Introduction to PCB Stencils
A PCB (Printed Circuit Board) stencil is a thin sheet of material, typically stainless steel or polyester, with laser-cut openings that correspond to the pads on a PCB. The stencil is used to apply Solder Paste onto the PCB pads before component placement and Reflow Soldering. This process ensures precise and consistent solder paste application, resulting in higher quality solder joints and improved manufacturing efficiency.
Importance of PCB Stencils in Electronics Manufacturing
PCB stencils play a crucial role in modern electronics manufacturing, especially in surface mount technology (SMT) processes. They offer several benefits, including:
- Precise solder paste application
- Consistent solder joint quality
- Increased production speed and efficiency
- Reduced solder paste waste
- Improved reliability of the final product
Types of PCB Stencils
There are two main types of PCB stencils: stainless steel and polyester. Each material has its advantages and disadvantages, making them suitable for different applications.
Stainless Steel Stencils
Stainless steel stencils are the most common type used in PCB Assembly. They are durable, long-lasting, and offer excellent paste release properties. The main advantages of stainless steel stencils include:
- High durability and long lifespan
- Excellent paste release properties
- Suitable for high-volume production
- Compatible with a wide range of solder paste types
However, stainless steel stencils are more expensive than polyester stencils and require more storage space due to their rigidity.
Polyester Stencils
Polyester stencils, also known as mylar stencils, are made from a flexible, transparent material. They are less expensive than stainless steel stencils and are suitable for low-volume production or prototyping. The main advantages of polyester stencils include:
- Lower cost compared to stainless steel stencils
- Flexibility and ease of storage
- Suitable for low-volume production or prototyping
- Transparency allows for easy alignment with the PCB
However, polyester stencils have a shorter lifespan and may not offer the same paste release properties as stainless steel stencils.
PCB Stencil Thickness and Aperture Design
The thickness of a PCB stencil and the design of its apertures play a crucial role in determining the quality of solder paste application.
Stencil Thickness
PCB stencil thickness typically ranges from 0.1 mm to 0.2 mm (4 to 8 mils). The appropriate thickness depends on several factors, such as the size of the components, the pitch of the pads, and the type of solder paste used. A thicker stencil will deposit more solder paste, while a thinner stencil will deposit less.
Component Size | Pitch | Recommended Stencil Thickness |
---|---|---|
0201 | 0.3 mm | 0.1 mm (4 mils) |
0402 | 0.5 mm | 0.1 mm (4 mils) |
0603 | 0.8 mm | 0.1-0.15 mm (4-6 mils) |
0805 | 1.0 mm | 0.15-0.2 mm (6-8 mils) |
1206 | 1.5 mm | 0.15-0.2 mm (6-8 mils) |
Aperture Design
The aperture design of a PCB stencil refers to the shape and size of the openings that correspond to the pads on the PCB. Proper aperture design ensures the correct amount of solder paste is deposited on each pad. There are several factors to consider when designing stencil apertures:
-
Aperture size: The size of the aperture should be slightly larger than the pad to accommodate the solder paste.
-
Aperture shape: The shape of the aperture can be circular, square, or rectangular, depending on the shape of the pad and the component.
-
Aperture wall angle: The wall angle of the aperture affects the release of the solder paste. A wall angle of 5° to 7° is recommended for optimal paste release.
-
Aperture aspect ratio: The aspect ratio is the ratio of the aperture width to the stencil thickness. An aspect ratio of 1.5 to 2.0 is recommended for most applications.
