Introduction to Castellated PCBs
Castellated printed circuit boards (PCBs) are a special type of PCB that feature plated half holes or castellations along the edges. These castellated holes allow for easy and secure connections between PCBs when stacked or placed side-by-side. Castellated PCBs enable modular and compact electronic designs suitable for a wide range of applications.
The plated half holes, also known as castellated holes or castellations, are essentially semi-circular cutouts along the perimeter of the PCB. These cutouts are copper plated, creating conductive surfaces that can be soldered to corresponding pads on other PCBs or components. This unique design allows for reliable electrical and mechanical connections without the need for additional connectors or wires.
Advantages of Castellated PCBs
Castellated PCBs offer several advantages over traditional PCB designs:
-
Compact and modular design: Castellated holes allow PCBs to be stacked or placed side-by-side, reducing the overall footprint of the electronic assembly. This modular approach enables flexible and space-efficient designs.
-
Simplified assembly: With castellated holes, PCBs can be easily aligned and soldered together, streamlining the assembly process. This reduces the need for additional connectors or wiring, saving time and cost.
-
Improved reliability: The plated half holes provide a strong mechanical and electrical connection between PCBs, enhancing the overall reliability of the electronic assembly. The castellated design also minimizes the risk of connection failures due to vibration or mechanical stress.
-
Enhanced signal integrity: Castellated holes enable direct board-to-board connections, minimizing the use of connectors or wires. This reduces signal degradation and improves overall signal integrity, especially for high-frequency applications.
-
Versatile applications: Castellated PCBs are suitable for a wide range of applications, including IoT devices, wearable electronics, sensor modules, and more. They are particularly useful in designs that require high density, low profile, or modular architecture.
Plated Half Hole PCB Design Considerations
When designing a castellated PCB, several key factors must be considered to ensure optimal performance and manufacturability.
Castellated Hole Dimensions
The dimensions of the castellated holes are critical for proper mating and soldering between PCBs. The hole size, pitch, and spacing should be carefully designed based on the specific requirements of the application and the capabilities of the PCB manufacturer.
Parameter | Typical Value Range |
---|---|
Hole Diameter | 0.5 mm – 1.0 mm |
Hole Pitch | 1.0 mm – 2.54 mm |
Hole Spacing | 0.5 mm – 1.0 mm |
Table 1: Typical castellated hole dimensions
It is essential to consult with the PCB manufacturer to determine their specific design rules and limitations for castellated holes.
Pad and Solder Mask Design
The pad size and solder mask opening around the castellated holes should be designed to ensure proper soldering and prevent Solder Bridging. The pad should be slightly larger than the castellated hole to provide sufficient area for solder fillets.
Parameter | Typical Value Range |
---|---|
Pad Diameter | Hole Diameter + 0.2 mm to 0.4 mm |
Solder Mask Opening | Pad Diameter + 0.05 mm to 0.1 mm |
Table 2: Recommended pad and solder mask dimensions
The solder mask opening should be slightly larger than the pad to prevent solder mask from encroaching onto the pad surface, which can hinder solderability.
PCB Thickness and Material
The thickness and material of the PCB should be carefully selected based on the application requirements and the capabilities of the PCB manufacturer. Thinner PCBs are generally preferred for castellated designs to minimize the height of the assembled stack.
Common PCB thicknesses for castellated designs range from 0.4 mm to 1.6 mm, with 0.8 mm and 1.2 mm being the most widely used. The choice of PCB material depends on factors such as the operating temperature range, dielectric constant, and thermal conductivity required for the application.
Routing and Signal Integrity
Proper routing techniques should be employed to ensure signal integrity and minimize crosstalk between adjacent castellated holes. The PCB layout should be designed to maintain controlled impedance and avoid sharp bends or vias near the castellated holes.
It is recommended to use ground planes and power planes to provide shielding and reduce electromagnetic interference (EMI). Adequate spacing should be maintained between castellated holes and other components or traces to prevent unintended short circuits or signal coupling.
Assembly and Soldering Techniques
The assembly and soldering of castellated PCBs require specific techniques to ensure reliable connections and prevent defects.
