Introduction to Peelable Solder Mask
Peelable solder mask (PSM) is a temporary protective coating used in printed circuit board (PCB) manufacturing. It is applied to specific areas of the PCB where soldering is required, protecting the underlying circuitry from damage during the soldering process. Unlike permanent solder masks, PSM can be easily removed after soldering, leaving a clean and precise solder joint.
Key Features of Peelable Solder Mask
- Temporary protective coating
- Applied to specific areas requiring soldering
- Easily removed after soldering
- Leaves clean and precise solder joints
Advantages of Using Peelable Solder Mask
1. Precision Soldering
PSM allows for precise control over the soldering process by exposing only the desired areas for soldering. This helps to prevent solder bridges and ensures accurate solder joint formation.
2. Protection of Sensitive Components
By covering sensitive components and circuitry with PSM, manufacturers can protect these areas from heat and potential damage during soldering.
3. Improved Efficiency
The use of PSM streamlines the soldering process, reducing the need for manual masking and unmasking. This leads to improved production efficiency and faster turnaround times.
4. Enhanced Product Quality
PSM contributes to the overall quality of the finished PCB by ensuring clean and precise solder joints, minimizing the risk of defects and improving the reliability of the end product.
Types of Peelable Solder Mask
1. Water-Soluble PSM
Water-soluble PSM is a popular choice due to its ease of removal using warm water. It is environmentally friendly and does not require the use of harsh chemicals.
2. Solvent-Based PSM
Solvent-based PSM offers excellent resistance to high temperatures and is suitable for applications that require extended exposure to heat during soldering. It is typically removed using solvents such as isopropyl alcohol.
3. UV-Curable PSM
UV-curable PSM is a fast-curing option that hardens when exposed to ultraviolet light. It provides good coverage and protection, and can be easily removed after soldering.
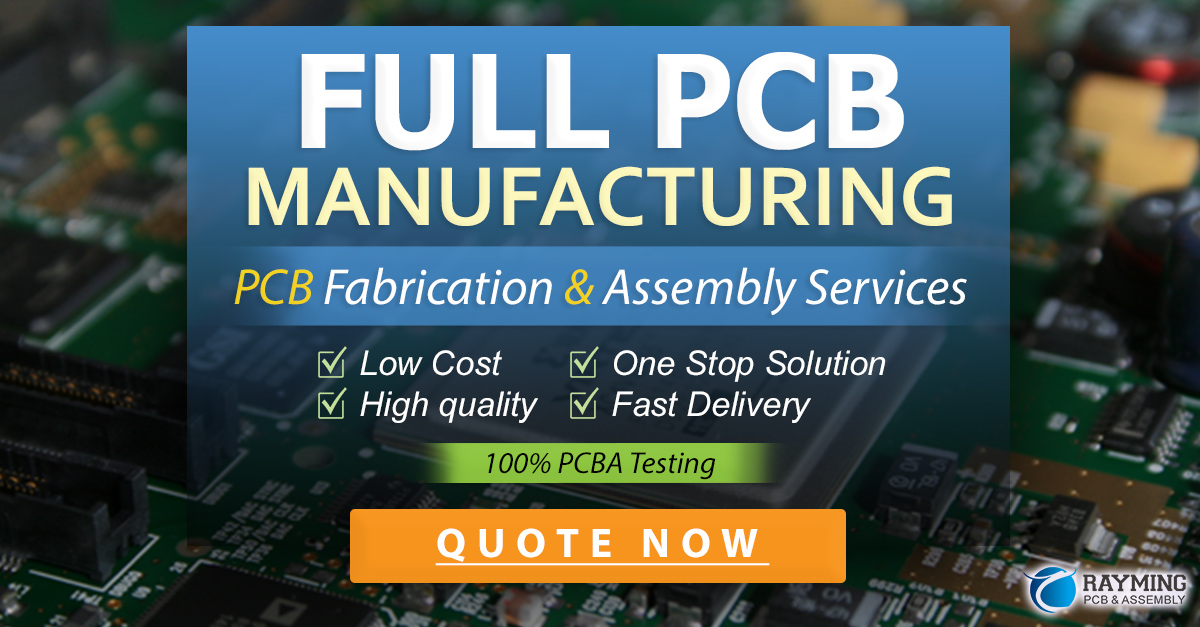
Application Process of Peelable Solder Mask
1. Surface Preparation
Before applying PSM, the PCB surface must be clean and free from contaminants. This ensures proper adhesion of the mask to the board.
2. Mask Application
PSM can be applied using various methods, such as screen printing, spray coating, or dip coating. The choice of application method depends on factors such as the size of the PCB, the required coverage area, and production volume.
3. Curing
After application, the PSM must be cured to achieve its desired properties. Curing methods vary depending on the type of PSM used, such as air drying, oven curing, or UV curing.
