Properties of Rogers materials
Rogers materials exhibit several unique properties that set them apart from traditional PCB Materials, such as FR-4. These properties include:
Low Dielectric Constant and Loss Tangent
Rogers materials have a low dielectric constant (Dk) and loss tangent (Df), which help to minimize signal loss and distortion at high frequencies. This property is crucial for maintaining signal integrity in high-speed digital and RF applications.
Thermal Stability
Rogers materials maintain their electrical and mechanical properties over a wide temperature range, making them suitable for use in harsh environments. They have a low coefficient of thermal expansion (CTE), which helps to minimize stress and warping of the PCB during temperature fluctuations.
Mechanical Strength
Rogers materials have excellent mechanical strength and durability, which helps to ensure the longevity and reliability of the PCB. They are resistant to cracking, delamination, and other mechanical failures that can occur in high-stress applications.
Moisture Resistance
Rogers materials have low moisture absorption, which helps to prevent the degradation of electrical properties and the growth of unwanted organisms on the PCB surface.
Types of Rogers Materials
Rogers Corporation offers a wide range of materials tailored for specific applications and performance requirements. Some of the most common Rogers materials include:
RO3000 Series
The RO3000 series is a family of high-frequency laminates designed for use in commercial wireless communication systems, automotive radar, and other RF applications. These materials have a low dielectric constant and loss tangent, making them ideal for applications requiring low insertion loss and high signal integrity.
Material | Dielectric Constant (Dk) | Loss Tangent (Df) | Applications |
---|---|---|---|
RO3003 | 3.00 ± 0.04 | 0.0013 | Wireless communication, automotive radar |
RO3006 | 6.15 ± 0.15 | 0.0025 | Wireless communication, automotive radar |
RO3010 | 10.2 ± 0.30 | 0.0035 | Wireless communication, automotive radar |
RO4000 Series
The RO4000 series is a family of hydrocarbon ceramic laminates designed for use in high-performance RF and microwave applications. These materials have a low dielectric constant, low loss tangent, and excellent thermal stability, making them suitable for use in base station antennas, power amplifiers, and other demanding RF applications.
Material | Dielectric Constant (Dk) | Loss Tangent (Df) | Applications |
---|---|---|---|
RO4350B | 3.48 ± 0.05 | 0.0037 | Base station antennas, power amplifiers |
RO4360G2 | 6.15 ± 0.15 | 0.0038 | Microwave and millimeter-wave applications |
RO4003C | 3.38 ± 0.05 | 0.0027 | Automotive radar, high-speed digital |
RT/duroid Series
The RT/duroid series is a family of PTFE (polytetrafluoroethylene) based laminates designed for use in high-frequency and microwave applications. These materials have a very low dielectric constant and loss tangent, making them ideal for use in radar systems, satellite communication, and other applications requiring the lowest possible signal loss.
Material | Dielectric Constant (Dk) | Loss Tangent (Df) | Applications |
---|---|---|---|
RT/duroid 5870 | 2.33 ± 0.02 | 0.0012 | Satellite communication, radar systems |
RT/duroid 5880 | 2.20 ± 0.02 | 0.0009 | Satellite communication, radar systems |
RT/duroid 6002 | 2.94 ± 0.04 | 0.0012 | High-frequency and microwave applications |
Applications of Rogers Materials
Rogers materials find applications in a wide range of industries and applications, including:
Telecommunications
In the telecommunications industry, Rogers materials are used in the manufacturing of PCBs for base station antennas, power amplifiers, and other high-frequency components. The low dielectric constant and loss tangent of these materials help to minimize signal loss and ensure high performance in demanding wireless communication applications.
Aerospace and Defense
Rogers materials are widely used in the aerospace and defense industries for radar systems, satellite communication, and other mission-critical applications. The excellent thermal stability and mechanical strength of these materials make them suitable for use in harsh environments and extreme temperature conditions.