PCB Alignment and Stacking
Accurate alignment of the castellated holes is crucial for successful assembly. Alignment pins or jigs can be used to ensure precise positioning of the PCBs during stacking. It is important to maintain consistent spacing between the PCBs to allow for proper soldering and prevent excessive stress on the castellated connections.
Soldering Methods
Several soldering methods can be used for assembling castellated PCBs, including:
-
Hand soldering: Manual soldering using a soldering iron and solder wire. This method is suitable for small-scale production or prototyping.
-
Reflow Soldering: Automated soldering process using a reflow oven. Solder Paste is applied to the castellated pads, and the PCBs are stacked and placed in the oven for solder reflow. This method is suitable for high-volume production.
-
Wave soldering: Automated soldering process using a wave soldering machine. The stacked PCBs are passed over a wave of molten solder, which selectively solders the castellated connections. This method is suitable for high-volume production but requires careful design considerations to prevent solder bridging.
Inspection and Quality Control
After soldering, the assembled castellated PCBs should be thoroughly inspected to ensure proper solder joints and identify any defects. Visual inspection using magnification tools can help detect solder bridging, insufficient solder fillets, or misaligned connections.
Automated optical inspection (AOI) systems can be employed for high-volume production to detect soldering defects and ensure consistent quality. Electrical testing should also be performed to verify the functionality and reliability of the castellated connections.
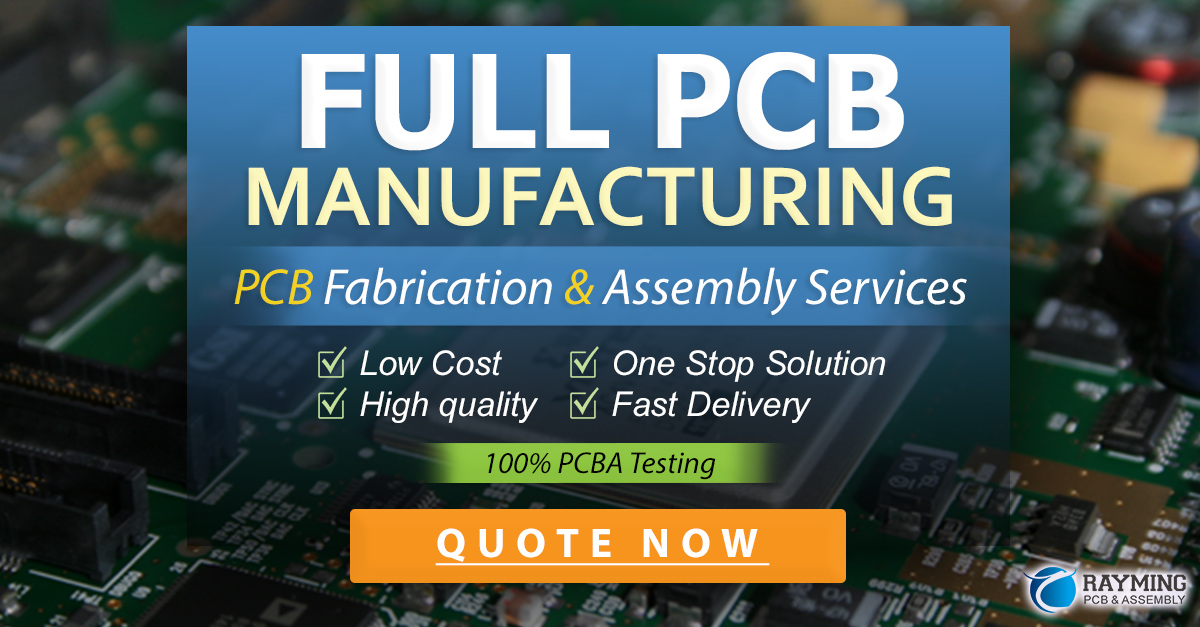
Applications of Castellated PCBs
Castellated PCBs find applications in various industries and product categories where modular, compact, and reliable electronic assemblies are required.