4. Soldering
Once the PSM is cured, the PCB undergoes the soldering process. The exposed areas of the PCB are soldered, while the masked areas remain protected.
5. Mask Removal
After soldering, the PSM is removed to reveal the soldered joints. The removal process depends on the type of PSM used, such as peeling off the mask or dissolving it using water or solvents.
Step | Process | Description |
---|---|---|
1 | Surface Preparation | Clean and prepare the PCB surface for mask application |
2 | Mask Application | Apply PSM using screen printing, spray coating, or dip coating |
3 | Curing | Cure the applied PSM to achieve desired properties |
4 | Soldering | Solder the exposed areas of the PCB |
5 | Mask Removal | Remove the PSM to reveal the soldered joints |
Factors to Consider When Selecting Peelable Solder Mask
1. Compatibility with PCB Materials
It is essential to choose a PSM that is compatible with the specific materials used in the PCB, such as the substrate, components, and solder alloy. Incompatible materials can lead to poor adhesion, incomplete protection, or difficulties in mask removal.
2. Temperature Resistance
Consider the temperature requirements of the soldering process when selecting a PSM. The mask should be able to withstand the peak soldering temperature without degradation or premature peeling.
3. Ease of Application and Removal
The chosen PSM should be easy to apply and remove without leaving residue or damaging the PCB. Water-soluble and solvent-based PSMs offer different levels of ease in application and removal.
4. Environmental and Safety Considerations
Opt for PSMs that are environmentally friendly and safe for operators to handle. Water-soluble PSMs are generally preferred due to their low environmental impact and minimal health risks.
Common Challenges and Solutions in Using Peelable Solder Mask
1. Incomplete Coverage
Incomplete coverage of the PSM can lead to exposed areas during soldering, resulting in potential defects or damage. To avoid this, ensure proper application techniques and consider using multiple coats if necessary.
2. Difficulty in Removal
Some PSMs may be challenging to remove completely, leaving residue on the PCB surface. This can be addressed by selecting a PSM with good removal properties and following the manufacturer’s recommended removal procedures.
3. Compatibility Issues
Incompatibility between the PSM and PCB materials can result in poor adhesion or premature peeling. Always check the compatibility of the selected PSM with the specific materials used in the PCB manufacturing process.
4. Shelf Life and Storage
PSMs have a limited shelf life and may degrade over time if not stored properly. Follow the manufacturer’s guidelines for storage conditions and use the PSM within its recommended shelf life to ensure optimal performance.
Future Trends in Peelable Solder Mask Technology
1. Improved Environmental Friendliness
There is a growing focus on developing PSMs that are more environmentally friendly, with reduced volatile organic compound (VOC) content and biodegradable formulations.
2. Enhanced Performance
Manufacturers are continuously working on improving the performance of PSMs, such as increasing temperature resistance, improving adhesion properties, and reducing the risk of residue formation.
3. Automation and Integration
The integration of PSM application and removal processes into automated PCB manufacturing lines is expected to increase, leading to improved efficiency and consistency in PCB production.
Frequently Asked Questions (FAQ)
1. What is the difference between peelable solder mask and permanent solder mask?
Peelable solder mask is a temporary protective coating that is removed after soldering, while permanent solder mask remains on the PCB throughout its lifetime.
2. Can peelable solder mask be used for all types of PCBs?
Peelable solder mask can be used for most types of PCBs, but it is essential to select a PSM that is compatible with the specific materials and manufacturing processes used.
3. How do I choose the right peelable solder mask for my PCB manufacturing process?
Consider factors such as compatibility with PCB materials, temperature resistance, ease of application and removal, and environmental and safety aspects when selecting a peelable solder mask.
4. What are the advantages of using water-soluble peelable solder mask?
Water-soluble peelable solder mask is environmentally friendly, easy to remove using warm water, and does not require the use of harsh chemicals.
5. Can peelable solder mask be reapplied if it peels off prematurely during the manufacturing process?
In most cases, peelable solder mask cannot be reapplied once it has peeled off prematurely. It is essential to ensure proper application and curing of the mask to prevent premature peeling.
Conclusion
Peelable solder mask is a vital component in PCB manufacturing, offering temporary protection to specific areas during the soldering process. It enables precise soldering, protects sensitive components, improves efficiency, and enhances the overall quality of the finished product. By understanding the types of PSM available, the application process, and factors to consider when selecting a PSM, manufacturers can optimize their PCB manufacturing process and produce high-quality, reliable products.
As technology advances, the development of more environmentally friendly, high-performance, and automation-compatible peelable solder masks will continue to shape the future of PCB manufacturing. By staying informed about the latest trends and best practices in PSM technology, manufacturers can remain competitive and meet the evolving demands of the electronics industry.
No responses yet