What is Polyimide?
Polyimide is a synthetic polymer that belongs to a class of materials known as high-performance polymers. It is formed by the reaction of a dianhydride and a diamine, resulting in a polymer chain with imide linkages. The chemical structure of polyimide gives it unique properties, including:
- High thermal stability
- Excellent mechanical strength
- Superior electrical insulation
- Low dielectric constant
- Resistance to chemicals and solvents
These properties make polyimide an ideal material for various applications, including high-temperature coatings, aerospace components, and flexible electronics.
Polyimide in PCB Manufacturing
In the context of PCB manufacturing, polyimide is used as a substrate material. A substrate is the base material on which the conductive traces and components are placed to form a functional circuit board. Traditionally, FR-4, a glass-reinforced epoxy laminate, has been the most common substrate material for PCBs. However, polyimide has emerged as a superior alternative for applications that require higher performance and reliability.
Advantages of Polyimide PCBs
-
High Temperature Resistance: Polyimide can withstand temperatures up to 400°C, making it suitable for applications that involve high-temperature environments, such as automotive and aerospace electronics.
-
Dimensional Stability: Polyimide has a low coefficient of thermal expansion (CTE), which means it maintains its dimensions even when subjected to temperature variations. This dimensional stability is crucial for maintaining the integrity of the circuit board and preventing failures due to thermal stress.
-
Flexibility: Polyimide PCBs can be made flexible, allowing them to conform to various shapes and bend without breaking. This flexibility enables the design of compact and lightweight electronic devices, such as wearables and medical implants.
-
Excellent Electrical Properties: Polyimide has a low dielectric constant and high insulation resistance, which minimizes signal loss and crosstalk between the conductive traces. This makes polyimide PCBs suitable for high-frequency applications, such as radar and communication systems.
-
Chemical Resistance: Polyimide is resistant to most chemicals and solvents, making it suitable for applications that involve exposure to harsh environments, such as industrial sensors and medical devices.
Manufacturing Process of Polyimide PCBs
The manufacturing process of polyimide PCBs is similar to that of standard FR-4 PCBs, with a few key differences:
-
Substrate Preparation: The polyimide substrate is cleaned and treated to improve its adhesion properties. This step is crucial for ensuring a strong bond between the substrate and the conductive traces.
-
Copper Cladding: A thin layer of copper is laminated onto the polyimide substrate using heat and pressure. The copper layer serves as the conductive material for the circuit traces.
-
Patterning: The desired circuit pattern is transferred onto the copper layer using photolithography. This involves applying a photoresist coating, exposing it to UV light through a patterned mask, and developing the resist to reveal the desired pattern.
-
Etching: The exposed copper is etched away using a chemical solution, leaving behind the desired circuit traces.
-
Protective Coating: A protective coating, such as soldermask, is applied to the PCB to protect the copper traces from oxidation and mechanical damage.
-
Component Assembly: Electronic components are soldered onto the PCB using surface mount technology (SMT) or through-hole mounting.
Applications of Polyimide PCBs
Polyimide PCBs find applications in various industries where high performance and reliability are critical. Some of the key applications include:
-
Aerospace and Defense: Polyimide PCBs are used in avionics, satellite systems, and military electronics due to their ability to withstand extreme temperatures and vibrations.
-
Automotive: In the automotive industry, polyimide PCBs are used in engine control units, sensor systems, and power electronics, where they are exposed to high temperatures and harsh environmental conditions.
-
Medical Devices: Polyimide’s biocompatibility and flexibility make it suitable for medical implants, such as pacemakers and hearing aids. Its chemical resistance also makes it ideal for diagnostic equipment and surgical tools.
-
Industrial Electronics: Polyimide PCBs are used in industrial control systems, power electronics, and sensors that operate in harsh environments, such as oil and gas, mining, and chemical processing.
-
Consumer Electronics: With the increasing demand for flexible and wearable electronics, polyimide PCBs are finding applications in smartwatches, fitness trackers, and virtual reality devices.
Challenges and Future Trends
Despite its superior properties, polyimide PCBs face some challenges that need to be addressed for their widespread adoption:
-
Cost: Polyimide substrates are more expensive than traditional FR-4 laminates, which can increase the overall cost of PCB manufacturing. However, the long-term benefits of using polyimide, such as improved reliability and longer product life, can offset the initial cost.
-
Processing Complexity: The manufacturing process of polyimide PCBs requires specialized equipment and expertise, which can be a barrier for some PCB manufacturers. However, with the increasing demand for high-performance PCBs, more manufacturers are investing in polyimide processing capabilities.
-
Recycling: Like most polymers, polyimide is not easily recyclable, which raises concerns about its environmental impact. Research is ongoing to develop recycling methods and biodegradable alternatives to polyimide.
The future of polyimide PCBs looks promising, with several trends driving their adoption:
-
Miniaturization: As electronic devices become smaller and more compact, the demand for high-density interconnect (HDI) PCBs is increasing. Polyimide’s dimensional stability and low dielectric constant make it an ideal substrate for HDI PCBs.
