What is PTFE?
PTFE, commonly known by the brand name Teflon, is a synthetic fluoropolymer of tetrafluoroethylene. It is a highly stable and inert material that possesses a unique combination of properties, making it an ideal choice for a wide range of applications. Some of the key properties of PTFE include:
- High thermal stability
- Excellent chemical resistance
- Low coefficient of friction
- Non-stick surface
- Electrical insulation
- Low dielectric constant
- Resistance to UV and weathering
These properties make PTFE a valuable material in applications where high temperature, chemical resistance, and low friction are critical.
The Lamination Process
PTFE laminate is produced by bonding a layer of PTFE to a substrate material using various lamination techniques. The most common methods include:
-
Adhesive Lamination: In this process, a layer of adhesive is applied between the PTFE and the substrate, and the layers are bonded together under heat and pressure.
-
Heat Lamination: This method involves heating the PTFE and substrate materials to their melting points and pressing them together to form a strong bond.
-
Mechanical Lamination: This process uses mechanical means, such as stitching or riveting, to join the PTFE and substrate layers.
The choice of lamination method depends on the specific requirements of the application, such as the desired bond strength, temperature resistance, and flexibility.
Substrate Materials
PTFE laminates can be produced with a variety of substrate materials, each offering unique properties and benefits. Some of the most common substrate materials include:
-
Fiberglass: Fiberglass-reinforced PTFE laminates offer excellent dimensional stability, high strength, and good electrical insulation properties. They are commonly used in printed circuit boards (PCBs) and other electronic applications.
-
Kevlar: Kevlar-reinforced PTFE laminates provide high tensile strength, excellent tear resistance, and good dimensional stability. They are often used in aerospace and defense applications.
-
Nomex: Nomex-reinforced PTFE laminates offer high temperature resistance, excellent flame retardancy, and good electrical insulation properties. They are commonly used in high-temperature wire and cable insulation.
-
Polyimide: Polyimide-based PTFE laminates offer exceptional thermal stability, excellent chemical resistance, and high mechanical strength. They are often used in high-performance electronic applications.
-
Metal foils: PTFE-laminated metal foils, such as copper or aluminum, provide a combination of the non-stick and low-friction properties of PTFE with the electrical conductivity and heat dissipation of the metal substrate.
The choice of substrate material depends on the specific requirements of the application, such as the desired mechanical, thermal, and electrical properties.
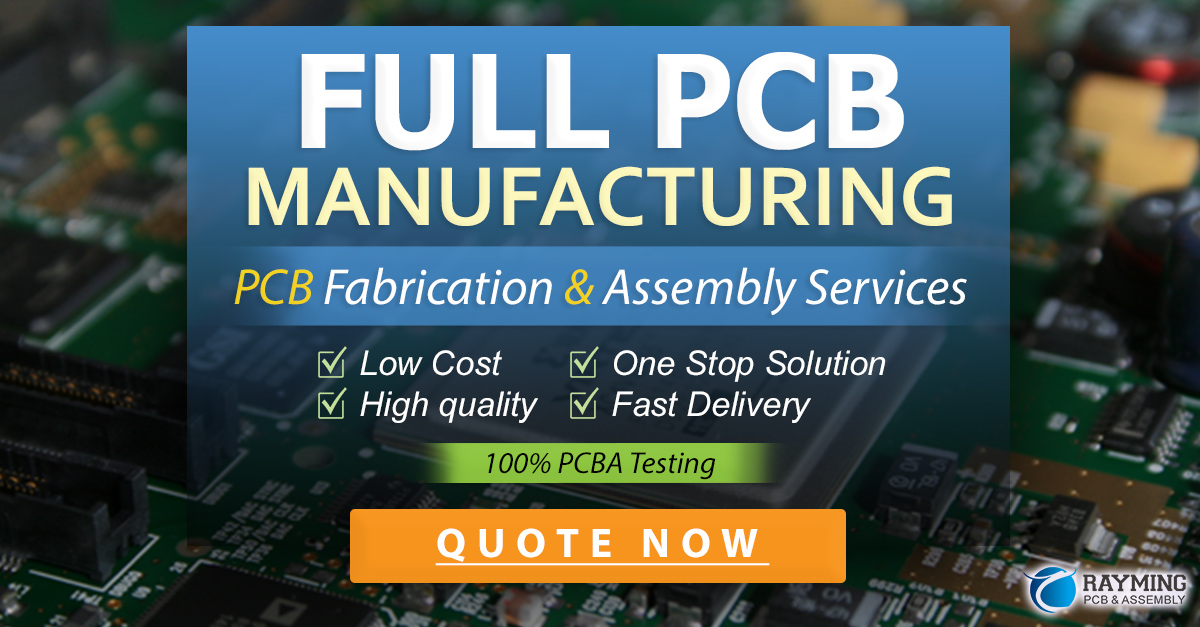
Properties of PTFE Laminates
PTFE laminates combine the unique properties of PTFE with the strength and stability of the substrate material, resulting in a composite with enhanced performance characteristics. Some of the key properties of PTFE laminates include:
-
High temperature resistance: PTFE laminates can withstand continuous operating temperatures up to 260°C (500°F) and short-term exposure to temperatures as high as 316°C (600°F).
