The holes are then plated with copper to establish electrical connections between layers.
-
Solder mask and silkscreen application: A solder mask is applied to protect the circuit pattern and prevent short circuits. Silkscreen printing is used to add component labels and other markings on the PCB surface.
-
Surface finish: A surface finish, such as HASL (Hot Air Solder Leveling) or ENIG (Electroless Nickel Immersion Gold), is applied to the exposed copper areas to improve solderability and protect against oxidation.
-
Electrical testing and quality control: The manufactured Teflon PCBs undergo rigorous electrical testing and quality control to ensure they meet the specified requirements and performance standards.
Challenges and Considerations
While Teflon PCBs offer numerous advantages, there are some challenges and considerations to keep in mind:
-
Higher material cost: Teflon laminates are more expensive than traditional FR-4 substrates, which can increase the overall cost of the PCB.
-
Specialized manufacturing processes: The unique properties of Teflon require specialized manufacturing processes and equipment, which may limit the number of PCB manufacturers capable of producing Teflon PCBs.
-
Design considerations: Designing Teflon PCBs requires careful consideration of the material properties, such as the coefficient of thermal expansion (CTE) and the dielectric constant, to ensure proper signal integrity and mechanical stability.
-
Assembly challenges: The non-stick properties of Teflon can make it challenging to achieve reliable solder joints during the assembly process. Special techniques, such as plasma treatment or mechanical roughening, may be required to improve adhesion.
Frequently Asked Questions (FAQ)
-
What is the difference between Teflon and PTFE?
Teflon is a brand name for polytetrafluoroethylene (PTFE), which is a synthetic fluoropolymer. While Teflon is a specific brand, PTFE refers to the generic material. In the context of PCBs, the terms Teflon and PTFE are often used interchangeably. -
Can Teflon PCBs be used for high-power applications?
Yes, Teflon PCBs are suitable for high-power applications due to their excellent thermal stability and high Dielectric strength. The low dielectric loss of Teflon minimizes heat generation, and its high melting point ensures that the PCB can withstand elevated temperatures. -
Are Teflon PCBs compatible with lead-free soldering processes?
Yes, Teflon PCBs are compatible with lead-free soldering processes. However, due to the non-stick properties of Teflon, special considerations may be necessary to ensure proper solder joint formation. Surface treatments or the use of compatible solder masks can help improve the solderability of Teflon PCBs. -
How do Teflon PCBs compare to Ceramic PCBs in terms of performance?
Teflon PCBs and ceramic PCBs both offer excellent high-frequency performance and thermal stability. However, Teflon PCBs have some advantages over ceramic PCBs, such as lower dielectric constant, lower loss tangent, and better mechanical flexibility. Ceramic PCBs, on the other hand, have higher Thermal conductivity and can handle higher temperatures. -
Can Teflon PCBs be recycled?
Recycling Teflon PCBs can be challenging due to the inert nature of Teflon and the presence of other materials, such as copper and solder mask. While some recycling methods exist, such as pyrolysis and chemical recycling, the process is more complex compared to the recycling of traditional FR-4 PCBs. Proper disposal and adherence to environmental regulations are essential when dealing with end-of-life Teflon PCBs.
Conclusion
Teflon PCBs offer a unique combination of properties that make them an excellent choice for high-frequency, high-temperature, and chemically demanding applications. Their superior dielectric properties, thermal stability, chemical resistance, and low moisture absorption enable reliable performance in challenging environments. From aerospace and military electronics to medical devices and industrial instruments, Teflon PCBs find use in a wide range of industries.
While the manufacturing process of Teflon PCBs differs from that of traditional FR-4 PCBs and may present some challenges, the benefits they offer justify their use in specific applications. As technology advances and the demand for high-performance electronics grows, Teflon PCBs will continue to play a crucial role in enabling the development of cutting-edge devices and systems.
When considering the use of Teflon PCBs, it is essential to carefully evaluate the specific requirements of the application, such as frequency, temperature range, and environmental conditions. Collaborating with experienced PCB manufacturers and designers can help ensure the successful implementation of Teflon PCBs in your projects.
As the electronics industry evolves, innovations in materials and manufacturing processes may further enhance the capabilities of Teflon PCBs. Continued research and development efforts will likely lead to new applications and improved performance, solidifying the position of Teflon as a valuable material in the world of PCBs.
No responses yet