-
5G and High-Frequency Applications: The rollout of 5G networks and the increasing use of high-frequency communication systems are driving the demand for low-loss PCB materials. Polyimide’s excellent electrical properties make it a suitable choice for these applications.
-
Flexible and Wearable Electronics: The market for flexible and wearable electronics is growing rapidly, and polyimide’s flexibility and biocompatibility make it a key material for these applications.
-
Sustainable Electronics: With the increasing focus on sustainability, there is a growing interest in developing eco-friendly PCB materials. Researchers are exploring the use of bio-based polyimides and other sustainable alternatives to conventional polyimide.
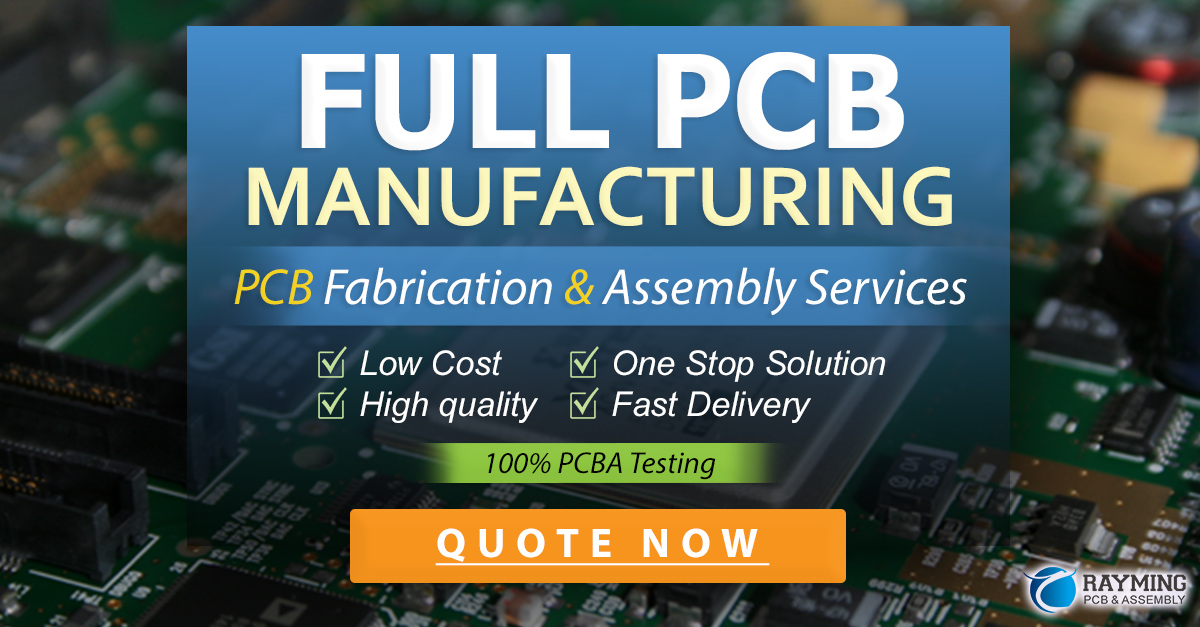
Frequently Asked Questions (FAQ)
-
Q: What is the maximum operating temperature of polyimide PCBs?
A: Polyimide PCBs can withstand temperatures up to 400°C, making them suitable for high-temperature applications. -
Q: Can polyimide PCBs be used in medical implants?
A: Yes, polyimide’s biocompatibility and flexibility make it suitable for medical implants, such as pacemakers and hearing aids. -
Q: Are polyimide PCBs more expensive than traditional FR-4 PCBs?
A: Yes, polyimide substrates are more expensive than FR-4 laminates, which can increase the overall cost of PCB manufacturing. However, the long-term benefits of using polyimide can offset the initial cost. -
Q: What are the key advantages of using polyimide PCBs?
A: The key advantages of polyimide PCBs include high temperature resistance, dimensional stability, flexibility, excellent electrical properties, and chemical resistance. -
Q: Can polyimide PCBs be recycled?
A: Like most polymers, polyimide is not easily recyclable, which raises concerns about its environmental impact. Research is ongoing to develop recycling methods and biodegradable alternatives to polyimide.
Conclusion
Polyimide has emerged as a high-performance material for PCB manufacturing, offering superior properties compared to traditional FR-4 laminates. Its ability to withstand high temperatures, maintain dimensional stability, and provide excellent electrical insulation makes it an ideal choice for demanding applications in various industries, such as aerospace, automotive, and medical devices.
As the electronics industry continues to evolve, with trends such as miniaturization, high-frequency communication, and flexible electronics, the demand for polyimide PCBs is expected to grow. While challenges such as cost and processing complexity need to be addressed, the long-term benefits of using polyimide, including improved reliability and longer product life, make it a compelling choice for PCB manufacturers and electronic product designers.
With ongoing research and development efforts focused on sustainable alternatives and recycling methods, polyimide PCBs are poised to play a significant role in shaping the future of the electronics industry. As manufacturers and designers continue to push the boundaries of what is possible with PCB technology, polyimide will undoubtedly remain a key material in enabling the next generation of high-performance electronic devices.
No responses yet