Introduction to PCBA Assembly
PCBA, or Printed Circuit Board Assembly, is the process of assembling electronic components onto a printed circuit board (PCB) to create a functional electronic device. The PCB is a flat board made of insulating material, such as fiberglass or plastic, with conductive tracks, pads, and other features etched onto its surface. These conductive elements allow electrical signals to be routed between the various components mounted on the board.
PCBA box build assembly is a comprehensive process that involves not only the assembly of the PCB but also the integration of the completed board into a fully functional electronic product, including enclosure, wiring, and testing.
Key Steps in PCBA Assembly
- Solder Paste Application
- Component Placement
- Reflow Soldering
- Inspection and Testing
- Final Assembly and Packaging
The Importance of PCBA Assembly in Electronics Manufacturing
PCBA assembly is a crucial aspect of electronics manufacturing, as it enables the creation of complex electronic devices with high precision and reliability. The process involves the integration of various electronic components, such as resistors, capacitors, integrated circuits (ICs), and connectors, onto a PCB to create a functional circuit.
The importance of PCBA assembly can be attributed to several factors:
-
Miniaturization: PCBA assembly allows for the creation of compact and highly integrated electronic devices, which is essential in today’s world of miniaturized electronics.
-
Consistency and Reliability: Automated PCBA assembly processes ensure consistent quality and reliability of the final product, reducing the risk of human error and improving overall device performance.
-
Cost-effectiveness: PCBA assembly, especially when automated, enables mass production of electronic devices at a lower cost per unit compared to manual assembly methods.
-
Flexibility: PCBA assembly can accommodate a wide range of electronic components and PCB designs, allowing for the creation of diverse electronic products across various industries.
PCBA Assembly Techniques
There are two primary techniques used in PCBA assembly: Through-Hole Technology (THT) and Surface Mount Technology (SMT).
Through-Hole Technology (THT)
THT is an older PCBA assembly technique that involves inserting component leads through drilled holes in the PCB and soldering them to pads on the opposite side of the board. This method is still used for larger components or in applications where high mechanical strength is required.
Advantages of THT:
– Stronger mechanical bonds between components and PCB
– Easier to replace or repair components
– Suitable for high-power applications
Disadvantages of THT:
– Larger PCB size due to the need for drilled holes
– Slower assembly process compared to SMT
– Higher assembly costs
Surface Mount Technology (SMT)
SMT is a more modern PCBA assembly technique that involves placing components directly onto pads on the surface of the PCB and soldering them in place using reflow soldering. This method allows for smaller, more densely packed PCBs and is widely used in today’s electronics manufacturing.
Advantages of SMT:
– Smaller PCB size and higher component density
– Faster assembly process and lower assembly costs
– Improved high-frequency performance due to shorter lead lengths
Disadvantages of SMT:
– More difficult to replace or repair components
– Requires specialized equipment and skillsets
– More susceptible to thermal stress and vibration
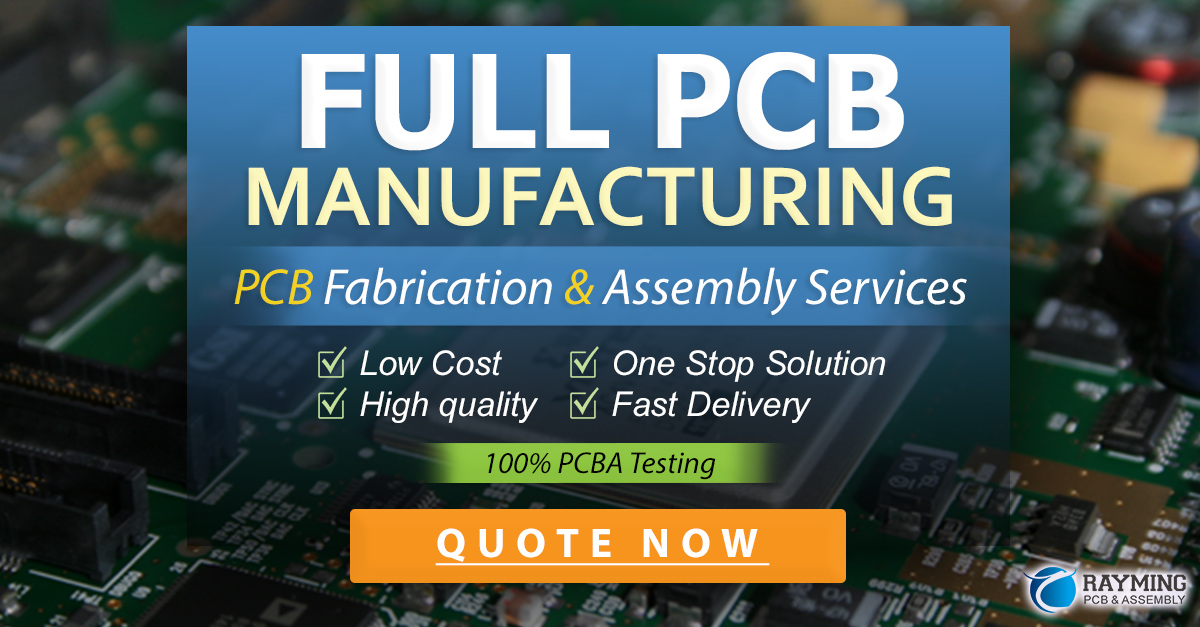
PCBA Box Build Assembly Process
The PCBA box build assembly process involves several key stages, from initial PCB design and component selection to final product assembly and testing.
