What is Surface-mount technology?
Surface-mount technology is an advanced method of manufacturing electronic circuits wherein the components are mounted directly onto the surface of a printed circuit board. The components used in this technology are referred to as surface-mount devices (SMDs). These components are typically smaller than their through-hole counterparts and have either small leads or no leads at all.
Advantages of SMT over Through-Hole Technology
Aspect | Surface-Mount Technology | Through-Hole Technology |
---|---|---|
Component Size | Smaller components, allowing for more compact designs | Larger components, limiting the density of the PCB |
PCB size | Smaller PCBs due to increased component density | Larger PCBs required to accommodate through-hole components |
Assembly Speed | Faster assembly process using automated equipment | Slower assembly process, often requiring manual intervention |
Component Placement | Components can be placed on both sides of the PCB | Components typically placed on only one side of the PCB |
Reliability | Higher reliability due to smaller size and less susceptibility to mechanical stress | Lower reliability due to larger size and increased susceptibility to mechanical stress |
Cost | Lower cost for high-volume production due to automation | Higher cost for high-volume production due to manual assembly |
The advantages of SMT have made it the preferred method for manufacturing electronic circuits in various industries, including consumer electronics, telecommunications, aerospace, and automotive.
The SMT Manufacturing Process
The surface-mount technology manufacturing process involves several steps, each of which is crucial to ensuring the quality and reliability of the final product.
1. PCB Design and Fabrication
The first step in the SMT manufacturing process is the design and fabrication of the printed circuit board. The PCB design is created using computer-aided design (CAD) software, which allows engineers to layout the circuit and determine the placement of components. Once the design is finalized, the PCB is fabricated using a variety of methods, such as etching, drilling, and plating.
2. Solder Paste Application
After the PCB is fabricated, a thin layer of solder paste is applied to the pads where the surface-mount components will be placed. This is typically done using a stencil printing process, in which a metal stencil with openings corresponding to the component pads is placed over the PCB. Solder paste is then spread over the stencil, filling the openings and depositing the paste onto the pads.
3. Component Placement
Once the solder paste is applied, the surface-mount components are placed onto the PCB using automated pick-and-place machines. These machines use a variety of methods, such as vacuum nozzles or grippers, to pick up the components from reels or trays and place them accurately on the PCB.
4. Reflow Soldering
After the components are placed, the PCB undergoes a reflow soldering process. In this process, the PCB is heated in a reflow oven, causing the solder paste to melt and form a bond between the component leads and the PCB pads. The temperature profile of the reflow process is carefully controlled to ensure proper solder joint formation and to prevent damage to the components.
5. Inspection and Testing
Once the reflow soldering process is complete, the PCB undergoes various inspection and testing procedures to ensure the quality and functionality of the assembled circuit. This may include automated optical inspection (AOI), X-ray inspection, and in-circuit testing (ICT).
Applications of Surface-Mount Technology
Surface-mount technology has revolutionized the electronics industry, enabling the production of smaller, faster, and more reliable electronic devices. Some of the key applications of SMT include:
1. Consumer Electronics
SMT is widely used in the production of consumer electronics, such as smartphones, tablets, laptops, and wearables. The compact size and high component density achievable with SMT allow for the creation of sleek and powerful devices that meet the demands of today’s consumers.
2. Telecommunications
The telecommunications industry relies heavily on surface-mount technology for the production of network infrastructure, such as routers, switches, and base stations. SMT enables the creation of high-performance, reliable equipment that can withstand the rigors of continuous operation.
3. Automotive Electronics
As vehicles become increasingly complex and reliant on electronic systems, surface-mount technology has become essential for the production of automotive electronics. SMT is used in the manufacture of various automotive components, such as engine control units, infotainment systems, and advanced driver assistance systems (ADAS).
4. Medical Devices
Surface-mount technology is also used in the production of medical devices, such as implantable pacemakers, hearing aids, and diagnostic equipment. The small size and high reliability of SMT Components make them ideal for use in these critical applications.
5. Aerospace and Defense
The aerospace and defense industries require electronic systems that can withstand extreme environmental conditions and meet stringent reliability requirements. Surface-mount technology is used extensively in these industries for the production of avionics, guidance systems, and communication equipment.
