Overview of Rogers PCB Materials
Rogers offers a wide range of PCB Materials designed for specific applications and performance requirements. These materials are known for their excellent electrical, thermal, and mechanical properties, making them ideal for high-frequency, high-speed, and high-reliability applications.
The most popular Rogers PCB materials include:
- RO4000 Series: A hydrocarbon ceramic laminate with low dielectric loss and stable electrical properties.
- RO3000 Series: A ceramic-filled PTFE composite with low dielectric constant and loss tangent.
- RT/duroid Series: A PTFE-based laminate with low dielectric constant and excellent high-frequency performance.
- TMM Series: A thermoset ceramic laminate with low thermal expansion and high thermal conductivity.
Advantages of Using Rogers PCB Materials
Rogers PCB materials offer several advantages over traditional FR-4 laminates, making them the preferred choice for high-performance applications. Some of the key benefits include:
1. Low Dielectric Constant and Loss Tangent
Rogers materials have low dielectric constant (Dk) and loss tangent (Df) values, which minimize signal loss and distortion at high frequencies. This enables the design of high-speed digital circuits and high-frequency RF applications.
Material | Dielectric Constant (Dk) | Loss Tangent (Df) |
---|---|---|
RO4350B | 3.48 @ 10 GHz | 0.0037 @ 10 GHz |
RO3003 | 3.00 @ 10 GHz | 0.0010 @ 10 GHz |
RT/duroid 5880 | 2.20 @ 10 GHz | 0.0009 @ 10 GHz |
2. Stable Electrical Properties
Rogers materials maintain their electrical properties over a wide range of frequencies and temperatures. This stability ensures consistent performance and reliability in demanding environments.
3. Excellent Thermal Management
Many Rogers materials have high thermal conductivity and low thermal expansion, which helps in dissipating heat efficiently. This is crucial for high-power applications where thermal management is a critical factor.
4. Mechanical Robustness
Rogers PCB materials offer excellent mechanical strength, durability, and dimensional stability. They can withstand the stresses of manufacturing processes and harsh operating conditions.
Applications of Rogers PCB
Rogers PCB materials find applications in various industries and products, including:
- Wireless Communication:
- 5G infrastructure
- Cellular base stations
- Satellite communication
-
IoT devices
-
Aerospace and Defense:
- Radar systems
- Avionics
-
Military communication equipment
-
Automotive Electronics:
- Advanced driver assistance systems (ADAS)
- Radar sensors
-
Vehicle-to-vehicle (V2V) communication
-
Industrial Electronics:
- High-speed data acquisition systems
- Industrial automation and control
- Medical imaging equipment
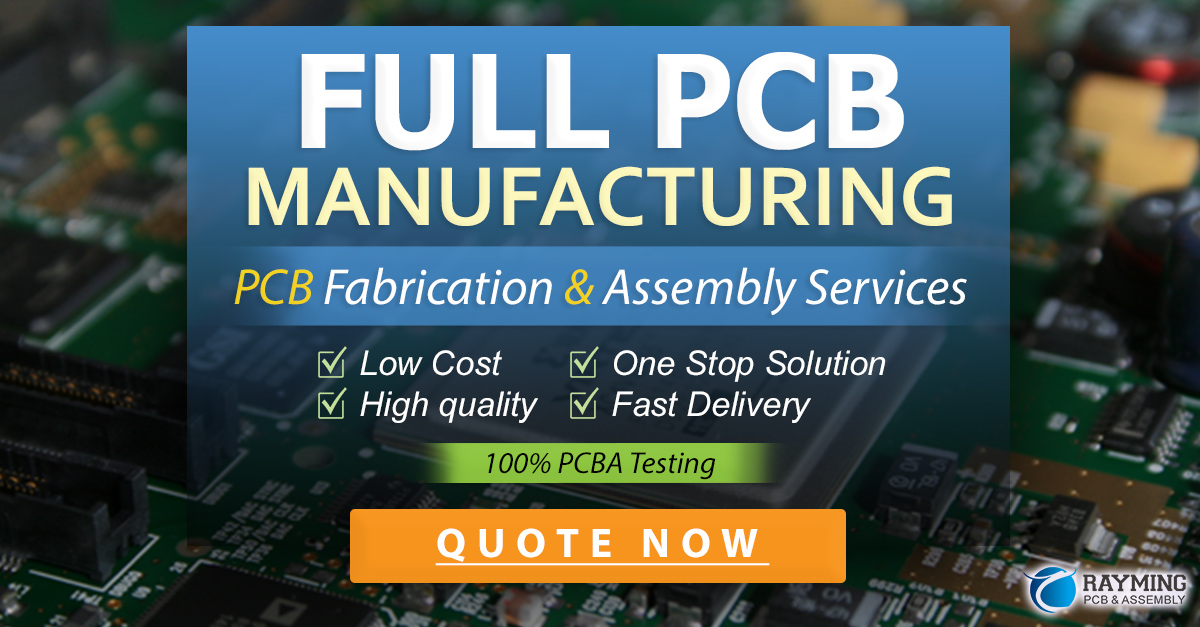
Designing with Rogers PCB Materials
When designing PCBs using Rogers materials, there are several considerations to keep in mind:
1. Material Selection
Choose the appropriate Rogers material based on the specific application requirements, such as frequency range, dielectric properties, thermal management, and mechanical constraints.
2. Layout and Routing
Follow proper layout and routing guidelines to optimize signal integrity and minimize losses. This includes controlled impedance routing, ground plane design, and via placement.