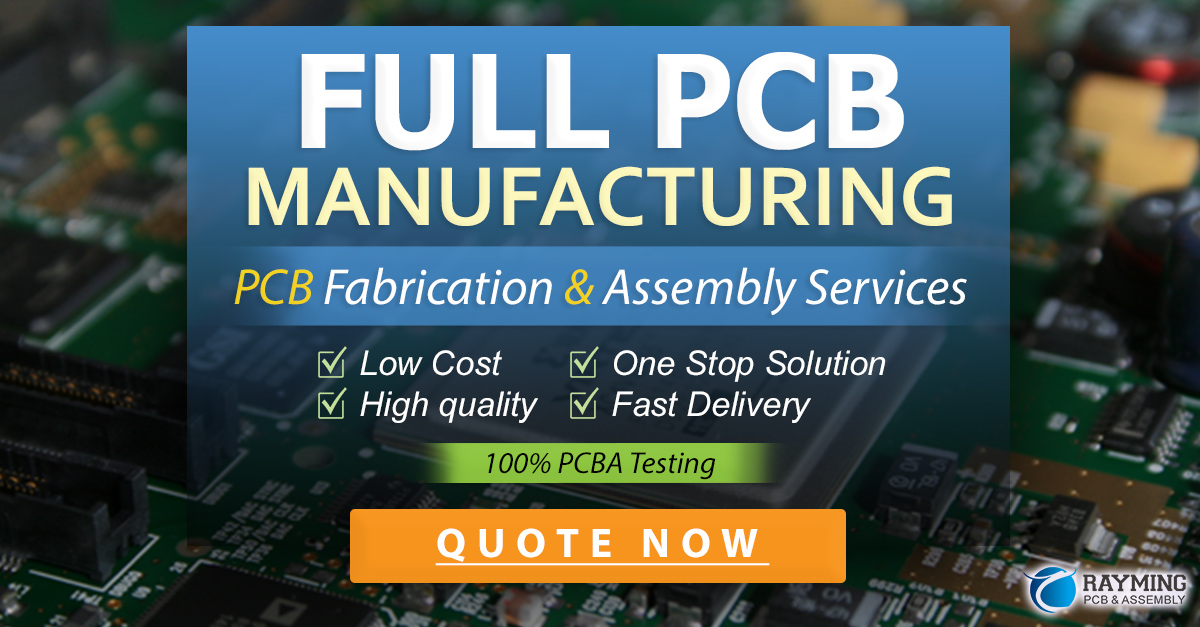
PCB Stencil Frame Types and Mounting
PCB stencils are typically mounted on a frame to ensure stability and proper alignment during the solder paste application process. There are two main types of frames used for PCB stencils: cast aluminum frames and tubular frames.
Cast Aluminum Frames
Cast aluminum frames are the most common type used in PCB assembly. They are sturdy, durable, and offer excellent stability during the printing process. Cast aluminum frames are available in various sizes to accommodate different PCB dimensions.
Advantages:
– High durability and stability
– Compatible with most stencil printers
– Available in various sizes
Disadvantages:
– Higher cost compared to tubular frames
– Heavier weight
Tubular Frames
Tubular frames, also known as stretch frames, are made from lightweight aluminum tubes. The stencil is stretched and glued onto the frame, providing a taut and flat surface for solder paste application. Tubular frames are less expensive than cast aluminum frames and are suitable for low-volume production or prototyping.
Advantages:
– Lower cost compared to cast aluminum frames
– Lightweight and easy to handle
– Suitable for low-volume production or prototyping
Disadvantages:
– Less durable than cast aluminum frames
– May not provide the same level of stability during printing
Stencil Mounting
Proper stencil mounting is essential for achieving accurate solder paste application. The stencil should be mounted securely on the frame and aligned with the PCB using fiducial marks or alignment pins. The distance between the stencil and the PCB, known as the snap-off distance, should be consistent across the entire PCB to ensure even solder paste deposition.
Stencil Type | Recommended Snap-Off Distance |
---|---|
Stainless Steel | 0.2-0.3 mm (8-12 mils) |
Polyester | 0.15-0.2 mm (6-8 mils) |
Solder Paste and PCB Stencil Interaction
The interaction between the solder paste and the PCB stencil is crucial for achieving high-quality solder joints. Several factors influence this interaction, including solder paste rheology, stencil aperture design, and printing parameters.
Solder Paste Rheology
Solder paste rheology refers to the flow and deformation properties of the solder paste. A solder paste with the appropriate rheology will flow easily through the stencil apertures and maintain its shape on the PCB pads. The main rheological properties to consider are:
-
Viscosity: The resistance of the solder paste to flow. A solder paste with the appropriate viscosity will flow easily through the stencil apertures without slumping or spreading on the PCB.