IoT Devices
Internet of Things (IoT) devices often require compact and modular designs to accommodate multiple sensors, wireless modules, and processing units. Castellated PCBs allow for the stacking of different functional modules, enabling the creation of small-form-factor IoT devices with enhanced functionality and flexibility.
Wearable Electronics
Wearable electronic devices, such as smartwatches, fitness trackers, and medical monitoring systems, benefit from the compact and low-profile design enabled by castellated PCBs. The modular approach allows for the integration of various sensors, displays, and power management modules in a small and lightweight package.
Sensor Modules
Sensor modules, such as environmental sensors, motion sensors, and biometric sensors, often require compact and robust packaging. Castellated PCBs enable the creation of standardized sensor modules that can be easily integrated into larger systems or stacked together to form multi-sensor assemblies.
Automotive Electronics
Automotive electronic systems, such as infotainment modules, advanced driver assistance systems (ADAS), and body control modules, can leverage castellated PCBs for modular and space-efficient designs. The castellated approach allows for the integration of multiple functional boards, reducing the overall system size and simplifying assembly.
Industrial Control Systems
Industrial control systems, such as programmable logic controllers (PLCs), motor drives, and power supplies, can benefit from the modularity and reliability offered by castellated PCBs. The castellated design enables the creation of standardized modules that can be easily replaced or upgraded, minimizing downtime and simplifying maintenance.
Frequently Asked Questions (FAQ)
1. What is the difference between castellated holes and plated through holes (PTHs)?
Castellated holes are plated half holes located along the edges of a PCB, while plated through holes (PTHs) are fully drilled and plated holes within the PCB. Castellated holes are used for board-to-board connections, while PTHs are used for mounting through-hole components or creating internal connections between layers.
2. Can castellated PCBs be used for high-frequency applications?
Yes, castellated PCBs can be used for high-frequency applications. The direct board-to-board connections enabled by castellated holes minimize signal degradation and improve signal integrity compared to using connectors or wires. However, proper design considerations, such as controlled impedance and adequate spacing, must be followed to ensure optimal high-frequency performance.
3. Are there any limitations on the number of PCBs that can be stacked using castellated holes?
The number of PCBs that can be stacked using castellated holes depends on several factors, including the hole size, pitch, and spacing, as well as the mechanical stability and thermal management requirements of the assembly. In general, castellated PCBs can be stacked up to several boards high, but the specific stacking limit should be determined based on the application requirements and design constraints.
4. How do castellated PCBs compare to connectors in terms of cost and reliability?
Castellated PCBs offer a cost-effective alternative to using connectors for board-to-board connections. By eliminating the need for separate connectors, castellated PCBs reduce the overall component count and simplify the assembly process, leading to lower manufacturing costs. In terms of reliability, castellated connections provide a strong mechanical and electrical bond between PCBs, minimizing the risk of connection failures due to vibration or mechanical stress. However, proper design and assembly techniques must be followed to ensure reliable castellated connections.
5. Can castellated PCBs be reworked or repaired?
Reworking or repairing castellated PCBs can be challenging due to the nature of the plated half-hole connections. If a castellated connection is damaged or requires rework, specialized soldering techniques and tools may be necessary. In some cases, the affected PCB may need to be replaced entirely. Therefore, it is important to follow proper design and assembly guidelines to minimize the need for rework or repair. If rework is necessary, it should be performed by experienced personnel using appropriate tools and techniques.
Conclusion
Plated half hole PCB castellated holes offer a unique and advantageous solution for creating modular, compact, and reliable electronic assemblies. By leveraging the benefits of castellated connections, designers can create space-efficient and flexible designs suitable for a wide range of applications, from IoT devices and wearable electronics to automotive and industrial control systems.
When designing castellated PCBs, careful consideration must be given to hole dimensions, pad and solder mask design, PCB thickness and material, and routing techniques to ensure optimal performance and manufacturability. Proper assembly and soldering methods, along with thorough inspection and quality control, are essential for achieving reliable and robust castellated connections.
As electronic devices continue to evolve and demand for compact and modular solutions grows, castellated PCBs are poised to play an increasingly important role in enabling innovative and efficient electronic designs across various industries.
No responses yet