1. PCB Design and Component Selection
The first stage in PCBA box build assembly is the design of the PCB and the selection of appropriate electronic components. This stage involves:
- Schematic capture: Creating a graphical representation of the electronic circuit, showing how components are connected.
- PCB layout: Designing the physical layout of the PCB, including component placement, trace routing, and layer stackup.
- Component selection: Choosing the appropriate electronic components based on the circuit requirements, such as power rating, precision, and cost.
2. PCB Fabrication
Once the PCB design is finalized, the next stage is PCB fabrication. This process involves:
- Printing the PCB layout onto a copper-clad laminate.
- Etching away unwanted copper to create conductive traces and pads.
- Drilling holes for through-hole components (if applicable).
- Applying solder mask and silkscreen layers for protection and labeling.
3. PCBA Assembly
With the fabricated PCB and selected components ready, the PCBA assembly process can begin. This stage typically involves:
- Solder paste application: Applying solder paste to the pads on the PCB using a stencil or screen printing process.
- Component placement: Placing electronic components onto the pasted pads using pick-and-place machines or manual methods.
- Reflow soldering: Passing the populated PCB through a reflow oven, which melts the solder paste and creates a strong electrical and mechanical bond between the components and the PCB.
- Inspection and testing: Visually inspecting the assembled PCB for defects and performing electrical tests to ensure proper functionality.
4. Final Assembly and Packaging
The final stage in PCBA box build assembly involves integrating the assembled PCB into its enclosure and packaging the complete product for shipment. This stage typically includes:
- Enclosure assembly: Placing the PCB into its designated enclosure and securing it in place.
- Wiring and connectors: Attaching any necessary wires, cables, or connectors to the PCB or enclosure.
- Final testing: Performing a final round of functional and quality control tests to ensure the product meets all specifications.
- Packaging and shipping: Packaging the finished product and preparing it for shipment to the end customer.
Quality Control in PCBA Assembly
Ensuring the quality of the final product is a critical aspect of PCBA box build assembly. Quality control measures are implemented throughout the assembly process to identify and rectify any defects or issues.
Common PCBA Assembly Defects
- Solder bridges: Unintended connections between two or more solder joints, causing short circuits.
- Cold solder joints: Weak or incomplete solder connections due to insufficient heat or solder.
- Component misalignment: Components placed incorrectly on the PCB, leading to poor connections or functionality.
- Tombstoning: When a component stands up on one end due to uneven heating during reflow soldering.
- Insufficient or excessive solder: Too little solder can result in weak connections, while too much solder can cause short circuits or bridging.
Quality Control Methods
- Visual inspection: Manual or automated visual checks of the assembled PCB for defects or anomalies.
- X-ray inspection: Non-destructive testing using X-rays to detect hidden defects, such as voids or bridging, beneath components or in solder joints.
- In-circuit testing (ICT): Electrical testing of individual components and circuits on the PCB using specialized test fixtures.
- Functional testing: Testing the assembled PCB or final product to ensure it performs as intended under various operating conditions.
- Burn-in testing: Subjecting the assembled PCB or final product to elevated temperatures and/or voltages to identify any early-life failures or weaknesses.
Benefits of Outsourcing PCBA Box Build Assembly
Outsourcing PCBA box build assembly to a specialized electronics manufacturing service (EMS) provider offers several advantages for companies looking to streamline their production processes and reduce costs.
