Introduction to Rogers substrate
Rogers substrate is a high-performance material widely used in the electronics industry for the fabrication of printed circuit boards (PCBs) and other electronic components. Developed by Rogers Corporation, these substrates are known for their excellent electrical, thermal, and mechanical properties, making them ideal for various applications, including high-frequency communications, automotive electronics, and aerospace systems.
Key Properties of Rogers Substrate
- Low Dielectric Constant and Loss Tangent
- High Thermal conductivity
- Excellent Dimensional Stability
- Mechanical Strength and Durability
- Chemical Resistance
Types of Rogers Substrate Materials
Rogers RT/duroid® Laminates
Rogers RT/duroid® laminates are high-frequency materials designed for applications that require low dielectric loss and controlled dielectric constant. These laminates are made from PTFE (polytetrafluoroethylene) reinforced with glass microfibers, offering excellent electrical properties and dimensional stability.
Some popular Rogers RT/duroid® laminates include:
Product | Dielectric Constant | Dissipation Factor | Thermal Conductivity (W/m·K) |
---|---|---|---|
RT/duroid 5870 | 2.33 | 0.0012 | 0.22 |
RT/duroid 5880 | 2.20 | 0.0009 | 0.20 |
RT/duroid 6002 | 2.94 | 0.0012 | 0.60 |
RT/duroid 6006 | 6.15 | 0.0027 | 0.55 |
Rogers RO4000® Series Laminates
The Rogers RO4000® series laminates are designed for high-frequency applications that require low loss and controlled dielectric constant. These laminates are made from a hydrocarbon ceramic material reinforced with glass fabric, offering excellent electrical and mechanical properties.
Some popular Rogers RO4000® series laminates include:
Product | Dielectric Constant | Dissipation Factor | Thermal Conductivity (W/m·K) |
---|---|---|---|
RO4003C™ | 3.38 | 0.0027 | 0.71 |
RO4350B™ | 3.48 | 0.0037 | 0.69 |
RO4360G2™ | 6.15 | 0.0038 | 0.66 |
Rogers TMM® Laminates
Rogers TMM® laminates are ceramic thermoset polymer composite materials designed for high-frequency applications that require a high dielectric constant and low loss. These laminates offer excellent electrical and mechanical properties, making them suitable for a wide range of applications.
Some popular Rogers TMM® laminates include:
Product | Dielectric Constant | Dissipation Factor | Thermal Conductivity (W/m·K) |
---|---|---|---|
TMM3 | 3.27 | 0.0020 | 0.50 |
TMM4 | 4.50 | 0.0020 | 0.50 |
TMM6 | 6.00 | 0.0023 | 0.50 |
TMM10 | 9.20 | 0.0022 | 0.50 |
Applications of Rogers Substrate Materials
High-Frequency Communications
Rogers substrate materials are extensively used in high-frequency communication systems, such as:
- 5G Networks
- Wireless Base Stations
- Satellite Communications
- Radar Systems
- Microwave Antennas
The low dielectric loss and controlled dielectric constant of Rogers substrates ensure high signal integrity and minimal signal attenuation, making them ideal for these applications.
Automotive Electronics
The automotive industry has seen a significant increase in the use of advanced electronic systems, such as:
- Advanced Driver Assistance Systems (ADAS)
- In-Vehicle Infotainment (IVI) Systems
- Vehicle-to-Vehicle (V2V) Communication
- Vehicle-to-Infrastructure (V2I) Communication
Rogers substrate materials provide the necessary performance and reliability for these automotive electronic systems, ensuring smooth operation in harsh environments.
Aerospace and Defense
Rogers substrate materials are used in various aerospace and defense applications, including:
- Avionics Systems
- Radar Systems
- Satellite Communications
- Military Communications Equipment
The high thermal conductivity and dimensional stability of Rogers substrates make them suitable for these demanding applications, where reliability and performance are critical.
Medical Electronics
Rogers substrate materials are also used in medical electronic devices, such as:
- Implantable Devices
- Medical Imaging Equipment
- Wireless Medical Sensors
- Wearable Medical Devices
The biocompatibility and high-frequency performance of Rogers substrates make them suitable for these medical applications, ensuring patient safety and accurate data transmission.