Automotive
In the automotive industry, Rogers materials are used in the manufacturing of PCBs for automotive radar systems, which are used for collision avoidance and autonomous driving applications. The low dielectric constant and loss tangent of these materials help to ensure accurate and reliable radar performance.
High-Speed Digital
Rogers materials are also used in high-speed digital applications, such as high-performance computing and data centers. The low dielectric constant and excellent thermal stability of these materials help to minimize signal distortion and ensure reliable performance in high-speed digital circuits.
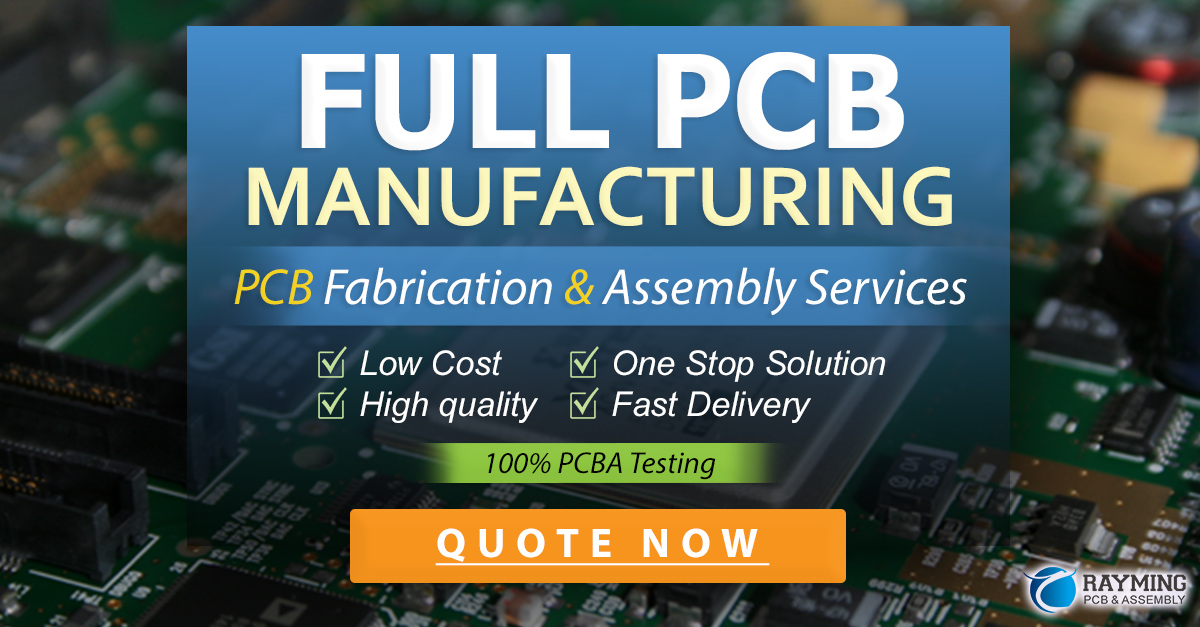
Manufacturing Process
The manufacturing process for Rogers materials involves several steps to ensure the highest quality and performance of the resulting PCB. The process typically includes:
-
Material selection: The appropriate Rogers material is selected based on the specific application and performance requirements.
-
Lamination: The Rogers material is laminated to a copper foil using heat and pressure to create a Copper-Clad Laminate.
-
Etching: The copper-clad laminate is then etched to create the desired circuit pattern on the PCB surface.
-
Drilling: Holes are drilled in the PCB for component mounting and interconnection.
-
Plating: The drilled holes are plated with copper to create electrical connections between the layers of the PCB.
-
Solder mask application: A solder mask is applied to the PCB surface to protect the circuits and prevent short circuits during soldering.
-
Surface finish: A surface finish, such as HASL (Hot Air Solder Leveling) or ENIG (Electroless Nickel Immersion Gold), is applied to the exposed copper surfaces to prevent oxidation and improve solderability.