-
Excellent chemical resistance: PTFE laminates are resistant to a wide range of chemicals, including acids, bases, solvents, and oxidizers.
-
Low coefficient of friction: The non-stick surface of PTFE provides a low coefficient of friction, reducing wear and tear on mating surfaces.
-
Electrical insulation: PTFE laminates offer excellent electrical insulation properties, with a high dielectric strength and low dielectric constant.
-
Dimensional stability: The substrate material provides dimensional stability to the PTFE laminate, reducing the risk of warping or deformation under high temperatures or mechanical stress.
-
Mechanical strength: The combination of PTFE and the substrate material results in a laminate with enhanced mechanical properties, such as tensile strength, tear resistance, and puncture resistance.
These properties make PTFE laminates suitable for a wide range of demanding applications across various industries.
Applications of PTFE Laminates
PTFE laminates find applications in numerous industries, thanks to their unique combination of properties. Some of the most common applications include:
- Aerospace and Defense:
- Aircraft wiring insulation
- Radar and antenna components
- Missile and rocket components
-
High-temperature seals and gaskets
-
Automotive:
- Fuel system components
- Brake system components
- Electrical insulation
-
Seals and gaskets
-
Electronics:
- Printed circuit boards (PCBs)
- High-frequency circuit substrates
- Insulation for wire and cable
-
Flexible heaters
-
Chemical Processing:
- Lining for tanks and vessels
- Gaskets and seals for pumps and valves
- Insulation for pipes and hoses
-
Filtration membranes
-
Food Processing:
- Non-stick conveyor belts
- Food-grade seals and gaskets
- Release sheets for baked goods
-
Insulation for ovens and fryers
-
Medical:
- Implantable devices
- Surgical instruments
- Pharmaceutical packaging
- Medical tubing and catheters
These are just a few examples of the many applications where PTFE laminates are used. The versatility and high-performance properties of PTFE laminates make them a valuable material in any application that demands chemical resistance, high temperature stability, low friction, and electrical insulation.
Advantages of PTFE Laminates
PTFE laminates offer several advantages over traditional materials in demanding applications. Some of the key benefits include:
-
Enhanced durability: The combination of PTFE and the substrate material results in a laminate with improved mechanical strength and durability, reducing the risk of failure in harsh environments.
-
Reduced maintenance: The non-stick and low-friction properties of PTFE reduce the build-up of contaminants and minimize wear and tear on mating surfaces, leading to reduced maintenance requirements.
-
Improved efficiency: The low coefficient of friction of PTFE laminates reduces energy losses due to friction, improving the overall efficiency of the system.
-
Extended service life: The high temperature resistance and chemical resistance of PTFE laminates allow them to withstand prolonged exposure to harsh conditions, extending the service life of components and systems.
-
Cost savings: The enhanced durability and extended service life of PTFE laminates can result in significant cost savings over the lifetime of the application, reducing the need for frequent replacements and maintenance.
These advantages make PTFE laminates a preferred choice in applications where reliability, efficiency, and long-term performance are critical.
Choosing the Right PTFE Laminate
When selecting a PTFE laminate for a specific application, several factors should be considered to ensure optimal performance and longevity. These factors include:
-
Temperature requirements: Consider the maximum continuous operating temperature and any short-term temperature spikes the laminate will be exposed to.
-
Chemical compatibility: Evaluate the chemical environment the laminate will be exposed to and ensure that it is compatible with the specific chemicals involved.
-
Mechanical properties: Assess the mechanical requirements of the application, such as tensile strength, tear resistance, and puncture resistance, and select a laminate with the appropriate properties.