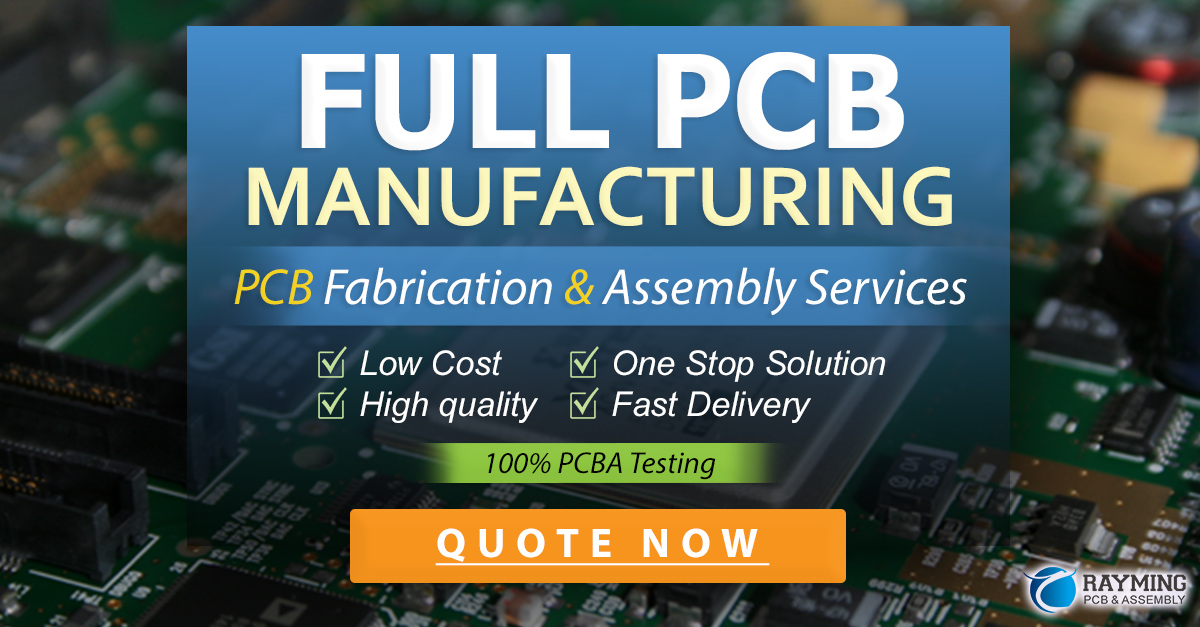
Manufacturing Process of Rogers Substrate Materials
The manufacturing process of Rogers substrate materials involves several steps, including:
- Raw Material Preparation
- Impregnation and Lamination
- Curing
- Copper Cladding
- Quality Control and Testing
Each step is carefully controlled to ensure consistent quality and performance of the final product.
Advantages of Using Rogers Substrate Materials
- Improved Signal Integrity
- Reduced Signal Attenuation
- Enhanced Thermal Management
- Increased Reliability and Durability
- Compatibility with Advanced Manufacturing Processes
Challenges and Future Developments
Despite the numerous advantages of Rogers substrate materials, there are still some challenges that need to be addressed, such as:
- Cost: Rogers substrates are generally more expensive than traditional FR-4 materials, which can limit their widespread adoption in cost-sensitive applications.
- Processing: Some Rogers substrate materials may require specialized processing techniques, which can increase manufacturing complexity and cost.
- Environmental Concerns: The use of PTFE in some Rogers substrate materials has raised concerns about their environmental impact, prompting the development of more eco-friendly alternatives.
Future developments in Rogers substrate materials are expected to focus on:
- Improving Cost-Effectiveness: Researchers are working on developing lower-cost Rogers substrate materials without compromising performance.
- Enhancing Environmental Sustainability: Efforts are being made to develop more environmentally friendly Rogers substrate materials, such as halogen-free and recyclable options.
- Expanding Application Areas: As technology advances, Rogers substrate materials are expected to find new applications in emerging fields, such as flexible electronics and the Internet of Things (IoT).
Frequently Asked Questions (FAQ)
-
Q: What are the main advantages of using Rogers substrate materials over traditional FR-4 materials?
A: Rogers substrate materials offer several advantages over traditional FR-4 materials, including lower dielectric loss, controlled dielectric constant, higher thermal conductivity, and better dimensional stability. These properties make Rogers substrates ideal for high-frequency applications and challenging environments. -
Q: Can Rogers substrate materials be used for flexible electronics applications?
A: While most Rogers substrate materials are designed for rigid PCBs, some products, such as the Rogers ULTRALAM® series, are specifically developed for flexible electronics applications. These materials combine the high-performance properties of Rogers substrates with the flexibility required for advanced electronic devices. -
Q: Are Rogers substrate materials compatible with standard PCB manufacturing processes?
A: Yes, most Rogers substrate materials are compatible with standard PCB manufacturing processes, such as etching, drilling, and plating. However, some materials may require specialized processing techniques or equipment to achieve optimal results. -
Q: How do I select the right Rogers substrate material for my application?
A: Selecting the right Rogers substrate material depends on various factors, such as the required dielectric constant, loss tangent, thermal conductivity, and mechanical properties. It is essential to consult with Rogers Corporation or an authorized distributor to determine the most suitable material for your specific application. -
Q: Are Rogers substrate materials RoHS compliant?
A: Most Rogers substrate materials are RoHS compliant, meaning they meet the restrictions on the use of certain hazardous substances in electrical and electronic equipment. However, it is essential to check the compliance status of specific products with Rogers Corporation or an authorized distributor.
Conclusion
Rogers substrate materials have revolutionized the electronics industry by providing high-performance solutions for challenging applications. With their excellent electrical, thermal, and mechanical properties, Rogers substrates have become the material of choice for high-frequency communications, automotive electronics, aerospace systems, and medical devices.
As technology continues to advance, Rogers Corporation remains committed to developing innovative substrate materials that meet the evolving needs of the electronics industry. By addressing challenges such as cost, environmental sustainability, and expanding application areas, Rogers substrate materials are poised to play a crucial role in shaping the future of electronics.
No responses yet