-
Inspection and testing: The finished PCB is inspected and tested to ensure that it meets the required specifications and performance standards.
Advantages of Using Rogers Materials
Using Rogers materials in PCB manufacturing offers several advantages over traditional materials, such as FR-4. These advantages include:
-
Improved signal integrity: The low dielectric constant and loss tangent of Rogers materials help to minimize signal loss and distortion, ensuring high signal integrity in high-frequency and high-speed applications.
-
Enhanced thermal stability: Rogers materials maintain their electrical and mechanical properties over a wide temperature range, making them suitable for use in harsh environments and extreme temperature conditions.
-
Increased reliability: The excellent mechanical strength and moisture resistance of Rogers materials help to ensure the longevity and reliability of the PCB, reducing the risk of failure in demanding applications.
-
Better performance: The unique properties of Rogers materials enable the design and manufacturing of high-performance PCBs that can operate at higher frequencies and speeds than traditional materials.
-
Cost-effective: While Rogers materials may have a higher initial cost than traditional materials, their superior performance and reliability can result in lower overall system costs and reduced maintenance requirements over the lifetime of the product.
Frequently Asked Questions (FAQ)
Q1: What is the difference between Rogers materials and FR-4?
A1: Rogers materials are high-performance dielectric materials designed for use in high-frequency and high-speed applications, while FR-4 is a standard glass-reinforced epoxy laminate material used in general-purpose PCBs. Rogers materials have a lower dielectric constant and loss tangent, better thermal stability, and higher mechanical strength compared to FR-4.
Q2: Can Rogers materials be used for multilayer PCBs?
A2: Yes, Rogers materials can be used for multilayer PCBs. Many Rogers materials, such as the RO4000 series, are available in a range of thicknesses and can be laminated together to create multilayer PCBs with excellent electrical and thermal performance.
Q3: How do I select the right Rogers material for my application?
A3: The selection of the appropriate Rogers material depends on the specific requirements of your application, such as the operating frequency, dielectric constant, loss tangent, and thermal requirements. Consult the Rogers Corporation product datasheets and application notes, or contact a Rogers technical representative for guidance on selecting the most suitable material for your application.
Q4: Are Rogers materials compatible with standard PCB manufacturing processes?
A4: Yes, Rogers materials are compatible with standard PCB manufacturing processes, such as etching, drilling, and plating. However, some Rogers materials may require special handling or processing techniques to ensure optimal performance. It is essential to follow the manufacturer’s guidelines and work with an experienced PCB fabricator when using Rogers materials.
Q5: How do I manage the higher cost of Rogers materials in my PCB design?
A5: While Rogers materials may have a higher initial cost than traditional materials, their superior performance and reliability can result in lower overall system costs and reduced maintenance requirements over the lifetime of the product. To manage costs, consider using Rogers materials only in critical areas of the PCB where their unique properties are essential, and using lower-cost materials in less demanding areas. Additionally, work with your PCB fabricator to optimize the design and manufacturing process to minimize material waste and reduce production costs.
Conclusion
Rogers materials are high-performance dielectric materials that offer unique properties and benefits for demanding high-frequency and high-speed electronic applications. With their low dielectric constant and loss tangent, excellent thermal stability, and mechanical strength, Rogers materials enable the design and manufacturing of high-performance PCBs that can operate reliably in harsh environments and extreme temperature conditions.
When selecting Rogers materials for your application, it is essential to consider the specific requirements of your design, such as the operating frequency, dielectric constant, loss tangent, and thermal requirements. By working with an experienced PCB fabricator and following the manufacturer’s guidelines, you can effectively integrate Rogers materials into your PCB design and manufacturing process to achieve optimal performance and reliability.
As technology continues to advance and the demand for high-performance electronic systems grows, Rogers materials will continue to play a critical role in enabling the development of cutting-edge applications across a wide range of industries, from telecommunications and automotive to aerospace and defense.
No responses yet