-
Thixotropy: The ability of the solder paste to maintain its shape after deposition. A thixotropic solder paste will maintain its shape on the PCB pads, preventing bridging or slumping.
-
Tackiness: The ability of the solder paste to adhere to the PCB pads and components. A solder paste with the appropriate tackiness will hold the components in place during the reflow process.
Printing Parameters
Printing parameters, such as print speed, pressure, and separation speed, also influence the interaction between the solder paste and the PCB stencil. Optimizing these parameters ensures consistent solder paste deposition and helps prevent defects, such as insufficient or excessive solder paste.
Parameter | Recommended Range |
---|---|
Print Speed | 25-100 mm/s |
Print Pressure | 0.2-0.4 kg/cm² |
Separation Speed | 1-5 mm/s |
PCB Stencil Cleaning and Maintenance
Regular cleaning and maintenance of PCB stencils are essential for ensuring consistent solder paste application and preventing defects. Solder paste residue, dust, and debris can accumulate on the stencil, affecting its performance and leading to issues such as clogged apertures or uneven paste deposition.
Stencil Cleaning Methods
There are several methods for cleaning PCB stencils, depending on the type of stencil and the level of contamination:
-
Manual cleaning: Using a lint-free cloth or paper towel and a suitable solvent, such as isopropyl alcohol (IPA) or a commercial stencil cleaner, to wipe the stencil clean.
-
Ultrasonic cleaning: Immersing the stencil in an ultrasonic cleaning bath filled with a cleaning solution to remove stubborn residue and contamination.
-
Automated cleaning: Using a stencil cleaning machine that automatically applies a cleaning solution and brushes or wipes the stencil clean.
Maintenance Tips
To maintain the performance and longevity of PCB stencils, follow these tips:
- Clean the stencil regularly, ideally after every print cycle or at least once per shift.
- Use compatible cleaning solutions and avoid aggressive solvents that can damage the stencil or the frame.
- Inspect the stencil for signs of wear, damage, or clogged apertures, and replace or repair the stencil as needed.
- Store the stencil in a clean, dry environment to prevent contamination and damage.
Frequently Asked Questions (FAQ)
1. What is the difference between a PCB stencil and a solder paste mask?
A PCB stencil is a separate sheet of material with openings that correspond to the pads on a PCB, used to apply solder paste. A solder paste mask, also known as a solder resist or Solder mask, is a layer applied directly to the PCB that covers the non-solderable areas and prevents solder from adhering to them.
2. Can I reuse a PCB stencil?
Yes, PCB stencils can be reused multiple times with proper cleaning and maintenance. However, the lifespan of a stencil depends on factors such as the material, thickness, and frequency of use. Regularly inspect the stencil for signs of wear or damage and replace it as needed.
3. How do I choose the right solder paste for my PCB stencil?
When selecting a solder paste for your PCB stencil, consider factors such as the type of components, the pitch of the pads, and the reflow profile. Consult the solder paste manufacturer’s recommendations and test the paste with your specific stencil and PCB Design to ensure compatibility and optimal performance.
4. Can I use a laser-cut PCB stencil for hand soldering?
While laser-cut PCB stencils are primarily used for automated solder paste application in SMT assembly, they can also be used for hand soldering. However, hand soldering with a stencil requires skill and practice to achieve consistent results. It is more common to use a solder paste dispenser or syringe for hand soldering applications.
5. How often should I clean my PCB stencil?
It is recommended to clean your PCB stencil regularly, ideally after every print cycle or at least once per shift. Regular cleaning prevents solder paste buildup, clogged apertures, and ensures consistent solder paste application. However, the specific cleaning frequency may vary depending on factors such as the type of solder paste, the volume of production, and the environment.
Conclusion
PCB stencils are essential tools in modern electronics manufacturing, enabling precise and consistent solder paste application for high-quality solder joints. Understanding the types of stencils, their materials, thickness, and aperture design is crucial for selecting the right stencil for your application. Proper mounting, cleaning, and maintenance ensure optimal stencil performance and long-lasting results.
By leveraging the benefits of PCB stencils and following best practices for their use and care, manufacturers can improve the efficiency, reliability, and quality of their PCB assembly processes.
No responses yet