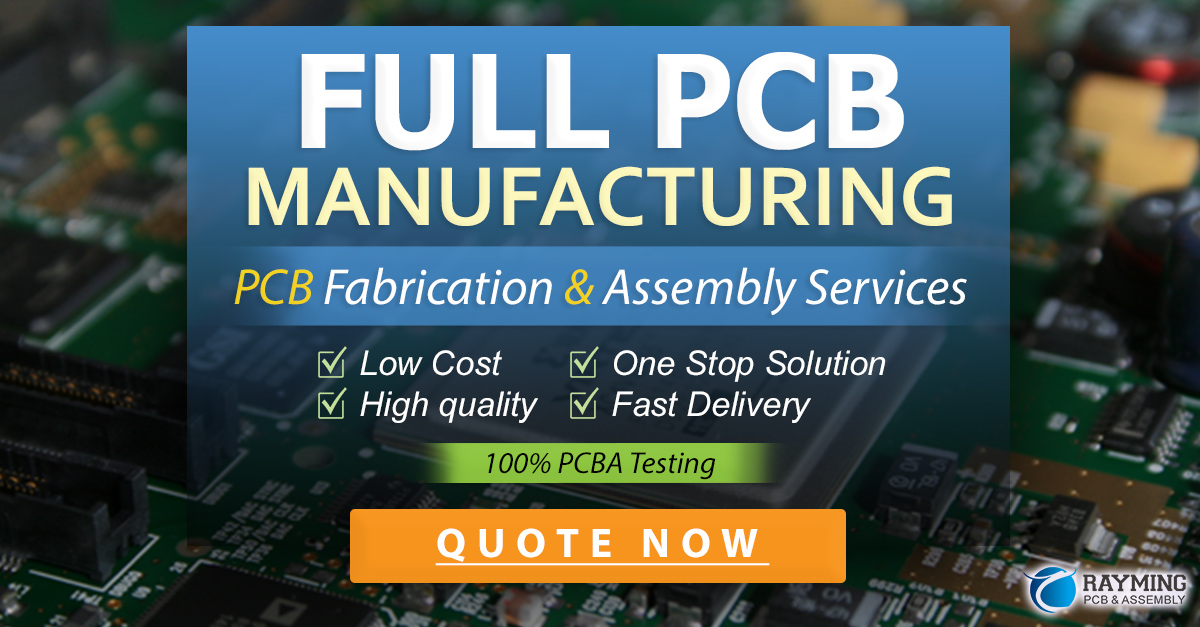
Future Trends in Surface-Mount Technology
As the electronics industry continues to evolve, surface-mount technology is expected to advance in several key areas:
1. Miniaturization
The trend towards miniaturization is expected to continue, with smaller and more compact surface-mount components being developed to enable the creation of even more compact and powerful electronic devices.
2. Advanced Packaging Technologies
New packaging technologies, such as system-in-package (SiP) and package-on-package (PoP), are being developed to further increase the density and functionality of surface-mount components.
3. Flexible and Stretchable Electronics
Surface-mount technology is being adapted for use in flexible and stretchable electronics, enabling the creation of wearable devices, smart textiles, and other innovative applications.
4. Increased Automation
As the demand for electronic devices continues to grow, there will be an increasing focus on automation in the SMT manufacturing process to improve efficiency, reduce costs, and ensure consistent quality.
Frequently Asked Questions (FAQ)
1. What is the difference between surface-mount technology and through-hole technology?
Surface-mount technology involves mounting components directly onto the surface of a printed circuit board, while through-hole technology involves inserting component leads through holes in the PCB and soldering them on the opposite side.
2. What are the advantages of using surface-mount technology?
The advantages of using surface-mount technology include smaller component sizes, increased component density on PCBs, faster assembly processes, improved reliability, and lower costs for high-volume production.
3. What are some common applications of surface-mount technology?
Surface-mount technology is widely used in the production of consumer electronics, telecommunications equipment, automotive electronics, medical devices, and aerospace and defense systems.
4. How does the reflow soldering process work in SMT manufacturing?
In the reflow soldering process, the PCB with components placed on solder paste is heated in a reflow oven. The solder paste melts and forms a bond between the component leads and the PCB pads. The temperature profile of the reflow process is carefully controlled to ensure proper solder joint formation.
5. What are some future trends in surface-mount technology?
Future trends in surface-mount technology include continued miniaturization of components, the development of advanced packaging technologies, the adaptation of SMT for flexible and stretchable electronics, and increased automation in the manufacturing process.
In conclusion, surface-mount technology has revolutionized the electronics industry, enabling the production of smaller, faster, and more reliable electronic devices. As the demand for these devices continues to grow, SMT will continue to evolve and adapt to meet the ever-changing needs of the industry.
No responses yet