3. Manufacturing Process
Work closely with the PCB manufacturer to ensure they have experience and capability in handling Rogers materials. Special processing techniques may be required, such as controlled depth drilling, plasma etching, and precise lamination.
4. Assembly and Soldering
Consider the specific requirements for assembling and soldering components on Rogers PCBs. High-temperature solder masks and appropriate soldering profiles may be necessary to avoid damaging the material.
Frequently Asked Questions (FAQ)
1. What is the difference between Rogers PCB and FR-4 PCB?
Rogers PCB materials have superior electrical, thermal, and mechanical properties compared to traditional FR-4 laminates. They offer lower dielectric loss, higher thermal conductivity, and better high-frequency performance, making them suitable for demanding applications.
2. Can I use Rogers PCB for low-frequency applications?
While Rogers PCB materials are primarily designed for high-frequency applications, they can also be used for low-frequency projects that require stable electrical properties, low losses, and high reliability.
3. Are Rogers PCBs more expensive than FR-4 PCBs?
Yes, Rogers PCB materials are generally more expensive than FR-4 laminates due to their advanced properties and specialized manufacturing processes. However, the enhanced performance and reliability they offer often justify the higher cost for critical applications.
4. How do I select the right Rogers PCB material for my application?
To select the appropriate Rogers PCB material, consider factors such as the operating frequency range, dielectric constant and loss requirements, thermal management needs, and mechanical constraints. Consult the Rogers material datasheets and application notes, and work with your PCB manufacturer to make an informed decision.
5. Can I mix Rogers PCB materials with other laminates in the same PCB stack-up?
Yes, it is possible to use Rogers PCB materials in combination with other laminates, such as FR-4, in a hybrid stack-up. This allows for optimizing the performance and cost of the PCB by using Rogers materials only where necessary. However, careful design and manufacturing considerations are required to ensure proper lamination and reliability.
Conclusion
Rogers PCB materials offer exceptional performance and reliability for high-frequency, high-speed, and high-reliability applications. With their low dielectric loss, stable electrical properties, and excellent thermal management, Rogers materials enable the design of advanced PCBs for various industries, including wireless communication, aerospace, defense, automotive, and industrial electronics.
When designing with Rogers PCB materials, it is essential to carefully consider the material selection, layout and routing guidelines, manufacturing processes, and assembly requirements. By working closely with experienced PCB manufacturers and following best practices, designers can leverage the full potential of Rogers materials and create high-performance electronic products.
As technology continues to advance and the demand for high-frequency applications grows, Rogers PCB materials will play an increasingly crucial role in shaping the future of electronic design and innovation.
No responses yet