-
Access to expertise and resources: EMS providers have the necessary expertise, equipment, and facilities to handle complex PCBA assembly projects efficiently and cost-effectively.
-
Scalability and flexibility: Outsourcing allows companies to scale their production up or down as needed, without the need to invest in additional infrastructure or personnel.
-
Cost savings: By leveraging the economies of scale and expertise of an EMS provider, companies can often achieve significant cost savings compared to in-house assembly.
-
Faster time-to-market: EMS providers can often complete PCBA assembly projects faster than in-house teams, due to their specialized expertise and optimized processes.
-
Focus on core competencies: Outsourcing PCBA assembly allows companies to focus on their core competencies, such as product design and marketing, while leaving the manufacturing to experts.
Choosing the Right PCBA Assembly Partner
When selecting an EMS provider for PCBA box build assembly, there are several key factors to consider:
-
Technical capabilities: Ensure the provider has the necessary equipment, expertise, and certifications to handle your specific PCBA assembly requirements.
-
Quality management: Look for providers with robust quality management systems, such as ISO 9001 certification, and a proven track record of delivering high-quality products.
-
Communication and responsiveness: Choose a provider that maintains clear and open communication channels and is responsive to your needs and concerns throughout the project.
-
Cost and lead times: Compare quotes and lead times from multiple providers to ensure you are getting a competitive price and delivery schedule for your project.
-
Reputation and references: Research the provider’s reputation in the industry and seek references from other clients to gauge their experience and level of satisfaction.
Future Trends in PCBA Assembly
As the electronics industry continues to evolve, PCBA box build assembly is also adapting to new technologies and market demands. Some of the key trends shaping the future of PCBA assembly include:
-
Miniaturization: The ongoing trend towards smaller, more compact electronic devices is driving the adoption of advanced packaging technologies, such as 3D packaging and system-in-package (SiP) solutions.
-
Increased automation: The use of automated assembly equipment, such as high-speed pick-and-place machines and 3D automated optical inspection (AOI) systems, is becoming more prevalent to improve efficiency and quality.
-
Adoption of Industry 4.0 technologies: The integration of Industry 4.0 technologies, such as the Internet of Things (IoT), big data analytics, and artificial intelligence (AI), is enabling smarter, more connected, and more efficient PCBA assembly processes.
-
Sustainable manufacturing practices: There is a growing emphasis on sustainable manufacturing practices in PCBA assembly, such as the use of lead-free solders and the adoption of green packaging materials.
-
Flexible and agile manufacturing: The ability to quickly adapt to changing market demands and produce a wide variety of products in smaller batches is becoming increasingly important in PCBA assembly.
Conclusion
PCBA box build assembly is a complex and critical process in the creation of modern electronic devices. By understanding the various techniques, processes, and quality control measures involved in PCBA assembly, companies can make informed decisions when it comes to designing, manufacturing, and outsourcing their electronic products.
As the electronics industry continues to evolve, staying up-to-date with the latest trends and technologies in PCBA assembly will be essential for companies looking to remain competitive and deliver high-quality, innovative products to their customers.
Frequently Asked Questions (FAQ)
- What is the difference between PCBA and PCB?
-
PCB (Printed Circuit Board) refers to the bare board with conductive tracks and pads, while PCBA (Printed Circuit Board Assembly) refers to the PCB populated with electronic components.
-
What are the main advantages of surface mount technology (SMT) over through-hole technology (THT)?
-
SMT allows for smaller PCB sizes, higher component density, faster assembly processes, and lower assembly costs compared to THT. However, THT still offers advantages in terms of stronger mechanical bonds and easier component replacement or repair.
-
What are some common defects that can occur during PCBA assembly?
-
Common PCBA assembly defects include solder bridges, cold solder joints, component misalignment, tombstoning, and insufficient or excessive solder.
-
What are the benefits of outsourcing PCBA box build assembly to an electronics manufacturing service (EMS) provider?
-
Outsourcing PCBA assembly offers advantages such as access to expertise and resources, scalability and flexibility, cost savings, faster time-to-market, and the ability to focus on core competencies.
-
What are some key trends shaping the future of PCBA assembly?
- Key trends in PCBA assembly include miniaturization, increased automation, adoption of Industry 4.0 technologies, sustainable manufacturing practices, and flexible and agile manufacturing approaches.
No responses yet