-
Electrical requirements: Consider the electrical insulation and dielectric properties required for the application and choose a laminate that meets these requirements.
-
Substrate material: Select a substrate material that complements the properties of PTFE and meets the specific requirements of the application, such as dimensional stability, mechanical strength, or thermal conductivity.
-
Lamination method: Choose a lamination method that provides the desired bond strength and performance characteristics for the application.
By carefully considering these factors and working with a knowledgeable supplier, you can select the optimal PTFE laminate for your specific application, ensuring reliable and long-lasting performance.
PTFE Laminate Manufacturers and Suppliers
There are several leading manufacturers and suppliers of PTFE laminates, each offering a range of products designed for specific applications and industries. Some of the top PTFE laminate manufacturers and suppliers include:
-
Saint-Gobain Performance Plastics: Saint-Gobain offers a wide range of PTFE laminates under the brand names CHEMFILM, FLUOROWRAP, and NORFILM, catering to various industries, including aerospace, automotive, and electronics.
-
Rogers Corporation: Rogers Corporation provides high-performance PTFE laminates for demanding applications, such as High-Frequency PCBs, under the brand names RO3000, RO4000, and RT/duroid.
-
Taconic: Taconic offers a range of PTFE-based laminates for RF and microwave applications, including the TLY, TLX, and RF-35 series.
-
Arlon: Arlon provides PTFE laminates for high-frequency and high-speed digital applications, including the DiClad and 85NT series.
-
Isola Group: Isola Group offers a range of PTFE laminates for RF and microwave applications, including the IS400, IS600, and IS700 series.
These are just a few examples of the many manufacturers and suppliers of PTFE laminates. When selecting a supplier, consider factors such as product quality, technical support, customization options, and delivery times to ensure the best fit for your specific requirements.
Conclusion
PTFE laminates are a versatile and high-performance composite material that combines the exceptional properties of PTFE with the strength and stability of a substrate material. The unique combination of chemical resistance, high temperature stability, low friction, and electrical insulation make PTFE laminates a valuable choice in demanding applications across various industries, including aerospace, automotive, electronics, and chemical processing.
By understanding the properties, advantages, and applications of PTFE laminates, and carefully considering the specific requirements of your application, you can select the optimal PTFE laminate to ensure reliable, efficient, and long-lasting performance.
FAQs
- What is the maximum continuous operating temperature for PTFE laminates?
-
PTFE laminates can typically withstand continuous operating temperatures up to 260°C (500°F) and short-term exposure to temperatures as high as 316°C (600°F).
-
Are PTFE laminates resistant to chemicals?
-
Yes, PTFE laminates offer excellent resistance to a wide range of chemicals, including acids, bases, solvents, and oxidizers.
-
What are some common substrate materials used in PTFE laminates?
-
Common substrate materials for PTFE laminates include fiberglass, Kevlar, Nomex, polyimide, and metal foils, such as copper or aluminum.
-
How do PTFE laminates provide cost savings over traditional materials?
-
PTFE laminates offer enhanced durability and extended service life, reducing the need for frequent replacements and maintenance, which can result in significant cost savings over the lifetime of the application.
-
What factors should be considered when selecting a PTFE laminate for a specific application?
- When selecting a PTFE laminate, consider factors such as temperature requirements, chemical compatibility, mechanical properties, electrical requirements, substrate material, and lamination method to ensure optimal performance and longevity.
Property | PTFE | Fiberglass-Reinforced PTFE | Kevlar-Reinforced PTFE |
---|---|---|---|
Maximum Continuous Operating Temperature | 260°C (500°F) | 260°C (500°F) | 260°C (500°F) |
Chemical Resistance | Excellent | Excellent | Excellent |
Coefficient of Friction | Low | Low | Low |
Dielectric Strength (kV/mm) | 60-173 | 20-40 | 20-40 |
Tensile Strength (MPa) | 20-35 | 100-200 | 200-400 |
Tear Resistance | Low | High | Very High |
Dimensional Stability | Low | High | High |
This table provides a comparison of key properties for PTFE, fiberglass-reinforced PTFE, and Kevlar-reinforced PTFE laminates. It demonstrates the enhanced mechanical properties and dimensional stability offered by reinforced PTFE laminates while maintaining the excellent chemical resistance and low friction of PTFE.
No responses yet